Diamond grinding wheel: a sharp tool in precision machining
Diamond grinding wheel, with its excellent hardness and wear resistance, has become an indispensable cutting and grinding tool in modern industry. As an efficient grinding tool, it is widely used in the processing of various hard and brittle materials, such as cemented carbide, glass, ceramics, semiconductor materials, etc. With its unique advantages, it has become a sharp tool in the field of precision machining.
This article will conduct a detailed and comprehensive analysis of the concept, classification, characteristics, application, wear and damage analysis, and dressing technology of diamond grinding wheel, to help everyone have a comprehensive understanding of the selection, use and dressing of diamond grinding wheel, and solve practical application problems.
1.Overview of diamond grinding wheel
Diamond grinding wheel is a high-performance grinding tool with diamond as abrasive. Diamond, known as the “king of hardness”, has a much higher hardness than other natural materials, which makes it show unparalleled advantages in processing various hard and brittle materials. The manufacturing process of diamond grinding wheel is complex and precise, involving the diamond abrasive grains firmly fixed to the substrate through a binder. The type and performance of the bond have a decisive influence on the final performance of the grinding wheel.
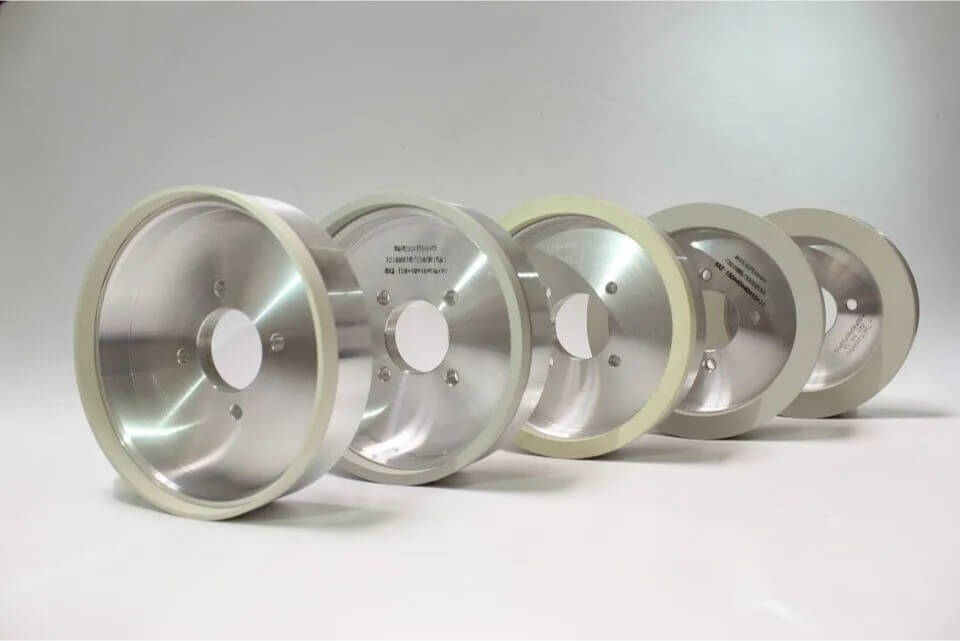
2.Classification of diamond grinding wheels
Diamond grinding wheels can be divided into three categories according to the type of bond: metal bond, resin bond and vitrified bond. Each type of grinding wheel has its specific application scenarios and advantages.
(1) Metal bond grinding wheel:
This type of grinding wheel uses metal as a bond, usually bronze powder and other metal materials. Diamond abrasive grains are combined with metal powder through a high-temperature sintering process to form a strong and durable grinding wheel.
Metal bond grinding wheels have high bonding strength and good wear resistance, can withstand large grinding loads, and are suitable for heavy-duty grinding and high-precision grinding. However, the dressing of metal bond grinding wheels is relatively difficult and requires special dressing equipment and technology.
