Best Guide for Cutting Titanium
Titanium is used in aerospace, medical, automotive and other fields due to its excellent performance. However, cutting titanium faces many challenges. Its unique physical and mechanical properties make cutting titanium a technically demanding job. This article will explore the various methods of cutting titanium to help you better cut titanium in future processing.
1.Characteristics of Titanium
Physical properties analysis
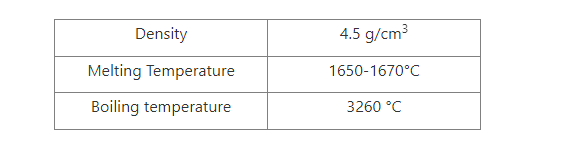
Mechanical properties interpretation
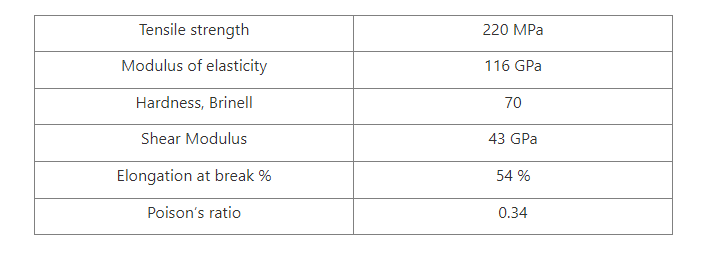
2.Difficulties in cutting titanium
Because titanium alloys are highly reactive, the cutting process must be carried out in a low-temperature environment to prevent contamination and discoloration of the metal. Its lower thermal conductivity causes the tool to transfer less heat, significantly shortening the tool’s service life. This makes cutting titanium an extremely challenging task that requires careful selection of the right processing technology and specialized tools.
3.Tools for cutting titanium
1.Carbide tools
In titanium cutting, most carbide tools play an important role. They are divided into two categories: titanium carbide and tungsten carbide, which can maintain their hardness values within a certain temperature range. In order to improve the heat dissipation performance and service life of the tool, different coating technologies, such as PVD coating, are often used on the tool surface. In the cutting process, fine-grained or medium-grained carbides are generally selected with a low binder content to meet the special needs of titanium processing.
2.Diamond tools
Diamond has become one of the special tools for cutting titanium due to its extremely high hardness, which is much higher than titanium. In operations such as cutting titanium rings, diamond-coated discs or diamond blades are often used. The high hardness of diamond enables it to effectively cut titanium, but it also requires attention to reasonable usage methods and conditions.
4. Methods for cutting titanium
1.Manual cutting
Manual cutting of titanium plates is feasible, but it is a difficult task due to the high hardness of titanium. Second-hand power hacksaws, bandsaws and circular saws can be used for cutting. Among them, hacksaws are relatively easy to obtain and the method of use is relatively simple. Just mark the sample and then operate the tool with force. However, this method is time-consuming, but it has certain advantages in cost control.
2.Sawing
Titanium alloy sawing is a precision cutting method that can produce clean and smooth edges, which is essential for applications such as aerospace and medical that require extremely high processing accuracy. During the sawing process, it is necessary to select the appropriate saw blade and cutting parameters according to the characteristics of titanium to ensure cutting quality and efficiency.
