CNC metal cutting: the perfect combination of precision and efficiency
As an indispensable part of modern manufacturing, CNC metal cutting technology has been widely used in many industries, including metal manufacturing, construction engineering, shipbuilding and aerospace. The precision and efficiency of this technology make it a key tool for processing complex metal parts.
This article will introduce in detail the importance, basic principles and classification, core equipment and components, process control points and related issues of industry application of CNC metal cutting.
1.Definition, importance and process analysis of CNC metal cutting:
(1) Definition
CNC metal cutting refers to the process of cutting metal materials using CNC technology. CNC technology is a technology that controls the movement and processing of mechanical equipment through digital information. It uses digital information composed of symbols, text and numbers to realize automatic control of machine tools and other equipment, thereby completing the cutting, cutting or processing of metal materials.
(2) Importance
The importance of CNC metal cutting lies in that it improves production efficiency and processing accuracy, reduces manual operation, reduces production costs, and can handle complex geometric shapes and sizes to achieve automated production. It is one of the key technologies for modern manufacturing to achieve modern, automated and intelligent production.
(3) Application of metal cutting in industrial production:
Metal cutting is an indispensable process in the manufacturing industry. It involves the process of cutting, cutting or processing metal materials. Metal cutting technology can be used for various metal materials, including aluminum, steel, copper and stainless steel. Among them, aluminum metal cutting technology is widely used in automobile manufacturing, aerospace, machinery manufacturing, high-precision instruments and building structures.
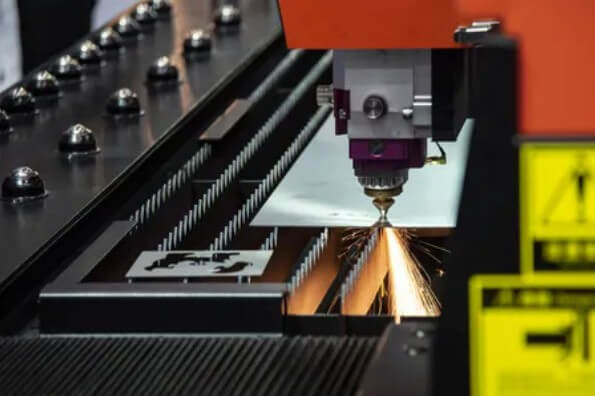
(4) CNC metal cutting process:
CNC metal cutting process includes many different cutting processes such as turning, drilling, milling, boring, cutting, grinding and threading. Each cutting process has its own special tools and equipment to achieve specific cutting operations.
With the rapid development of CNC technology, metal cutting is also developing in the direction of automation, high efficiency and high precision. CNC cutting machine tools can realize complex cutting operations through computer control systems, accurately control the movement of tools, improve cutting accuracy and repeatability, and greatly improve production efficiency and production capacity.
2.Basic principles and classification of CNC metal cutting technology
The basic concept of CNC metal cutting technology is to use digital programs to control the movement of cutting machinery, thereby realizing automatic cutting of metal materials. This technology ensures cutting accuracy and surface quality by precisely controlling the cutting path, speed and power.
CNC metal cutting technology can be mainly divided into the following types:
(1) Flame cutting:
It mainly uses the high-temperature flame generated by the mixed combustion of combustible gas and oxygen to heat and melt the metal, and then blows away the molten metal through a high-pressure oxygen flow to form a cut. This method is suitable for cutting thicker metal materials such as carbon steel and low-alloy steel, and has the advantages of low equipment cost and simple operation. However, the cutting accuracy and incision quality of flame cutting are relatively low, and the cutting speed is slow.
(2) Plasma cutting:
Metal is cut through a high-temperature and high-speed plasma arc. The plasma arc can generate a high temperature of more than 10,000°C, quickly melting and blowing away the metal material. This cutting method is suitable for a variety of metal materials such as stainless steel and aluminum alloy, and has the advantages of fast cutting speed, good incision quality and small deformation. The core of plasma cutting technology lies in the stability and energy density of the plasma arc. High-quality plasma cutting machines are usually equipped with advanced arc voltage automatic height adjustment systems and fine plasma power supplies to ensure the stability of the cutting process and the cutting effect.
