3-axis, 4-axis, and 5-axis CNC machining: How to choose
Choosing the right type of CNC machining machine is one of the most critical decisions before a project begins. It determines the design, cost, and final result of the project. Which one should I choose among 3-axis, 4-axis, and 5-axis CNC machining? Which one is the best option? With such questions, we officially enter the reading of this article.
This guide will comprehensively compare the working principles, processing differences, and advantages and disadvantages of 3-axis, 4-axis, and 5-axis CNC machining.
1.What are 3-axis, 4-axis, and 5-axis CNC milling?
(1) 3-axis CNC milling
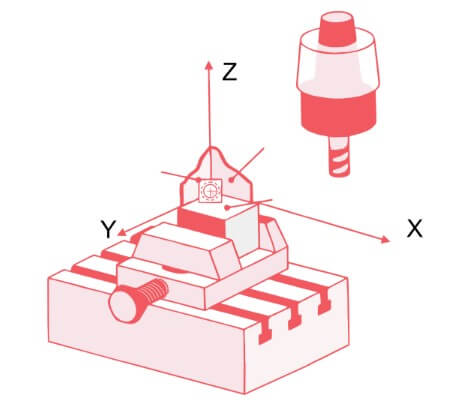
In 3-axis CNC milling, the cutting tool can move along the X, Y, and Z axes. This is the most basic type of milling and is suitable for producing simple, flat parts with relatively straight edges. However, it has limited ability to produce complex shapes and curves.
(2) 4-axis CNC milling
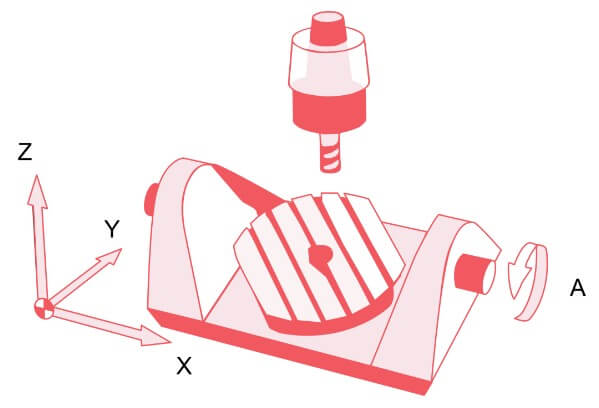
In 4-axis CNC milling, the cutting tool can move along the X, Y, and Z axes, as well as an additional rotational axis (called the A-axis). This allows for the production of more complex parts, such as parts with curved surfaces or angled features. 4-axis milling is often used in industries such as aerospace and automotive that require parts with complex shapes and angles.
(3) 5-axis CNC milling
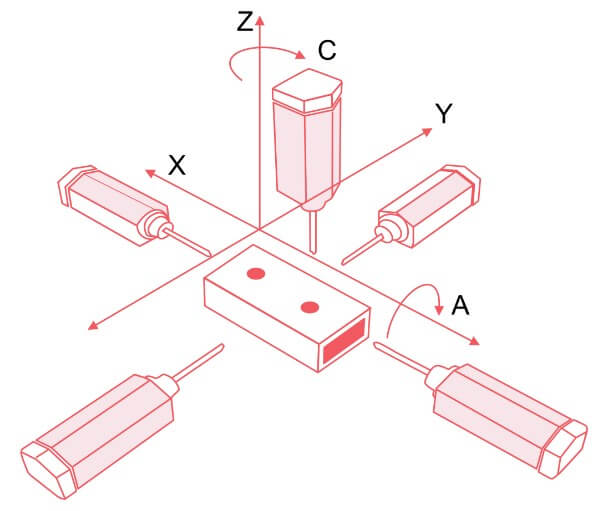
In 5-axis CNC milling, the cutting tool can move along the X, Y, and Z axes, as well as two additional rotational axes (called the A-axis and C-axis). This allows for more complex parts that can be produced, including parts with highly contoured surfaces and intricate details. 5-axis CNC milling is often used in industries such as medical, dental, and jewelry that require highly detailed and precise parts.
2.Working Principles of 3-axis, 4-axis, and 5-axis CNC Machining
(1) 3-axis CNC Machining
3-axis CNC machining involves multiple steps, from part design in CAD software to the actual machining process. Here’s how it works:
- Computer-Aided Design (CAD) and Computer-Aided Manufacturing (CAM): The first step in 3-axis CNC machining is to design the part in CAD software. Once the design is complete, it is converted into a format that the CAM software can read.