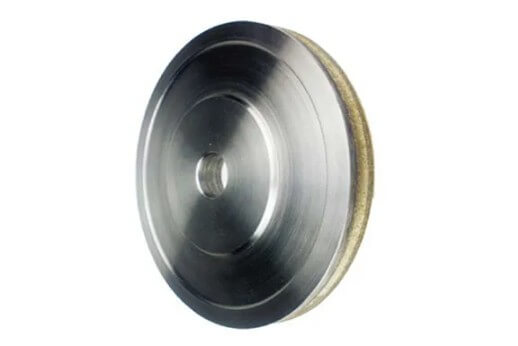
(2) Resin bond grinding wheels:
Resin bond grinding wheels use resin materials as a bond, usually phenolic resin or polyimide resin. Resin bond grinding wheels have the advantages of good self-sharpening, good elasticity, and easy dressing, and are suitable for precision grinding and semi-fine grinding. The manufacturing process of resin bond grinding wheels is relatively simple and the cost is low, but its heat resistance and wear resistance are relatively poor, and it is not suitable for high-load grinding. Resin bond grinding wheels are widely used in the grinding of materials such as glass and ceramics.
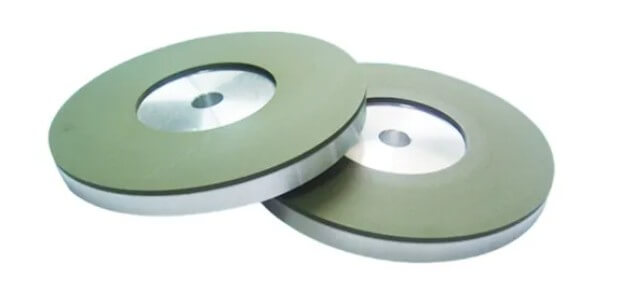
(3) Vitrified bond diamond grinding wheels:
Vitrified bond grinding wheels use ceramic materials as binders and have good chemical stability and thermal stability. Vitrified bond grinding wheels have strong grinding force, low grinding temperature, small grinding wheel wear, and can maintain good shape stability. They are suitable for high-precision grinding and forming grinding. Vitrified bond grinding wheels have a high porosity, which is conducive to chip removal and heat dissipation, reducing workpiece burns and blockages.
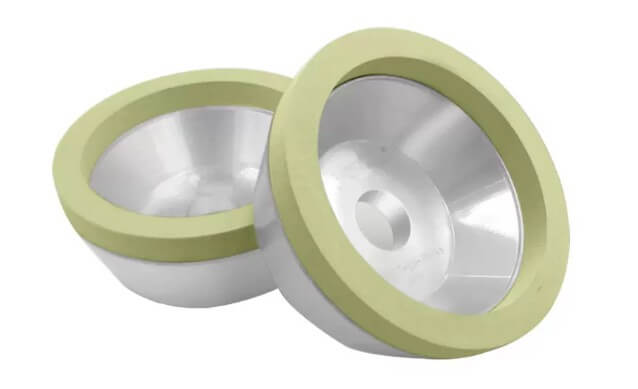
In addition to classification by binder, diamond grinding wheels can also be classified according to production process, shape and grinding method. For example, according to the production process, they can be divided into sintering, electroplating and brazing types; according to the shape, they can be divided into cup, bowl and dish shapes. Different classification methods enable diamond grinding wheels to meet various processing needs.
3.Characteristics of diamond grinding wheels
(1) High hardness and strong grinding force:
Diamond grinding wheels use diamond as abrasive and have extremely high hardness. They can effectively grind hard alloy, ceramics, glass and other difficult-to-process materials.
(2) Good wear resistance and long service life:
Due to the high wear resistance of diamond, the grinding wheel wears less and has a longer service life, which reduces the frequency and cost of replacement.
(3) High grinding accuracy and good surface quality:
Diamond grinding wheels can maintain a stable abrasive shape and size during the grinding process, which is suitable for high-precision processing. The surface roughness of the workpiece after grinding is low and the accuracy is high.
