Aluminum welding: technical points and precautions
In modern manufacturing, aluminum plays a vital role as a key material widely used in many engineering fields such as aviation, automobiles and sheet metal manufacturing. Its outstanding strength-to-weight ratio, excellent corrosion resistance, and good thermal and electrical conductivity make it one of the indispensable materials.
In the processing of aluminum, welding is an extremely critical technology. Aluminum welding is a challenging but indispensable skill that requires in-depth knowledge and rich practical experience. This article will explain the relevant content of aluminum welding in detail, including welding difficulties, welding technology and other aspects.
Why is aluminum welding difficult?
(I) High thermal conductivity and low melting point
The interaction of aluminum’s high thermal conductivity and low melting point makes heat conduction in aluminum materials rapid and difficult to control. This situation can easily lead to serious problems such as deformation, cracking and burn-through of welded parts, posing a major challenge to welding.
(II) Effect of aluminum oxide layer
Although the oxide layer on the surface of aluminum gives it corrosion resistance, it is a problem during welding. Because the melting point of the oxide layer is much higher than that of ordinary aluminum alloys (the melting point of ordinary aluminum alloys is about 660°C, and the melting point of the oxide layer is about 1400°C higher), this huge difference in melting point will lead to unstable welding quality and joint strength.
(III) Pollution problem
Molten aluminum is very easy to absorb polluting compounds such as hydrogen in the environment, and these pollutants will eventually form pores or cracks at the welded joint.
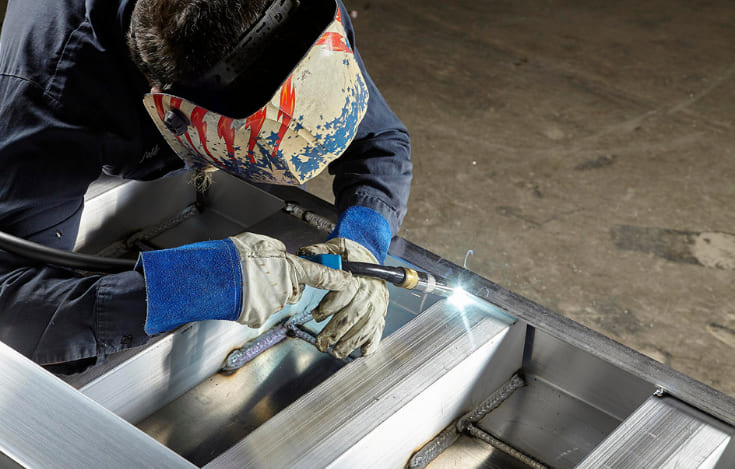
(IV) Poor wire feeding ability
Compared with other welding wires, aluminum welding wire is softer, which makes it difficult for automatic feeders to handle aluminum welding wire, increasing the complexity of welding operations.
(V) No color change characteristics
Unlike most metals that change color before melting, aluminum has no obvious color change during the melting process. This makes it difficult for aluminum welders to judge when the metal is melted, increasing the difficulty of welding operations.
Five Common Aluminum Welding Techniques
(I) Gas Tungsten Arc Welding (TIG)
TIG welding is one of the preferred methods for aluminum welding. It provides a high degree of operational freedom, allowing welders to precisely control the heat input into the welding device. This allows them to penetrate the oxide layer on the aluminum surface for welding and effectively control the molten pool while avoiding bending of the metal due to excessive temperature.
Typically, TIG welding with high-frequency AC current is more commonly used because it has a lower level of contamination. This is because the tungsten electrode does not need to come into contact with the workpiece, which reduces the possibility of tungsten electrode deposition in the weld pool.
