CNC metal: the key to improving machining accuracy and efficiency
CNC metal processing technology is a method of precision processing of metals through computer digital control technology. This technology enables machine tools to automatically complete complex processing tasks according to preset programs, and has the characteristics of high precision, high efficiency and high adaptability. This article will discuss the definition and characteristics of CNC metal processing, processing equipment and application fields, an overview of key technologies of CNC metal processing, how to choose suitable cutting tools, and the practical application fields of CNC metal technology.
1.Definition and characteristics of CNC metal processing
CNC metal processing is a modern manufacturing technology that uses digital programs to control machine tools to automatically process metal workpieces. Its core lies in controlling various movements of machine tools through pre-written CNC programs to achieve precise processing of metal materials. CNC metal processing has the following significant characteristics:
(1) High precision and stable processing quality:
CNC machine tools control the processing process through digital programs, eliminating human operation errors, and can use software to compensate and correct errors, thereby ensuring the stability of processing accuracy and quality.
(2) High productivity:
CNC metal processing can shorten production preparation time and increase the ratio of cutting processing time. Its strong structural rigidity and automation capabilities make the processing process more efficient, especially in the processing of complex parts, the efficiency is far higher than that of ordinary machine tools.
(3) Wide adaptability and flexibility:
By changing the CNC program, the machine tool can quickly adapt to the processing of parts of different types and shapes, and can complete complex surface processing that is difficult to complete with ordinary machine tools, which reflects great flexibility.
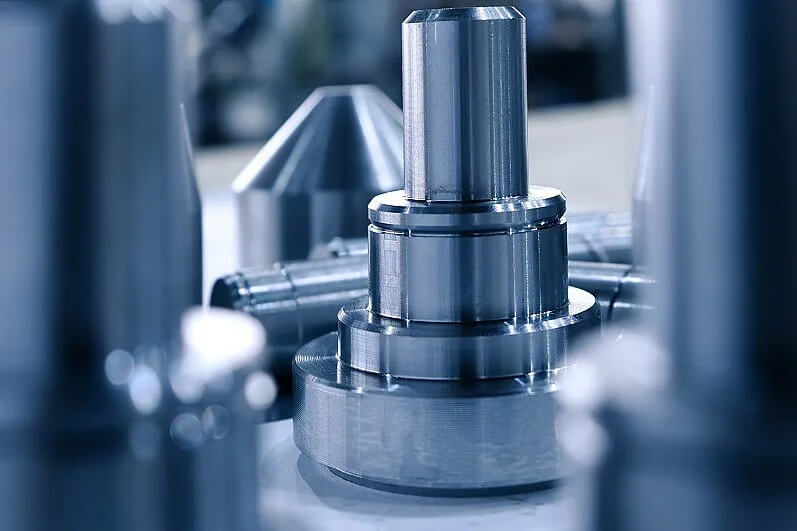
(4) Reduce labor intensity and improve working conditions:
CNC metal processing has a high degree of automation, and operators only need to program and monitor, which greatly reduces labor intensity and improves working conditions.
(5) Favorable to modern production management:
The processing time of parts in CNC metal processing can be accurately calculated, which simplifies the inspection and management of workpieces and fixtures, and facilitates the formation of a small-batch production system controlled and managed by computers, realizing production automation and optimization.
2.Analysis of CNC metal processing equipment and application fields
(1) CNC lathe:
Mainly used for processing rotating parts, such as shafts and disc parts. It has the characteristics of high precision and high efficiency and is suitable for mass production. It has stable performance and is relatively simple to operate, and is suitable for the processing of small and medium-sized workpieces.
(2) CNC milling machine:
It is suitable for the processing of flat contour, variable bevel and spatial curved contour parts. CNC milling machines have high processing accuracy and flexibility, and can process complex-shaped workpieces. They are widely used in mold manufacturing and aerospace fields.