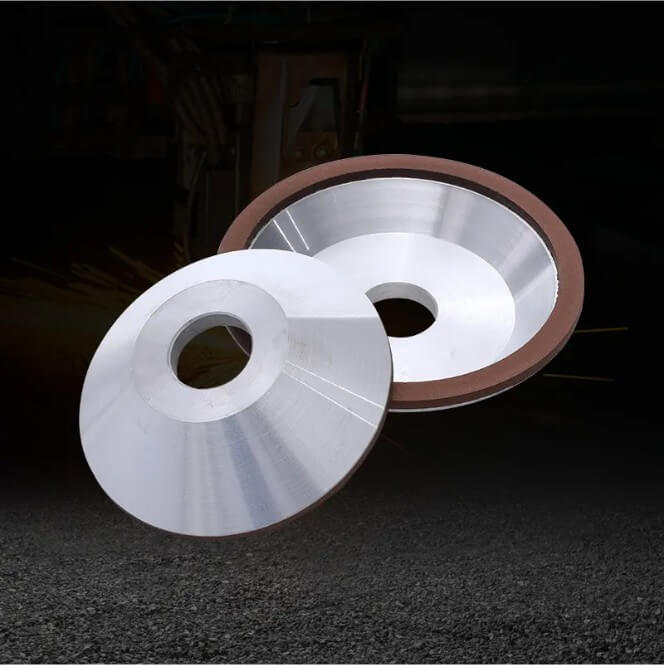
(4) High grinding efficiency:
The sharp abrasive grains and good self-sharpening properties of diamond grinding wheels make them extremely efficient during the grinding process.
(5) Good thermal conductivity to avoid damage to the workpiece:
Diamond has good thermal conductivity, which helps to dissipate heat during the grinding process and reduce phenomena such as burns and cracks on the workpiece.
(6) Less dressing requirements, improved production efficiency:
After being sharpened, diamond grinding wheels can maintain micro-edge properties for a long time, reducing the number of dressing times and improving production efficiency.
(7) Strong adaptability and wide application:
It can be used for grinding a variety of materials, including hard and brittle materials and metal materials, and is widely used in machinery, electronics, construction, optical glass processing and other fields.
4.Application fields of diamond grinding wheels
(1) Precision grinding
Diamond grinding wheels play a vital role in the field of precision grinding. Their extremely high hardness and wear resistance enable diamond grinding wheels to maintain sharp cutting edges during precision machining, thereby ensuring the surface finish and dimensional accuracy of the workpiece. Especially in optical instruments, semiconductor industry, precision machinery manufacturing and precision instruments, diamond grinding wheels are widely used to process high-hardness materials such as glass, silicon wafers, etc.
1) Optical instruments
In the manufacturing process of optical instruments, diamond grinding wheels can achieve efficient grinding of high-precision optical components such as lenses and prisms, ensuring their surface finish and shape accuracy.
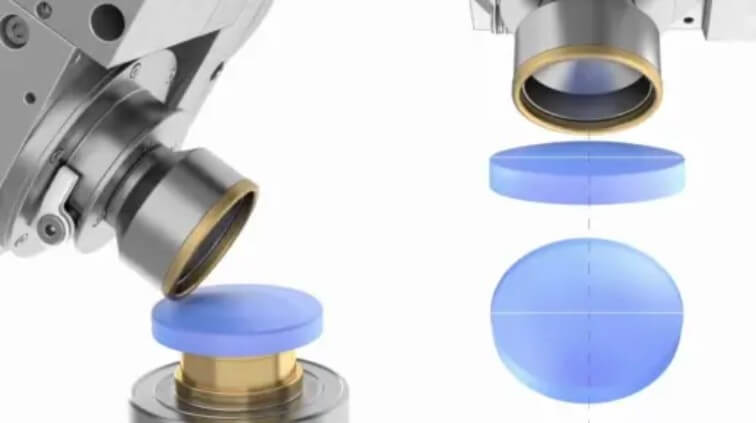
2) Semiconductor industry
In the semiconductor industry, diamond grinding wheels are used for grinding materials such as silicon wafers and sapphire substrates. They can provide high-precision, low-roughness surface quality to meet the high requirements of semiconductor manufacturing.
