Horizontal milling machine: universal, multi-task processing
A horizontal milling machine is a machine tool with a milling spindle parallel to the worktable and in a horizontal position. The milling cutter and cutter shaft are mounted on the spindle and rotate around the spindle axis. It can mill planes, forming surfaces, grooves, gears, spiral grooves, etc. Horizontal milling machines have become a popular choice for various applications due to their cutting ability of the tool and their ability to handle large-scale operations with high production requirements.
This article will first introduce the definition, characteristics and main components of horizontal milling machines, so that everyone has a basic understanding of horizontal milling machines. Next, it will introduce the horizontal milling process, horizontal milling machine processing steps, and advantages and disadvantages analysis. Finally, it will introduce the precautions and applications of horizontal milling machine processing. From front to back, detailed introduction, comprehensive summary, I believe that after reading this article, you will get the information you want.
1.Definition, characteristics, and main components of horizontal milling machines
Definition: A horizontal milling machine is a heavy-duty milling machine with a worktable fixed to the machine bed and a spindle that moves vertically along the Z axis.
Main Features: Horizontal milling machines are known for their high structural rigidity, large surface area, and excellent load-bearing capacity, making them ideal for machining large and heavy workpieces.
Main Components: Spindle Assembly, Table, Column, and Bed.
Spindle Assembly: Drives the cutting tool for various machining operations.
Table: Holds the workpiece and can only move along the X-axis (horizontally).
Column and Bed: Provide support for the vertical movement of the spindle, ensuring the overall rigidity and stability of the machine.
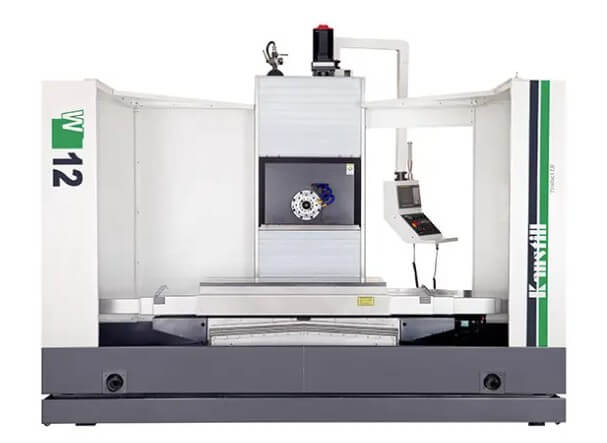
2.What is Horizontal Milling
A rotating spindle is mounted horizontally, holding and moving the cutting tool, which removes material from the fixed workpiece. Horizontal milling is known for its higher cutting forces and faster milling process. It also allows the cutting head to approach the workpiece from multiple angles.
With a horizontal milling machine, you can use specialized tools to help create bevels, grooves, and radii. This type of milling machine is common when working with large workpieces or when the project requires deeper cuts.
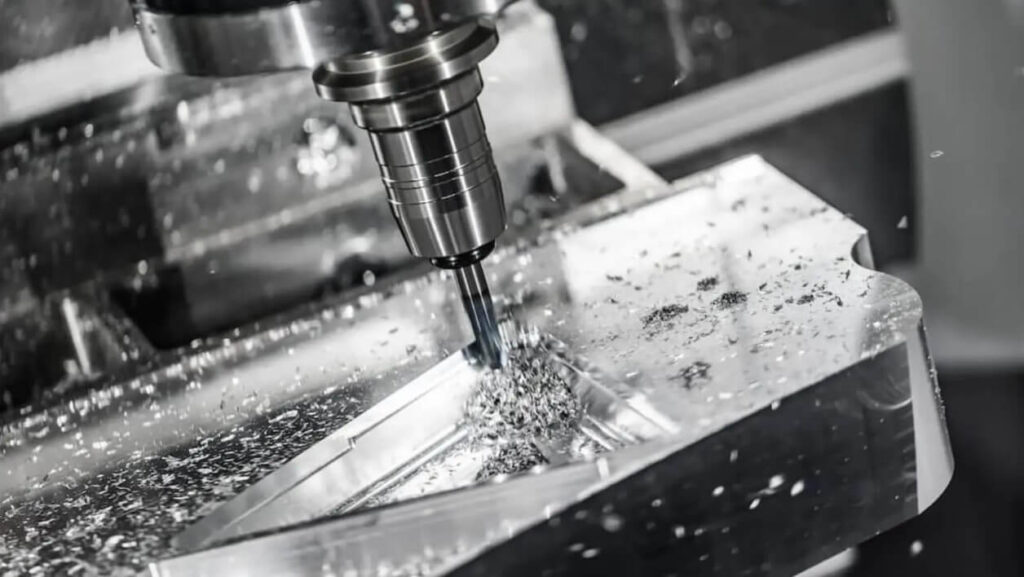
3.How to use a horizontal milling machine for machining?
