Rubber Molding Best Practices
Rubber molding products are widely used in various industries, from insulation protection to wear-resistant parts to sealing devices. Rubber molding products have become the choice of various companies due to their unique properties. As a key manufacturing process, rubber molding covers a wide variety of methods. In this article, we will explore the three main rubber molding methods: injection molding, compression molding, and transfer molding, and lead readers to fully understand the secrets of rubber molding.
1.Basic Introduction to Rubber Molding
Rubber molding is a crucial process in rubber manufacturing. It uses metal molds to transform rubber raw materials into final plastic products. This process involves filling the mold cavity with rubber and then molding it into the desired shape by applying pressure and heat. The entire process is carried out under the strict supervision of professionals.
The reason why rubber molding has become a darling in the industrial field is due to its efficiency and cost-effectiveness. It can produce parts with extremely high precision and excellent mechanical properties, so it is widely used in various industries.
2.Rubber Injection Molding
1)Process
Rubber injection molding is similar to plastic injection molding, specifically for processing uncured rubber. Uncured rubber strips are fed into the machine through a hopper, where they are heated and compressed in the screw cavity by an external heater and screw movement. As the rubber approaches the end of the screw, it is highly fluid and is then injected into the mold at high pressure to fill the cavity in the mold. After injection, the mold cools, the rubber solidifies, the mold opens, and the finished product is ejected in preparation for the next cycle.
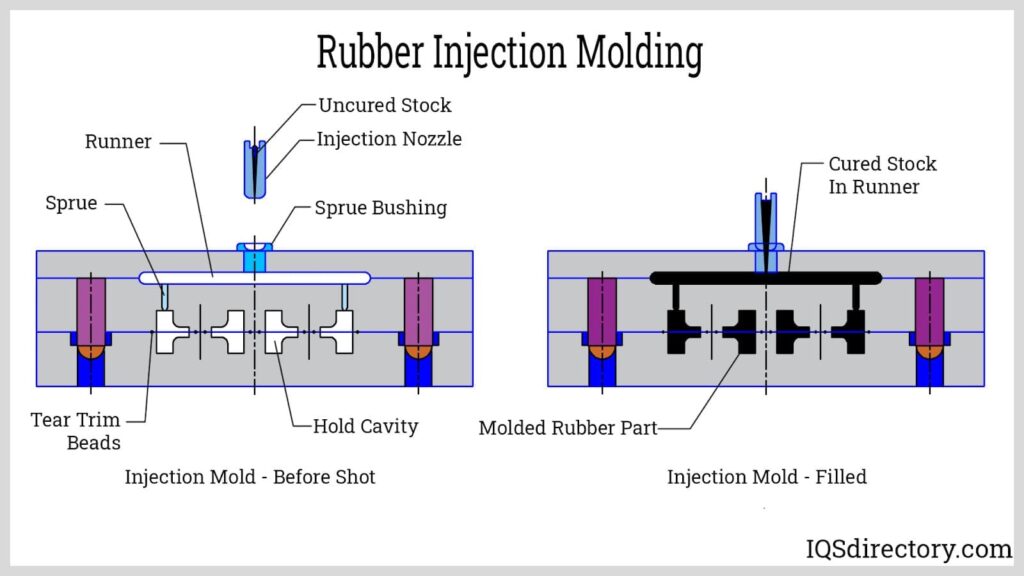
2)Advantages
High precision: Pressurized injection combined with the flow characteristics of rubber ensures accurate mold filling and produces high-precision products.
Complex geometry: Designs with complex features such as holes, curves, and sharp contours can be produced, and the mold cavity design is flexible and can include elements such as cores.
High mechanical strength: Pressure applied during the molding process and sufficient curing time give rubber molded parts excellent mechanical strength and durability.
Minimum finishing required: Rubber molded products have few post-processing defects or excess material, and the finished product is close to the final shape except for parting lines and gate marks.