3) Precision machinery manufacturing
In precision machinery manufacturing, diamond grinding wheels are used to process high-precision bearings, gears and other parts to ensure their dimensional accuracy and surface quality.
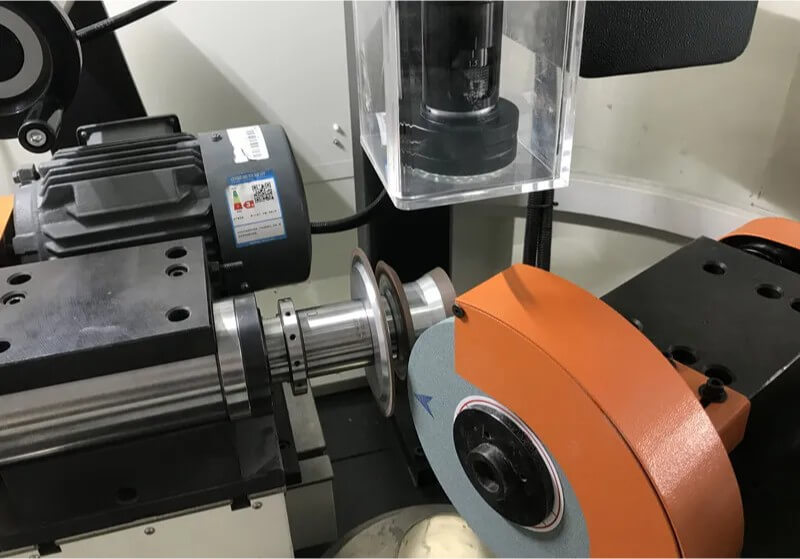
4) Precision instruments
In addition, diamond grinding wheels are also widely used in the manufacture of precision instruments, such as high-precision measuring tools and medical equipment, which have extremely high requirements for the dimensional accuracy and surface quality of parts.
(2) Superhard material processing
Diamond grinding wheels are ideal for processing superhard materials such as cemented carbide, ceramics and gemstones. These materials are difficult to process with traditional grinding tools due to their high hardness and wear resistance, while diamond grinding wheels can effectively meet these challenges and provide efficient and stable grinding results.
1) Cemented carbide processing
Cemented carbide is a composite material composed of hard carbide and metal binder. It has high hardness, high strength and good wear resistance. It is widely used in the manufacture of cutting tools, molds and wear-resistant parts. However, the high hardness of cemented carbide also brings great challenges to grinding. Diamond grinding wheel can effectively grind cemented carbide due to its extremely high hardness, improving grinding efficiency and surface quality.