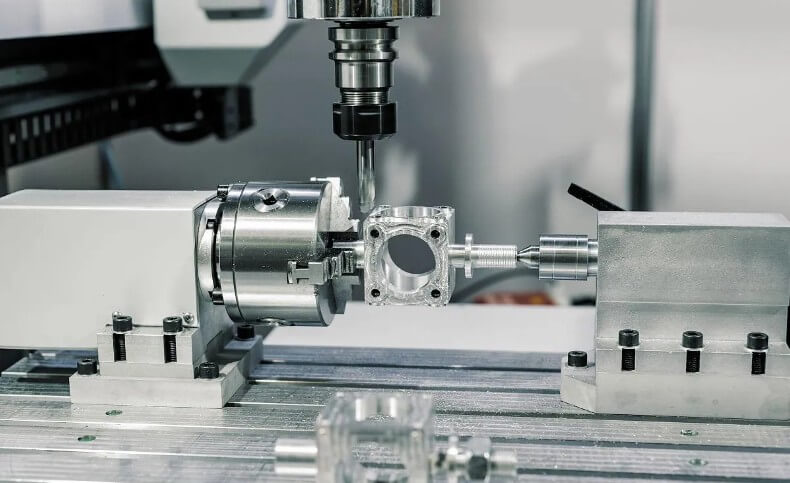
(3) Machining center:
It is equipped with a tool magazine and automatic tool changing device, and can realize continuous processing of multiple processes. Vertical machining centers are suitable for processing workpieces with smaller height dimensions, while horizontal machining centers are suitable for processing large workpieces or workpieces with larger height dimensions. Machining centers are widely used in the fields of automobiles, aerospace and mold manufacturing.
(4) CNC grinding machines:
It is mainly used for high-precision grinding processing, such as precision bearings, gears, etc. CNC grinding machines have high precision and stable performance and are suitable for processing workpieces with extremely high surface quality requirements.
(5) CNC boring machines:
It is suitable for hole processing of large box-type parts and has the characteristics of high precision and high efficiency. CNC boring machines are widely used in machine tool manufacturing, aerospace, energy equipment and other fields.
(6) CNC wire cutting machine tools:
Using electric spark wire cutting technology, it is suitable for processing molds and parts of various complex shapes. CNC wire cutting machine tools have the characteristics of high precision and high efficiency, and are widely used in mold manufacturing and precision parts processing.
(7) CNC laser cutting machine tools:
Using laser beams for cutting, it is suitable for cutting metal sheets. CNC laser cutting machine tools have the characteristics of fast cutting speed, high precision and small heat-affected zone, and are widely used in automobile, aerospace and electronic manufacturing and other fields.
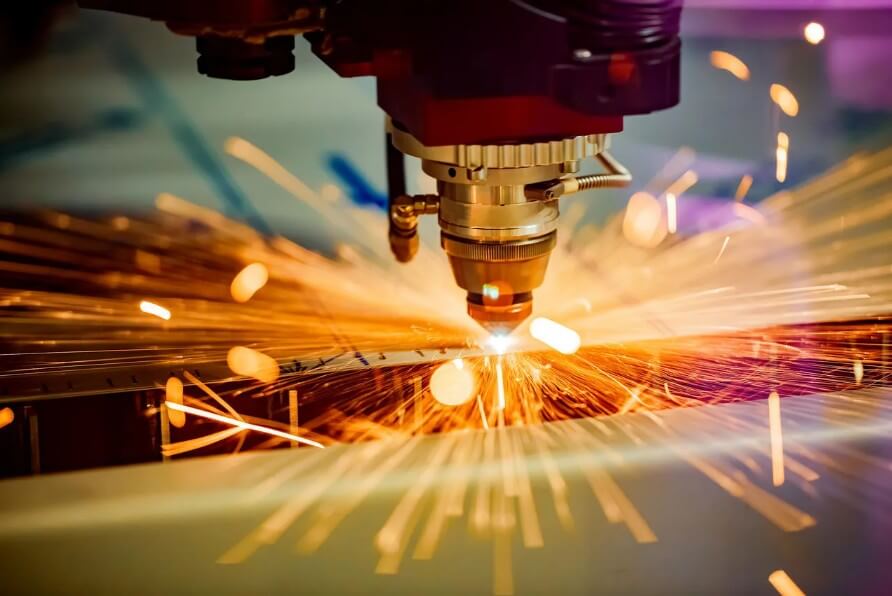
3.Overview of key technologies in CNC metal processing
CNC metal processing is a complex and high-precision technology involving multiple key technical links. The following are the core points:
(1) High-speed cutting technology:
High-speed cutting technology is one of the key technologies in CNC metal processing. By increasing the cutting speed and feed speed, the processing efficiency and surface quality can be significantly improved. High-speed cutting machine tools must have a high-speed spindle unit and a high-speed feed system. The high-speed spindle unit includes the electric spindle, high-speed bearings and lubrication and cooling system, while the high-speed feed system involves high acceleration and high positioning accuracy drive technology, such as linear motors and rolling element guide technology.
