Importance of Wire EDM in Auto Parts Manufacturing
1、What is wire EDM?
Wire electrical discharge machining (WEDM) uses metal wire to generate sparks to remove workpiece material. The metal wire is usually made of brass or other materials. It is sent to the workpiece through a conduit, and a high-voltage current is applied to it to discharge and generate sparks, gradually removing the material to form the desired shape. This is a high-precision processing technology that can shape complex shapes, but it is time-consuming and costly. It is generally used for special processing needs and is widely used in tool and mold manufacturing, military, medical equipment manufacturing and other fields, and is more common in the field of automotive parts manufacturing.
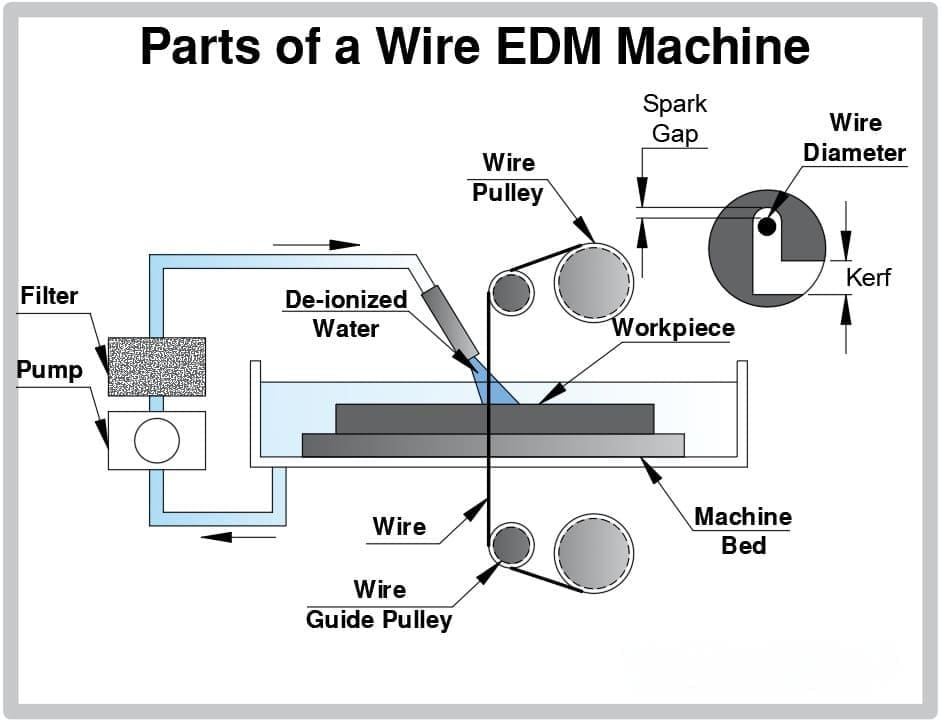
2、Advantages of Wire EDM for the Automotive Industry
1.High Precision
Wire EDM has the characteristics of high precision, which enables it to produce automotive parts with strict tolerance requirements. It has a wide range of uses and can process a variety of materials. It is famous for its rapid processing technology and can produce parts quickly and in large quantities, which is of great significance to the improvement of production efficiency in the automotive industry.
2.No mechanical force required
Wire EDM does not require any mechanical force when processing precision materials, which is in sharp contrast to other traditional cutting procedures that require a lot of force to obtain results, and will not cause deformation or distortion of the final product.
3.Customizable design
Wire EDM can realize complex designs based on drawings and samples provided by customers. In this process, the connector mold parts used do not require much mechanical force, making the entire production process more precise. At the same time, it can meet customers’ specific requirements for design, shape and size, and use the principle of fine wire discharge to process hard and brittle materials in mass production.
4.Economical and efficient
Durable materials are required for automobile production. Wire EDM does not apply force during processing and does not require additional processing steps, thereby reducing costs.
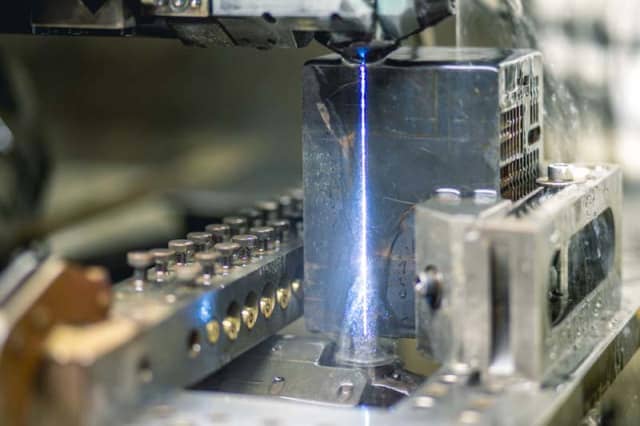
5.Reduce secondary operations
Wire EDM can produce parts with extremely fine and smooth surfaces. No or very few secondary operations are required after processing, which not only improves production efficiency but also reduces costs.
6.Can cut hard materials
Wire EDM can be used to cut hard materials. Its technology is not limited by the hardness of the material and is very suitable for processing hard materials such as copper, molybdenum, and tungsten.
7.Environmental protection
Traditional processing methods will produce a lot of waste after the processing program is completed. The treatment of these wastes is both expensive and time-consuming. Wire cutting produces the least waste, which greatly reduces the cost of waste treatment.
