A Comprehensive Guide to Ceramic Machining
Ceramic machining is a technology for the efficient mass production of ceramic products. It can produce complex designed ceramic parts with precise tolerances, and the finished product is of high quality and smooth surface. However, ceramic machining involves a variety of machining operations, design considerations, etc. This guide will explore these aspects in depth to provide a comprehensive guide to ceramic machining.
1.What is Ceramic Machining ?
Ceramic Machining is the process of carving ceramic materials into various shapes through milling, drilling, grinding and turning techniques using computer-guided tools. This process is suitable for fired ceramics that have reached maximum density. Due to the high hardness and brittleness of ceramics, traditional machining methods are ineffective, while CNC machines can achieve higher precision and stronger control when machining ceramics, which is particularly effective for producing parts with complex designs and tight tolerances.
First, a computer-aided design (CAD) model of the target part or design is created, which guides the generation of tool paths, which are then input into the CNC machine, and the machine accurately cuts or molds the ceramic material according to the defined tool paths.
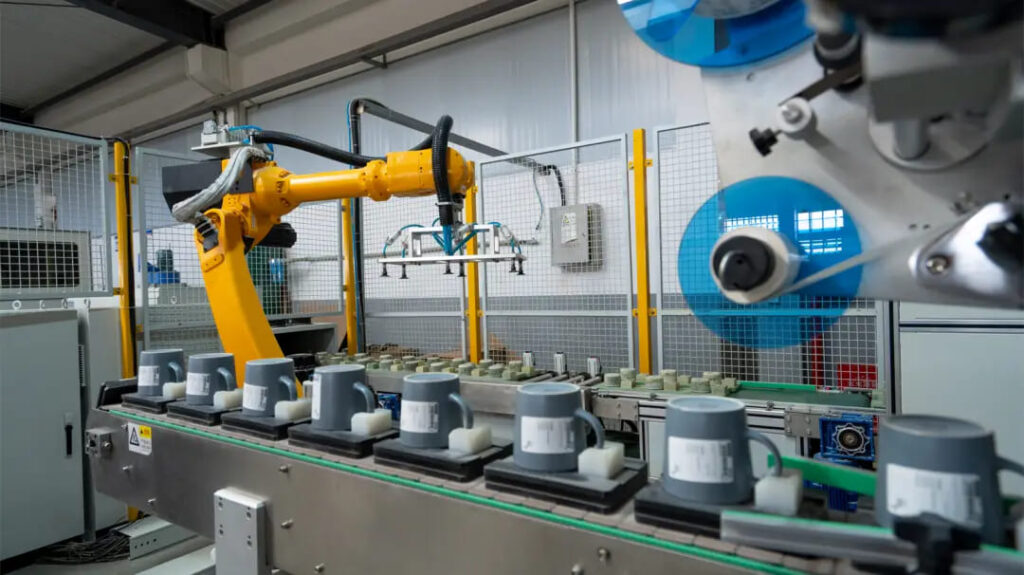
2.Ceramic Machining steps
(1) Design
Design plays a key role in the production of CNC ceramic parts. Engineers use CAD software to create detailed plans of ceramic parts. This design is the basis for machining operations and is converted into a CNC program to guide the machine in high-precision machining.
(2) Preparing materials
Choosing the right ceramic material is key, taking into account factors such as strength, thermal conductivity and durability. After selecting the materials, make sure there are no impurities, contaminants or abnormalities to ensure processing accuracy.
(3) Processing
This is the core stage of ceramic machining. Under the guidance of the CNC program, the CNC machine processes the ceramic from the original shape into precisely shaped parts. Its distinctive features are high precision and the ability to handle complex geometries and multi-part production.
(4) Final processing
Post-processing is required after machining, including cleaning to remove residual material and ensure that ceramic parts meet quality and accuracy standards.
3.Types of ceramic machining
(i) CNC milling
CNC milling uses computer commands to control the machine, using a rotating cutting tool to remove material to shape ceramic parts. Its advantages are that it can produce complex shapes with high precision, computer control ensures accurate and consistent cutting, and can also produce smooth surfaces, reducing or eliminating additional polishing or finishing procedures.
(ii) Core drilling
Core drilling is a drilling technology that removes cylindrical parts from large blocks or sheets of ceramic materials. It is used to accurately drill holes of specific diameters and is used for wiring, component installation, and pipe or ventilation system construction. CNC machine tools guide rotating tools (usually diamond drill bits) to drill holes. The drill speed must be carefully controlled, and coolants are used to reduce heat accumulation, and special cutting tools are often required.
