Precision auto body: cutting-edge technology in the automotive industry
Precision auto body technology is a cutting-edge technology in modern automobile manufacturing. It is not only related to the beauty and comfort of the auto, but also directly affects the safety and performance of the auto This article will explore in depth the importance, components, structural design, manufacturing process and precision control of the precision auto body, as well as the advanced equipment and applications of precision auto body manufacturing.
1.The importance of precision auto body
Precision auto body occupies a pivotal position in automobile manufacturing. Its importance is mainly reflected in the following aspects:
(1) Load-bearing function:
The auto body not only carries passengers and cargo, but also serves as the installation basis for many parts. From the engine to the suspension system, these key components are directly or indirectly installed on the body to ensure that the vehicle can run normally.
(2) Safety protection:
In the event of a collision, the precision-designed body can absorb and disperse the collision energy to protect the safety of the passengers in the auto. High-strength steel and reasonable structural design provide passive safety protection. At the same time, the body shape design also takes into account aerodynamic factors to reduce wind resistance, improve driving stability, and enhance active safety.
(3) Shaping the exterior:
The exterior design of the auto body is an important reflection of the auto brand image. autos of different brands have unique body lines and styling styles to meet consumers’ aesthetic needs and brand recognition.
(4) Isolating the external environment:
The precision auto body can effectively insulate and reduce noise, prevent rain, dust, etc. from entering the auto, and ensure riding comfort and a clean and dry interior environment.
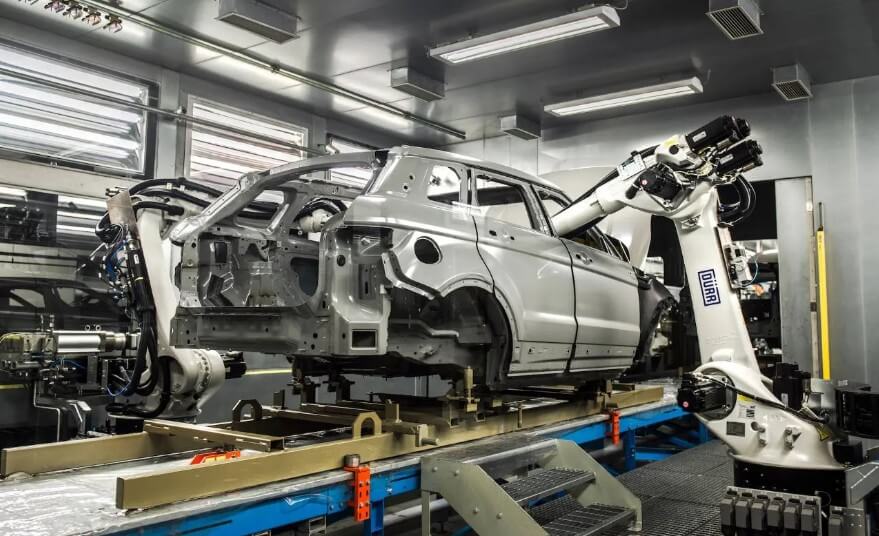
2.Components of the precision auto body
As a key part of the auto, the precision auto body’s complex structural design ensures the safety, comfort and stability of the vehicle. The precision auto body is mainly composed of the following parts:
(1) Front body
1) Front bumper: located at the front end of the vehicle, plays a protective and decorative role.
2) Front fender: installed on the lower side of the engine hood and the upper part of the front wheel, the main function is decoration and diversion.
3) Engine hood: a cover to maintain the engine compartment, which is convenient for repairing and inspecting the engine.
4) Front panel: separates the engine compartment from the passenger compartment to ensure passenger safety.
5) Front longitudinal beam: the main strength member of the front body, welded to the lower part of the body, providing support and stability.
(2) Middle body
1) Pillars, sill plates, floor: constitute the frame of the body, providing overall rigidity and strength.
2) Roof: the cover on the top of the auto, which may be equipped with a skylight, ventilation window or antenna, etc.
3) Door: the passage for passengers to get on and off, equipped with door locks, glass, glass lifter and other auxiliary facilities.
(3) Rear body
1) Luggage compartment and luggage compartment cover: provide storage space for storing items.
2) Rear side panel: the body sheet metal covering the rear wheels and the rear side of the body.
3) Rear bumper: located at the rear of the vehicle, plays a decorative and protective role.
(4) Body shell
1) Body frame: including the engine compartment assembly, roof assembly, floor assembly, side assembly, etc., is the supporting structure of the body.
