Metal grinding wheel: Innovator of grinding process
Metal grinding wheel, as an indispensable grinding tool in modern industry, has redefined the standard of grinding process with its excellent performance and innovative design. This article will explore the definition, classification, structure, application, grinding performance and related issues of wear and maintenance of metal grinding wheel in depth, hoping to be helpful to you.
1.Definition and classification of metal grinding wheel
Metal grinding wheel is a bonded abrasive tool that uses metal binder to consolidate abrasive particles together. It grinds metal or non-metal workpieces through high-speed rotation and can complete various processing tasks such as rough grinding, semi-finishing grinding, fine grinding and cutting. The following is the classification of metal grinding wheels according to different methods:
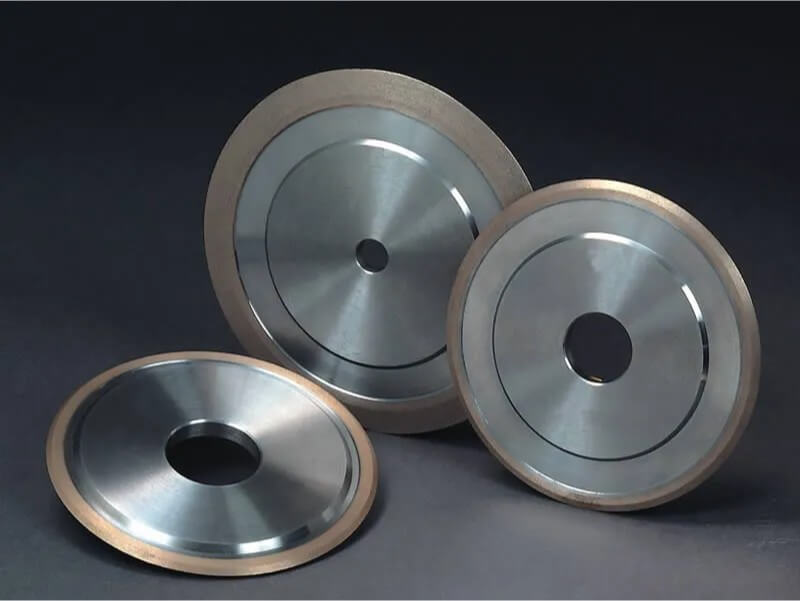
(1) Classification by binder
1) Resin bond grinding wheel: has good elasticity and polishing performance, suitable for high-speed grinding.
2) Vitrified bond grinding wheel: has stable chemical properties and good heat resistance, suitable for high-precision grinding.
3) Rubber bond grinding wheel: has large elasticity and good polishing performance, suitable for fine grinding and polishing processes.
4) Metal bond grinding wheel: Made by metal powder metallurgy or electroplating process, it has high strength and high wear resistance and is suitable for processing hard and brittle materials.
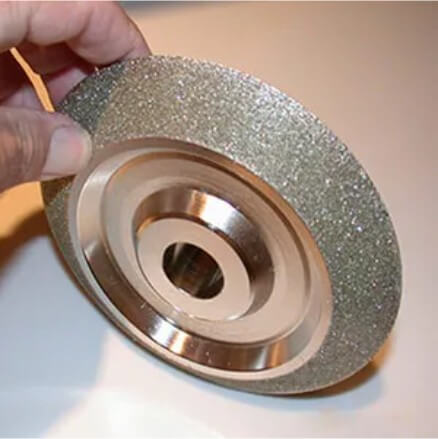
(2) Classification by abrasive
1) Ordinary abrasive grinding wheel: Uses ordinary abrasives such as corundum (Al2O3) and silicon carbide, suitable for grinding general metal materials.
2) Super abrasive grinding wheel: Uses super hard abrasives such as diamond and cubic boron nitride, suitable for grinding high hardness materials such as cemented carbide.
(3) Classification by shape
1) Parallel grinding wheel: Suitable for surface grinding.
2) Cylindrical grinding wheel: Suitable for external cylindrical grinding.
3) Cup grinding wheel: Suitable for internal cylindrical grinding and groove grinding.
4) Disc grinding wheel: Suitable for cutting and grooving.
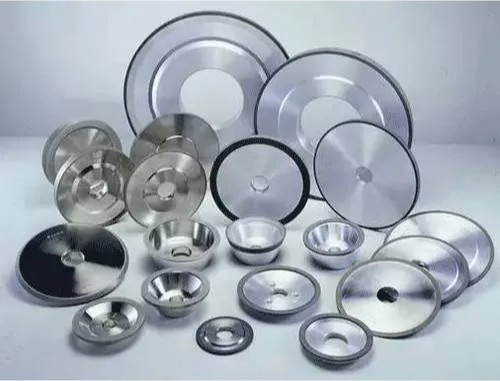
2.Application fields of metal grinding wheels
Due to their excellent grinding performance, metal grinding wheels are widely used in many industries.
