Comprehensive comparison between electroplating and electroless plating
Electroless plating and electroplating are two common metal surface treatment methods, playing a key role in improving metal performance and appearance. However, there are many differences between them, and each has its own unique advantages and disadvantages. Understanding these differences and characteristics is crucial to choosing the right surface treatment process. This article will explore the differences between electroplating and electroless plating, their respective advantages and disadvantages, to help you better understand these two technologies.
1.The difference between electroplating and electroless plating
1.Process principle
Electroplating is the process of depositing metal ions on the metal surface being plated by passing an electric current through a solution of dissolved metal ions. Electroless plating, on the other hand, is a chemical process that uses a reducing agent to deposit metal on the metal surface without the use of an electric current.
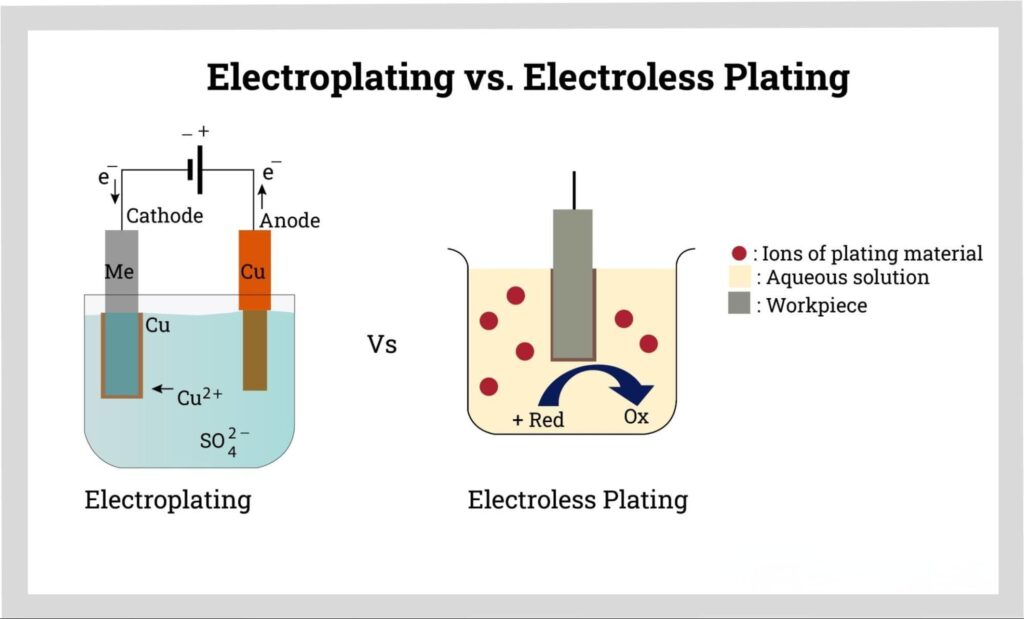
2.Degree of control
Electroplating provides better control over the thickness and uniformity of the metal coating, and can deposit a precise amount of metal on the surface by adjusting the current. In contrast, electroless plating is more difficult to control and may result in uneven coating thickness.
3.Surface treatment requirements
Electroplating requires a clean and conductive surface for the metal coating to adhere properly. Electroless plating can be used on non-conductive surfaces without the same degree of surface preparation.
4.Cost difference
Electroless plating is generally more expensive than electroplating because of the higher cost of the chemicals used in the process.
5.Application range
Electroplating is often used to provide a decorative or protective coating on metal surfaces. Electroless plating is often used to deposit a thin layer of metal on non-metallic surfaces (such as plastics or ceramics).
6.Coating Thickness
Electroless plating typically produces coatings from 0.0001 to 0.002 inches thick, and thickness can be increased by using thicker substrates or applying multiple layers of coating. Electroplating produces coatings from 0.00002 to 0.02 inches thick, and thicker coatings can also be achieved by applying multiple layers of coating.
2.Advantages and Disadvantages of Electroplating
1.Advantages
Enhanced durability: Electroplating can improve the durability and wear resistance of metal surfaces by providing a protective layer of another metal.
Improved corrosion resistance: The resulting coating provides better corrosion protection and extends the service life of metal parts.
Decorative options: Can be used to create decorative finishes on metal parts, such as chrome or gold plating.
Precise control: The thickness and uniformity of the coating can be precisely controlled, allowing for more precise customization.
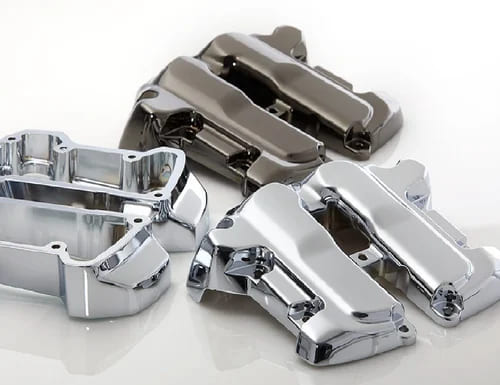
2.Disadvantages
Higher cost: The electroplating process requires specialized equipment and skilled operators, which is costly.
Environmental issues: Toxic waste is generated and needs to be handled carefully to avoid damage to the environment.
High surface preparation requirements: A clean and conductive surface is required for the metal coating to adhere properly, and additional surface preparation steps may be required.
3.Advantages and Disadvantages of Electroless Plating
1.Advantages
Uniform coating thickness: It can produce more uniform and consistent coating thickness than electroplating, improving coating quality and consistency.
Good adhesion: It has better adhesion than electroplating, especially on non-conductive surfaces, and has a wider range of applications.
Strong corrosion resistance: Because the process can produce a dense and uniform coating, it is more corrosion-resistant than electroplating.
