The rise of AI manufacturing
Artificial intelligence (AI) is revolutionizing many industries, and manufacturing is no exception. AI manufacturing is like a shining new star, bringing new opportunities and challenges to the manufacturing industry. With the continuous advancement of artificial intelligence technology, its application in the manufacturing industry is becoming more and more extensive. AI manufacturing is reshaping the manufacturing industry with its unique advantages. This article will deeply explore the application, advantages and future development trends of AI manufacturing in the manufacturing industry.
1.Introduction to AI Manufacturing
AI manufacturing refers to the integration of artificial intelligence software and systems into the manufacturing process to improve efficiency, accuracy and productivity. By leveraging advanced algorithms and machine learning technologies, various aspects of production can be automated, such as monitoring, tracking, predictive maintenance and quality control. AI applications in manufacturing can analyze data in real time, allowing factory managers and IT experts to make quick and informed decisions.
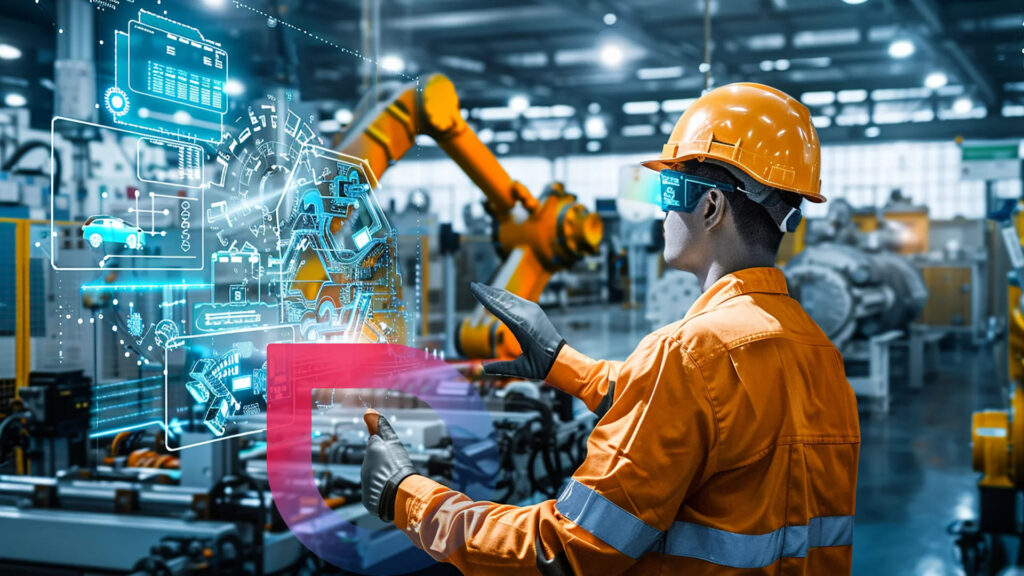
2.Benefits of AI Manufacturing
1.Improve efficiency
AI manufacturing software can streamline repetitive tasks, reducing the time and resources required for manual intervention, allowing human operators to focus on more complex activities.
2.Enhance quality control
Artificial intelligence systems can identify defects and anomalies in real time, ensuring high-quality products move to the next production stage.
3.Predictive maintenance
AI algorithms can predict equipment failures, reduce downtime and extend machine life.
4.Reduce operating costs
Significantly reduce operating costs by optimizing production processes and reducing waste.
5.Real-time monitoring and alerts
Provide real-time monitoring and alerts to detect problems and take action promptly.
3.AI manufacturing software
1.Features of AI manufacturing software
Predictive analysis: Use historical data to predict equipment failures and maintenance needs to reduce downtime.
Real-time monitoring: Continuously track production lines to ensure smooth operation and detect anomalies in a timely manner.
Quality control: Use computer vision to automatically inspect systems to identify defects and inconsistencies.
Supply chain optimization: Use AI algorithms to manage inventory levels, supplier performance, and logistics to ensure on-time delivery.
Demand forecasting: Machine learning models predict future demand and assist in resource allocation and production planning.
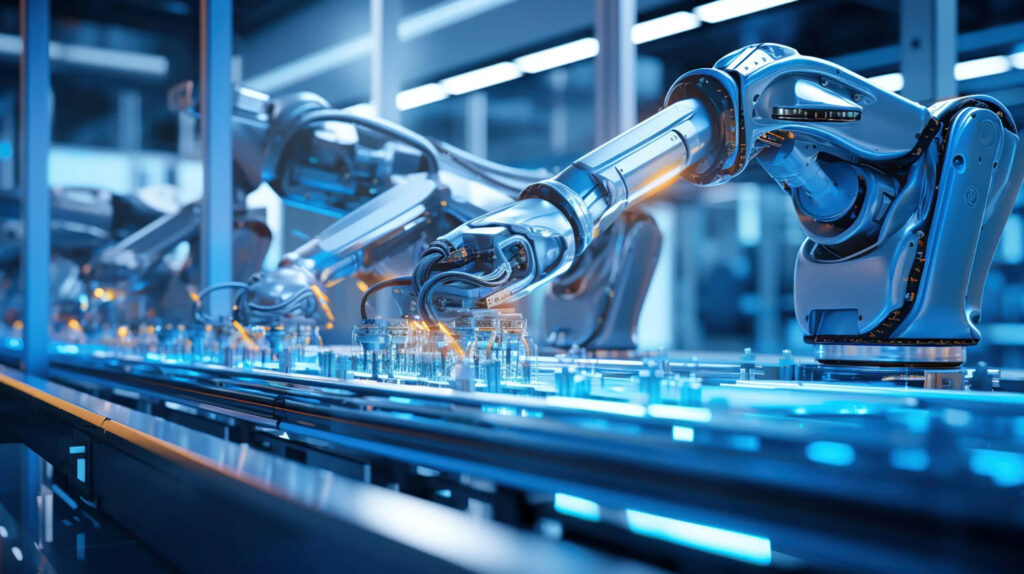
2.Application of AI software in streamlining processes
Equipment health monitoring: AI systems continuously monitor machine health, issue alerts and notifications, perform preventive maintenance, and reduce downtime.