2) Body panels: such as doors, engine hoods, front fenders, trunk lids, etc., covering the surface of the body frame.
(5) Load-bearing and non-load-bearing structures
1) Load-bearing body: There is no independent frame, and the body itself is the load-bearing structure. It has the advantages of small mass and low height, and is widely used in auto.
2) Non-load-bearing body: It has an independent frame, and the body and frame are connected by elastic elements. The advantages are high stability and safety. It is mostly used in trucks and off-road vehicles.
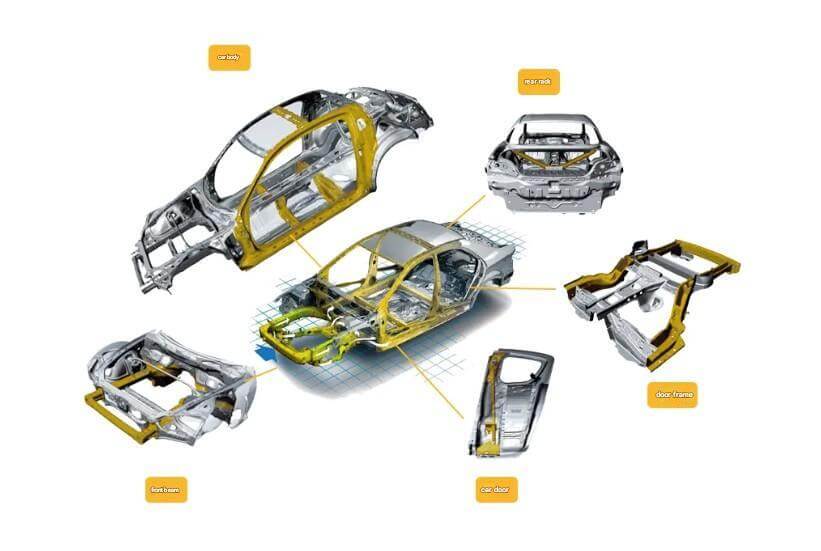
Summary:
The various parts of the precision auto body work together to provide drivers and passengers with a safe, comfortable and stable driving experience.
3.Precision auto body structure design
Precision auto body structure design is an important part of automotive engineering. It involves multiple aspects such as material selection and application, lightweight design, and structural strength and safety design. The following are detailed answers to these three aspects:
(1) Selection and application of body materials:
The selection of body materials needs to consider factors such as strength, weight, cost and processing performance. Traditional body materials are mainly steel, but with the development of technology, lightweight materials such as aluminum alloy, magnesium alloy, carbon fiber reinforced plastic (CFRP) are gradually being used. For example, aluminum alloy is used in body structural parts such as engine hoods and fenders to reduce weight due to its low density and high strength.
Magnesium alloy is the lightest metal structural material with high specific strength and specific stiffness, suitable for manufacturing parts that withstand impact loads and vibration. Composite materials such as CFRP are used in high-end models due to their high strength and lightweight characteristics, but the cost is relatively high.
(2) Lightweight design:
Body lightweight design is to reduce weight by combining reasonable structural design, optimized material distribution and advanced manufacturing processes under the premise of ensuring structural performance. Lightweighting can not only improve fuel efficiency, but also improve vehicle handling and acceleration performance.
Lightweight design methods include the use of lightweight materials such as high-strength steel, aluminum alloy, magnesium alloy, plastic and composite materials, as well as advanced manufacturing processes such as laser welded blanks (TWB) and continuously variable section rolled plates (TRB).
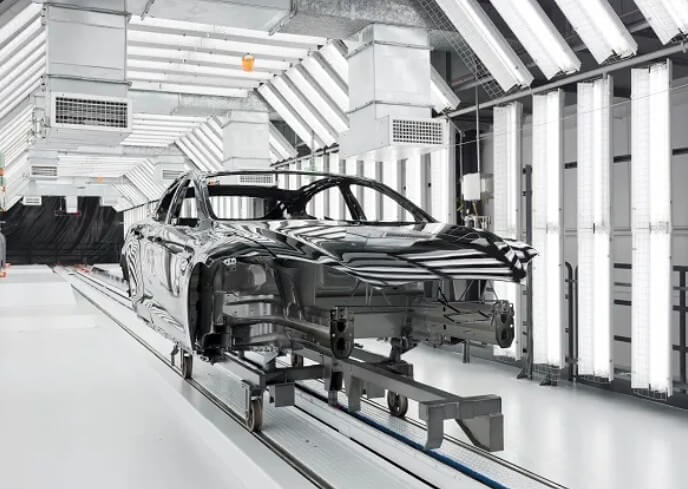
(3) Structural strength and safety design:
The structural strength design of the vehicle body needs to ensure that the vehicle can maintain sufficient rigidity and strength under various working conditions, and at the same time be able to effectively absorb and disperse collision energy to protect the safety of the occupants. For example, the front structure of the vehicle body should be designed to be able to deform step by step and absorb energy during a collision, while the body cabin needs to remain strong and reliable to ensure the effective survival space of the occupants.
