Exploring Precision Spare Parts: How to Achieve High-end Manufacturing
Precision spare parts play an indispensable role in modern manufacturing, whether it is high-end electronic products, complex machinery and equipment, or cutting-edge aviation and spacecraft, are inseparable from these small but vital components. Precision spare parts are not only the cornerstone of industrial production, but also a key factor in promoting technological progress and innovation. This article will comprehensively introduce the definition of precision spare parts, importance, application areas, material selection and processing, processing technology, measurement and control technology and other related content.
1.Definition and importance analysis of precision spare parts
(1) Definition
Precision spare parts refer to those spare parts with high dimensional accuracy, good surface quality and excellent material properties, which are usually used in high-precision equipment or instruments and play a vital role in the performance and reliability of the whole equipment. These parts are used in a wide range of high-tech applications including, but not limited to, aerospace, medical devices and high-end manufacturing. Key characteristics of precision parts include dimensional accuracy, material and performance.

(2) Importance Analysis
In the modern industrial field, the importance of precision spare parts is self-evident. They not only ensure the overall accuracy of mechanical equipment, but also improve the performance and reliability of the equipment. For example, in CNC machine tools, high-precision screws, guide rails and other spare parts can ensure the machining accuracy of the machine tool, so as to produce high-quality products.
High-quality precision spare parts can improve the performance and reliability of machinery. For example, high-strength gears, shafts and other spare parts can withstand greater loads, improve mechanical transmission efficiency and service life. At the same time, the surface quality of precision machined spare parts is good, and the friction coefficient is small, which can reduce the energy loss and wear of machinery.
2.Overview of the application fields of precision spare parts
(1) Aerospace:
In the field of aerospace, precision spare parts are used to manufacture engines, flight control systems and other key components, and their precision and reliability are directly related to flight safety. For example, the turbine blades and combustion chamber components in the aviation engine need to withstand extreme high temperature and high pressure environment, so the choice of materials and processing precision of these spare parts is very high.
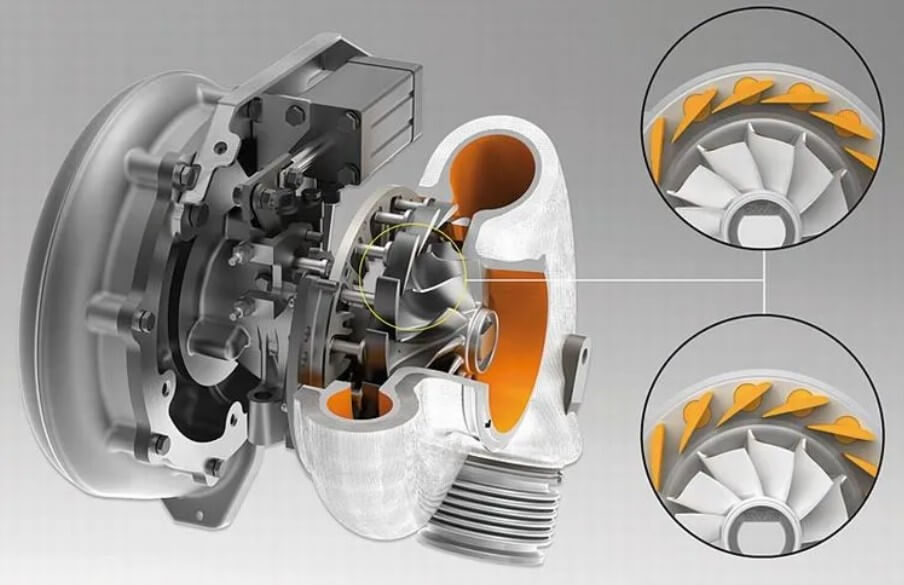
(2) medical equipment:
The demand for precision parts in the field of medical equipment is also urgent, such as surgical robots, high-precision diagnostic equipment, etc. The precision of the parts of these devices directly affects the treatment effect and patient safety. For example, high-precision medical devices such as minimally invasive surgical instruments and artificial joints, etc., need to have extremely high dimensional accuracy and surface quality to ensure their reliability and safety in surgery.