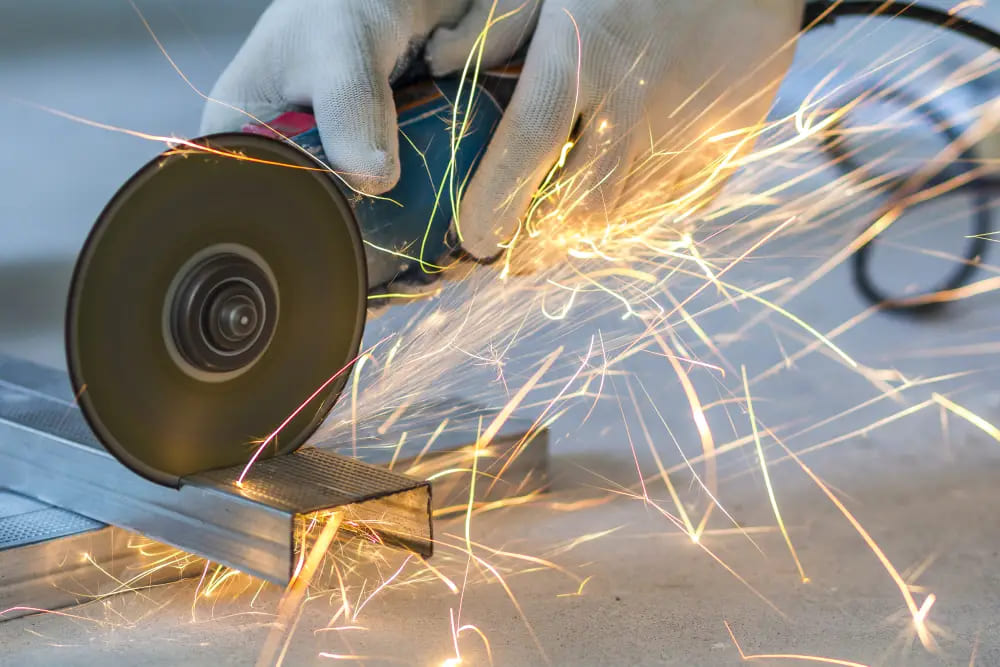
3.Band saw cutting
In the band saw titanium cutting method, a special blade is used with carbide tips on its teeth. Compared with ordinary steel tip tools, this blade maintains sharpness longer and can better adapt to the cutting needs of titanium. At the same time, this cutting process requires the use of coolant, which can improve cutting accuracy on the one hand and effectively prevent pollution problems caused by the high reactivity of titanium on the other hand. Band saw blades have a relatively long life and fast cutting speed when cutting titanium, which is a more efficient cutting method.
4.Angle grinder cutting
Titanium cutting can be done with the help of an angle grinder with a cutting disc. When choosing a cutting disc, an angle grinder with a masonry cutting disc may be more effective. Masonry cutting discs use silicon carbide abrasives instead of ordinary aluminum oxide abrasives, because when cutting titanium, if ordinary grinding discs are used, it is easy to cause the grinding disc to melt due to the high hardness of titanium, and it is impossible to achieve correct cutting. When using an angle grinder to cut titanium, the operator needs to have a certain amount of patience, because titanium is really hard and the cutting process takes a certain amount of time.
5.Laser cutting
Laser cutting machines can also be used for titanium cutting. The process uses a combination of nitrogen and oxygen in a carbon dioxide laser to cut titanium through the energy of the laser beam. However, this process causes the metal substrate to burn, so professional metal manufacturers are required to optimize the gas combination to provide excellent surface cutting results. Laser cutting has the advantages of high precision and high speed, but the process parameters need to be finely adjusted when cutting titanium.
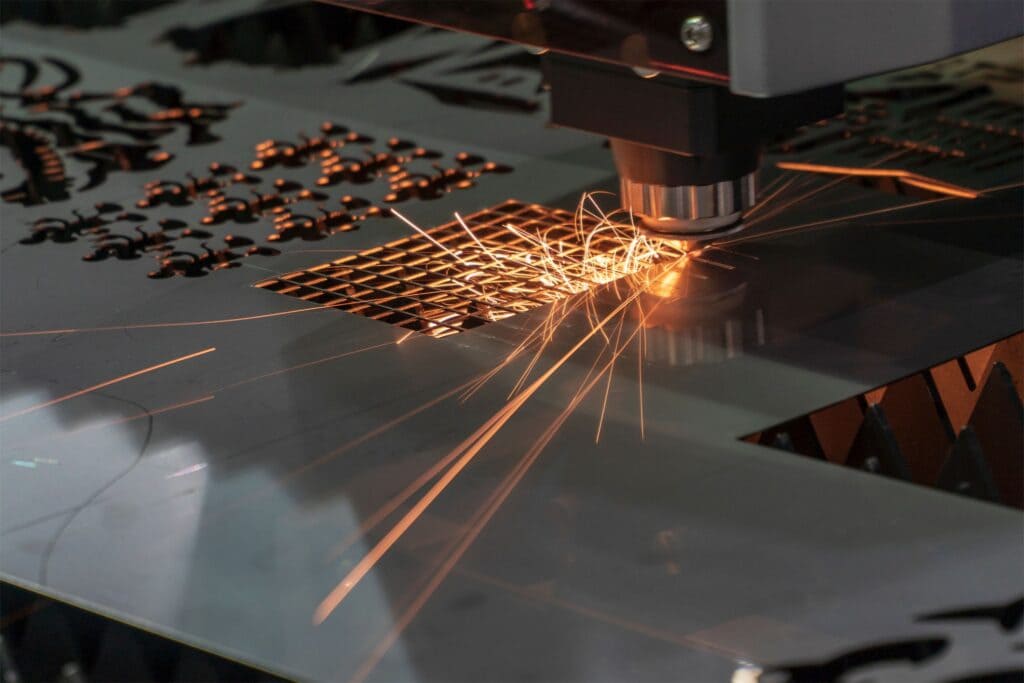
6.Plasma cutting
Plasma cutting torches or plasma CNC machines can be used for precise cutting of titanium, especially for samples that are difficult to position on a workbench or CNC bed. When cutting titanium, special gases are required, generally argon and nitrogen. Argon provides better cutting accuracy, while nitrogen can increase cutting speed. Plasma cutting is an efficient cutting method, but it also requires reasonable parameter settings based on the characteristics of titanium.
