High-speed milling: the acceleration engine of modern manufacturing
High-speed milling (HSM) is an important and efficient processing technology in modern manufacturing. It achieves high-efficiency and high-precision processing effects by increasing the rotational speed and feed rate of milling cutters. With its unique advantages, high-speed milling is gradually becoming the preferred processing method in many industries, especially aerospace, automobiles, mold manufacturing and precision instruments.
This article will deeply explore the basic principles, processing processes, technical characteristics, applications in mold manufacturing and other fields, and future development trends of high-speed milling.
1.Principle of high-speed milling processing
High-speed milling is a milling strategy that utilizes high speed, small depth of cut, and fast feed to achieve efficient and high-precision processing by reducing cutting force, lowering cutting temperature, and increasing material removal rate.
The processing principles of high-speed milling mainly include the following aspects:
(1) Cutting mechanism
During high-speed cutting, the contact time between the milling cutter and the workpiece is extremely short, and the cutting force is significantly reduced. This helps reduce the deformation of the workpiece and the generation of cutting heat, and improves machining accuracy and surface quality.
(2) Cutting parameters
High-speed milling uses small cutting depth and fast feed speed, which makes the cutting process more stable and the cutting force fluctuation is small, which is beneficial to extending the tool life.
(3) Cooling and lubrication
Due to the high cutting speed, it is difficult for traditional cutting fluids to effectively enter the cutting area, so dry cutting methods using oil and gas cooling and lubrication are often used. This method can effectively reduce cutting temperature and improve tool life and processing quality.
2.High-speed milling process
The high-speed milling process mainly includes the following steps:
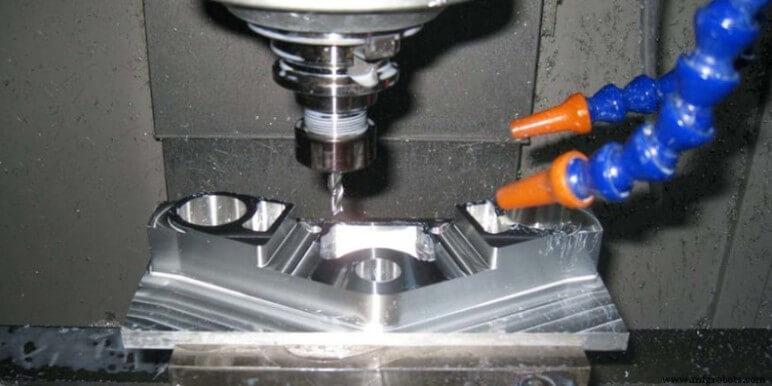
(1) Machine tool preparation
Choose machine tools with high rigidity, high stability and high precision to ensure stability and precision during processing.
(2) Tool selection and clamping
Select the appropriate milling cutter type and specifications according to the processing materials and processing requirements. At the same time, a high-rigidity and high-precision tool clamping method is used to ensure the stability of the tool under high-speed rotation.
(3) Cutting parameter settings
According to the processing materials and machine tool performance, cutting parameters such as cutting speed, feed amount and cutting depth are reasonably set to ensure processing efficiency and processing quality.
(4) Process monitoring
During the machining process, the CNC system monitors the machining process in real time and adjusts cutting parameters and tool paths in a timely manner to ensure the stability and accuracy of the machining process.
(5) Post-processing treatment
After the processing is completed, the workpiece must be cleaned and inspected as necessary to ensure that the processing quality meets the requirements.
3.Characteristics of high-speed milling processing technology
(1) Efficient processing
High-speed milling significantly improves the material removal rate and shortens the machining cycle by increasing the cutting speed and feed rate.
(2) High precision
Due to the small cutting force, small heat-affected zone and small deformation of the workpiece, higher machining accuracy and surface quality can be achieved.
(3) Wide applicability
It is suitable for processing a variety of materials, including carbide, titanium alloy, aluminum alloy, composite materials, etc., and performs particularly well in processing difficult-to-machine materials.
(4) Flexibility
Combined with CAD/CAM technology, high-speed milling can easily cope with the processing needs of complex shapes and curved surfaces, achieving “one clamping, complete processing”.
(5) Environmental protection and energy saving
Due to the high efficiency of the cutting process, the use of cutting fluid and the generation of waste materials are reduced, which is conducive to environmental protection, energy conservation and emission reduction.
4.Application of high-speed milling processing
High-speed milling has been widely used in mold manufacturing, aerospace, automobile manufacturing and other fields. The following are some typical application examples:
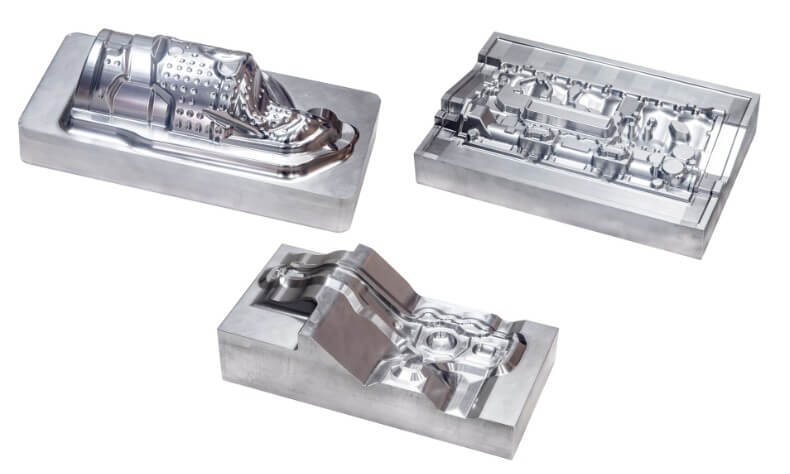
(1) Mold manufacturing
In mold manufacturing, high-speed milling can be used to process complex curved surfaces such as mold cavities and punches. By optimizing cutting parameters and tool path planning, high-efficiency and high-precision mold processing can be achieved, significantly shortening the mold manufacturing cycle and reducing manufacturing costs.