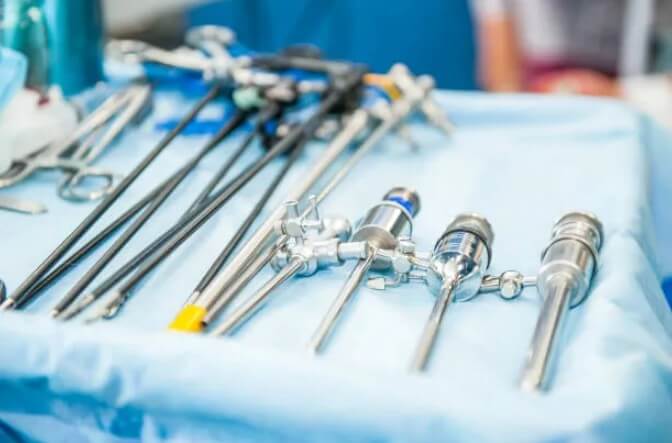
(3) High-end manufacturing:
In high-end manufacturing industries, such as semiconductor manufacturing equipment and precision instruments, precision spare parts are the basis for ensuring high performance and stable operation of the equipment. For example, semiconductor manufacturing equipment in the precision parts need to achieve nanometer-level processing accuracy to ensure the accuracy and quality of chip manufacturing.
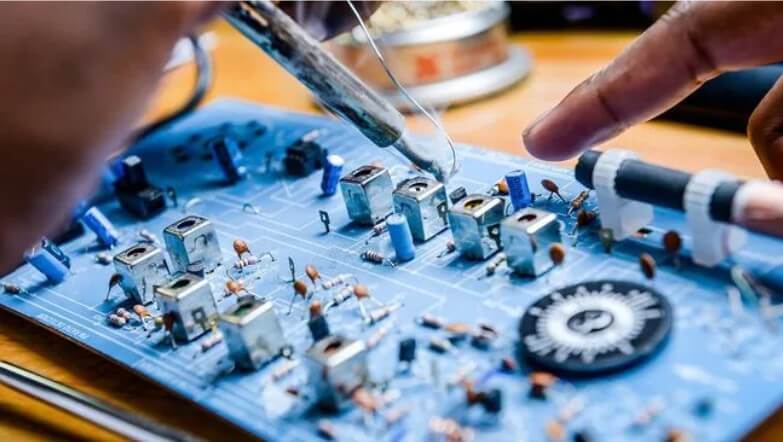
3.Material selection and processing of precision spare parts
(1) Material selection criteria
1) Material performance, processability and other factors
When choosing materials for precision spare parts, the first thing to consider is their use and performance in the working environment. The mechanical properties of the material, such as strength, hardness, and wear resistance, are key factors in the selection. For example, for parts used in high-strength environments, materials with high strength and good toughness need to be selected. In addition, the processability and cost of the material are also factors that cannot be ignored.
2) Select the appropriate material according to the application scenario
In precision hardware spare parts processing, the choice of materials is crucial. Different application scenarios have different requirements for materials. For example, in the aerospace field, commonly used materials include high-temperature alloys and titanium alloys, which have excellent high-temperature resistance and strength and can meet the needs of use in extreme environments. In the field of medical equipment, materials such as stainless steel and titanium alloys are widely used for their good biocompatibility and corrosion resistance. In the high-end manufacturing industry, commonly used materials include aluminum alloys, copper alloys, etc. These materials have good processability and conductivity.
(2) Material processing technology
Material processing technology is crucial for improving the performance of precision parts. In the material treatment process of precision spare parts, heat treatment and surface treatment are two very important links.
1) Heat treatment technology
Heat treatment is the key process to improve the performance of metal materials. Through the process of heating, holding and cooling, the microstructure of the material can be changed, so as to adjust its hardness, strength and toughness. For precision tools and molds and other spare parts, heat treatment is particularly important. High hardness and high strength of the material after appropriate heat treatment, can significantly extend its service life and improve cutting performance. For example, high-speed steel tools after quenching and tempering treatment, can obtain excellent hardness and toughness, to meet the needs of high-intensity cutting.
2) surface treatment technology
The surface treatment technology of precision spare parts is an important means of improving its performance. Among them, electroplating technology by depositing a layer of metal film on the surface of spare parts, effectively enhancing its wear resistance, corrosion resistance and aesthetics. For example, in the field of medical devices, stainless steel parts can significantly improve their corrosion resistance and meet strict hygiene requirements by electroplating nickel or chromium. In addition, coating technology is also widely used in precision parts, such as in the engine piston surface coated with ceramic materials, can significantly improve its heat resistance and wear resistance.