Efficient process: Modern control technology precisely controls the heat and pressure of the injection molding machine. Optimizing the process can shorten the curing cycle and save time.
Economy of scale: In addition to the initial mold cost, the molding cost per product is low, which is suitable for large-scale production.
3)Disadvantages
Material restrictions: The requirement for rubber to have good flow properties limits the range of raw material selection, but most rubber materials can still be processed.
High initial cost: The cost of tools and machinery is high, and small batch production may not be economical.
3.Rubber Compression Molding
1)Process
he mold used for compression molding consists of two halves, each containing part of the cavity. The uncured raw material (charge) is preheated and placed in the lower half of the mold, and the two halves of the mold are also preheated. Then, the movable part of the mold (plug) is lowered into the fixed mold, and pressure is applied to make the material take the shape of the mold cavity. The mold is then heated to cure the rubber and finally the finished product is obtained.
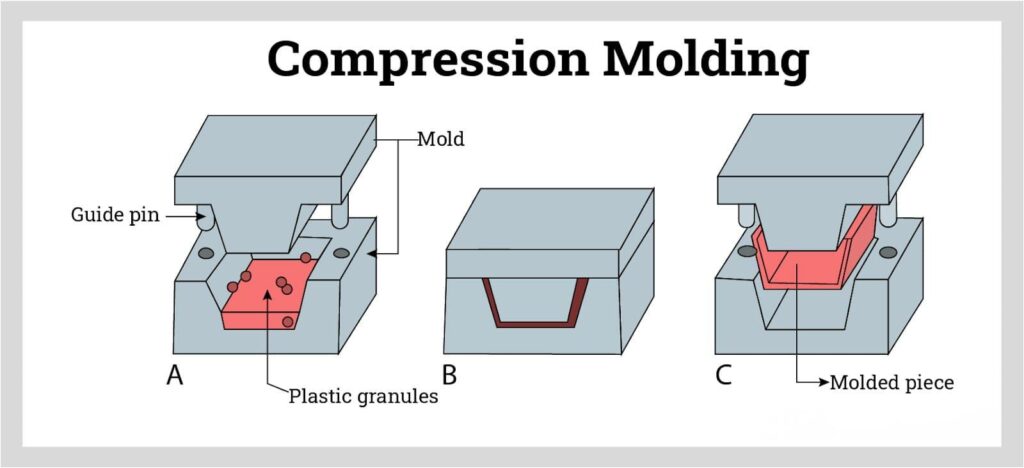
2)Advantages
Low cost: simple design, low tooling cost, and when the production volume increases, the production cost is also reduced.
Low maintenance cost: the mold design is simple, there is no complex gate network, and it is easy to clean, repair and polish, with low maintenance time and cost.
Material type: It can adapt to a variety of rubber materials and does not rely on material flow like injection molding.
No gate marks: The mold has no gates, the product has no gate residues, the appearance is high, and the finishing operation is reduced.
3)Disadvantages
Dimensional tolerance: The accuracy is not as good as injection molding, and deviations from the mold cavity may occur, especially in curvature or concave areas.
Finishing: Although there are no signs of gates, it is still necessary to remove the flash and parting lines and perform finishing operations.
4.Rubber Transfer Molding
1)Process
Rubber transfer molding uses a specific mold design. The mold consists of two halves. The upper half has an open cavity (tank), and the gate network connects the tank to the main cavity. The preform is placed in the tank, and high pressure and heat are applied by the plunger to “transfer” it to the cavity. After the raw materials are cured, cooled, and vulcanized, the finished product is demolded.