Safety design also includes the use of high-strength materials, such as high-strength steel and advanced high-strength steel (AHSS), and the addition of reinforcements to key parts such as doors and door sill beams to improve the impact strength. In addition, the reasonable design of the beam frame structure of the cabin to effectively transfer the lateral impact force to the beams, columns, door sills, floors, roofs and other components with load-bearing capacity on the body structure is also an important measure to improve the safety of the vehicle body.
4.Precision auto body manufacturing process and precision control
In the modern automobile manufacturing industry, precision auto body manufacturing process and precision control are key links to ensure the quality and performance of the vehicle. As an important part of the vehicle, the advancement of its manufacturing process and the level of precision control directly affect the safety, comfort and durability of the vehicle. The following is an introduction to the main processes of precision auto body manufacturing:
(1) Stamping technology
Stamping technology is one of the basic processes of precision auto body manufacturing. It is to place metal sheets in a stamping machine and use a mold to apply pressure to them so that they are deformed into parts of the desired shape. The accuracy of the stamping process directly affects the accuracy of subsequent welding and assembly.
1) Mold design and manufacturing:
The mold is the core of the stamping process. Its design and manufacturing accuracy determine the quality of the stamped parts. Modern mold manufacturing widely uses CAD/CAM technology to ensure the accuracy and surface quality of the mold through three-dimensional modeling and CNC machining.
2) Material selection:
The material selection of stamping parts is crucial. Common materials include high-strength steel, aluminum alloy, etc. The performance of the material directly affects the formability and final strength of the stamped parts.
3) Stamping process parameter control:
Parameters such as pressure, speed, and temperature during the stamping process need to be precisely controlled to ensure the dimensional accuracy and surface quality of the stamped parts. Modern stamping equipment is generally equipped with a closed-loop control system to monitor and adjust process parameters in real time.
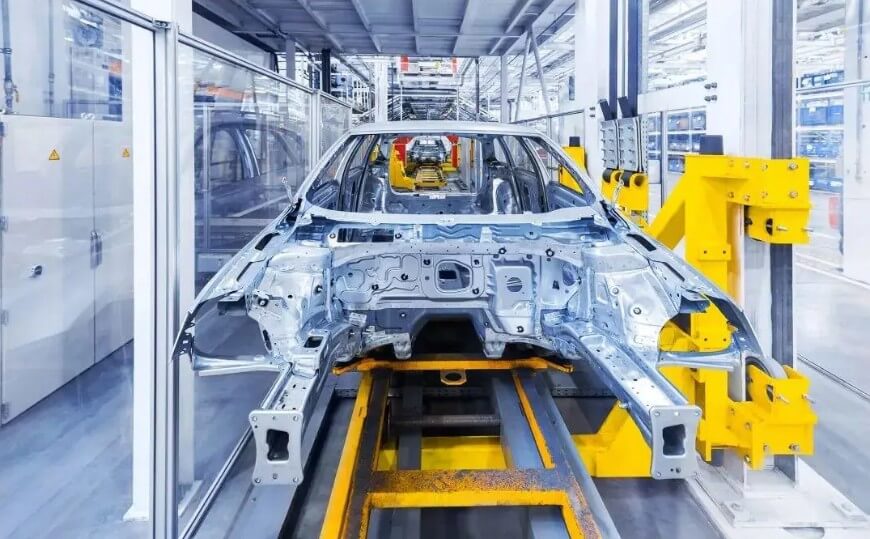
(2) Welding technology
Welding technology is a key link in precision auto body manufacturing. It forms a complete autobody structure by connecting multiple stamping parts together. The welding quality directly affects the strength and rigidity of the auto body.
1) Resistance spot welding:
Resistance spot welding is one of the most commonly used methods in auto body welding. The resistance heat generated by the current passing through the contact surface of the workpiece melts it and forms a weld spot. The widespread use of spot welding robots has improved welding accuracy and consistency.
2) Laser welding:
Laser welding is a high-precision and high-efficiency welding method suitable for welding materials such as high-strength steel and aluminum alloy. Laser welding can significantly improve the strength and sealing of the auto body.