- Generate G-code: The CAM software generates G-code, which is a series of instructions that the CNC machine can understand. The G-code contains information about tool paths, speeds, and cutting depths.
- Load the G-code into the CNC controller: The G-code is loaded into the CNC controller, which is responsible for interpreting the code and controlling the movement of the machine.
- Set up the machine: The workpiece is loaded onto the table and secured in place. The cutting tool is also mounted and secured in the spindle.
- Execute the program: Once the machine is set up, the program is executed. The CNC controller reads the G-code and moves the machine along the X, Y, and Z axes to create the desired shape.
- Post-processing and inspection: After the machining process is completed, the part is checked for accuracy and any necessary post-processing steps are performed.
(2) 4-axis CNC machining
All CNC machining works on the same principle. A computer-guided tool rotates around the workpiece to remove material. In addition, all CNC machines use M-codes or G-codes to decipher the tool’s movement relative to the workpiece.
The difference lies in the additional ability to rotate around different planes. Both 4-axis and 5-axis CNC milling allow for rotation around different coordinates, a quality that results in the creation of more complex shapes with relative ease.
4-axis CNC machining works by adding a rotational axis (called the A-axis) to the traditional X, Y, and Z axes. The A-axis allows the machine to rotate the part being machined, which enables more complex cuts and contours to be made with greater precision.
This greatly increases the precision and flexibility of the manufacturing process.
(3) 5-axis CNC machining
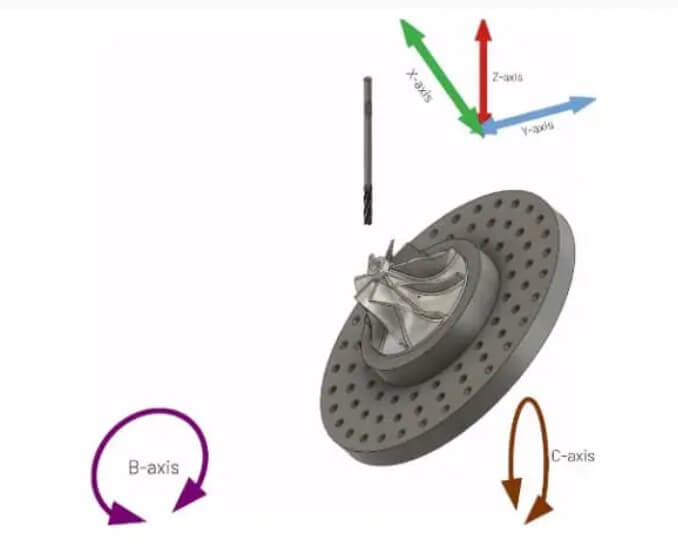
The 5-axis CNC machining process is also very similar to the 3-axis and 4-axis CNC machining processes. However, it has some very important features that provide these two additional axes and greater cutting flexibility.
In 5-axis CNC machining, the spindle and tool move along three axes. However, there are additional rotations for the X-axis (called the A-axis), the Y-axis (called the B-axis), and the Z-axis (called the C-axis). 5-axis machines can use any two of these rotational axes, depending on their configuration.
5-axis CNC machining is used in different capacities based on this functionality. It can perform operations such as milling, turning, etc. Therefore, you can process multiple parts with just one machine.
3.Differences between 3-axis, 4-axis, and 5-axis CNC machining
(1) Flexibility
3-axis has no additional axis, 4-axis CNC machining has one additional axis, the A-axis, while 5-axis CNC machining has two additional axes, which can be the A-axis, B-axis, or C-axis, depending on the configuration. 4-axis CNC machining allows rotation on the A-axis, while 5-axis allows rotation on two of the three axes (A-axis, B-axis, and C-axis).
(2) Accuracy and Precision
All 4-axis and 5-axis machines can move their cutting tools in more ways and at more angles than 3-axis machines. This allows for more complex machining operations and greater precision, and can eliminate the need for multiple setups. Also, it is important to note that this error range for 3-axis CNCs is negligible. However, for sensitive applications such as aerospace and automotive applications, even the smallest deviations can cause problems.
(3) Cost
Cost is one of the main differences between 3-axis, 4-axis, and 5-axis CNC milling. It is naturally more economical to purchase and maintain a 3-axis machine. However, the expense of using them depends on factors such as fixtures and operator availability.