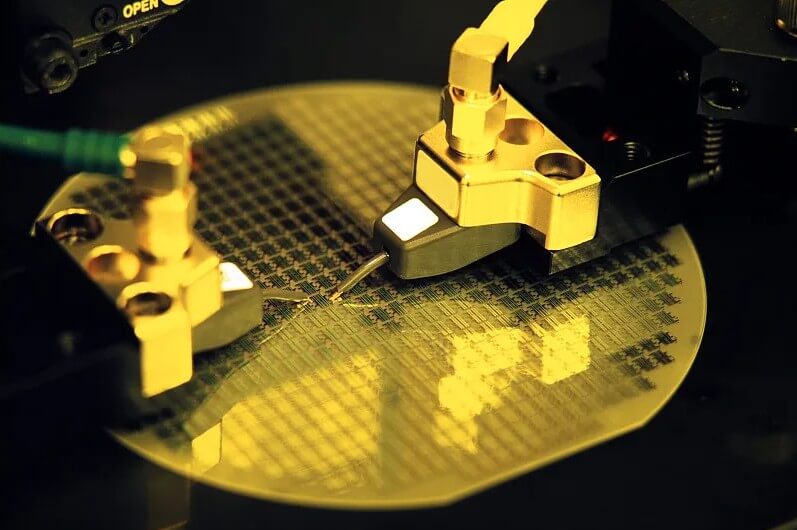
4.Precision spare parts processing technology details
Precision spare parts processing technology in the modern manufacturing industry occupies a pivotal position, its high efficiency, high precision and high reliability characteristics, to meet the demand for high-quality parts in various industries. The following points will be introduced in detail CNC machining technology and special processing technology:
(1) CNC machining technology
CNC machining technology is the core component of modern precision machining. CNC machine tools through the computer program control, can automatically complete a variety of complex processing operations. CNC machining technology mainly includes CNC turning, CNC milling and CNC grinding. They are characterized by high precision, high efficiency and high flexibility, and are widely used in the processing of precision spare parts of various materials and shapes.
1) CNC turning
CNC turning is mainly used for the processing of rotating parts, such as shafts and disk parts. Through the CNC system to control the movement of the tool trajectory, can realize high precision internal and external turning, face turning, grooving and threading. CNC turning can handle a variety of materials, including steel, aluminum, copper and some difficult-to-machine materials, such as titanium alloys and high-temperature alloys.
2) CNC Milling
CNC milling is suitable for the processing of complex shape parts, such as molds, aerospace structural components. CNC milling machine can carry out multi-axis linkage processing, to realize the three-dimensional space in any shape processing. High-precision CNC milling technology can ensure the dimensional accuracy and surface quality of precision spare parts, which are widely used in aerospace, automotive and medical equipment and other fields.
3)Numerical control grinding
CNC grinding is mainly used to improve the surface quality and dimensional accuracy of parts. CNC grinding machine can carry out external grinding, internal grinding, plane grinding and other grinding operations. Through the selection of appropriate grinding wheels and grinding parameters, CNC grinding can achieve sub-micron surface roughness and very high dimensional accuracy.
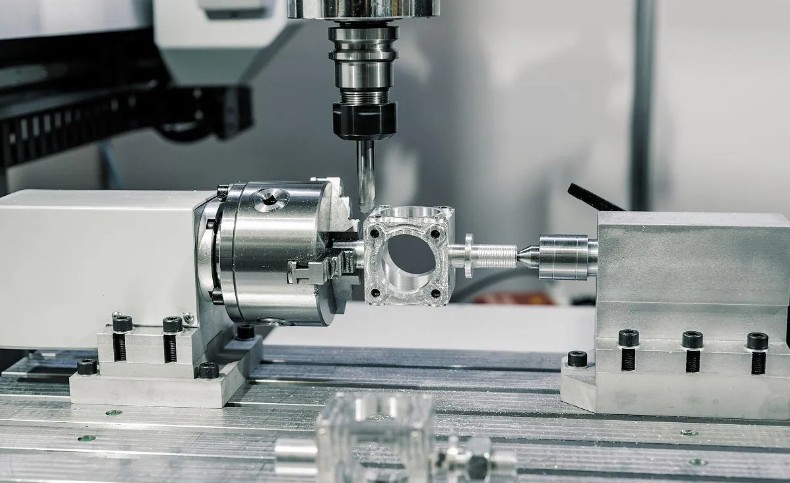
(2) Special processing technology
Special processing technology is also indispensable in precision parts processing. These technologies are usually used to process traditional machining difficult to deal with the material or shape, including EDM, laser processing, ultrasonic processing, electrolytic processing.
1) Electrical Discharge Machining (EDM):
Electrical Discharge Machining (EDM) cuts or shapes materials through electric spark discharge, and is suitable for hard-to-machine materials such as carbide and stainless steel. This technology is capable of processing complex shapes and high-precision precision spare parts, which are widely used in mold manufacturing and aerospace fields.
2) laser processing:
Laser processing technology utilizes a high energy density laser beam to cut, punch and weld materials. Laser processing has high precision, high efficiency and high flexibility, suitable for microfabrication and flexible manufacturing areas, such as electronic components, medical equipment and so on.