(iii) Wafer cutting
The wafer cutting process is effective for producing ceramic parts from materials such as quartz and graphite. It involves separating individual wafers from a ceramic wafer, which can be done by crushing, laser cutting, mechanical sawing or scribing. For ease of handling, wafers are often mounted on film frames or glass to improve cutting accuracy.
(iv) ID Slicing
ID slicing (inside diameter slicing) is a processing technique for repeated cutting of brittle or hard materials, using an inside diameter diamond-coated saw blade and a ring design to improve cutting accuracy and reduce cut loss. This method is simple and cost-effective to make ceramics.
(v) Surface Grinding
Surface grinding uses a grinding wheel to remove material from the surface of the workpiece and is used in the ceramic industry to produce precise and smooth surfaces. The accuracy of ceramic surface grinding is critical and is often used to achieve flat and parallel surfaces of ceramic parts and eliminate surface defects or damage.
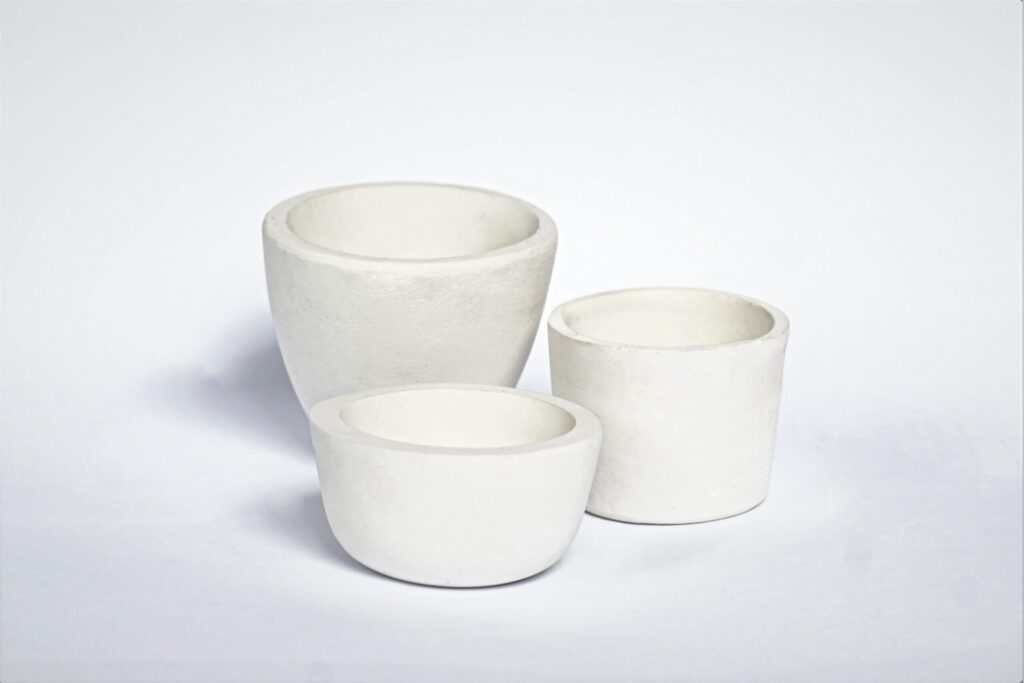
4.Ceramics suitable for CNC machining
(I) Alumina ceramics
Alumina ceramics are widely used and are known for their high hardness, durability, electrical insulation, heat resistance and corrosion resistance. Its hardness and wear resistance make it an ideal cutting tool material, and its high temperature resistance and electrical insulation make it suitable for high temperature and electrical applications.
(II) Aluminum nitride
The thermal expansion rate of aluminum nitride is lower than that of aluminum oxide, close to that of silicon wafers, and has metallization properties. It is an excellent material for semiconductor applications and is used to produce related precision parts in CNC machining.
(III) Boron nitride
Boron nitride (chemical formula BN) is a special ceramic made of boron and nitrogen. It has a low dielectric constant, minimal thermal expansion, low loss tangent, chemical inertness, strong electrical resistance, and can withstand thermal shock. It is produced in the form of hot-pressed solids to form a hexagonal plate-like crystal structure, which can be used for precision machining of complex parts. It does not require firing or heat treatment before use and is suitable for semiconductor and electronic product production.