The processing process of a horizontal milling machine mainly includes the following steps:
(1) Process analysis and program formulation:
- First, a process analysis is required to clarify the structural characteristics, material properties, processing accuracy and other requirements of the parts.
- According to these requirements, a reasonable processing process plan is formulated, including the selection of appropriate tools, cutting parameters and processing paths.
- The programmer uses the CNC programming language to convert the process plan into a CNC program that can be recognized by the machine tool.
(2) Workpiece positioning and clamping:
- In the automated processing process, the workpiece needs to be accurately positioned and clamped to ensure processing accuracy and stability.
- Horizontal CNC milling machines usually use hydraulic, pneumatic and other clamping devices to achieve automatic positioning and clamping of the workpiece.
- The workpiece coordinate system origin setting function can also be used to conveniently set the workpiece origin and coordinate system conversion.
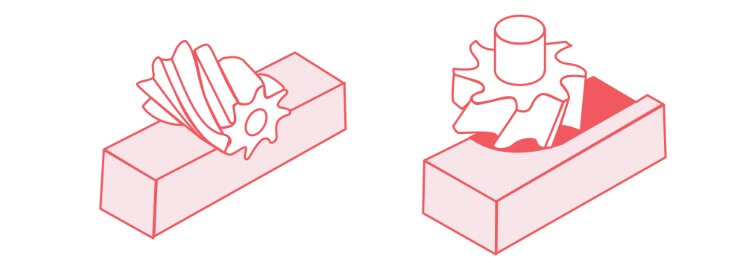
(3) Tool selection and pre-adjustment:
- According to the process plan and processing requirements, select the appropriate tool for processing.
- Horizontal CNC milling machines are usually equipped with a variety of tools, such as cylindrical milling cutters, disc milling cutters, angle milling cutters, etc.
- When selecting a tool, factors such as the tool material, coating, and geometric parameters need to be considered.
In order to improve the tool life and processing efficiency, the tool also needs to be pre-adjusted and compensated.
These steps ensure that the horizontal milling machine can efficiently and accurately complete various processing tasks and meet the requirements of precision and efficiency in industrial manufacturing.
4.Advantages and disadvantages of horizontal milling machines
Advantages:
(1) The horizontal milling machine has good rigidity and can bear heavy-load cutting.
(2) The spindle motor of the horizontal milling machine has high power and a wide speed range, which can give full play to the tool efficiency and is suitable for high-speed cutting.
(3) Wear-resistant cast iron is used for easily worn castings, and high-quality alloy steel is used for important parts, which is stable and durable.
(4) The machine tool has a complete lubrication system.
(5) The horizontal milling machine can be equipped with a digital display device according to user needs, making the operation of the equipment simple, convenient and fast.
(6) One of the biggest advantages of the horizontal milling machine is its cutting efficiency. This milling machine has a faster cutting speed than the vertical milling machine, which increases production and shortens delivery time.
(7) Excellent chip removal. Machining operations generate chips that, if not removed effectively, can lead to manufacturing defects. On horizontal milling machines, gravity facilitates the natural removal of chips and other debris, resulting in an excellent surface finish.
(8) Horizontal milling machines can process large workpieces that vertical milling machines cannot. Horizontal machines have greater cutting depths and support attachments, making it easier to manufacture complex products.
Disadvantages:
(1) Expensive
Horizontal milling machines are much more expensive to purchase and maintain than vertical milling machines. Therefore, large manufacturing companies are more likely to use this type of equipment. Small businesses tend to use vertical milling machines because they do not require huge capital investments.
(2) Lack of trained operators
Horizontal milling machines are not common. Therefore, there is a lack of operators with direct experience in operating this equipment.
(3) More floor space required
Horizontal milling machines tend to take up more floor space than vertical milling machines. Therefore, this option is more suitable for large workshops that have enough space to accommodate such equipment.
5.Precautions for horizontal milling machine processing
(1) Selecting appropriate tools and cutting parameters
Selecting appropriate tools and cutting parameters is a key link in the horizontal milling machine processing process.
