Cutting Aluminum: A Comprehensive Analysis of Skills and Methods
Cutting aluminum is a technical activity. It needs to master certain skills and methods to ensure that the cutting effect is precise and meets various application needs. This article will introduce you in detail the techniques of cutting aluminum to help you easily cope with various cutting challenges.
1.The importance of cutting aluminum and the field of application
Due to its light quality, corrosion resistance, and good processing performance, aluminum materials have been widely used in aerospace, automobile manufacturing, building decoration, and household appliances. Cut the aluminum as a key step in aluminum processing directly affects the quality and performance of the product. For example, in the field of aerospace, high -precision aluminum cutting technology is the basis of manufacturing precision parts; in automotive manufacturing, the efficiency of aluminum cutting directly affects the speed and cost of the production line.
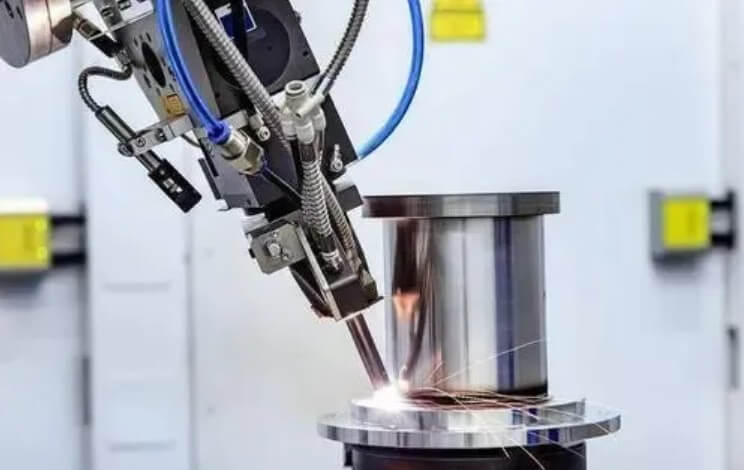
2.Cut the challenge facing aluminum
Although aluminum has many advantages, its cutting process also faces a series of challenges. The high thermal and softness of aluminum make high heat and burrs during the cutting process, affecting the cutting accuracy and surface quality. In addition, the chips produced when cutting aluminum are easy to adhere to the tool, accelerate the wear of the tool, and increase production costs. Therefore, how to choose the appropriate cutting tools and processes, optimize cutting parameters, and improve cutting efficiency and quality is a key problem that needs to be solved when cutting aluminum.
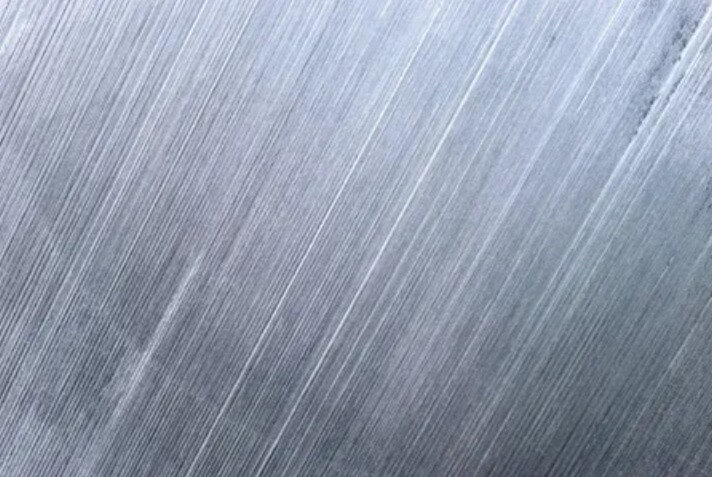
3.The main cutting technology of cutting aluminum
(1) Disc cutting machine
The disc cutting machine is one of the most commonly used equipment in aluminum cutting, which has the advantages of simple operation and low cost. However, the disc cutting machine is easy to produce burrs and calories when cutting aluminum, and it needs to be frequently replaced with a cutting task that is suitable for small -scale or high -precision requirements. In order to improve the quality and efficiency of the cutting, pay attention to the use of the appropriate saw blade type and specifications when using a disc cutting machine, and ensure the sharpness and stability of the saw blade.