3) Welding quality inspection:
After welding is completed, the welding quality needs to be inspected. Commonly used inspection methods include non-destructive testing (NDT) and destructive testing. NDT technologies such as ultrasonic testing and X-ray testing can effectively detect welding defects and ensure welding quality.
(3) Painting and surface treatment
Painting and surface treatment are the last key link in precision autobody manufacturing. Its main purpose is to improve the corrosion resistance, weather resistance and aesthetics of the auto body.
1) Pretreatment:
Before painting, the body surface needs to be cleaned and phosphated to remove oil and rust on the surface and improve the adhesion of the paint.
2) Painting process:
Modern automobile painting generally adopts a three-coat system, namely electrophoretic primer, intermediate coating and topcoat. Electrophoretic primer can provide good anti-corrosion performance, intermediate coating is mainly used to improve the flatness of the coating and the adhesion of the topcoat, and the topcoat determines the appearance quality and weather resistance of the body.
3) Painting equipment and technology:
Advanced painting equipment such as electrostatic sprayers and robot spraying systems can accurately control the thickness and uniformity of the coating and reduce painting defects.
4) Quality inspection:
After painting, the quality of the coating needs to be inspected, including thickness inspection, adhesion inspection and appearance inspection, to ensure that the coating quality meets the standards.
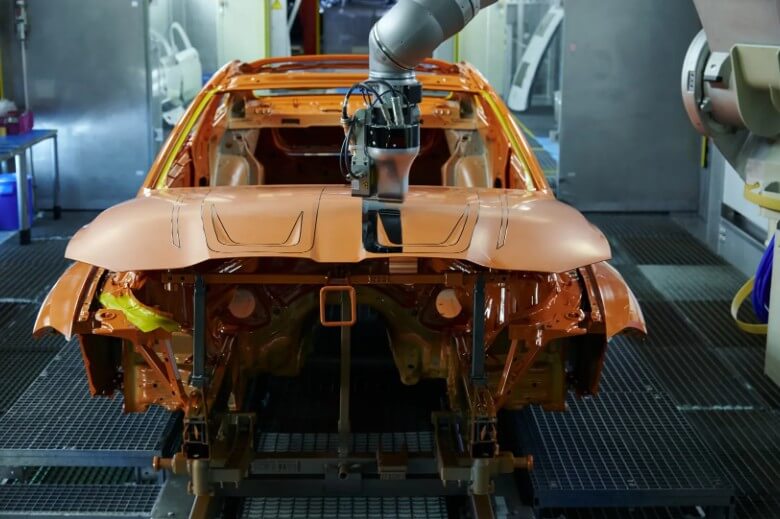
Summary:
Precision auto body manufacturing process and precision control is a systematic project involving multiple links and multiple technologies. Stamping technology, welding technology, painting and surface treatment are the core processes of precision auto body manufacturing. Their precision control level directly affects the quality and performance of the final product.
5.Advanced equipment and applications for precision auto body manufacturing
In modern manufacturing, the processing requirements for precision auto bodies are getting higher and higher. Traditional manufacturing equipment can no longer meet the production needs of high efficiency and high precision. In order to meet this challenge, advanced manufacturing equipment and technology have emerged. The following will introduce several key advanced manufacturing equipment and their applications in precision auto body manufacturing.
(1) CNC machining center
1) Principles and advantages
The CNC machining center is one of the core equipment in precision auto body manufacturing. It realizes automated processing through a computer numerical control system and can perform a variety of processing operations such as high-precision milling, drilling, and boring. The advantages of the CNC machining center are its high efficiency, stability and flexibility. It can significantly shorten the processing time and improve production efficiency. At the same time, it can reduce the errors caused by human operation and ensure the dimensional accuracy and surface quality of auto body parts.
2) Application
In precision auto body manufacturing, CNC machining centers are widely used to process various complex-shaped parts, such as doors, window frames, engine hoods, etc. High-precision machining enables these parts to achieve a higher degree of fit during assembly, thereby improving the quality and performance of the entire vehicle.
(2) Robotic automated production line
1) Principles and advantages
Robotic automated production line is an indispensable part of modern precision auto body manufacturing. Industrial robots can simulate human operations and perform welding, painting, assembly and other processes. Compared with traditional manual operations, robotic automated production lines have higher efficiency, consistency and safety.
2) Application
In the welding process, robots can perform high-precision spot welding and arc welding to ensure welding quality and strength. In the painting process, robots can evenly spray auto paint to avoid the uneven coating problem that may be caused by manual operation. In addition, robotic automated production lines can also achieve rapid switching of multiple production modes through programming, adapt to the production needs of different models, and improve the flexibility of the production line.