(IV) Silicon carbide ceramics
Silicon carbide (SiC) ceramics are advanced technical ceramics with excellent hardness, high thermal conductivity, strong resistance to thermal shock and wear, and are widely used in industrial environments. In CNC machining, they can be used to manufacture cutting tools, wear-resistant parts and structural parts. Its high hardness can process tough materials, and its high thermal conductivity helps dissipate heat, reduce tool wear, and improve cutting speed and precision. Its excellent thermal shock resistance and chemical stability make it suitable for harsh conditions.
(V) Zirconia ceramics
Zirconium oxide ceramics are high-end ceramics with excellent strength, toughness, chemical resistance and corrosion resistance, making them ideal materials for medical and dental applications. Its high hardness allows for rapid processing, and its excellent heat resistance, high melting point and strong stress absorption ability make it suitable for structural ceramic parts. It has excellent mechanical strength at room temperature and is often used in structural parts such as ball valves, fiber optic needles, and watch cases. It has excellent thermal properties and is also used in functional parts such as induction heating tubes and heating elements.
(VI) Talc ceramics
Talc ceramics (commonly known as high-frequency ceramics) are mainly composed of hydrated magnesium silicate and are economical and affordable. It has excellent electrical resistance at high temperatures, low dielectric loss, low dissipation factor, high mechanical strength, can withstand huge stresses, and is suitable for CNC processing. Its low loss characteristics are suitable for manufacturing insulators for broadcast antenna equipment, and its heat resistance combined with dielectric properties are used to produce durable, fire-proof terminal blocks.
(VII) Quartz ceramics
Quartz ceramics are mainly made of pure silica (silicon dioxide), have excellent optical and chemical properties, high tensile strength, good thermal stability, and good thermal insulation performance. They are the first choice for the lighting and semiconductor industries. Processing quartz ceramics requires powerful diamond tools, water jets or grinding. It is suitable for manufacturing precision parts and is used in a variety of components in rockets and space technology.
(VIII) Cordierite ceramics
Cordierite ceramics are composed of magnesium, aluminum and silicates, and come in a variety of colors. They are mainly used for parts with high impact resistance and fire resistance requirements. They have excellent high temperature resistance and are used in ceramic kiln plates, saggers, high-temperature heat dissipation materials and electronic packaging materials. Although the thermal insulation performance is slightly inferior, it can withstand repeated heating and cooling and is suitable for products such as catalytic converters.
5.Advantages of ceramic machining
(I) Versatility
Ceramic machining has excellent precision and can produce complex and fine ceramic parts. CNC machinery and software integration can finely control cutting and forming tools to ensure the manufacture of high-quality, high-precision parts that meet strict requirements.
(II) Cost-effectiveness
Compared with manufacturing methods such as laser cutting and water jet cutting, CNC machining of ceramics is more cost-effective. This is due to its fewer errors, high productivity, and lower overall cost than laser cutting.
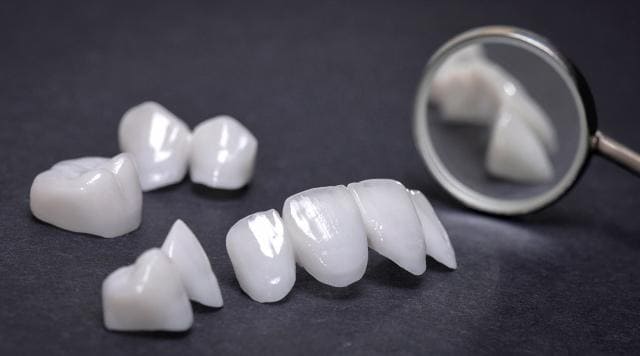
(III) Scalability
The CNC machining process of ceramics can adjust production volume according to market demand, effectively reduce material waste, and achieve on-demand production.
(IV) High cutting and forming accuracy
CNC machining has excellent process control and precision, which is particularly critical for machining rigid and brittle ceramics.
(V) Ability to produce complex geometries
Ceramic machining can create complex shapes that are difficult to produce with other technologies.
(VI) Tight tolerances
Ceramic machining can achieve tight tolerances and meet the key requirements of many applications.
6.Disadvantages of ceramic machining
(I) Fragility
Although ceramics have high strength and hardness, their crystal structure lacks flexibility and is brittle, and they are prone to cracking and breaking under pressure.
(II) Vulnerability
During CNC machining, ceramic materials are at high risk of damage. Machining will increase stress, and they are prone to cracking, breaking or breaking, which will affect the design implementation.