(2) Tool technology:
The selection and use of tools directly affect the CNC metal processing effect. High-speed cutting tools usually use materials such as cemented carbide, polycrystalline diamond (PCD), polycrystalline cubic boron nitride (PCBN) and ceramics. These materials have high hardness, high wear resistance and high thermal stability, and can withstand the high temperature and high pressure generated by high-speed cutting.
(3) CNC system:
The CNC system is the “brain” of the CNC machine tool and is responsible for controlling all operations of the machine tool. Modern CNC systems must have fast data processing capabilities, high feed rates and large program storage. Fast processing of tool trajectories, pre-feedforward control and responsive servo systems are key technologies of CNC control systems.
(4) Process optimization:
The selection of cutting methods and cutting parameters is crucial to the CNC metal processing effect. Optimizing cutting parameters, including cutting speed, feed rate and cutting depth, can improve machining efficiency and tool life. In addition, choosing different cutting strategies and tool geometry parameters for different materials (such as aluminum, steel, titanium alloy, etc.) is also the key to process optimization.
(5) Cooling and chip handling:
A large amount of chips and heat will be generated during high-speed cutting. Efficient cooling system and chip handling device are important links to ensure machining stability and safety. The use of cutting fluid can cool the tool and workpiece, but dry cutting technology combined with blowing or suction to clean chips is more suitable in some occasions.
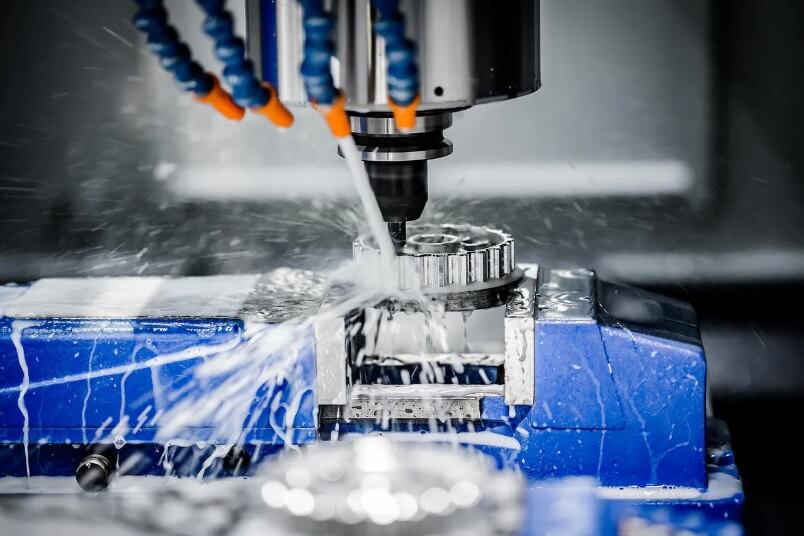
4.How to choose the right cutting tool in CNC metal machining?
In CNC metal machining, choosing the right cutting tool is a key factor in ensuring machining efficiency and quality. Here are some suggestions to help you make the right choice:
(1) Understanding the workpiece material:
First, you must understand the material properties of the workpiece, including hardness, strength, toughness, etc. Different materials require different types of cutting tools. For example, when machining metal materials with higher hardness, such as stainless steel or high-temperature alloys, tool materials with high hardness and good wear resistance, such as cemented carbide or coated cemented carbide, should be selected.
(2) Determine the type of machining:
Select the appropriate tool type according to the type of machining (such as turning, milling, drilling, etc.). Each tool is designed for a specific machining operation. For example, the commonly used tool types in CNC turning include pointed tools, arc tools and forming tools, while face milling cutters, end milling cutters, mold milling cutters, etc. are commonly used in CNC milling machine machining.
(3) Consider tool materials:
Tool materials have a direct impact on machining performance. Commonly used tool materials include high-speed steel, cemented carbide, ceramics, diamond and cubic boron nitride. High-speed steel tools are suitable for general materials, cemented carbide tools are suitable for harder materials, and ceramics and diamond tools are suitable for machining high-hardness materials under extreme conditions.
(4) Select appropriate tool geometry parameters:
The geometry of the tool, such as the tip angle and cutting edge shape, has an important impact on the machining effect. For example, arc-shaped tools are suitable for machining internal and external surfaces and joints, while pointed tools are suitable for machining parts with clear contours.