(1) Mechanical processing:
In the process of mechanical manufacturing, metal grinding wheels are widely used in the grinding of various metal materials, such as carbon steel, alloy steel, stainless steel, etc. It can not only remove materials efficiently, but also ensure the accuracy and surface quality of the workpiece. Especially when processing high-hardness and high-strength metal materials, it performs well and meets the processing requirements of complex parts.
(2) Automobile industry:
In the automobile industry, metal grinding wheels are mainly used for grinding key components such as engine cylinder blocks, cylinder heads, crankshafts, camshafts, etc. Its high hardness and wear resistance ensure the high accuracy and low surface roughness of parts, improving the overall performance and service life of the car.
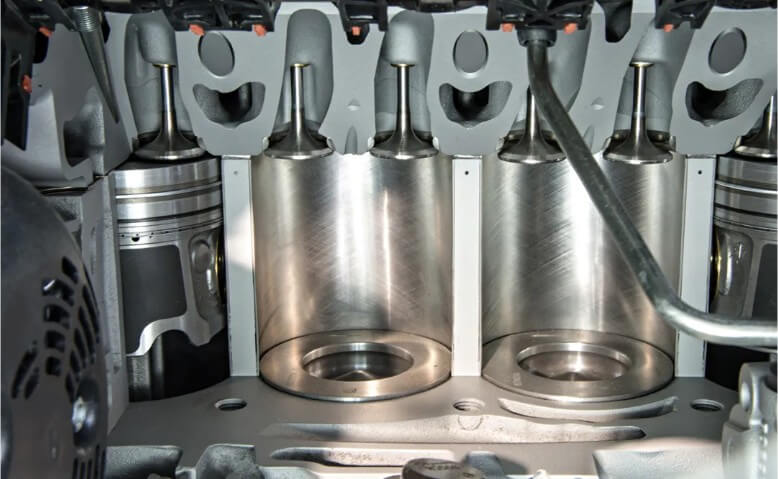
(3) Aerospace:
The materials of aerospace parts are usually high-strength and high-hardness, such as titanium alloys and high-temperature alloys. Metal grinding wheels can effectively cope with these difficult-to-process materials, ensure the processing accuracy and surface integrity of parts, and meet the high requirements of safety and reliability in the aerospace field.
(4) Tool manufacturing:
In tool manufacturing, metal grinding wheels are mainly used for grinding various cutting tools, such as drills, milling cutters, reamers, etc. Its high hardness and sharp abrasive grains can ensure the sharp cutting edge of the tool, improve the service life and cutting performance of the tool.
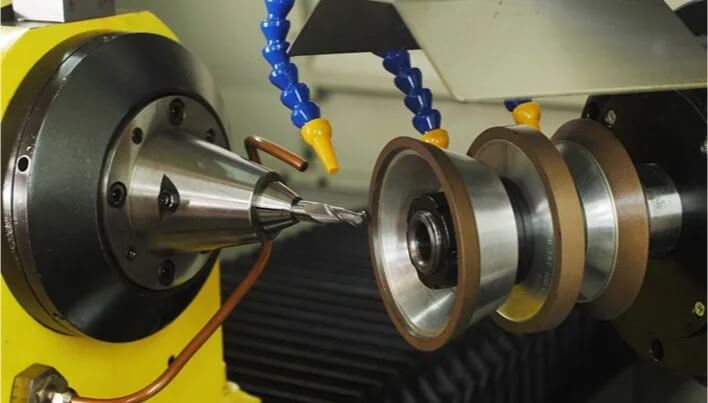
3.Structure and manufacturing of metal grinding wheels
(1) Structural composition
The structure of the grinding wheel is mainly composed of three parts: abrasive grains, binders and pores.
1) Abrasive grains:
This is the core part of the grinding wheel and is used for direct cutting. Abrasive grains are usually made of high-hardness materials such as aluminum oxide, silicon carbide or diamond to ensure that they have sufficient sharpness and wear resistance.
2) Binder:
The binder is used to firmly bond the abrasive grains together to form a grinding wheel with a certain shape and strength. Common binders include ceramic binders, resin binders and metal binders. Different binders give the grinding wheel different performance characteristics.
3) Pores:
The pores in the grinding wheel not only help to accommodate chips and grinding fluid, but also promote heat dissipation to prevent the grinding wheel from overheating during operation.