(2) Cutting with a saw bed
The cutting technology of a sawtage is suitable for aluminum materials with large size or thickness, which has the advantages of high cutting accuracy and low material loss. Tibetan cutting machines can be cut through continuous movement zone, which can effectively reduce vibration and friction in the cutting process, thereby improving the cutting quality and efficiency. When cutting aluminum materials with a tape, you need to pay attention to adjusting the tension and speed of the saw band to ensure the stability of the cutting process and the life of the sawbone.
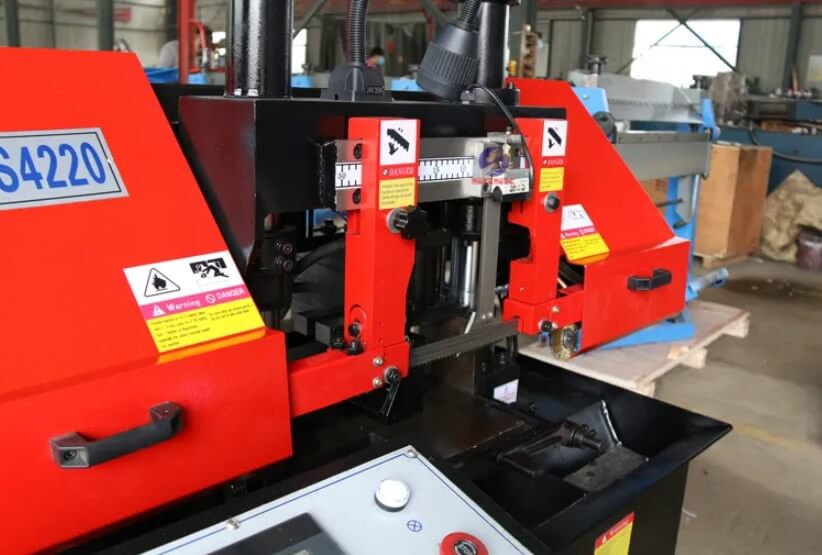
(3) Cold -cutting machine cutting
Cold -cutting machines are cut into aluminum cutting through powerful shear, and are suitable for straight cutting and mass production. There are less calories generated during the cutting process of the cold shear, which can effectively avoid the thermal deformation of aluminum materials and improve the cutting accuracy. However, the equipment cost of cold shear machines is high and the operating technical requirements are high. It is suitable for large -scale and high -precision aluminum cutting tasks.
(4) CNC saw cutting system
The CNC sawting system combines advanced computer control technology to achieve high -precision and high efficiency cutting aluminum. CNC sawing systems can control the cutting path and parameters through programming to meet the cutting requirements of various complex shapes. In addition, the CNC sawing cutting system also has the characteristics of automation and intelligence, which can effectively reduce the errors caused by manual operation and improve production efficiency and product quality.
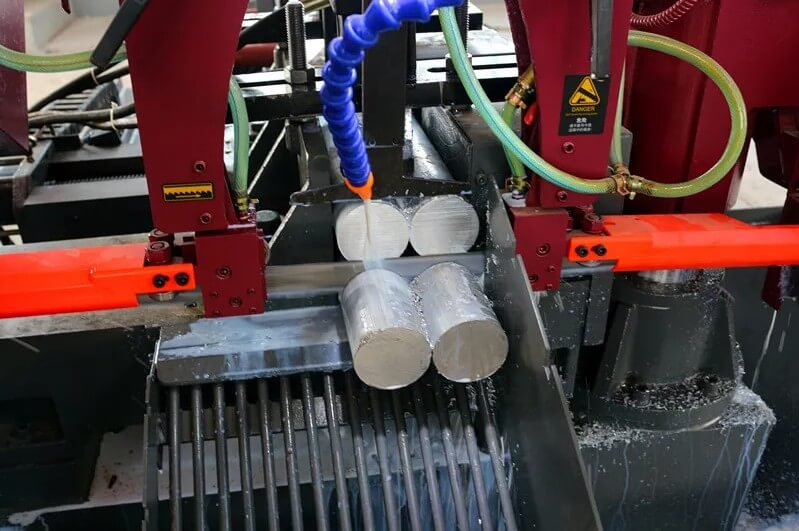
(5) Comparison of laser cutting, plasma cutting and water shooting cutting
These three high -tech cutting technologies are outstanding in aluminum processing. Laser cutting has extremely high accuracy and speed, suitable for cutting of complex graphics and aluminum plates; plasma cutting efficiency is high, suitable for fast cutting of thicker aluminum; The area is suitable for the occasion of extremely high requirements for cutting quality. Although these high -tech cutting technologies are high, they can significantly improve the quality and efficiency of cutting, and are suitable for aluminum cutting tasks with high precision and high requirements.