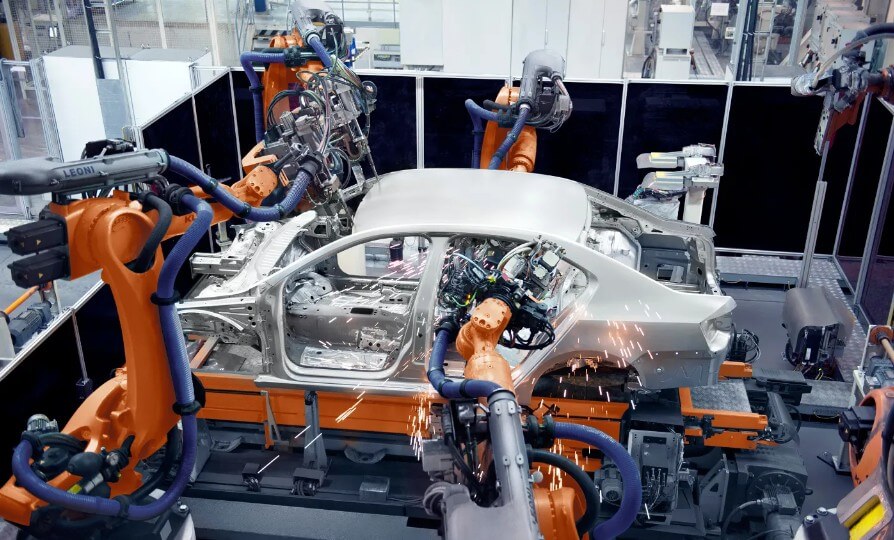
(3) 3D laser scanner
1) Principle and advantages
3D laser scanner is a high-precision detection equipment that can quickly and accurately obtain the 3D geometric information of an object. Through 3D laser scanning, manufacturers can promptly detect the dimensional deviation and surface defects of parts and make corresponding adjustments and improvements. In addition, 3D laser scanning data can also be used for reverse engineering to help manufacturers optimize product design and improve the overall performance of the auto body.
2) Application
In precision auto body manufacturing, 3D laser scanners are widely used for quality inspection of parts and verification of the overall dimensions of the auto body.
(4) Additive manufacturing equipment
1) Principle and advantages
Additive manufacturing, also known as 3D printing, is a rapid prototyping technology. Through additive manufacturing, manufacturers can quickly verify the feasibility of design solutions and shorten the new product development cycle.
2) Application
In precision auto body manufacturing, additive manufacturing equipment is used for rapid prototyping and small batch production. In addition, additive manufacturing can also be used to produce some complex structures or customized parts. For example, additive manufacturing technology can be used to produce lightweight auto body structural parts to improve fuel efficiency while meeting personalized needs.
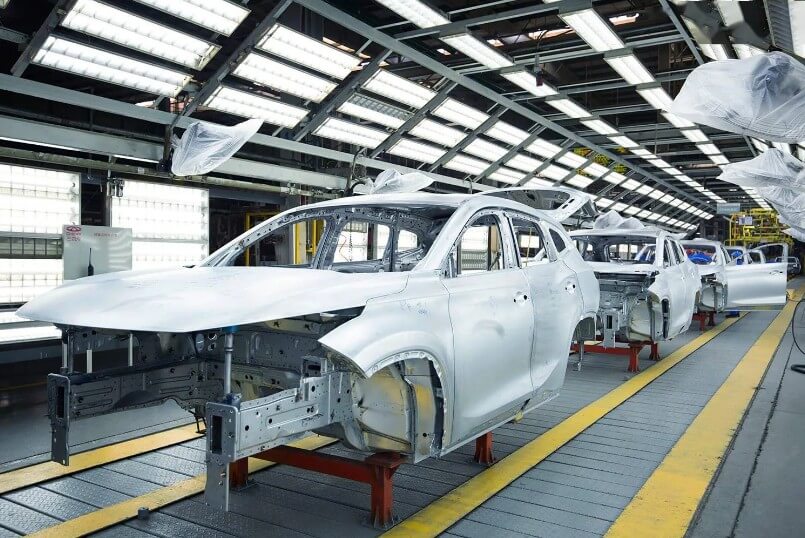
6.Summary
In summary, the precision auto body manufacturing process and precision control is a systematic project. Advanced production processes and manufacturing equipment jointly promote the continuous development and innovation of precision auto body technology.
3 Comments