The importance of metal polishing
Metal polishing is an important surface treatment technology, widely used in mechanical processing. Through polishing, the metal surface can glow with amazing luster, improving the beauty and quality of the product. This article will explore the metal polishing process in depth, please read it carefully.
1.What is metal polishing?
Metal polishing is a method of finishing a metal surface by using abrasive materials to remove scratches and nicks on the finished machined part, improving its gloss and giving the treated surface a mirror-like finish.
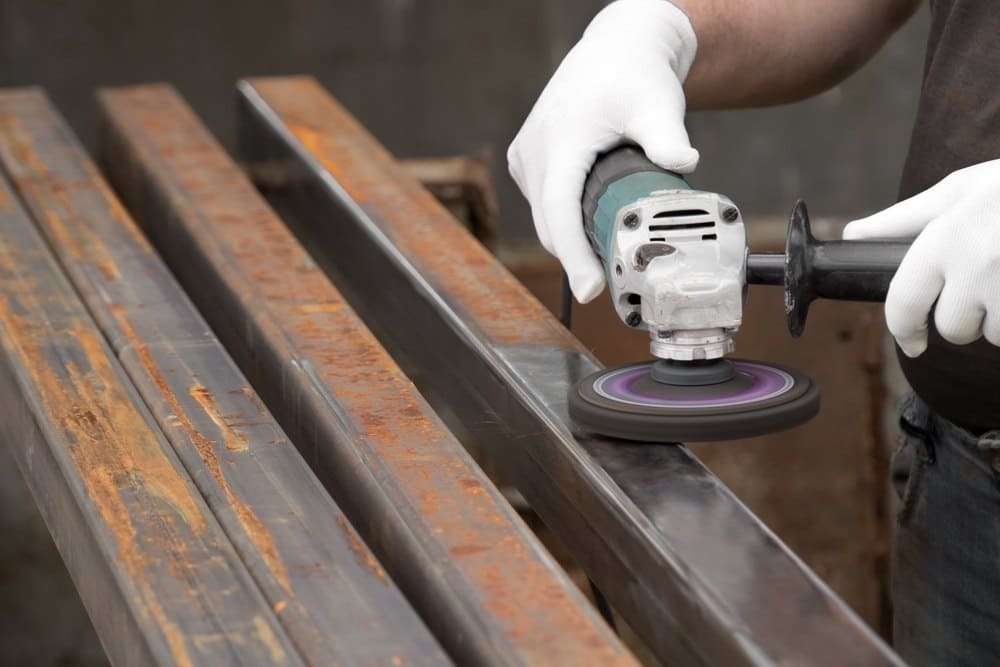
2.Working principle of metal polishing
Usually includes four steps: roughing, polishing, whitening and protection.
Step 1
It is to eliminate scratches and defects on the metal surface. The appropriate abrasive can be selected according to the different surface sizes.
Step 2
Use fast-cutting abrasive paste and wool beret, polishing sponge and other tools to make the surface smoother.
Step 3
In order to restore the initial appearance of the metal surface or even better results.
Step 4
Finally, apply protective wax to enhance the durability of the polished surface.
3.Different types of metal polishing
1)Mechanical polishing
Mechanical polishing mainly relies on plastic deformation or cutting of the metal surface to achieve smooth surface treatment by removing raised areas. In this process, commonly used materials include sandpaper, flat wheels and grinding rods, most of which are suitable for manual operation. However, for situations where high-quality surface treatment is required, ultra-precision technology and auxiliary tools such as turntables are used.
Advantages: It can achieve high-brightness surface effects, greatly improve surface finish, have better surface cleanliness, give products higher aesthetic appeal, and reduce product adhesion.
Disadvantages: High labor intensity, difficult to effectively treat complex parts, the gloss may be more consistent but may not last for a long time, and is easily affected by corrosion.