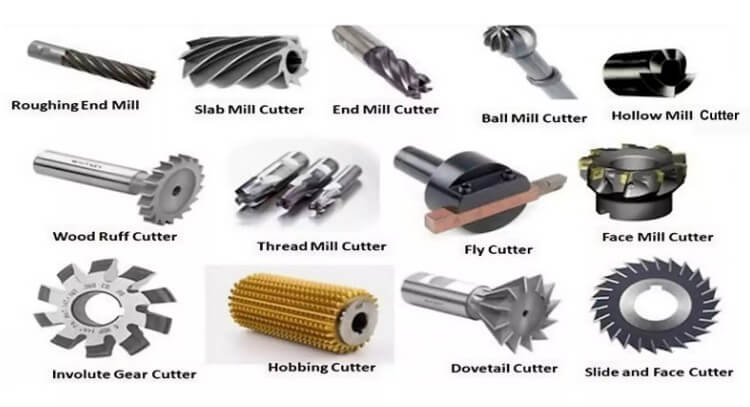
The selection of tools should be determined based on factors such as the hardness, strength, toughness and processing accuracy of the material being processed, and the size and grinding angle of the tool should also be considered.
In terms of cutting parameters, the appropriate cutting speed, feed speed and cutting depth should be selected based on factors such as the nature of the material being processed, the type of tool and the cutting amount.
In actual processing, adjustments should be made according to actual conditions to achieve the best processing effect. For example, when processing materials with higher hardness, the cutting speed and feed speed should be appropriately reduced to avoid tool wear and damage; when processing materials with lower hardness, the cutting speed and feed speed can be increased to improve processing efficiency.
(2) Control vibration during processing
During the processing of horizontal milling machines, vibration often occurs due to the action of cutting force, affecting processing accuracy and quality. In order to reduce vibration, a variety of methods can be used.
For example, the cutting force can be changed by adjusting the cutting parameters to reduce vibration; a shock absorber can be added to the machine tool table to reduce the impact of vibration on the machine tool; and vibration suppression technology can be used to suppress vibration by controlling factors such as the cutting force action time, action position and force magnitude.
(3) Accurate control of tool path
Accurate control of tool path is one of the core technologies of horizontal milling machine processing technology. In actual processing, the tool path should be accurately calculated and designed based on factors such as the size, shape and precision of the processed parts. At the same time, the impact of factors such as tool wear and coolant use on the tool path should also be considered.
In actual operation, accurate control of tool path can be achieved by using advanced computer-aided design and manufacturing technology (CAD/CAM) and high-precision CNC systems.
(4) Optimizing the use of coolant
Coolant plays an important role in horizontal milling machine processing. It can effectively reduce cutting temperature, reduce tool wear and workpiece deformation, and improve processing efficiency and quality.
In actual processing, the appropriate coolant type, flow rate and pressure should be selected based on factors such as the processed material, tool type and processing accuracy.
At the same time, attention should also be paid to the use of coolant. For example, the coolant can be sprayed directly into the cutting area to improve the cooling effect; the coolant can also be sprayed into some parts of the machine tool to reduce the temperature of the machine tool; the coolant can also be concentrated and used in a circulation system to improve the cooling effect and processing efficiency.
In short, choosing the right tool and cutting parameters, controlling vibration during processing, accurately controlling the tool path, and optimizing the use of coolant are the key links to improve the processing accuracy and quality of horizontal CNC milling machines. In actual processing, adjustments and optimizations should be made according to actual conditions to achieve the best processing effect.
6.Application areas of horizontal milling machine processing
Aerospace: used for machining structural parts and engine parts that require extremely high precision and rigidity.
Mold manufacturing: especially suitable for processing large molds, such as automotive stamping molds.
Heavy industry: used to manufacture large machinery and equipment parts, such as generators and large transmission systems.
7.Summary
Horizontal milling machines excel in producing extremely high-precision parts and large parts, and can also select appropriate operations to achieve complex shapes and features in your project. Each operation provides unique advantages and functions for creating specific geometric shapes. Furthermore, advanced machines are essential to perform these various operations efficiently so that the exact desired results can be achieved.
If you are looking for an experienced CNC horizontal milling manufacturer, Xavier is the ideal choice. The Xavier team is well-equipped to provide high-quality CNC horizontal milling solutions. If you require more information or would like to discuss your milling needs with us, please feel free to contact us.