Reduced environmental impact: It produces less toxic waste and is a more environmentally friendly choice.
Economical and efficient: Compared with electroplating, it has lower energy consumption and simpler processes, making it an economical and efficient choice for metal surface coating.
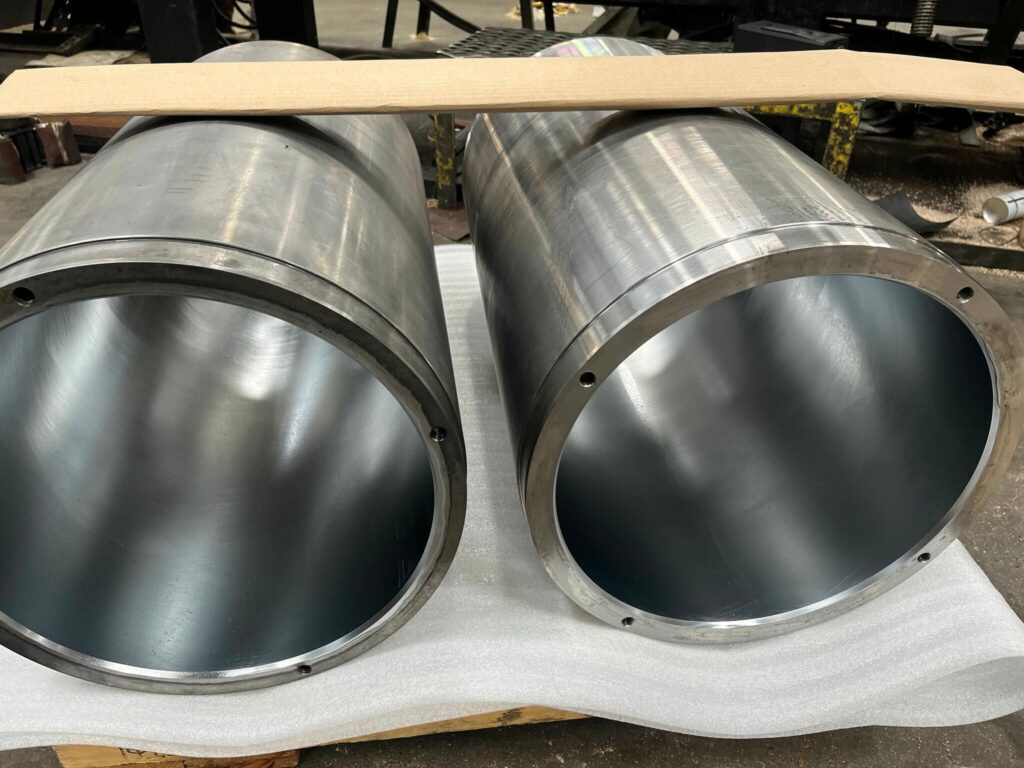
2.Disadvantages
Less precise control: It is more difficult to control than electroplating, resulting in less precise coating thickness and quality.
Long process time: It usually takes longer than electroplating, increasing production time and cost.
Limited metal range: It is usually limited to plating certain metals, such as nickel, gold and copper.
4.Why electroless plating is better than electroplating
1.Uniform coating thickness
Electroless plating produces a more uniform coating thickness than electroplating, which may produce an uneven coating due to current distribution.
2.Better adhesion
Electroless plating has better adhesion on non-conductive surfaces than electroplating, and the absence of an electric current to deposit metal makes it more effective in coating non-conductive surfaces.
3.Strong corrosion resistance
The dense and uniform coating produced by electroless plating can provide better corrosion protection.
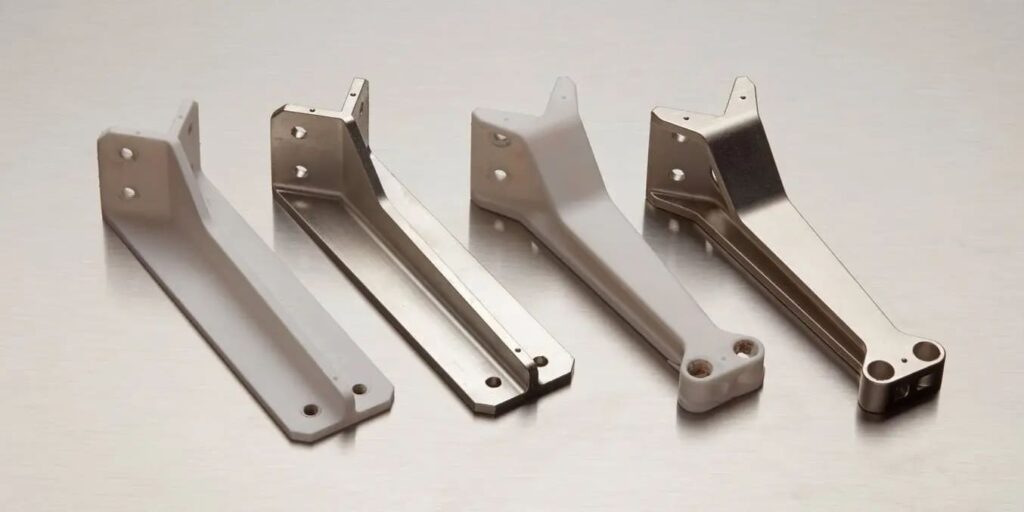
4.Improved durability
Uniform coating thickness provides higher durability and wear resistance.
5.Fewer process steps
Fewer process steps are required than electroplating, making the process simpler and more cost-effective.
Summary
electroplating and electroless plating have obvious differences in process principles, application scope, etc. They each have unique advantages and disadvantages and play different roles in different application scenarios. When choosing a metal surface treatment process, various factors need to be considered comprehensively.