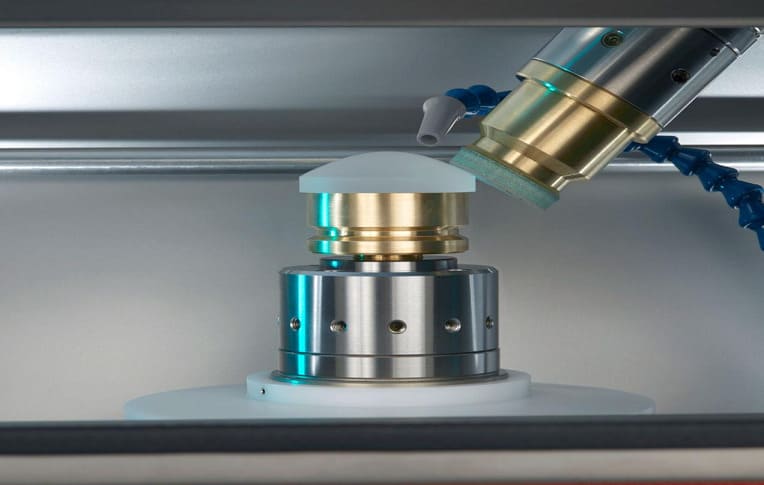
2)Chemical polishing
It is a method of obtaining a smooth surface by selectively dissolving the protruding parts of the material surface in a chemical medium. In this process, chemical solutions and galvanic couples interact with the metal surface, resulting in the formation of a passivation layer. Generally, chemical polishing can effectively eliminate micro-roughness and cause parallel dissolution of the upper layer of the material.
Advantages: It can process workpieces with complex shapes, can process multiple parts at the same time, has relatively small equipment investment, has efficient processing capabilities, and has good corrosion resistance.
Disadvantages: uneven brightness may result, heating treatment is difficult, the process may release harmful substances, and the adjustment and regeneration of polishing liquid are difficult.
3)Electrolytic polishing
Use chemical solution to dissolve the protrusions on the metal surface to make the surface smoother. Unlike chemical polishing, electrolytic polishing does not involve cathode reaction, so its effect is more obvious. This process can effectively remove excess material on metal parts, smooth valleys and micro-peaks, thereby reducing surface roughness and improving overall surface finish.
Advantages: more lasting gloss, consistent color inside and outside, wide range of applications, low cost, short cycle, can encourage pollution reduction, and has high corrosion resistance.
Disadvantages: high equipment investment, complex process, tooling and auxiliary electrodes are required for complex parts.
4.Advantages of metal polishing
1.It can greatly improve the cleanliness of metal parts and effectively prevent dirt and microorganisms from accumulating on the metal surface, making the parts easier to clean and even achieving sterility in some cases.
2.It can significantly enhance the corrosion resistance of parts and provide strong protection for metal parts, allowing them to maintain good condition in various environments.
3.Beautiful: It can ensure that the appearance and smoothness of metal parts are improved, making metal parts more charming.
4.It can also remove impurities on the metal surface, making the metal surface more pure and flawless. Moreover, it can reduce the bonding performance of parts and play an important role in some specific application scenarios.