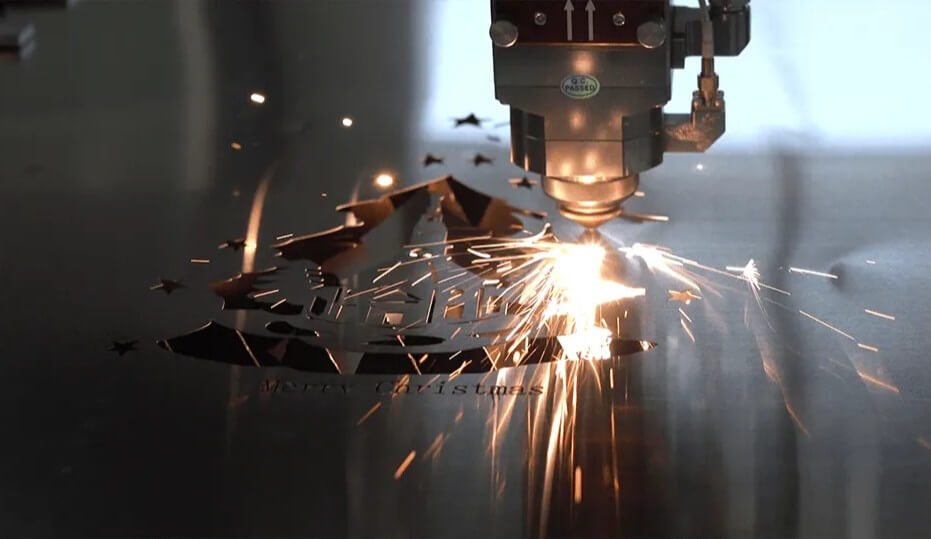
4.Optimization of the skills and parameters of cutting aluminum
(1) Selection and optimization of cutting parameters
The selection of cutting parameters has a significant impact on cutting quality and efficiency. Parameters such as cutting speed, feed rate, and tension need to be optimized according to the type and thickness of aluminum materials. For example, too fast cutting speed may lead to rough cutting surface, and too slow cutting speed may lead to increased juoper wear; too fast feed rate may lead to the break of the saw blade. It may cause a saw blade to break, and too small tension may cause rough cutting surface. Therefore, reasonable selection and optimization of cutting parameters are the key to improving aluminum cutting quality.
(2) Selection and maintenance of cutting tools
Choosing a suitable cutting tool is essential for improving cutting efficiency and quality. For example, when cutting aluminum materials, you should choose knife materials with high hardness and abrasion resistance, such as hard alloy or diamond -coated tool. In addition, regularly grinding and inspecting the tools, maintaining the sharpness of the tool can effectively reduce the friction and heat generation during the cutting process, and improve the use of cutting quality and the service life of the tool.