(III) Difficulty of machining
Ceramics have high hardness, which often exceeds the hardness of cutting tools, resulting in severe wear and damage to the tools, increasing tool costs, extending machining time, and possibly reducing the quality of the finished product.
(IV) Extended production time
Ceramic machining takes a long time to produce, because its hardness and brittleness make machining more complex and time-consuming than metal, and high precision requirements require the use of special tools and equipment, which can easily lead to delays in project completion.
7.Application of ceramic machining
(I) Medical Field
ceramic machining are widely used in the medical field. Their strength, biocompatibility and corrosion resistance make them ideal materials for medical implants. In dentistry, they are often used to make prostheses such as crowns, bridges and implants. Zirconia ceramics are particularly popular in the dental field. Ceramics can be processed into complex shapes, which is conducive to the manufacture of customized implants and the realization of precise and personalized medical solutions.
(II) Electronic Field
In the electrical and electronic industry, ceramic machining is used to manufacture parts with high dielectric properties, durability, heat resistance and wear resistance. The heat resistance of ceramics makes it suitable for the manufacture of components in extreme temperatures and harsh environments, such as circuit board heat sinks, vacuum circuit breakers, substrates, insulators and microwave oven components.
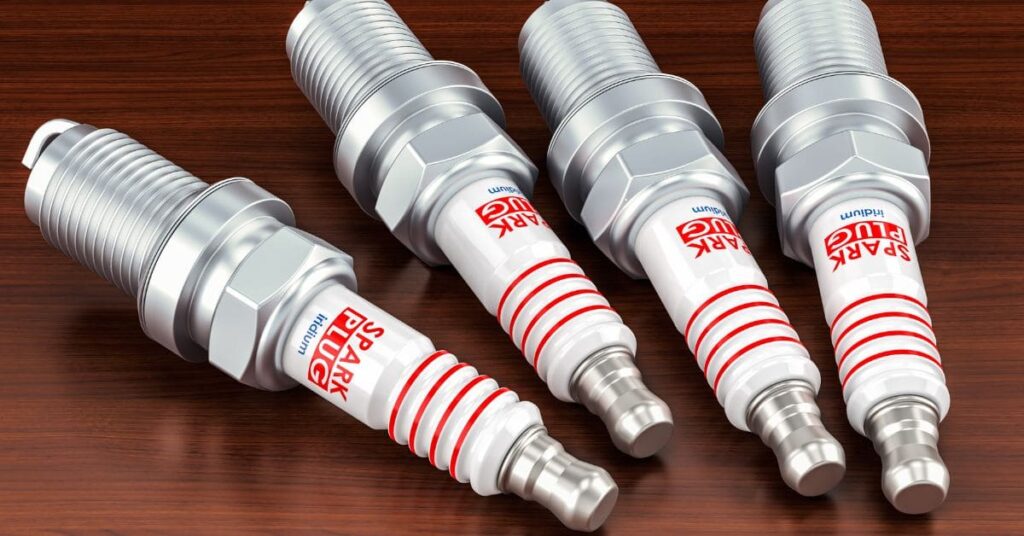
(III) Industrial Field
Ceramics are widely used in industry, suitable for large structures as well as small and complex industrial parts. Its excellent wear resistance makes it suitable for the manufacture of durable parts.
(IV) Automotive Sector
The automotive industry takes advantage of the advantages of ceramic machining. Ceramic brake pads are popular parts with excellent wear resistance, greater durability, and good heat dissipation, which improves performance and safety. In addition, automotive parts such as spark plugs, valves, gears, and engine blocks can also be made with CNC ceramics, often using materials such as aluminum nitride or boron nitride.
8.Guide to Efficient ceramic machining
(I) Appropriate Materials
Choosing the right ceramic material is the basis for effective ceramic machining. It is necessary to balance properties such as hardness, wear resistance, thermal stability and electrical insulation to meet specific needs and ensure excellent performance and long life.
(II) The Right Tool
For ceramic machining, the selection of cutting tools is crucial. Diamond or CBN (cubic boron nitride) tools are the first choice, which can withstand the hardness of ceramics and resist wear, reduce wear and improve machining efficiency.
(III) Correct Machining Parameters
Fine-tuning machining parameters is crucial to achieve accuracy and alleviate problems. Careful adjustment of cutting speed, feed rate and cutting depth is required to reduce material brittleness, tool wear and overheating. Regular monitoring and adjustment of these parameters are the key to successful machining.