(3) Laser cutting:
Use a high-energy-density laser beam to irradiate the surface of the material, convert light energy into heat energy, and quickly melt or vaporize the material to achieve cutting. Laser cutting has extremely high precision and cutting speed, and is suitable for various metal materials and non-metallic materials, such as steel, aluminum alloy, plastic, wood, etc. The advantage of laser cutting is that its cutting edge is smooth and burr-free, and the cutting accuracy can reach micron level, which is suitable for high-precision processing and the production of high value-added products.
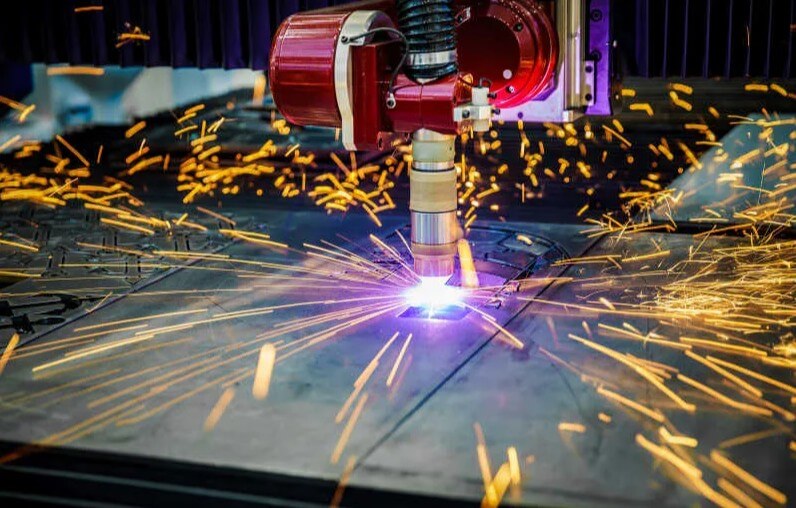
(4) High-pressure water jet cutting:
Use high-pressure water flow (sometimes with abrasives) to cut materials. This cutting method is suitable for almost all materials, including metals, glass, ceramics, etc., and has the advantages of no heat-affected zone during cutting and environmental protection. High-pressure water jet cutting technology is particularly suitable for processing heat-sensitive materials, such as titanium alloys and composite materials. The cutting process is free of thermal deformation, oxidation and smoke. It is a green and efficient cutting technology.
3.Core equipment and components of CNC metal cutting technology
CNC metal cutting technology is an indispensable part of modern manufacturing. It uses high-precision automated equipment to achieve rapid cutting of metal materials. The following will introduce the core equipment and components of CNC metal cutting technology in detail.
(1) CNC system:
The CNC system is the “brain” of the CNC cutting machine and consists of a computer system, a servo system, a control unit and an actuator. The computer system includes a computer host, a display and a keyboard for inputting and displaying cutting programs. The servo system realizes stepless speed regulation of the motor to ensure cutting accuracy. The control unit is responsible for processing manual and computer control signals and directing the actuator to complete the corresponding actions.
(2) Cutting machine tool:
The cutting machine tool is the main equipment for metal cutting, including a bed, a workbench, a cutting head and other parts. The bed provides support and stability, the workbench is used to fix and move the workpiece, and the cutting head performs the actual cutting operation. The cutting head can be a flame cutting head, a plasma cutting gun or a laser cutting head, which is selected according to the thickness of the workpiece and the material properties.
(3) Transmission system:
The transmission system is responsible for transmitting power and controlling the movement trajectory of the cutting head, mainly including servo motors, reducers and screws. Through precise control, the transmission system ensures that the cutting head performs high-precision cutting according to the preset path.
(4) Gas system:
The gas system includes gas supply pipelines, valves, pressure reducers, pressure gauges and electromagnetic gas valves, etc., which are used to control the supply of cutting gas. Cutting gases such as oxygen and acetylene react with materials to generate high temperatures during the cutting process, thereby achieving cutting.