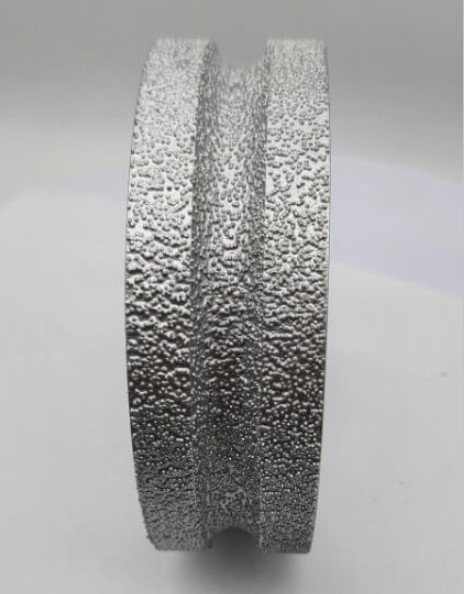
(2) Manufacturing process
1) Mixing:
Mix the abrasive, binder and other additives in a certain proportion to ensure the uniformity and performance stability of the grinding wheel.
2) Pressurization:
Put the mixed materials into a mold and form them under high pressure to give them a certain shape and density.
3) Sintering:
The formed grinding wheel blank is sintered at high temperature to solidify the binder and firmly bond the abrasive together.
4) Hardness test:
The hardness of the sintered grinding wheel is tested to ensure that its hardness meets the use requirements.
5) Safe rotation test:
Perform a safe rotation test to test the strength and safety of the grinding wheel to ensure that it will not break when rotating at high speed.
6) Dressing:
According to the use requirements, the grinding wheel is dressed to give it the required shape and size.
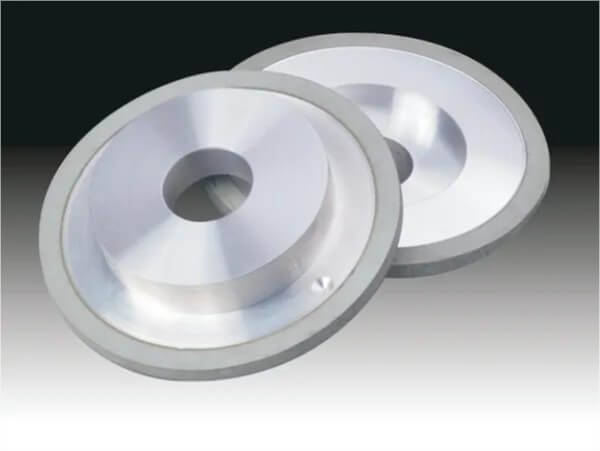
4.Analysis of the grinding performance of metal grinding wheels
(1) Grinding principle
The grinding principle of metal grinding wheels is to use the abrasive on the surface of the high-speed rotating grinding wheel to cut the workpiece. The distribution of abrasive grains on the surface of the grinding wheel is random, and each abrasive grain can be regarded as a tiny cutting edge. During the grinding process, the abrasive grains perform tiny cuts on the surface of the workpiece, thereby achieving material removal. Due to the hardness and sharpness of the abrasive grains, metal grinding wheels can effectively grind high-hardness materials.
During the grinding process, the rotation speed and grinding pressure of the grinding wheel have an important influence on the grinding effect. For example, the higher the rotation speed of the grinding wheel, the higher the grinding efficiency, but at the same time, more heat will be generated, which may cause burns on the workpiece surface; the greater the grinding pressure, the higher the grinding efficiency, but at the same time, it will also accelerate the wear of the grinding wheel.
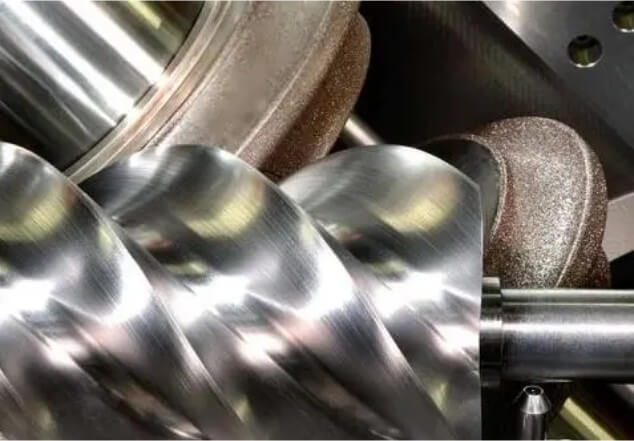
Therefore, in the actual grinding process, it is necessary to reasonably select the rotation speed and grinding pressure of the grinding wheel according to the material and processing requirements of the workpiece.
(2) Performance characteristics
The grinding performance of metal grinding wheels is mainly reflected in three aspects: grinding efficiency, grinding accuracy and durability. First, the grinding efficiency of metal grinding wheels is high, and a large amount of material can be removed in a short time. Second, the grinding accuracy of metal grinding wheels is high, and good workpiece surface quality and dimensional accuracy can be obtained. In addition, it has good durability and can maintain grinding performance for a long time, reducing the frequency of dressing and replacement.
