Key factors in manufacturing metal parts
Metal parts play a vital role in the modern industrial field. From automobile manufacturing to aerospace, from medical devices to industrial equipment, the quality and performance of metal parts directly affect the development of various industries. In the process of manufacturing metal parts, material selection, process type and the intended use of the parts are three crucial factors. This article will explore these three key factors in depth to reveal the secrets of metal parts manufacturing for you.
1.Factors affecting the manufacturing of metal parts
Mechanical properties
When selecting materials for metal parts, its mechanical properties, including hardness, tensile strength, and ductility, must be considered. Different application scenarios require different combinations of mechanical properties. For example, stainless steel is favored for its corrosion resistance and durability, especially in situations where high strength and good corrosion resistance are required; while aluminum is widely used in fields with strict weight requirements such as automobiles and aerospace due to its light weight.
Corrosion resistance
Depending on the use environment of the part, corrosion resistance is an important consideration. For parts used in harsh environments such as marine, medical, or outdoor, it may be necessary to choose corrosion-resistant materials such as stainless steel or anodized aluminum. These materials can maintain their performance and appearance in harsh environments and extend the service life of the parts.
Cost-effectiveness
When selecting materials, cost-effectiveness is also a key factor. Some materials, such as titanium and certain high-performance alloys, have excellent properties but are more expensive. Therefore, when selecting materials, it is necessary to find a balance between cost and performance, especially for parts produced on a large scale.
Machinability
The machinability of the material affects the manufacturing time and overall cost. Some metals, such as brass and aluminum, are relatively easy to machine, while harder materials such as hardened steel or titanium may require more time and specialized tools to machine.
2.Commonly used materials for metal parts manufacturing
Steel
Steel is an iron alloy with a carbon content of about 1%, which has high strength and great flexibility. It can be processed by many methods such as machining, stamping, roll forming, welding, etc., so it is one of the commonly used materials in metal parts manufacturing.
Stainless steel
Stainless steel has the advantage of corrosion resistance by increasing the chromium content (10% or more by weight) on the basis of steel. Stainless steel parts are often used in places with high corrosion resistance requirements such as marine applications and chemical plants.
Aluminum
Aluminum is a soft element and is usually mixed with other elements such as copper, magnesium and zinc and heat treated to improve its properties. Automobile and aircraft parts are often made of aluminum to reduce weight.
Brass
Brass is an ideal choice when corrosion resistance is important. It has a wide range of uses, and many pipe parts such as valves are made of brass. Brass is also very strong and can be used to make everything from ship parts to coins.
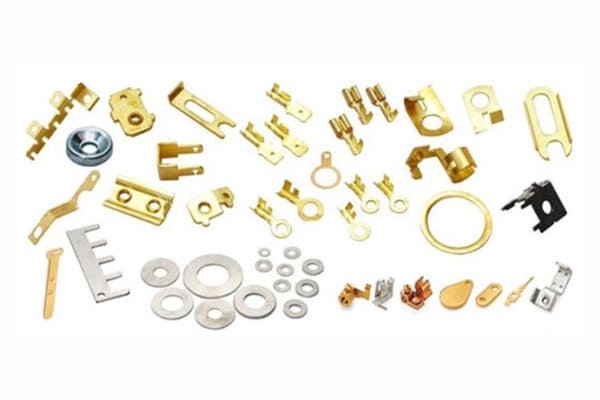
Copper
Copper has a fibrous structure and is difficult to process. However, due to its good conductivity, it is an extremely important power generation metal and is often used in wires and pipes. Copper is also commonly found as an element in many different metal alloys.
3.Types of metal parts manufacturing processes
(I) Considerations
Part geometry and complexity
For parts with complex shapes and rich details, it is necessary to select a process that can achieve high-precision machining. Processes such as CNC machining or precision casting may be more suitable for such parts. CNC machining allows for tight tolerances and is ideal for parts that require precision machining.
Production volume
The size of the production volume will also affect the choice of process. For small-batch production or prototyping, processes such as CNC machining and 3D printing are more cost-effective and flexible. For large-volume production, methods such as stamping, forging or die casting can help reduce unit costs.
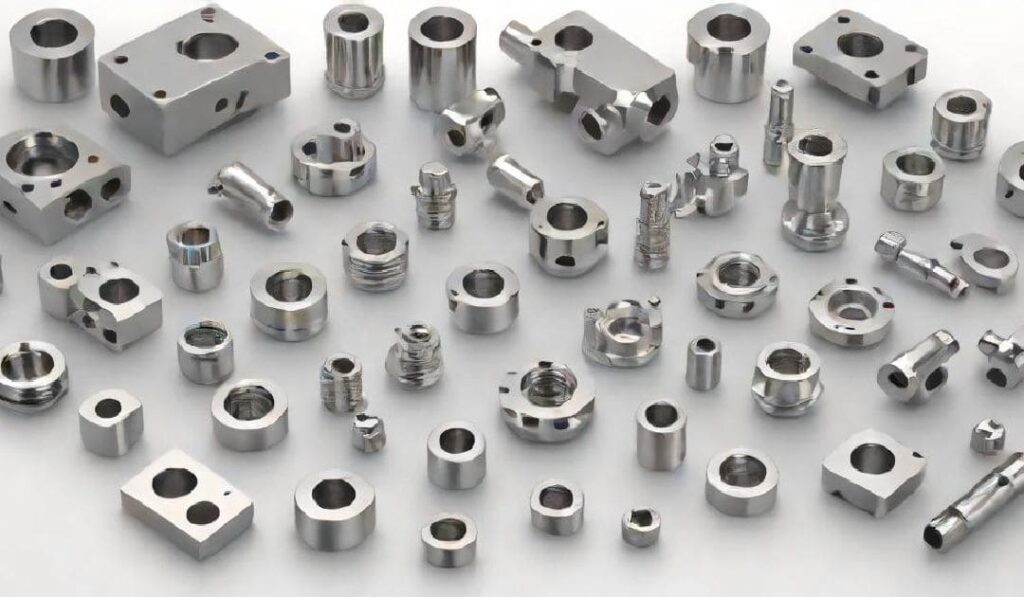
Tolerance and surface finish requirements
The accuracy required for the part determines the choice of machining process. CNC machining is well suited to achieve high tolerances, while processes such as forging may require secondary processing to meet tighter tolerance requirements.