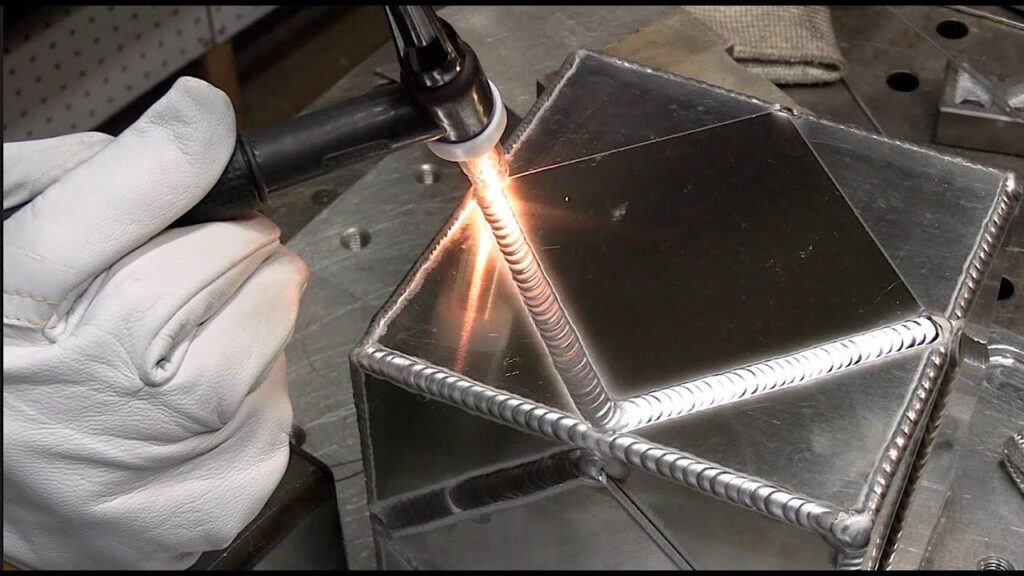
(II) Metal Inert Gas Welding (MIG)
MIG welding is another way to weld aluminum. It performs well in aluminum welding applications and has the advantages of easy operation, low cost and a wide range of applications. Although its weld quality is slightly inferior to TIG welding, it can still meet high quality requirements.
By properly adjusting process parameters such as travel speed and component preheating, MIG welding can effectively deal with the problems caused by the high thermal conductivity of aluminum. However, the softness of aluminum wire may cause some problems, which require the use of a spool gun or push-pull gun. In addition, aluminum MIG welding requires the use of 100% pure argon as a shielding gas, which is relatively cheap but may not be easily available in some workshops due to its limited use.
(III) Electron beam welding
Electron beam welding is a high-precision and high-efficiency aluminum welding method. The method is to project a concentrated high-speed electron beam onto the joint interface to form a local high-temperature area to achieve welding. This welding method is accurate and clean because it can accurately apply heat to the required location, minimizing the heat-affected zone and its related defects.
Moreover, electron beam welding is extremely fast (about 10 times faster than TIG or MIG), so the heat does not have enough time to penetrate deeply into the material. In addition, because the electron beam welding process is carried out in a vacuum, the joint purity is very high and most impurities in the welding area can be removed during the welding preparation process. It is worth noting that the electron beam can penetrate aluminum up to 15 cm deep, which makes its welding capabilities not limited to metal plate welding.
(IV)Laser welding
Laser welding of aluminum is similar to electron beam welding, but is slightly inferior in terms of weld quality, precision, and weld depth. It uses a laser beam to achieve the weld, which also has the advantages of precise, direct heat transfer and high welding speed.
However, laser welding also has certain limitations in terms of cost and operator skill requirements. In addition, a significant advantage of laser welding is its ability to act on narrow points because the laser beam is very thin, unlike traditional welding guns. This feature helps weld metal sheet structures with curling features.
(V)Friction stir welding
Friction stir welding is an innovative aluminum welding method that is becoming increasingly popular in the industry. It uses a rotating tool to generate heat at the joint interface through friction. The main advantage of this welding method is that it is a solid phase process that can weld below the melting point of the material. Therefore, heat-related problems can be almost completely avoided and the heat-affected zone is very small.
Because the joint does not melt during the welding process, there is no way for contaminants to enter the joint and warping will not occur. In addition, friction stir welding is repeatable and relatively inexpensive.