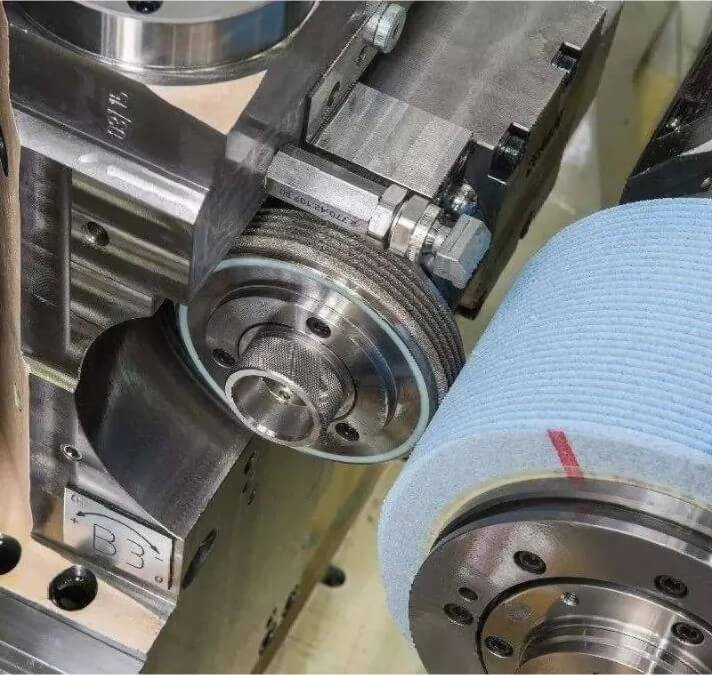
2) Ceramic material processing
Ceramic materials have the characteristics of high hardness and high brittleness. They are widely used in electronics, medical and aerospace fields, and have extremely high performance requirements for materials. However, traditional grinding tools are difficult to achieve efficient and high-precision processing. Diamond grinding wheel can provide stable grinding effect and ensure the dimensional accuracy and surface quality of ceramic workpieces.
3) Other precious material processing
In addition, diamond grinding wheel is also widely used in the processing of precious materials such as gemstones and jade, which can achieve high-precision cutting and grinding to maintain the beauty and value of materials.
5.Dressing technology of diamond grinding wheels
(1) Importance of dressing
Diamond grinding wheels will gradually wear out during use, affecting their grinding performance. Dressing is a key process to restore the sharpness and shape accuracy of the grinding wheel. Regular dressing of diamond grinding wheels can not only extend their service life, but also ensure the stability of the grinding process and the quality of the processed workpiece. The quality of dressing technology directly affects the performance and grinding effect of the grinding wheel.
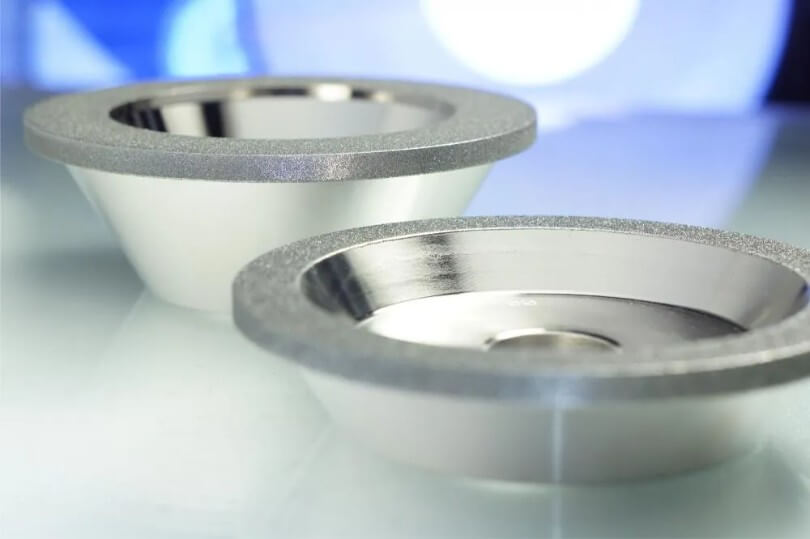
During the dressing process, it is necessary to select appropriate dressing methods and parameters according to the wear of the grinding wheel and the processing requirements. Reasonable dressing can restore the cutting performance of the grinding wheel, improve grinding efficiency, and reduce the roughness of the workpiece surface. In addition, dressing can prevent grinding wheel clogging, reduce grinding heat, avoid workpiece burns, and thus improve grinding quality.
(2) Dressing methods
Diamond grinding wheel dressing methods are mainly divided into two categories: shaping and sharpening. Shaping is mainly to restore the geometric shape accuracy of the grinding wheel, while sharpening is to restore the sharpness of the cutting edge of the grinding wheel.