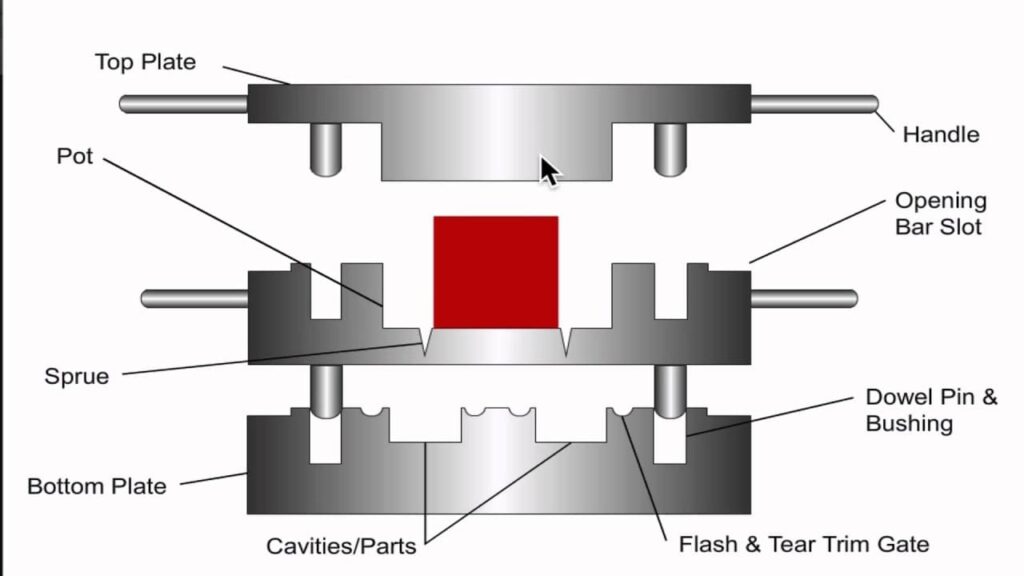
2)Advantages
Strict tolerances: Excellent dimensional tolerances can be achieved, suitable for manufacturing precise part geometries.
Metal bonding: Good bonding effect on rubber and metal, convenient for the production of metal-rubber combination brackets and other components.
Large parts: The mold design can accommodate large cavities and can produce larger rubber molded parts.
Many cavities: The preform has a simple shape, less preparation work, and can be reused, saving time and energy.
3)Disadvantages
High mold cost: The mold has additional features such as tanks and gates, which are complex to design and manufacture and have high initial costs.
Finishing: Due to the existence of the gate network, excess material needs to be removed for deburring operations.
Long cycle time: The curing time is longer than other molding processes and needs to be considered in applications with high cycle time requirements.
5.Material selection for rubber molding
1)Common rubber materials
1.Natural rubber (NR): Extracted from rubber trees through a “lap” process, it has high strength, high elasticity and high stretchability. It can be used alone or mixed with other compounds, often in the form of latex.
2.Styrene-Butadiene Rubber (SBR): Synthetic rubber that resists abrasion, is durable, resists compression set, and can withstand water expansion for demanding applications.
3.Neoprene: Synthetic rubber that maintains mechanical properties over a wide temperature range and is used in engine fluid pipes and friction belts, etc. It has high chemical stability and corrosion resistance.
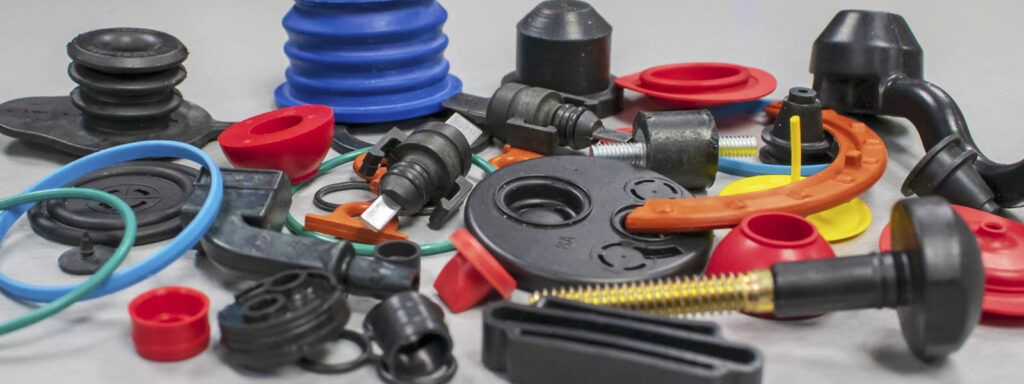
4.Nitrile Butadiene Rubber (NBR): High-performance rubber with good compression set and mechanical integrity, and resistance to chemical degradation such as oil and gas, making it ideal for sealing components.