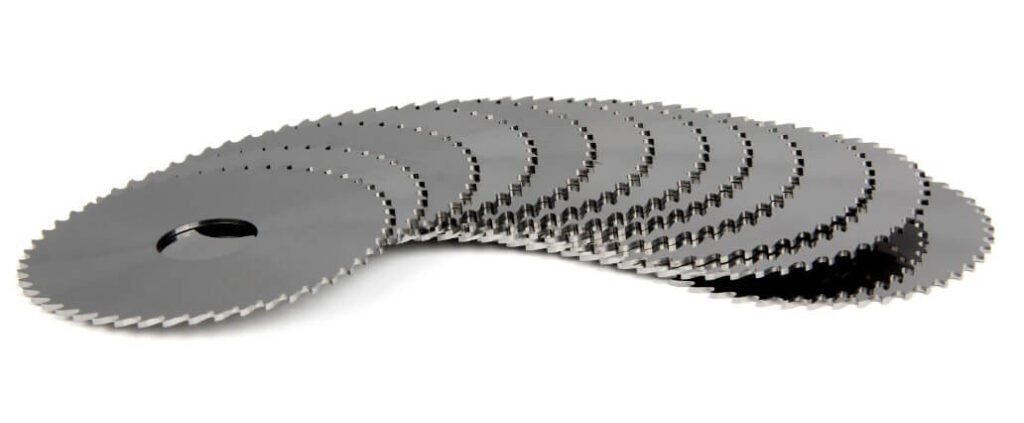
(3) Use of cutting solution
The cutting solution plays a role in cooling and lubricating during the cut aluminum process, which can effectively reduce cutting heat and tool wear. For example, when using a disc cutting machine or cutting the aluminum with a sawnop, proper use of the cutting solution can reduce the wear of the saw blade or the sawbone and improve the cutting quality and efficiency. In addition, the cutting solution can also help eliminate dandruff, reduce chip cutting to adhesion to tools and workpieces, and improve the stability of the cutting process.
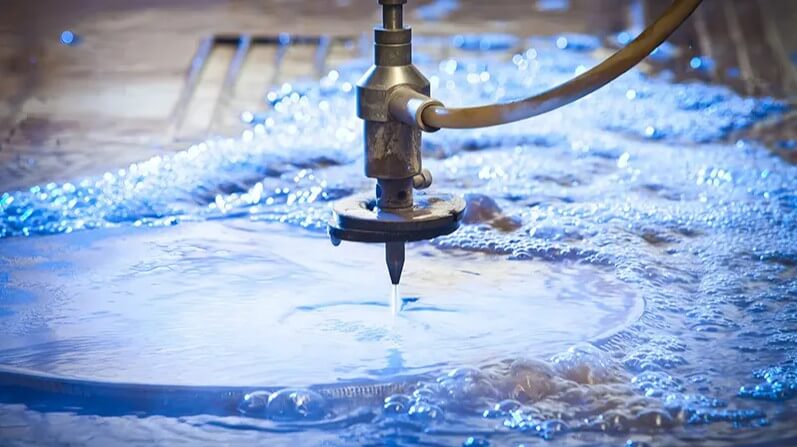
5.Common problems and solutions when cutting aluminum.
There may be various problems when cutting aluminum. The following are some common problems and their solutions:
(1) The size of the saw is not accurate and unstable
1) Reason:
The feeding or cutting of the countertop is not smooth, and the quality of the saw blade is not good, resulting in a leisure when the saw.
2) Solution:
Check whether the feed pressure is solid to ensure that the material delivery material is not mop; check the vertical and peaceful plane of the countertop of the equipment to adjust to the accurate range; use high -quality saw blades, such as imported quality -cut aluminum saw blades.
(2) Saw marks and burrs the cut surface
1) Reason:
The cutting saw blade is not sharp or the product quality is poor, the lubricating oil is not in place or the special aluminum alloy lubricating oil is not used.
2) Solution:
Replace the new or more sharp saw blade; check the lubrication device to ensure that the special aluminum alloy lubricating oil is used and sprayed correctly.