1) Treating method:
Treating usually adopts mechanical shaping method, such as mechanical grinding of the grinding wheel with a diamond pen or diamond dresser. Diamond pen is a tool with diamond abrasive grains, which removes the wear layer on the surface of the grinding wheel by mechanical grinding to restore its geometric shape accuracy. During the shaping process, it is necessary to control the dressing force and dressing speed to avoid damage to the grinding wheel. In addition, laser shaping method can also be used to locally heat and remove materials on the surface of the grinding wheel by laser beam to achieve high-precision shaping.
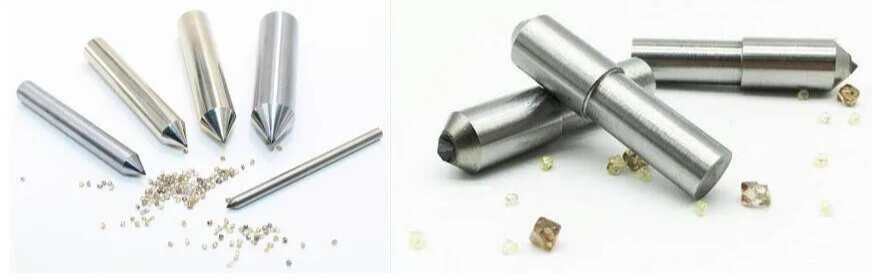
2) Sharpening method:
Sharpening methods include mechanical sharpening, laser sharpening and electric spark sharpening. Mechanical sharpening is to remove blockages and passivation layers on the surface of the grinding wheel by mechanical grinding to restore the sharpness of the cutting edge. Laser sharpening is to locally heat and remove materials on the surface of the grinding wheel by laser beam to achieve sharpening of the cutting edge. Electric spark sharpening is to locally erode the surface of the grinding wheel by electric spark discharge to restore the sharpness of the cutting edge.
6.Laser dressing technology for diamond grinding wheels
(1) Principle of laser dressing
Laser dressing technology is to use a high-energy-density laser beam to locally heat and remove material from the surface of a diamond grinding wheel. By precisely controlling the power, pulse width, and scanning speed of the laser, the surface of the grinding wheel can be accurately dressed. During the laser dressing process, the laser beam is irradiated onto the surface of the grinding wheel, causing the local material to heat and vaporize rapidly, thereby removing the worn or clogged parts and restoring the sharpness and shape accuracy of the grinding wheel.
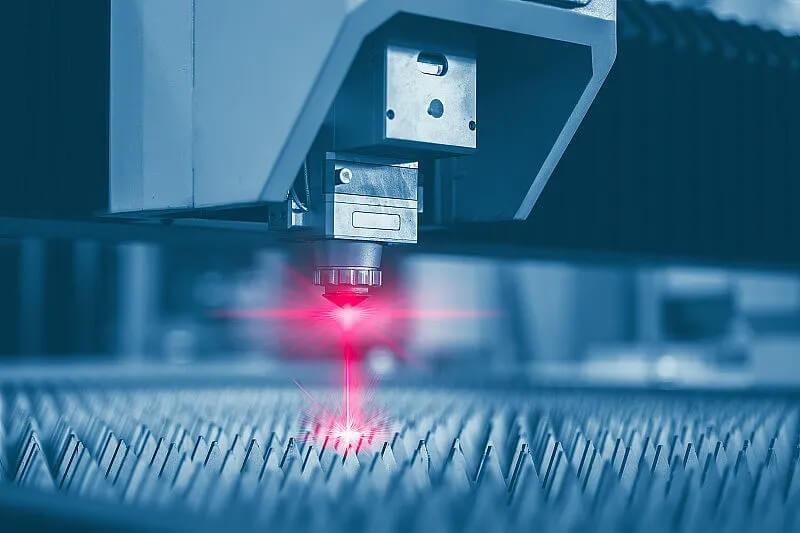
(2) Selection of laser
When selecting a laser, the wavelength and power density of the laser are mainly considered. YAG laser and CO2 laser are two commonly used types. YAG laser has a shorter wavelength and is more easily absorbed by metal binders, making it suitable for dressing metal-bonded diamond grinding wheels. Although CO2 lasers have a longer wavelength, they are more effective when processing non-metallic materials. The choice of laser directly affects the dressing efficiency and surface quality, so it is necessary to select according to the specific application scenario of the grinding wheel.