(IV) Effective Cooling and Lubrication
In ceramic machining, cooling and lubrication are essential to control heat generation, prevent thermal deformation, extend tool life, ensure the quality of ceramic parts, and ensure seamless and efficient machining.
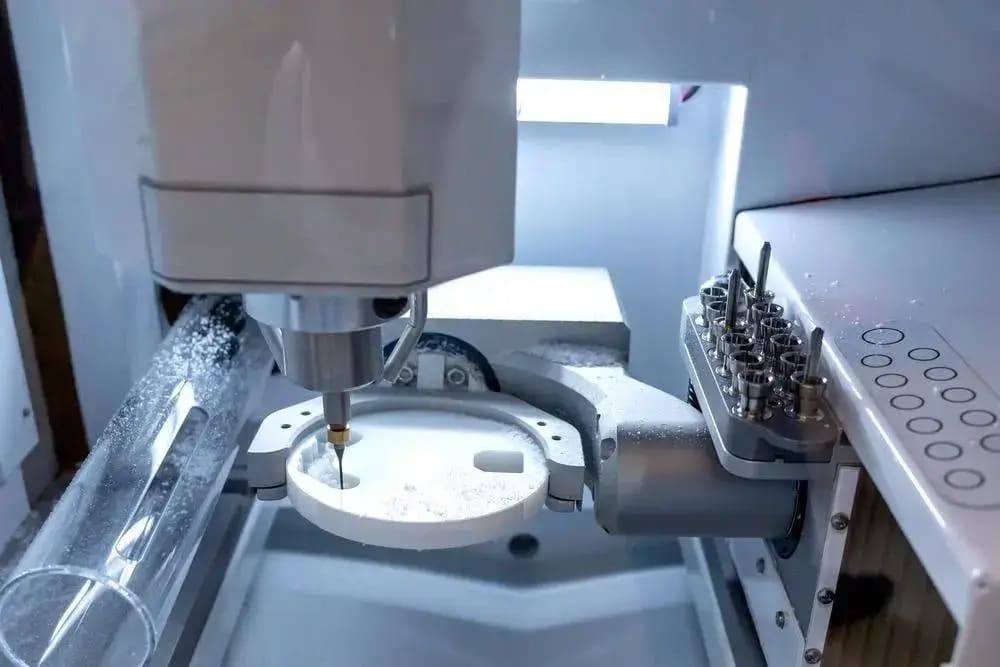
9.Challenges and Solutions in ceramic machining
(I) Challenges
Ceramic brittleness: Ceramics are prone to breakage or cracking, especially when subjected to force, vibration or defects, which can lead to waste, increased costs and production delays.
Challenges of complex designs: Ceramic materials are hard and difficult to shape complex designs. Small tools or high-precision machining techniques are required, which may affect the integrity of fine features or the realization of design details.
Tool wear: The hardness and abrasiveness of ceramics can severely wear cutting tools, causing rapid tool damage, increasing costs, reducing product accuracy and quality, and generating more waste.
(II) Solutions
Managing ceramic brittleness: This can be solved by improving the quality of ceramic materials (reducing raw material defects, using advanced sintering technology to reduce porosity, and carefully managing additive ingredients to improve toughness) and improving CNC machining processes (determining the best tool path and speed, monitoring cutting forces, and equipping with adaptive control systems to reduce vibration). Proper tool design (such as choosing diamond tools) can also help reduce cracks and stress.
Meeting the challenges of shaping complex designs: Using CAD software to conceptualize parts and optimize machining paths, selecting appropriate cutting tools (such as diamond tools), using multi-axis CNC machines to rotate and adjust workpieces, and combining other machining technologies can effectively manage the machining of complex designs and produce complex ceramic parts with high precision, tight tolerances and detailed features.
Solving tool wear issues: Tool wear can be reduced by using high-quality cutting tools made specifically for machining ceramics, or applying protective coatings on the tools (such as diamond-like carbon (DLC) coatings), while properly cooling or lubricating (using high-temperature coolants or lubricants), and adjusting cutting conditions (speeds and feed rates).
Conclusion
Ceramic machining excels in mass-producing high-precision, design-specific products and components, but ceramics’ inherent properties, such as brittleness and limited tensile strength, present challenges. Designing parts requires attention to detail to reduce the risk of breakage, using specialized tools that can handle the properties of ceramics is essential, and understanding the various types of ceramics is important to select the right material for your product.