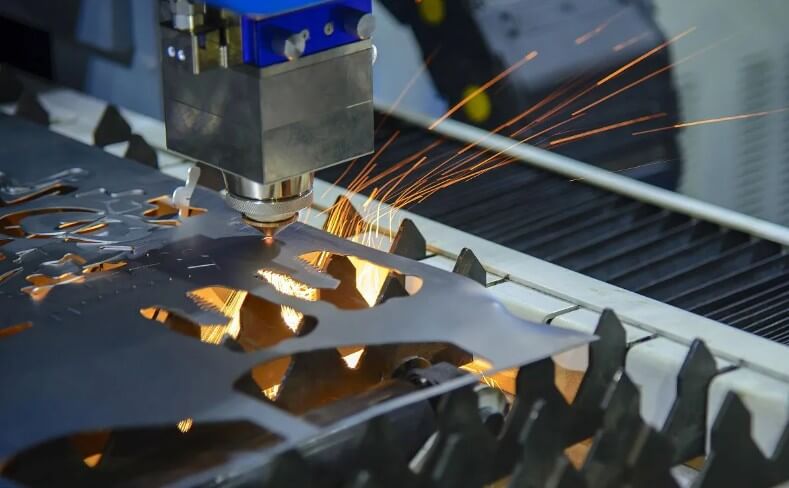
(5) Cooling system:
The cooling system provides coolant to cool and lubricate the lubrication points and processing areas of the machine tool to prevent failures and damage caused by friction and heat, and ensure the normal operation of the machine tool.
(6) Programming system:
The programming system is a tool that converts the cutting process into a code that can be understood by the computer, usually including CAD (computer-aided design) and CAM (computer-aided manufacturing) software. The programming system can realize the integration of the entire process of design, programming and production.
Summary:
The core equipment and components of CNC metal cutting technology work together to achieve efficient and accurate metal cutting processing, and promote the digitalization and intelligent development of the manufacturing industry.
4.Key points of process control of CNC metal cutting technology
CNC metal cutting technology is a high-precision and high-efficiency processing method that is widely used in the cutting of various metal materials. In the process of CNC metal cutting, the key points of process control mainly include the optimization of cutting parameters and the control of cutting quality.
(1) Optimization of cutting parameters:
1) Select the appropriate cutting speed:
The cutting speed should be determined according to the type and thickness of the material and the performance of the cutting machine. Too fast speed may result in a rough cutting surface, while too slow speed will affect production efficiency.
2) Adjust the cutting gas pressure:
The gas pressure directly affects the cutting quality and efficiency. Excessive pressure may cause the edge of the cut to melt, while too little pressure may cause incomplete cutting.
3) Control the focus position:
The focus position has an important influence on the cutting quality and efficiency. The focus should be located about 1/3 below the material surface to maximize the cutting depth and minimize the cut width.
4) Select a suitable nozzle:
The shape and size of the nozzle will affect the cutting quality and efficiency. The appropriate nozzle should be selected according to the cutting requirements.
5) Optimize the cutting path:
The cutting sequence and direction should be arranged reasonably during programming to reduce cutting deformation and improve cutting accuracy.
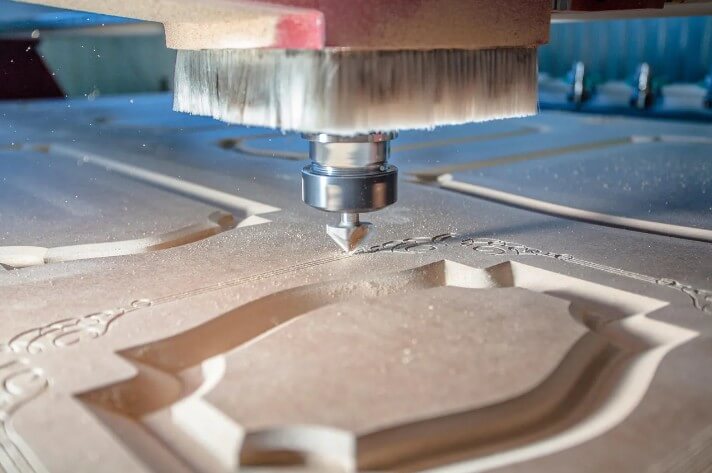
(2) Control of cutting quality:
Control cutting deformation: Cutting deformation can be effectively reduced by reasonably arranging the cutting sequence and direction, and adopting the new cutting method.
1) Arrangement of the lead-in line:
The lead-in line should be as short as possible and consistent with the running direction of the cutting machine to reduce material waste and cutting defects.