3) ultrasonic processing:
Ultrasonic machining utilizes ultrasonic vibration to grind, punch and polish materials, and is suitable for hard and brittle materials such as gemstones and ceramics. This technology can achieve high precision and low surface roughness processing, widely used in the manufacture of optical components and precision medical devices.
4) Electrolytic machining:
Electrolytic machining removes material through electrolysis and is suitable for the machining of hard, high-strength metal materials such as titanium alloys and high-temperature alloys. Electrolytic machining can achieve high precision and surface quality, and is widely used in the manufacture of aircraft engine blades and impellers.
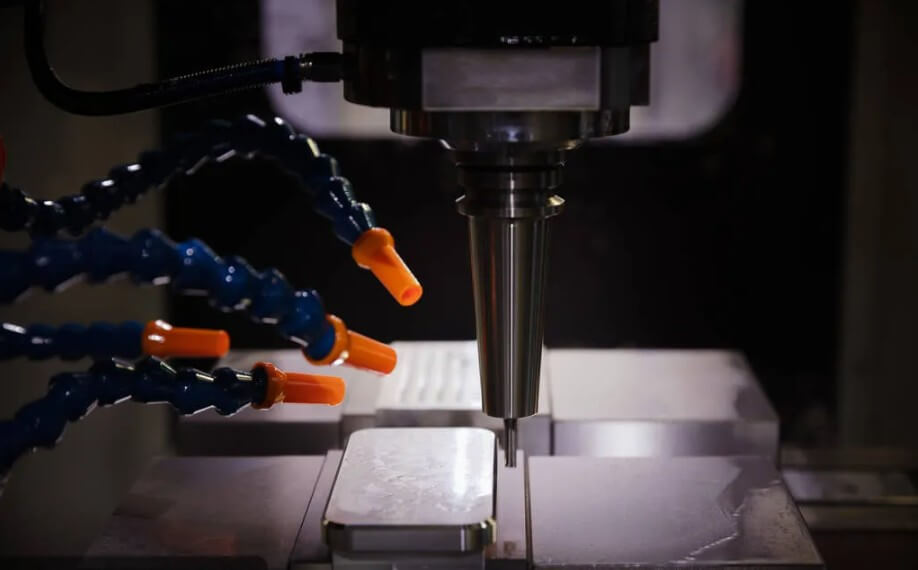
Summary:
Precision spare parts processing technology continues to push forward, CNC machining technology and the combined application of special processing technology, so that the manufacturing industry can produce higher precision, higher quality spare parts to meet the growing demand of various industries.
5.Precision spare parts of the measurement and control technology
(1) Precision measurement technology
Precision measurement technology is also vital in the process of spare parts processing. Precision measuring equipments such as coordinate measuring instrument, optical microscope and contour meter can accurately detect the size, shape and surface roughness of parts. By comparing with the design drawings, these technologies can detect and correct processing errors in time. Some high-end CNC machining centers are equipped with online measurement systems, but also in the machining process to achieve automatic measurement and compensation, thus further improving processing accuracy and efficiency.
(2) quality control and data analysis:
Through statistical process control (SPC) and other methods, real-time monitoring and analysis of measurement data, timely detection and correction of abnormalities in the production process of precision spare parts. At the same time, using big data technology, historical data is analyzed to optimize the production process and improve product consistency.
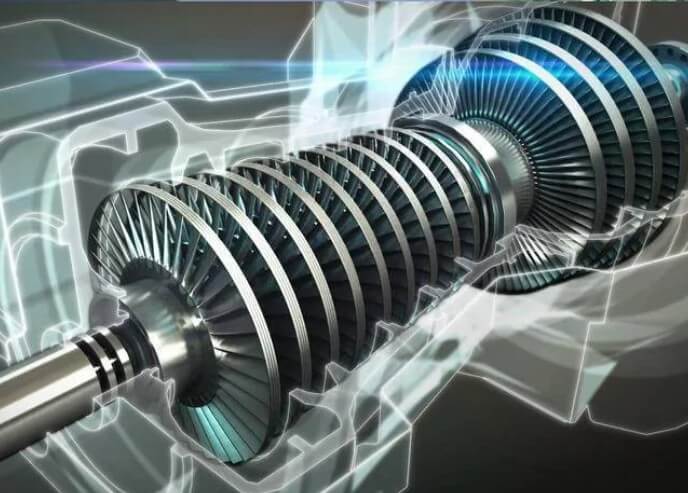
6.Summary
As an important part of modern industry, the importance of precision spare parts is self-evident.
Through core technologies such as high-precision processing equipment, precision measurement technology, advanced processing technology and strict quality control, the precision spare parts industry will continue to provide a solid guarantee for the development of various high-tech fields.
1 Comment