On the other hand, 4-axis and 5-axis machining technology is more advanced and has better performance. Therefore, they are naturally expensive. However, they bring a lot of features and are viable options in many unique situations.
(4) Application
Neither 3-axis, 4-axis, nor 5-axis are industry-wide applications. The difference in CNC type is related to the nature and difficulty level of the product. The differences between 3-axis, 4-axis, and 5-axis milling products will be based on the overall complexity of the design, rather than simply on a particular industry. For example, simple parts in the aerospace field can be developed on 3-axis machines, while some complex parts in other fields may also require the use of 4-axis or 5-axis machines.
(5) Lead time
3-axis CNC machining machines have the longest lead time because cutting is done in stages. In addition, the limitations of 3-axis machines mean that the workpiece requires a lot of repositioning, which will increase the overall lead time of any project.
4-axis CNC machining machines have medium lead times because they allow rotation on one axis and can only process flat angle features at a time.
5-axis CNC machining machines have the best overall effect and the fastest lead time because they have no stoppages and single-step processing. They can even process the most complex shapes in the shortest time with multi-axis linkage.
4.Which is better: 3-axis, 4-axis, or 5-axis CNC machining?
3-axis, 4-axis, and 5-axis each have their advantages and disadvantages. In manufacturing, there is no absolutely better way or one-size-fits-all solution. The right choice depends on the complexity of the project, the overall budget, time and quality requirements.
(1) Advantages and disadvantages of 3-axis CNC machining
Advantages:
1.Affordable
Affordability is one of the main advantages of 3-axis CNC machining over 4-axis or 5-axis systems. In addition, they tend to be easier to program and operate, requiring less extensive training for employees. Ultimately, running costs can be reduced in this way.
2.Accurate and repeatable
The dimensional accuracy and repeatability of parts machined on 3-axis CNC machines are also very high. It will consistently and completely produce products with the same accuracy. Therefore, such aspects are very suitable for large-scale production.
3.Simple geometry
3-axis machining is very suitable for parts with simple geometries. It can effectively handle cutting such as pockets, slots, holes and contours through simple paths.
4.Sturdy and stable
3-axis CNC machines have a simple, rigid design. With fewer moving parts, there is less possibility of instability or vibration during machining. This helps the cutting tool achieve clean, accurate cutting and good surface finish.
Disadvantages:
1.Relatively low productivity
The limited capabilities and increased difficulty of 3-axis machining ultimately mean reduced productivity. When a part requires frequent repositioning or multiple setups to complete all features, it takes more time to actually cut the material.
2.Limited materials
3-axis machining also limits the types of materials that can be cut. Softer materials such as aluminum and plastics are well suited to 3-axis methods, but harder materials require more advanced equipment. Machining steel, titanium or nickel alloys on a basic three-axis machine is difficult and time-consuming, and the results are not good.
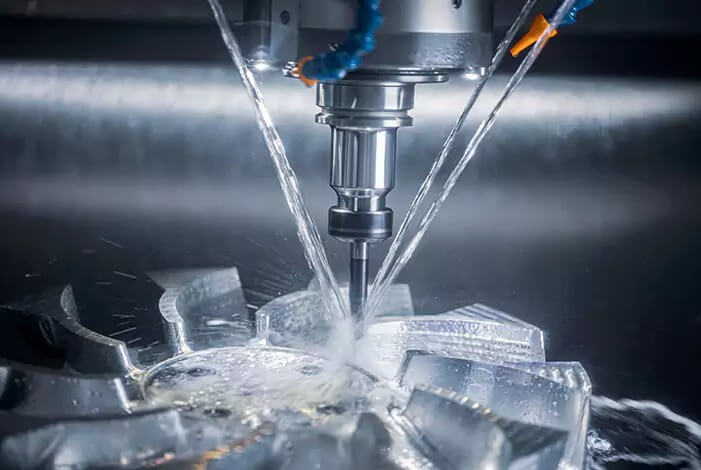
(2) Advantages and disadvantages of 4-axis CNC machining
Advantages:
1.Greater flexibility
Four-axis machining provides greater flexibility in creating shapes and forms. The ability to efficiently machine parts with contours, curves and complex geometries such as impellers, turbine blades and propellers.
2.Reduced setup time
With 4-axis machining, you can machine multiple part features in a single setup. This reduces the number of setup changes required, thereby reducing production time and labor costs. Multiple operations such as milling, drilling, and tapping can be performed on one machine.
