Advantages of Aerospace CNC Machining and Defense Industry CNC Machining
Aerospace CNC machining is an important technology in the manufacturing industry. It uses computer-controlled machine tools to quickly and accurately complete the molding and manufacturing of parts. Especially in high-precision industries, CNC machining plays a vital role and greatly improves production and innovation capabilities. This article will explore the advantages and specific applications of aerospace CNC machining and defense industry CNC machining.
1.The purpose of CNC machining
The core goal of CNC machining is to transform digital designs into actual physical products. In the manufacturing process, the technology enables high precision and repeatability, which are essential for consistently and efficiently producing high-quality parts. By automating machining tasks, you can effectively reduce the probability of errors, shorten production time, and eliminate the need for manual adjustments.
This processing method is excellent at reducing waste, reducing defects, reducing manual operations and setup time, and is suitable for high-volume, low-volume production, and custom parts production. Modern CNC machines offer multi-axis capabilities, automatic tool changers and advanced automation features that significantly optimize production efficiency.
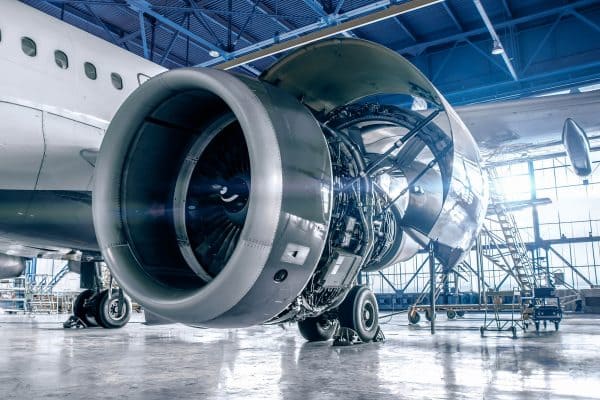
2.Materials commonly used in defense industry CNC machining and aerospace CNC machining
(i) Aluminum
Aluminum is lightweight and corrosion-resistant, making it an ideal material for aircraft structural components.
(ii) Titanium
Titanium is strong and lightweight, making it extremely valuable for components that are subject to high stress.
(iii) Stainless steel
Stainless steel is corrosion-resistant, has high tensile strength, a high melting point, and excellent durability.
(iv) Nickel alloys
Nickel alloys can withstand extremely high temperatures, are corrosion-resistant, have high hardness, are wear-resistant, and are resistant to erosion.
(v) Plastics
Plastics are often used to replace metals when weight, noise, and aesthetics are a concern. Engineering plastics are durable, extend part life, reduce maintenance, and avoid corrosion problems.
(vi) Composites
Composites are used to reduce weight while maintaining structural integrity.
3.Advantages of Aerospace CNC Machining and Defense Industry CNC Machining
(1) High accuracy and consistency
Aerospace CNC machining and defense CNC machining meet the stringent precision requirements of their industries. In these industries, small deviations can lead to failures, and consistency ensures uniformity in production, thereby maintaining high quality standards in large-scale manufacturing.
(2) Customization capabilities
The military often needs to create unique parts for new weapons or equipment, and CNC machining can quickly meet this customization need.
(3) Efficiency and speed
CNC machining improves production efficiency through high speed and automation, enabling shorter lead times and increased output while maintaining quality. Rapid production has strategic and tactical implications in the military, and automated processing minimizes human error.
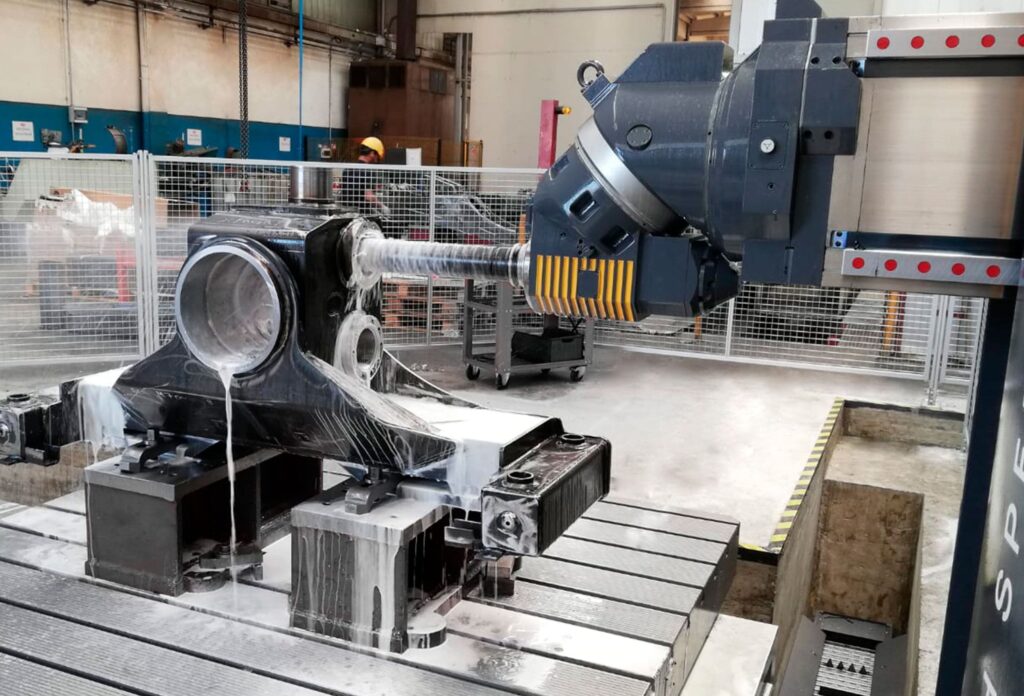
(4) Cost-effectiveness
CNC machining helps save costs due to reduced waste and shorter production times, which is a significant advantage in the military and defense sectors.