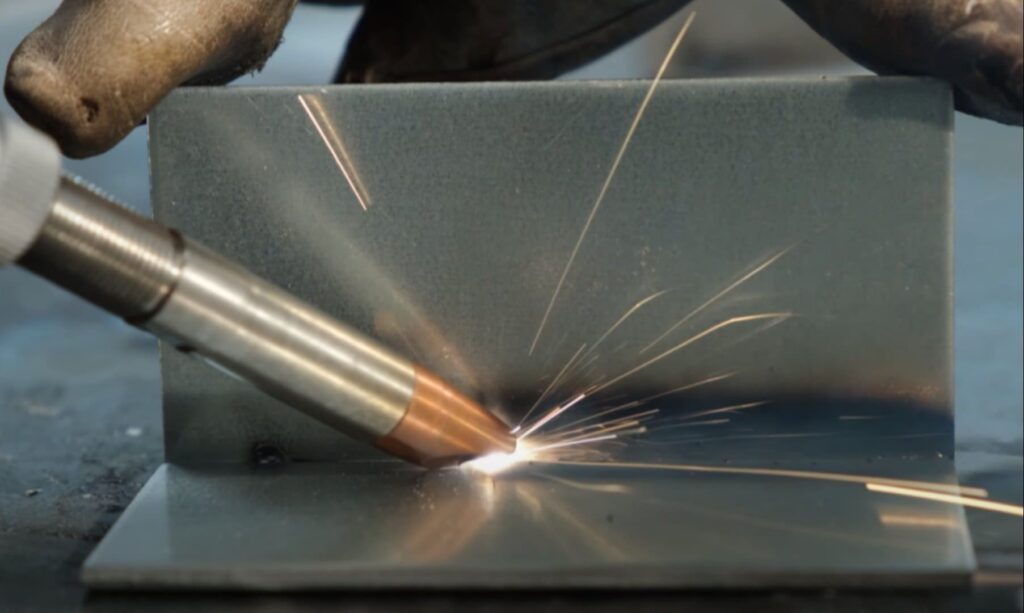
Preparation for aluminum welding
(I) Cleaning
Cleaning the workpiece surface is a key step in the preparation process for aluminum welding. It has a dual purpose: one is to remove dirt such as oil and dust, and the other is to eliminate the aluminum oxide layer. Both of these will damage the quality of the weld because they will introduce contaminants into the weld area.
For the removal of dirt particles and water vapor, cleaners such as acetone or alkaline solutions are commonly used. These cleaners are inexpensive and easily available. For the removal of oxides, using a metal brush usually achieves good results.
(II) Selecting the welding method
Common aluminum welding methods have been discussed above. Although the options are limited, it is crucial to determine the most appropriate welding technology. Usually, it is necessary to choose between TIG and MIG. Although TIG welding is a high-quality welding method, it requires a skilled aluminum welder and sufficient time, and the workshop needs to be equipped with a dedicated TIG welder.
(III) Selecting the filler material
The filler material plays a key role in determining the strength of the weld. Selecting the most suitable welding wire for the aluminum welding application is necessary to optimize the weld quality. This choice mainly depends on factors such as the welding method, the grade of aluminum and the required performance. The properties of the filler metal should be as close as possible to the base metal. The diameter of the wire will affect the amount of material entering the weld pool, which in turn determines the weld strength, leakage resistance, ductility and other properties.
(IV) Consider inert gas
Both MIG and TIG welding require the use of inert gas to protect the weld pool from the reactive environment. The composition of the gas will affect the quality of the weld, so it needs to be carefully selected in the preparation stage. Generally speaking, 100% pure argon is a good choice for both welding processes. It is cheap and easy to obtain.
Notes on aluminum welding
(i) The importance of clean metal
Clean metal is critical to the quality of aluminum welding, and this needs to be emphasized again, because any residual dirt or oxides will have a significant impact on the overall weld quality.
(ii) Proper storage environment
Storing aluminum materials in a dry environment can prevent the cleaned aluminum from oxidizing again, providing good conditions for welding work.