2) Workpiece preparation:
The workpiece should be selected from materials with good forging performance, good hardenability, and uniform internal structure, and should be subjected to appropriate heat treatment to reduce deformation after processing.
3) Selection and installation of electrode wire:
The electrode wire should be selected according to the width of the slit, the thickness of the workpiece and the size of the corner, and ensure that it is installed correctly and properly tensioned.
4) Use of auxiliary gas:
Select appropriate auxiliary gas, such as oxygen, nitrogen, etc., according to the cutting material to promote the cutting process and improve the cutting quality.
5) Control of the distance between the nozzle and the workpiece:
Maintain an appropriate distance between the nozzle end face and the workpiece surface, generally 0.5 to 2.0 mm, to ensure the stability of the cutting process.
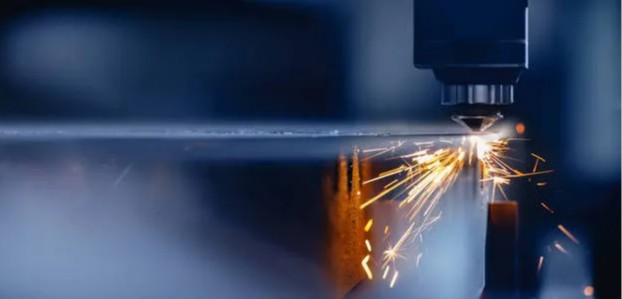
Summary:
Through the optimization and implementation of the above process control points, the accuracy and efficiency of CNC metal cutting can be significantly improved, while ensuring the cutting quality and meeting various processing requirements.
5.Application of CNC metal cutting technology
(1) Automobile manufacturing industry:
CNC metal cutting technology is widely used in the automobile manufacturing industry for cutting body structural parts, chassis parts, etc. Laser cutting technology can achieve high-precision cutting and improve the manufacturing quality of automobile parts.
(2) Aviation industry:
In the aviation field, CNC metal cutting technology is used to process aircraft structural parts, engine parts, etc. Three-dimensional CNC laser cutting machines can process complex curved parts and improve the performance and reliability of aircraft parts.
(3) Mechanical manufacturing:
CNC metal cutting is used in the field of mechanical manufacturing to process various metal parts, such as gears, shaft parts, etc. High-precision CNC cutting equipment can meet the requirements of precision and efficiency in mechanical manufacturing.
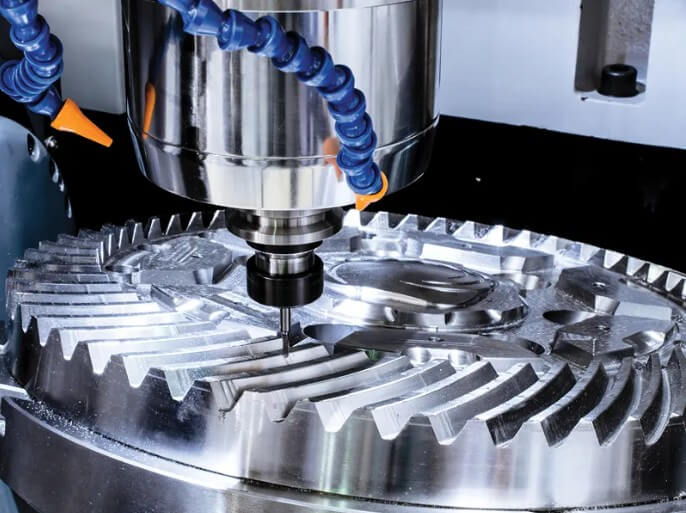
(4) Steel industry:
The steel industry uses CNC metal cutting technology for plate cutting, blanking and other operations. High-power laser cutting machines can process large-format thick plates and improve the efficiency of steel production.
(5) Shipbuilding industry:
In the field of shipbuilding, CNC metal cutting technology is used to cut hull structural parts, decks, etc. Laser cutting technology can meet the precision requirements of special boat manufacturing and promote the development of the “precision shipbuilding” era.
(6) National defense and military equipment:
CNC metal cutting is used in the field of national defense and military equipment to process complex curved parts such as helicopter propellers, improving the performance and production efficiency of military equipment.
6.Summary
In short, CNC metal cutting technology has been widely used in various industries with its high precision and high efficiency, promoting the modernization and intelligent development of the manufacturing industry.