7.Turning and milling
Turning and milling of titanium are more complicated than the processing of other non-precious metals. During the processing, titanium is prone to overheating due to friction, which can cause equipment damage and processing stoppage. Therefore, many factors must be considered when turning and milling titanium. The service life of titanium processing tools is generally 45-90 minutes. Cutting titanium metal on a lathe requires a low speed to extend tool life. Titanium aluminum nitride (TiAlN) tools coated with carbides using the PVD process perform well in the milling process and can effectively improve processing efficiency and quality.
8.Waterjet Cutting
Water jet cutting of titanium is a very effective process. It can cut titanium blocks up to 8 inches thick (compared to 12 inches for softer materials such as aluminum). This cutting thickness advantage far exceeds other technologies such as laser or plasma cutting. Almost all titanium alloys on the market can be processed using waterjet cutting technology. The characteristic of waterjet cutting is the cold cutting process, which does not produce a heat-affected zone during the cutting process, ensuring that the titanium material maintains good performance after cutting. Waterjet cutting is often used in occasions where high cutting accuracy and material performance are required, such as exhaust titanium cake cutting.
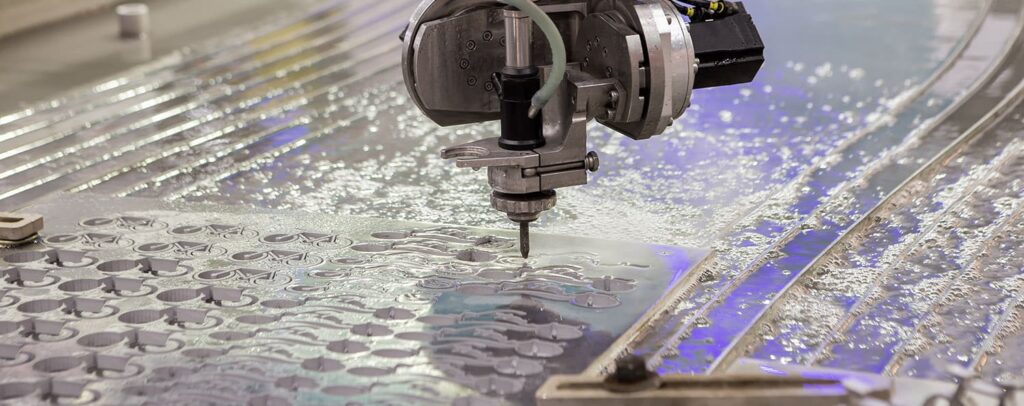
9.CNC Machine Cutting
Computer numerical control machine tools are suitable for the cutting process of titanium. Through programming, accurate and safe cutting of titanium plates and sheets can be achieved. The operator uses unique techniques, angles and speed settings to ensure that the titanium material is not damaged during the cutting process and achieve precision cutting of titanium alloys. CNC machine cutting has the advantages of high degree of automation, consistent and repeatable cutting accuracy, and can meet the needs of large-scale production and high-precision processing.
10.EBM Electron Beam Machining
Electron beam machining (EBM) technology has unique application value in advanced titanium metal cutting. It is particularly suitable for difficult-to-process materials such as titanium, because the technology can achieve high-precision cutting by accurately removing materials through high-speed electron flow. Compared with traditional methods such as laser or water jet cutting, EBM technology is a more professional and costly processing method, but it has significant advantages of reduced thermal effects and improved precision, which makes it used in some fields with extremely high cutting accuracy and quality requirements, such as special parts processing in the aerospace field.