(iii) Preheating of aluminum materials
It is a good operating habit to preheat the aluminum materials before welding. This helps to make the temperature of the entire workpiece uniform, avoid deformation and cracking problems caused by uneven internal heat conduction, and also helps to remove moisture.
(iv) Higher moving speed
During the welding process, try to use a faster moving speed, which can reduce the heat input to the welding area. Because the high thermal conductivity of aluminum will quickly disperse heat, if the moving speed is too slow, additional heat will enter the welding area from the heat source, eventually causing deformation of the parts.
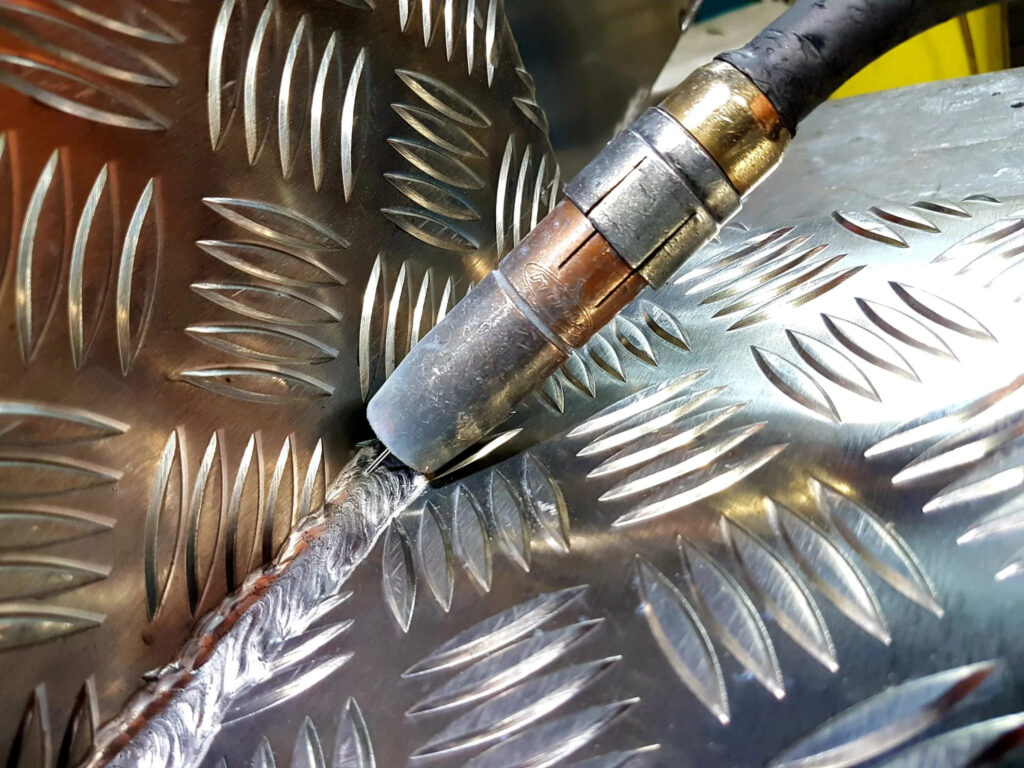
(v) Proper welding gun angle
For TIG and MIG welding of aluminum, a 15° welding gun angle is the most suitable, which helps to improve welding quality.
(vi) MIG welding “push welding” method
When using MIG welding, using the “push welding” method (i.e. tilting the welding gun away from the direction of travel) can help improve the gas shielding effect and avoid welding defects.
Xavier: A quality choice for welding services
At Xavier, we are well aware of the key role of welding in post-processing and assembly of parts. We have experienced machinists who can handle the welding needs of different metals, including aluminum, excellently. In addition, we also provide one-stop processing and surface treatment services, whether it is prototype design or part production, you can get the product in a convenient and cost-effective way.
Summary
As one of the core manufacturing technologies in the manufacturing industry, aluminum welding plays a key role in all aspects. Mastering the technical points of aluminum welding is crucial to ensuring welding quality and improving product performance. At the same time, choosing a professional welding service organization can provide strong support for aluminum welding-related production activities and ensure the smooth progress of the entire manufacturing process.