3.Increased productivity
Four-axis machining can improve productivity in a variety of ways. The ability to machine complex parts in a single setup reduces non-cutting time. More efficient tool paths also mean shorter cycle times. Since 4-axis machining can produce higher quality parts with tighter tolerances, fewer defective products and less rework time are required. Overall, 4-axis machining can significantly speed up production and reduce manufacturing costs.
Disadvantages:
1.Single rotation direction of the rotary axis
The fourth rotary axis can only rotate the part within a single horizontal plane. This means that projects such as undercuts, contours, and complex geometries that require movement in multiple planes at the same time are not allowed. If you need to machine parts with complex, curved shapes or contours, a four-axis machine may be difficult.
2.Obstructed tool access
The location of the four-axis machine’s rotary table or trunnion mounting to fix the workpiece may hinder the access of some tools. When the part is repositioned, the tool must be able to reach and touch all required areas. Some machine configurations and workholding may limit the tools that can be used.
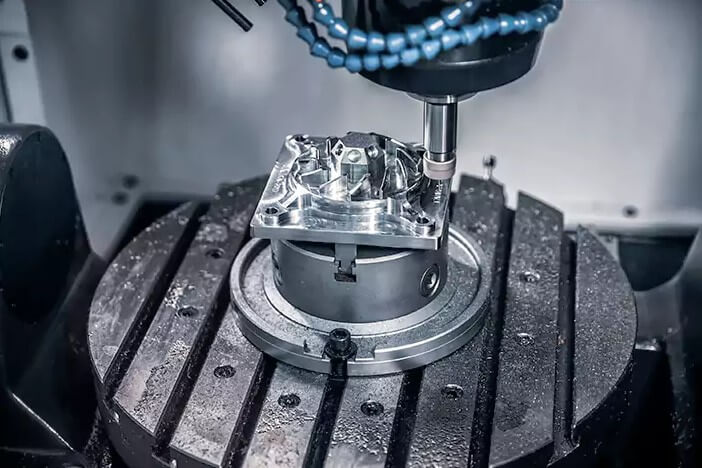
(3) Advantages and disadvantages of 5-axis CNC machining
Advantages:
- Increased geometric flexibility
You can create organic sculptured shapes that were previously difficult to make.
- Improved part accuracy
The multi-directional approach means fewer setups and workpiece repositioning, resulting in fewer errors.
- Improved machining efficiency
Shorter tool paths, single setup operations, and less material waste can reduce total cycle time.
- Less manual programming
Advanced CAM software can automatically generate optimized 5-axis tool paths, minimizing manual programming.
- Higher quality surface finish
Multi-axis cutting capabilities provide more uniform tool loads and cutting, resulting in better part surface quality.
Disadvantages:
- Expensive
5-axis machines are more complex, so they tend to be much more expensive than 3-axis or 4-axis CNC machines.
- Complex operation
Additional axes require more advanced programming to control the machine, so you need software and employees with appropriate capabilities, experience and testing to supervise and support them
- Long cycle time
5-axis machining may require multiple tool changes to complete all the necessary cuts.
In summary, there is no answer to the question of which one is the better choice. You can only choose a balanced machining method between cost, time and results based on your project.
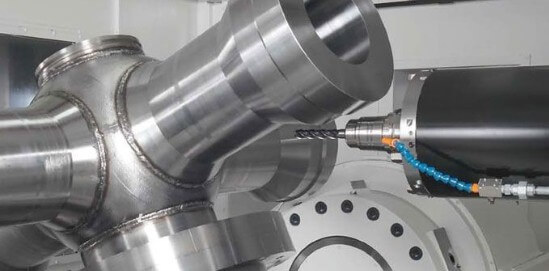
5.Summary
Now you have learned the main differences between 3-axis, 4-axis, and 5-axis CNC machining. Although 3-axis can complete the work of many parts, 4-axis or 5-axis opens new doors in manufacturing. In the end, you only need to comprehensively evaluate your production needs and budget based on the key points in this article to come up with which 3-axis, 4-axis, and 5-axis CNC machining is the ideal machining solution.
If you are looking for an experienced CNC machining manufacturer, Xavier is your ideal choice. The Xavier team is well-equipped to provide high-quality CNC machining solutions. If you need more information or to discuss your machining needs with us, please feel free to contact us.