(5) Complex design
CNC machines are capable of creating complex designs, optimizing geometries, increasing strength and efficiency while reducing weight. In addition, it can process advanced materials such as titanium, superalloys and composites.
(6) Safety and reliability guarantee
In the aerospace and defense sector, component reliability is critical as failure can have serious consequences. CNC machined products are manufactured within tight tolerances and meet regulatory standards, helping to improve safety and reliability.
4.Specific applications of defense industry and aerospace CNC machining
(I) Aircraft and spacecraft manufacturing
The flight and space environment is extremely harsh, requiring parts to withstand extreme temperatures, vibrations and pressures. CNC machining can produce key parts such as wings, engines, landing gear and spacecraft elements with excellent precision and lasting quality.
(II) aerospace CNC machining
The normal operation of weapon systems depends on the accuracy and consistency of parts. Using CNC machining, parts for weapons such as guns, missiles, bombs, etc. can be manufactured with strict guarantees of precise dimensions to ensure the highest operational performance.
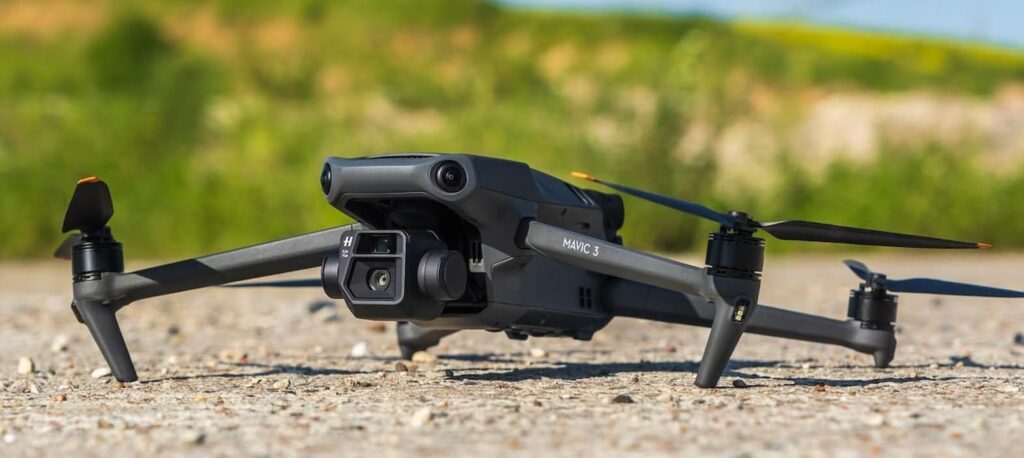
(III) Naval applications
The marine environment has special requirements for equipment, and parts need to be rust-proof and able to withstand harsh marine environments. CNC machining is used to manufacture parts for submarines, ships and vessels to ensure their reliability and long service life.
(IV) Communication and surveillance equipment manufacturing
Today’s war technology is highly dependent on advanced communication and surveillance technologies. The manufacturing of parts for drones, radar systems and satellites has a huge demand for CNC machining to ensure accuracy and efficiency in critical missions.
(V)Vehicle and Armored Vehicle Manufacturing
The Army’s various vehicles, such as tanks, armored personnel carriers, and support vehicles, have parts manufactured using CNC machining, which ensures the durability, mobility, and safety of the vehicles.
(VI)Radar and Electronic Systems Manufacturing
Radar and electronic systems are essential for detecting and tracking threats. CNC machining is used to manufacture important components such as antennas and circuit boards to ensure that these systems operate accurately and reliably.
(VII)Warship Component Manufacturing
Modern warships are complex systems that require a variety of components. Drive mechanisms, communication tools, weapon systems, and other key components are all manufactured using CNC machining to ensure that warships are mission-ready at all times.
Summary
In summary, Aerospace CNC machining and defense industry CNC machining are indispensable key technologies in the manufacturing industry. It brings many advantages to the military and defense fields through precise and efficient processing methods and the use of a variety of suitable materials. It is widely used in various key links, effectively ensuring the high performance and high reliability of military equipment and facilities, and providing solid technical support for national security and strategic implementation.