5.Butyl Rubber (IIR): Known for its flexibility and air-impermeability, favored by sealant companies.
6.Fluoroelastomer rubber: highly resistant to liquid penetration and suitable for applications that are resistant to water, oxygen, ozone and other liquids.
7.Silicone rubber: has excellent properties such as biocompatibility, fire resistance, ozone impermeability and various color options.
2)Considerations in selecting appropriate materials
1.Material properties: Rubber properties such as strength, durability, abrasion resistance, and impermeability to specific fluids should be consistent with the final product requirements. Factors such as high temperature resistance, chemical compatibility, and mechanical load-bearing capacity should also be considered.
2.Industrial applications: The application environment of the final product is critical to material selection. Different rubber materials are suitable for different environments, such as high temperature, high humidity, chemical exposure and specific loading conditions.
3.Budget: Budget constraints are an important consideration. Some rubber materials are high-cost but perform well, while others are more economical but may compromise in some aspects. A balance needs to be struck between cost and quality.
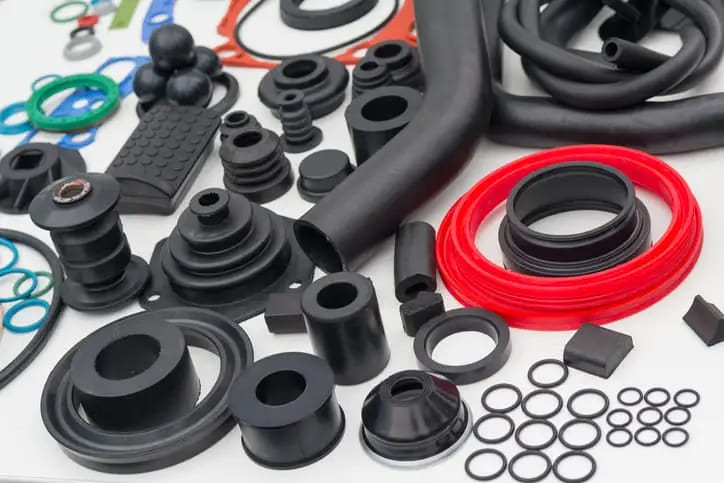
6.Rubber molding applications
Rubber molding products are widely used in industry
1.Rubber O-rings: One of the most common rubber molding products. It plays a key role in fluid sealing applications, such as piston cylinder assemblies. Different rubber materials are selected according to different requirements.
2.Rubber sealing rings: Suitable for a variety of occasions, with various shapes and sizes, can be used for leak-proof flange joints, bellows, ventilation ducts, etc.
3.Rubber gaskets: It is an essential component for high-pressure sealing in automobiles. It can be customized according to needs and used to seal key areas such as engine cylinders.
4.Rubber tubes: Used as fluid conveying conduits, can be used for the pipe itself or as a coating for other materials, with leak-proof and heat-insulating properties, such as commonly used in household plumbing systems in colder areas.
5.Rubber bearings: The damping properties of rubber make it an ideal material for suppressing vibrations. Heavy machinery often uses rubber bearings to extend service life and improve performance, such as CNC machine tools.
Summary
Rubber molding, from injection molding, compression molding to transfer molding, each process has its own unique features; from natural rubber to various synthetic rubbers, different materials have their own characteristics. In practical applications, by comprehensively considering factors such as material properties, industrial application requirements and budget, the most suitable rubber molding solution can be selected to produce high-quality rubber products that meet various needs.