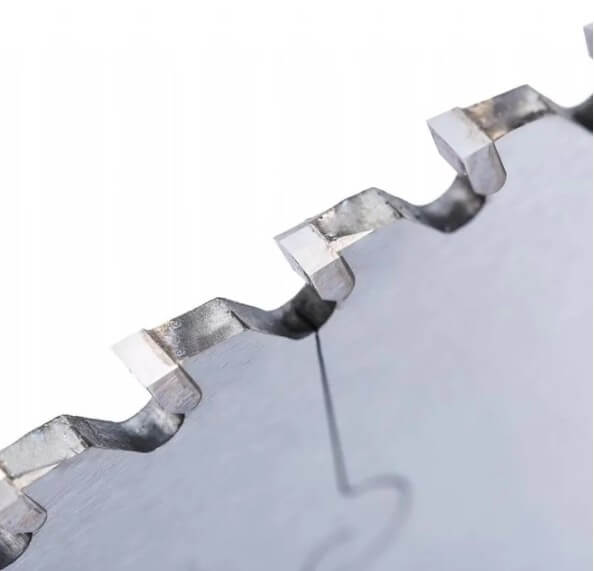
(3) The motor is hot or even strike
1) Reason:
The motor power is insufficient or the quality is not good, and long -term high load operation cannot be affected.
2) Solution:
Select equipment equipped with a suitable power motor, such as 7.5kW or higher power motor when cutting solid materials.
(4) Large equipment vibration
1) Reason:
The rotating wheel balance is not good, the support of the support wheel parts is too large, and the motor is not fixed.
2) Solution:
Check and replace the rotor wheels with poor balance to ensure that the support wheel parts are closely coordinated and the motor is fixed.
(5) Noise
1) Reason:
The base and supporting parts are insufficient, the gap between the parts is too large, the inferior bearing, and the belt speed is too fast.
2) Solution:
Use high -quality raw materials to ensure close cooperation when assembling, and adjust the belt speed.
(6) Specifies are unstable
1) Reason:
The gas source and the air pressure are not up to standard, the cylinder damage, and the knife shell -oriented pillar bearing has foreign objects.
2) Solution:
Check the air pressure to ensure that the damaged cylinder is replaced within the standard range;
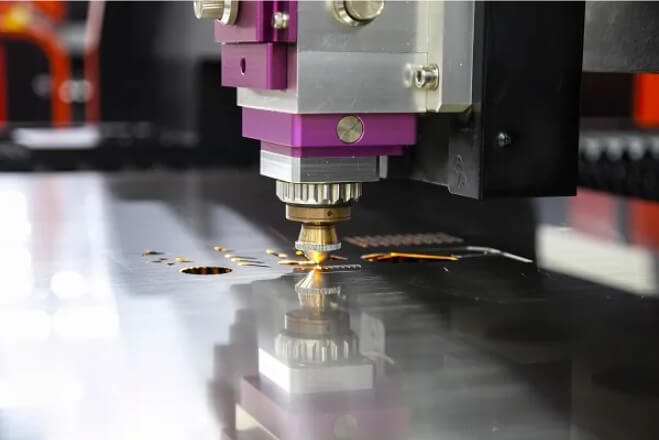
(7) Lubricating device does not spray fuel
1) Reason:
The lubricating device is blocked by the oil inlet or the nozzle, and the circuit part is faulty.
2) Solution:
Clean up the oil inlet and nozzle, check and repair the circuit part.
(8) An abnormal noise appears in the aluminum cutting machine
1) Reason:
The saw blade was external, and the spindle gap was too large, and there may be wear or loosening in each part of the equipment.
2) Solution:
Check the saw blade and the spindle, replace or repair the wear and loosening parts.
summary:
By identifying these common problems and reasons, and taking corresponding solutions, it can effectively improve the efficiency and quality of cutting aluminum, reduce equipment failure and maintenance costs.
6.Summary
All in all, when cutting aluminum, we must pay attention to optimizing the cutting process, choose the appropriate cutting equipment and tools, and improve the cutting quality and efficiency. In addition, strengthening the safety training of operators and the maintenance management of equipment is also an important measure to improve the quality of aluminum cutting.