5.Summary and advantages of cutting titanium methods
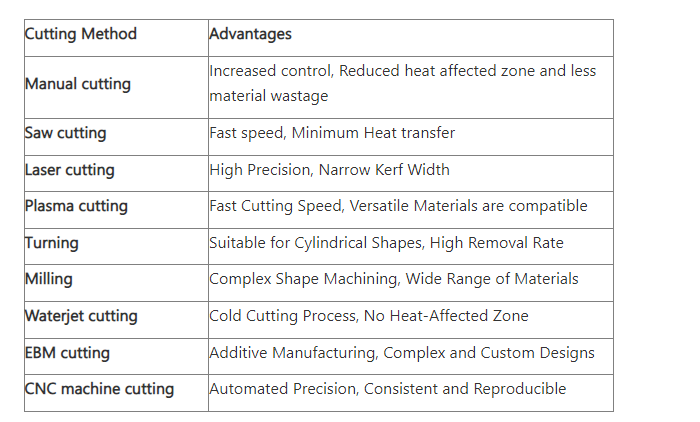
6.Application fields of cutting titanium
Aerospace field
In the aerospace field, its high strength-to-weight ratio makes it an ideal choice for manufacturing precision parts in aircraft such as aircraft engine parts, fuselage structural parts, etc.
Medical field
In the medical field, titanium is the first generation of implant biomaterials, known for its good biocompatibility and corrosion resistance, and is widely used in the manufacture of implants (such as orthopedic implants, dental implants, etc.) and surgical instruments.
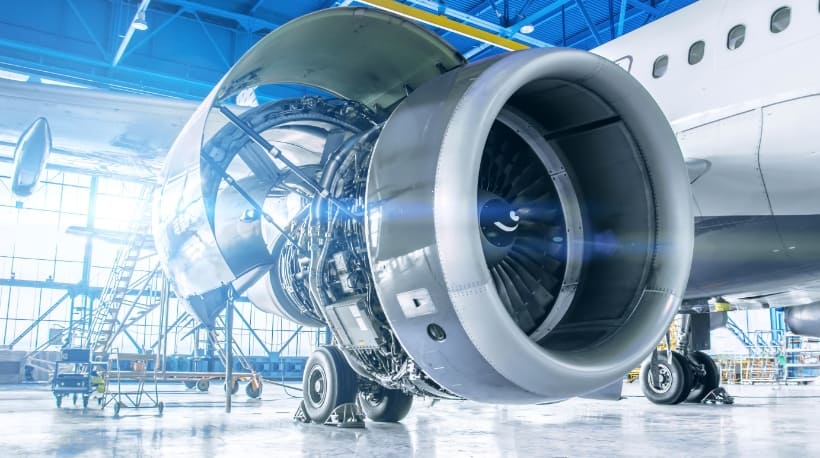
Industrial application
In industrial applications, titanium’s non-toxic, durable and extreme resistance make it widely used in chemical industry, marine engineering and other fields, such as corrosion-resistant pipes in chemical equipment, structural parts of offshore platforms, etc.
7.Tips for Successful Cutting Titanium
Cutting Parameter Optimization
Using low cutting speeds can minimize heat input and reduce the possibility of material deformation, thereby maintaining the mechanical properties of titanium materials. At the same time, a high feed rate should be given, which can reduce the time the tool stays on the material, thereby maximizing processing efficiency and reducing tool wear.
Cooling and lubrication measures
Using a large amount of cutting fluid is one of the key measures to ensure a smooth cutting process. Cutting fluid helps lubricate and cool, which can effectively extend tool life and minimize overheating. When selecting cutting fluid, it is necessary to make a reasonable selection based on the characteristics of titanium and the cutting method to ensure that it performs the best effect.
Tool Management
It is essential to keep the tool sharp. Timely replacement of sharp tools can maintain consistent processing quality, and sharp tools can ensure precise cutting and eliminate excessive friction during the cutting process. At the same time, according to the service life and wear of the tool, the tool replacement cycle should be reasonably arranged to avoid the decline in processing quality and efficiency caused by tool wear.
Operation Precautions
During the cutting process, damage should be avoided when the tool and the workpiece come into contact. Maintaining continuous feed prevents heat accumulation, protects the integrity of the tool, and avoids damage to the workpiece. Operators need to have rich experience and professional skills and strictly follow the operating procedures to ensure the safety and stability of the cutting process.
Conclusion
Cutting titanium is a complex process involving multidisciplinary knowledge and technology, covering multiple fields such as material science, mechanical engineering, and processing technology. A deep understanding of the performance characteristics of titanium and mastering various cutting methods are essential to achieve efficient, precise, and high-quality titanium cutting. With the continuous advancement of science and technology, it is believed that more advanced cutting technologies and methods will appear in the future, further promoting the application of titanium materials in a wider range of fields and injecting new vitality into the development of advanced manufacturing.