(2) Aerospace
In the aerospace field, high-speed milling can be used to process high-precision, high-complexity parts such as aircraft engine blades and fuselage frames. These parts have extremely high requirements for machining accuracy and surface quality. It can meet these requirements and improve the reliability and performance of the parts.
(3) Automobile manufacturing
In automobile manufacturing, high-speed milling can be used to process parts such as automobile panel molds and engine blocks. By improving processing efficiency and processing quality, it helps shorten the automobile manufacturing cycle, reduce manufacturing costs, and improve the market competitiveness of automobiles.
5.Application advantages of high-speed milling
(1) Shorten the product development cycle
The rapid processing capability of high-speed milling greatly shortens the cycle from product design to production and accelerates the speed of product launch.
(2) Reduce costs
Although the initial investment in high-speed milling equipment is relatively high, in the long run, the overall cost is effectively controlled due to increased production efficiency and reduced scrap rates.
(3) Improve product quality
High-precision processing capabilities ensure the dimensional accuracy and surface quality of products, improving the market competitiveness of products.
(4) Promote technological innovation
The continuous development of high-speed milling technology has promoted the application of new materials and new processes, and promoted technological innovation in the manufacturing industry.
6.Advantages of high-speed milling compared with ordinary milling
The core of high-speed milling is to increase the rotational speed and feed rate of the milling cutter to remove a large amount of material in a short time. Compared with ordinary milling, the cutting speed of high-speed milling can be increased several to dozens of times, and the feed rate is also significantly improved. This high-speed cutting not only reduces cutting time, but also reduces cutting force and cutting heat, thereby improving machining accuracy and surface quality.
High-speed milling has the following advantages over ordinary milling:

(1) Efficient
The spindle speed of high-speed milling is generally 15000r/min ~ 40000r/min, and can reach up to 100000r/min. When cutting steel, the cutting speed is about 400m/min, which is 5 to 10 times higher than traditional milling;
(2) High precision
The precision of high-speed milling is generally 10μm, and some precisions are even higher.
(3) High surface quality
Since the temperature rise of the workpiece is small (about 3°C) during high-speed milling, there is no deterioration layer and micro-cracks on the surface, and the thermal deformation is also small. The best surface roughness Ra is less than 1μm, which reduces the workload of subsequent grinding and polishing.
(4) Can process high-hard materials
It can mill steel materials with 50-54HRC, and the highest hardness can reach 60HRC.
7.Future development trends
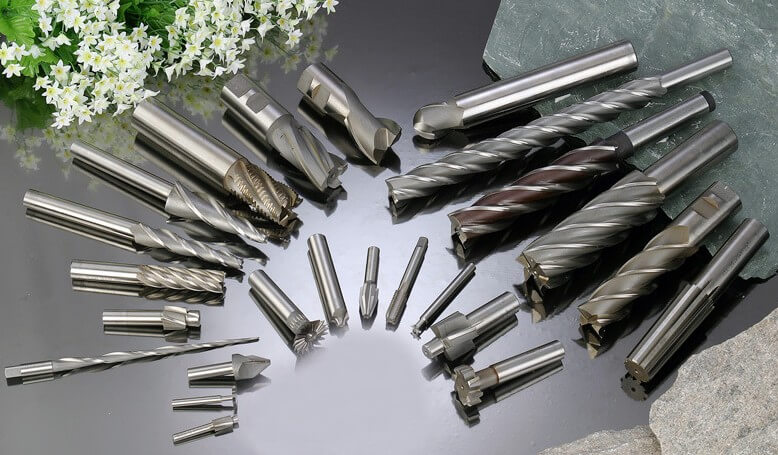
(1) Higher speed and higher precision
With the development of materials science, machine tool design, and numerical control technology, the cutting speed and processing accuracy of high-speed milling will continue to improve.
(2) Intelligence and automation
Combined with the Internet of Things, big data, artificial intelligence and other technologies, this technology will develop in a more intelligent and automated direction, realizing remote monitoring, fault prediction and diagnosis, intelligent dispatching and other functions.
(3) Green manufacturing
The increasing awareness of environmental protection will prompt high-speed milling technology to pay more attention to energy conservation and emission reduction, develop more environmentally friendly cutting fluids, tool materials, and realize the recycling of cutting waste materials.
(4) Multifunctional composite processing
In order to further improve processing efficiency and flexibility, high-speed milling will be combined with turning, drilling, grinding and other processing methods to form a multi-functional composite processing machine tool.
8.Conclusion
To sum up, high-speed milling, as an important technical support for modern manufacturing, is leading the manufacturing industry to develop in a more efficient, precise, and environmentally friendly direction with its unique advantages. In the future, with the continuous advancement of technology and the continuous expansion of application fields, this technology will play an important role in more fields.