(3) Optimization of dressing process parameters
Optimizing the process parameters of laser dressing is the key to improving the quality and efficiency of dressing. It mainly includes selecting appropriate laser power, pulse width, scanning speed and spot diameter. Laser power affects the number of ablations per unit time, thereby affecting the dressing speed; pulse width controls the depth of each ablation and affects the surface roughness.
For example, for metal-bonded diamond grinding wheels, higher laser power and pulse width can be selected to achieve rapid material removal. For resin-bonded diamond grinding wheels, lower laser power and pulse width can be selected to avoid damage to the resin material.
7.Wear and damage analysis of diamond grinding wheels
(1) Wear mechanism
Diamond grinding wheels are subject to normal wear during the grinding process, which is due to the friction and cutting action between the abrasive grains and the workpiece material. As the grinding proceeds, the abrasive grains will gradually become blunt and the cutting ability will decrease. In addition, the grinding wheel may also suffer abnormal wear, such as abrasive grain shedding or breakage, which is usually caused by improper grinding wheel selection, untimely dressing or unreasonable grinding parameter settings.
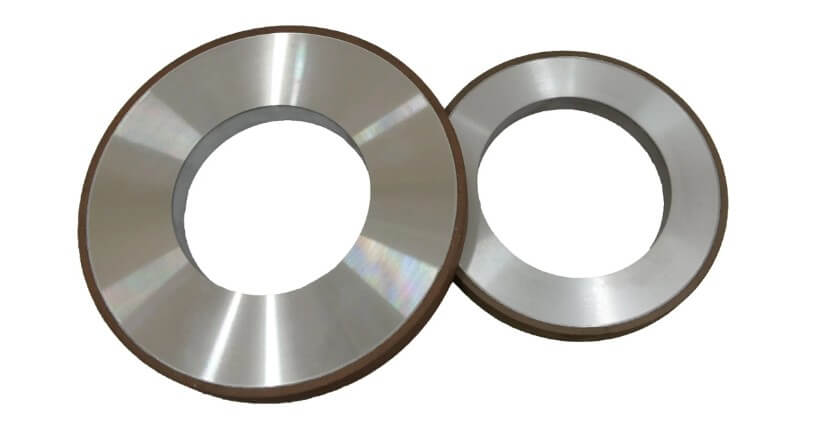
(2) Damage forms
The damage forms of diamond grinding wheels mainly include abrasive grain shedding, grinding wheel breakage and shape distortion. Abrasive grain shedding is caused by insufficient holding force of the bond on the abrasive grains, resulting in abrasive grain shedding during the grinding process. Grinding wheel breakage is caused by excessive grinding force or defects in the grinding wheel itself, resulting in the grinding wheel breaking during the grinding process. Shape distortion is caused by uneven wear of the grinding wheel during the grinding process, resulting in changes in the geometric shape of the grinding wheel.
In order to prevent these damages, it is necessary to reasonably select the type and specification of the grinding wheel, perform dressing in time, and correctly set the grinding parameters. For example, when grinding cemented carbide, a metal bond grinding wheel with high bonding strength should be selected, and the grinding parameters should be reasonably set to avoid excessive grinding force. When grinding ceramic materials, a ceramic bond grinding wheel with good wear resistance should be selected, and dressing should be performed in time to avoid uneven wear of the grinding wheel.
8.Summary
In summary, selecting a suitable diamond grinding wheel and dressing it regularly can not only extend the service life of the grinding wheel, but also significantly improve processing efficiency and product quality. In the fiercely competitive market environment, mastering this key technology will bring significant economic benefits and market competitiveness to enterprises.