(5) Determination of cutting parameters:
Cutting parameters include cutting depth, cutting width and cutting speed. Cutting parameters should be reasonably selected according to machine tool performance and workpiece material. During rough machining, a larger cutting depth and width can be selected to improve production efficiency; during fine machining, a smaller cutting depth and width should be selected to ensure machining accuracy.
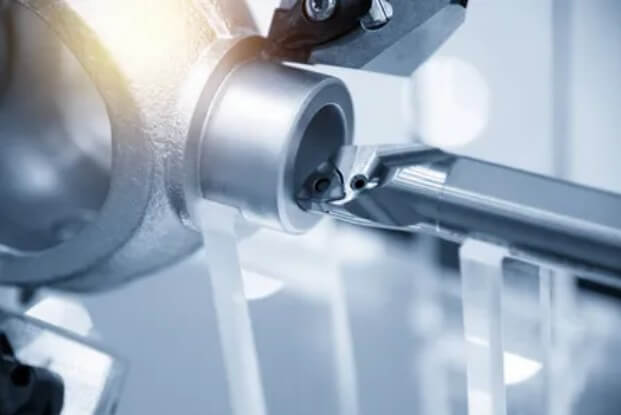
(6) Consider the durability and economy of the tool:
When selecting a tool, its durability and economy should be considered. Although high-performance tools are more expensive, they can reduce the number of tool changes, improve production efficiency, and are more economical in the long run.
5.Practical application areas of CNC metal technology
CNC metal technology occupies an important position in modern manufacturing due to its advantages of high efficiency, precision and high degree of automation. The following are several major practical application areas:
(1) Aerospace manufacturing:
The requirements for the precision and quality of mechanical parts are extremely high, and CNC metal processing can meet these stringent requirements. It is widely used in processing aerospace parts such as aircraft structures and engine parts, improving production efficiency and parts precision.
(2) Automobile manufacturing field:
With the rapid development of the automobile industry, CNC metal plays an important role in processing key parts such as engine parts, transmission parts, and steering system parts. Its high speed, high precision, and high quality ensure the precision and quality of automobile parts.
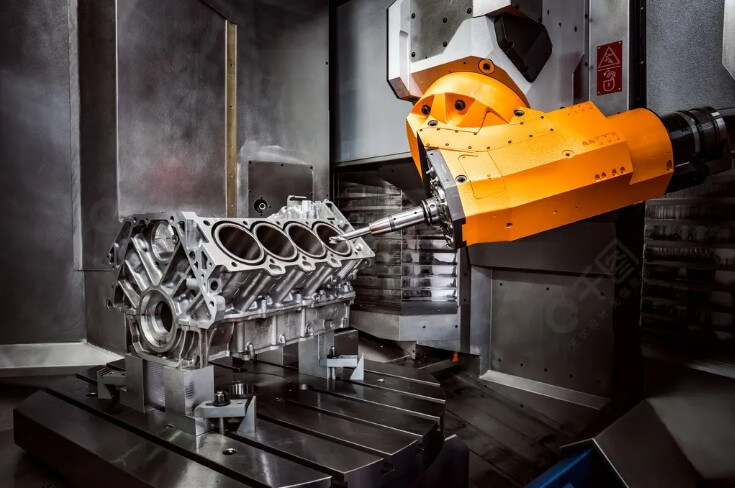
(3) Mold manufacturing industry:
CNC metal processing technology can achieve fast and accurate mold processing, improving the manufacturing efficiency and precision of molds. Molds are the basis of many product manufacturing. The application of CNC technology greatly shortens the manufacturing cycle of molds.
(4) Electronic manufacturing field:
With the continuous upgrading of electronic products, higher requirements are placed on processing precision and production efficiency. CNC metal can be used to process various electronic components, circuit boards and other electronic metal parts, greatly improving the efficiency and quality of electronic manufacturing.
(5) Industrial production field:
In the process of metal smelting and manufacturing, CNC machining technology can be used to intelligently control the actual operation links, provide information feedback on the actual operation of the equipment, and centrally control the link operation and logical construction process, effectively improving the efficiency and quality of industry production and processing.
6.Conclusion
CNC metal processing technology plays an irreplaceable role in modern manufacturing with its high precision, high efficiency and high adaptability. Through CNC machining, high-precision and high-efficiency machining of complex metal parts can be achieved, improving product quality and consistency. At the same time, CNC machining technology can also reduce manual operation and downtime, and improve production efficiency and safety.
1 Comment