Delivery time and flexibility
Different processes have different delivery times and flexibility. For example, CNC machining has a short turnaround time and is ideal for rapid prototyping or small-batch production.
(II) Common processes
CNC machining
Highly accurate and versatile, it is suitable for prototyping and production.
Casting
Effective for large quantities of complex shaped parts, but may require post-processing to ensure accuracy.
Forging
Used to produce high strength, high stress parts, but less flexible for complex geometries.
Sheet Metal Fabrication
Great for making parts such as housings and panels, often used in automotive and industrial applications.
4.Uses of Metal Parts
Automotive Industry
Parts such as gears, axles, and brackets in the automotive industry need to be durable, cost-effective, and often produced in large quantities. Steel is popular for its strength, but lightweight materials such as aluminum are becoming increasingly popular.
Aerospace
In the aerospace field, weight reduction is key, so materials such as titanium and aluminum are favored. Parts also require high precision and must withstand extreme conditions.
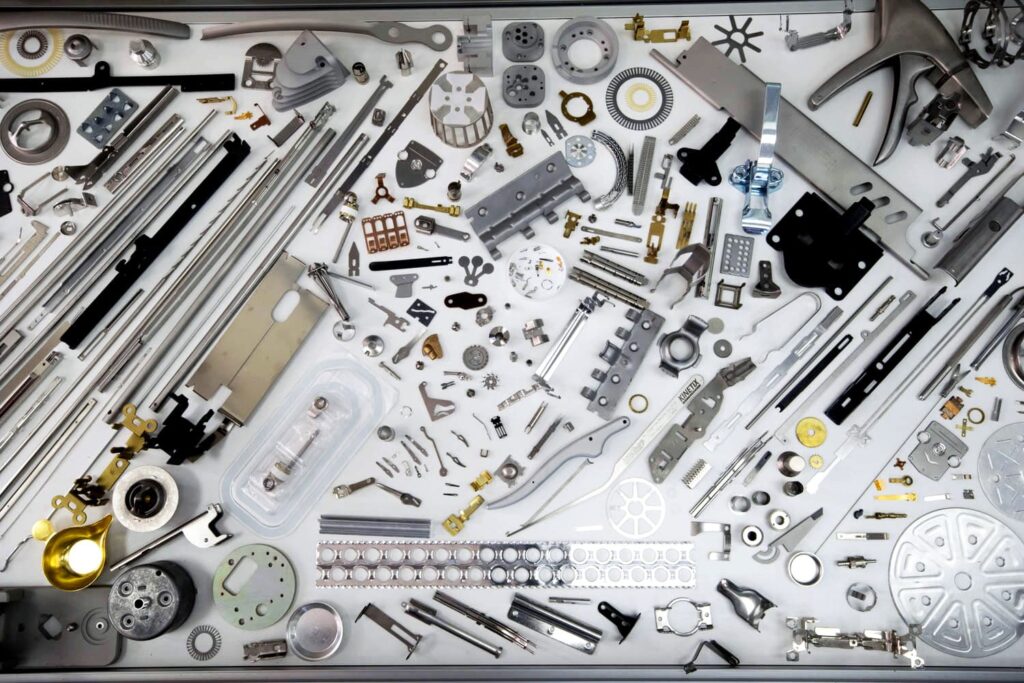
Medical Devices
In the field of medical devices, biocompatibility is crucial, and materials such as stainless steel and titanium are widely used because of their sterilizable and corrosion-resistant properties.
5.Main considerations for metal parts
Loads and pressures
If the part is subject to heavy loads or pressures, it needs to be made of strong and durable materials, and a manufacturing process that ensures optimal strength must be selected. For example, forged steel is often used to make high-stress automotive parts such as axles and crankshafts.
Temperature and environmental conditions
Will the part be exposed to extreme temperatures, moisture, or chemicals? High-temperature environments may require heat-resistant alloys, while parts exposed to chemicals or moisture may require corrosion-resistant materials such as stainless steel or aluminum.
Friction and wear
If the part will be subject to friction, such as in moving machinery, materials with wear-resistant properties such as hardened steel or alloys with added coatings should be considered.
Precision requirements
If the part is critical to the function of the component, such as in aerospace or medical devices, it must be manufactured with tight tolerances and surface finish, requiring precise machining processes.
Summary
In the process of manufacturing metal parts, material selection, process type and the intended use of the part are three key interrelated factors. By carefully considering these factors, manufacturers can select the right materials, use the best manufacturing process, and ensure that the metal parts meet specific application needs.