Production tracking: Advanced AI systems track production progress, provide real-time updates and notifications, ensure plan execution and deviation correction.
Energy management: AI solutions adjust power consumption based on real-time data, optimize energy use, and reduce waste and operating costs.
Worker safety: AI-enhanced monitoring systems use sensors and cameras to ensure safety protocols are followed and workplace hazards are reduced.
Logistics and supply chain: AI-driven platforms provide end-to-end visibility into the supply chain, making processes more flexible and responsive.
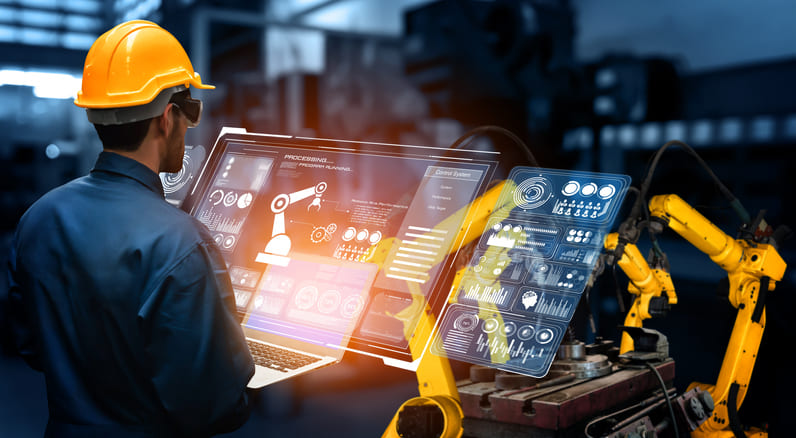
4.Implementation of AI in Manufacturing Plants
1.Challenges and Solutions
Challenges: compatibility with existing infrastructure, data integration and quality, ensuring business continuity, high initial investment.
Solutions: Evaluate AI software that is compatible with existing systems and use middleware solutions; ensure robust data management practices; plan AI deployment in stages; analyze long-term ROI and explore incentives or partnerships.
2.Training and Application
Training needs: comprehensive training programs, ongoing support and resources, simulation-based learning environments.
Adoption strategies: develop detailed training plans covering basics and advanced analytics; provide resources and support teams on call; use simulation-based environments for training.
Training metrics: training completion rate, user proficiency, support utilization.
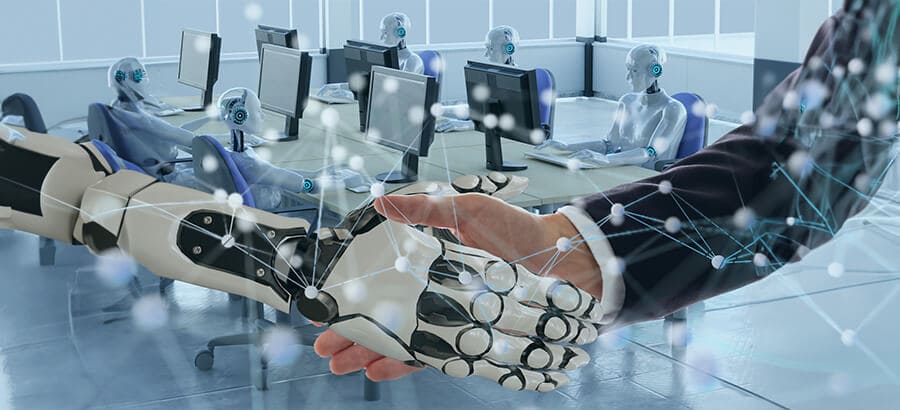
5.The future of AI manufacturing
1.Innovations and trends shaping AI in manufacturing
AI tracking solutions: Increasingly sophisticated AI tracking technologies monitor every step of the production process, optimize workflows, and reduce bottlenecks.
AI monitoring systems: Advanced monitoring systems provide real-time insights for more precise adjustments and improvements.
AI alerts: Notify managers and technicians before potential problems escalate, reducing downtime and maintenance costs.
2.Potential impact on efficiency and productivity
Reduce machine downtime: AI predictive maintenance predicts equipment failures and schedules optimal maintenance activities.
Increase production output: AI monitors and adjusts production parameters in real time to ensure high-quality output.
Enhance predictive maintenance accuracy: AI algorithms improve the accuracy of predictive maintenance strategies.
Reduce energy consumption: AI systems optimize energy use and reduce waste.
Finally
AI manufacturing has great potential and advantages in the manufacturing industry. From improving efficiency and quality control to reducing costs and optimizing energy management, AI manufacturing has brought about all-round changes to the manufacturing industry. However, the implementation of AI manufacturing also faces some challenges, and it is necessary to solve problems such as compatibility, data management, and training. With the continuous advancement of technology, AI manufacturing will continue to drive the manufacturing industry towards a more efficient and intelligent direction.