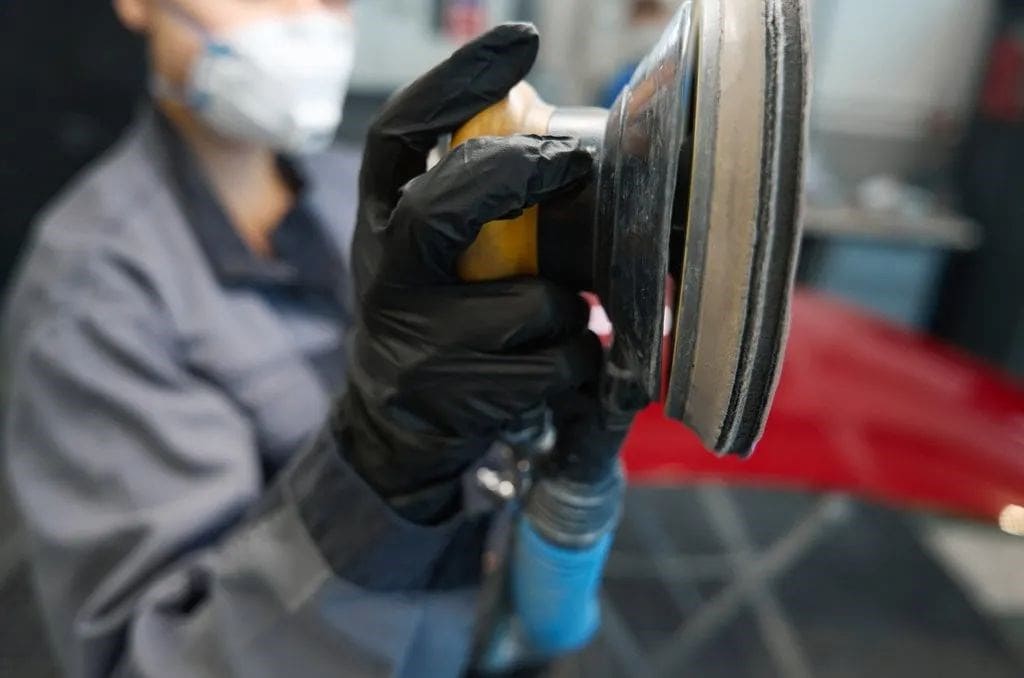
5.Disadvantages of metal polishing
1)Limitations in high-purity applications
Mechanically treated parts may have certain limitations in specific scenarios, especially in applications with extremely high purity requirements, which may not fully meet the requirements. This is because the mechanical treatment process may introduce some tiny impurities or change the surface structure of the material, making its performance in a high-purity environment unsatisfactory. For example, in some precision electronic component manufacturing or high-purity chemical experimental equipment, the purity requirements for materials are extremely strict, and mechanically treated parts may not be suitable.
2)Abrasive and compound residue issues
The abrasives and other compounds used in the treatment process may remain in the material, which is an issue that cannot be ignored. These residual substances may have a multi-faceted impact on the performance of the material. On the one hand, it may affect the chemical stability of the material, making it more susceptible to chemical reactions in a specific environment, thereby reducing the service life of the material. On the other hand, the residual substances may change the physical properties of the material, such as hardness, conductivity, etc., which in turn affects the performance and quality of the entire product.
3)Challenges with greater labor demand
This treatment method may require a lot of labor input during implementation. Since the treatment process is often more complicated, it requires multiple steps and delicate operations, which requires a lot of manpower to complete. Moreover, for some parts with complex shapes or tasks requiring high precision, experienced operators are required to perform meticulous processing, which further increases the demand for labor. A large number of labor demands will not only increase costs, but may also be limited by human resources, which may affect production progress and efficiency in some cases.
6.Application of polishing
The main advantage of the surface is its smoothness, which prevents the accumulation of dirt or microorganisms, making parts easier to clean and even achieve sterility levels. This property makes polished metal surfaces widely used in industries such as medical, aerospace, and electrical.
In the medical field, polished metal parts are often used in the manufacture of medical equipment to ensure the cleanliness and hygiene of the equipment and protect the health of patients.
In the aerospace field, polished metal surfaces can effectively reflect light and play an important role in improving the performance of some key components.
In the electrical industry, polished metal parts can improve the performance and reliability of electrical equipment.
In addition, polished metal parts can also be used in reflectors and mirrors, such as solar concentrators, safety mirrors, etc.; fire truck bumpers to improve their aesthetics and durability; fasteners, springs and steel wire cracks for ships, etc. fields and contribute to the development of various industries.
Summarize
To sum up, the polishing process is an indispensable part of modern industrial manufacturing. It has both artistic beauty and scientific rigor. Different types of metal polishing technologies have their own advantages and disadvantages, and they need to be selected according to the specific requirements of the project in practical applications.