3、Application examples of wire cutting in automobile parts manufacturing
1.Bumper
The car bumper is converted from precious metal materials to plastic materials through injection molding. In addition to the original protective function, the processed bumper can also be coordinated with the shape, lighter and has the advantages of weldability and good coating performance. In the processing of certain special parts or precision parts of the bumper, EDM wire cutting can play an important role.
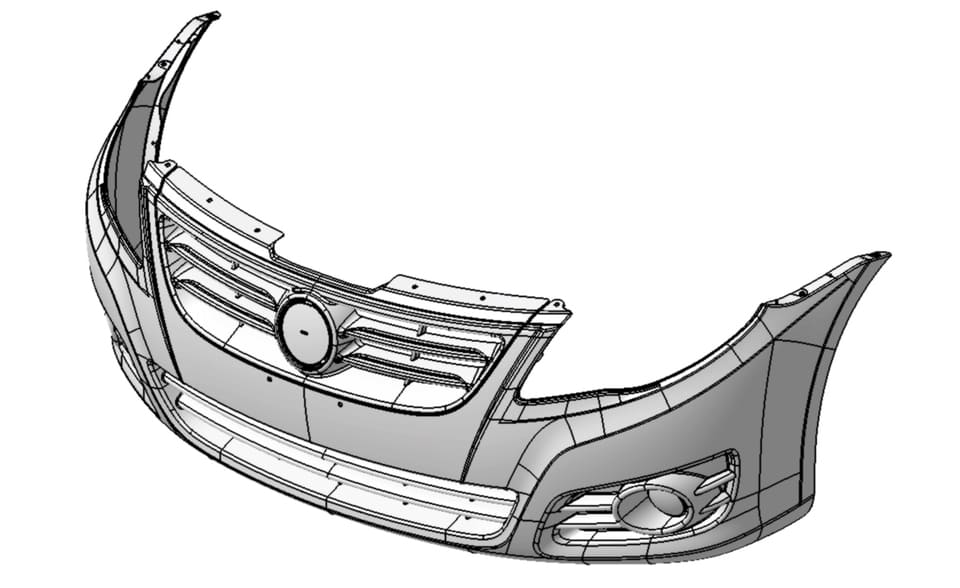
2.Instrument panel
The instrument panel is classified into various categories according to safety and comfort. The hard plastic instrument panel adopts injection molding process, which is simple and requires less investment; the blister instrument panel presents the surface feel through a specific process; the semi-hard foam soft instrument panel is filled with polyurethane foam to improve the touch and increase the energy absorption capacity.
3.Car door
The car door is designed for people to enter and exit and isolate interference from outside the car. The quality is reflected in anti-collision, sealing, and convenient opening and closing. It is made of new plastic materials for injection molding to enhance the overall performance of the vehicle. In the manufacture of car doors, for parts with special shapes or high precision requirements, EDM wire cutting can ensure the processing accuracy and quality.
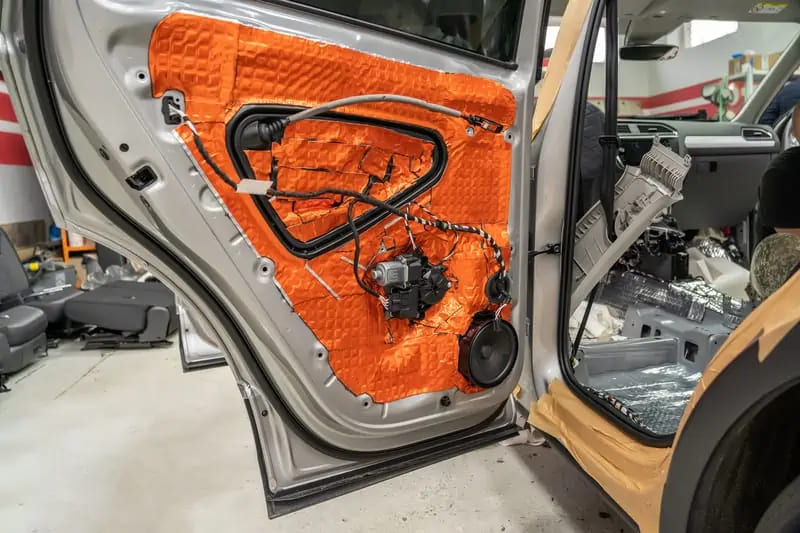
4.Air conditioner and filter
The shell of the automobile air conditioner is an important component. Its structure determines the performance of the air conditioner. It is made of injection molding of new engineering plastic materials. The air conditioner can perform various treatments on the air inside the car and has become a symbol of the functional device of the car. In the manufacturing of precision parts or special-shaped parts related to air conditioners and filters, EDM wire cutting plays an irreplaceable role.
4、Conclusion
In summary, wire EDM has an important significance in the manufacturing of automotive parts. Its unique processing principle brings many benefits to the automotive industry and is widely used in the manufacturing of various automotive parts, providing strong support for the development of automotive parts manufacturing.
If you are looking for an experienced machining manufacturer, Xavier is your ideal choice. The Xavier team is well-equipped to provide high-quality CNC machining solutions. If you want to learn more or discuss your machining needs with us, please feel free to contact us.