The grinding performance of metal grinding wheels is also affected by factors such as abrasive type, binder type, and pore structure. CBN grinding wheels have good heat resistance and chemical stability and are suitable for grinding difficult-to-process materials such as high-temperature alloys and titanium alloys. Resin bond grinding wheels have a faster grinding speed but poorer durability; metal bond grinding wheels have better durability but slower grinding speed. Therefore, when selecting metal grinding wheels, it is necessary to comprehensively consider these factors based on specific processing requirements.
5.Application of metal grinding wheels in processing of different materials
(1) Application in processing of metal materials
1) Steel materials:
Metal grinding wheels are mainly used to remove oxide scale, rust and burrs on the surface of steel materials. Their high hardness and wear resistance enable materials to be removed quickly and effectively during processing while maintaining the flatness and precision of the processed surface.
2) Aluminum alloy materials:
For soft and easily deformed metals such as aluminum alloys, metal grinding wheels can achieve fast cutting and grinding through their sharp abrasive grains, reduce heat generation during processing, and avoid burns or deformation on the aluminum alloy surface.
3) Stainless steel materials:
Stainless steel has high hardness and is prone to work hardening, so it has high requirements for grinding tools. By selecting suitable abrasives and binders, metal grinding wheels can effectively deal with the work hardening problem of stainless steel, improve grinding efficiency and extend the service life of grinding wheels.
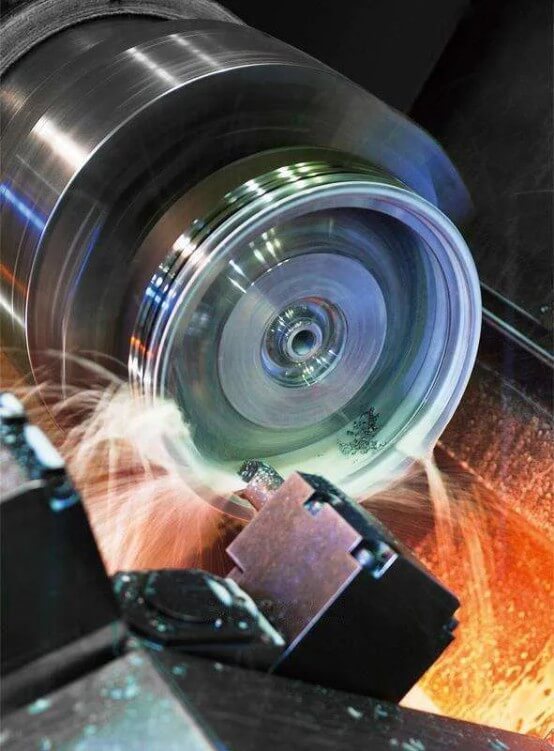
(2) Application in non-metallic material processing
1) Stone:
In stone processing, such as marble and granite, metal grinding wheels can effectively remove defects and rough parts on the stone surface through the grinding force generated by high-speed rotation, achieving high-precision grinding and polishing effects.
2) Glass:
Metal grinding wheels are mainly used for edge grinding and surface treatment in glass processing. Its uniform grinding force and controllable processing accuracy make the glass edge smooth and free of edge collapse, improving the quality of glass products.
3) Ceramic materials:
Due to their high hardness and brittleness, ceramic materials have high requirements for processing tools. Metal grinding wheels can ensure processing efficiency while avoiding cracks or damage on the ceramic surface by selecting appropriate abrasive grain size and hardness.
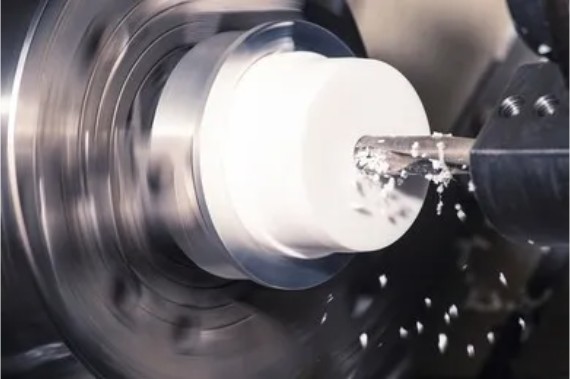
6.Wear and maintenance of metal grinding wheels
(1) Wear mechanism of grinding wheels
Metal grinding wheels will wear out during long-term use, mainly manifested in the passivation and shedding of abrasive grains and wear of the binder. Passivation of abrasive grains will lead to a decrease in grinding efficiency, shedding of abrasive grains will affect the shape accuracy of the grinding wheel, and wear of the binder may cause excessive shedding of abrasive grains. Therefore, understanding and mastering the wear mechanism of grinding wheels is of great significance for timely dressing and replacement of grinding wheels to ensure grinding quality.
(2) Causes of grinding wheel wear
The wear mechanism of grinding wheels is also affected by factors such as grinding materials, grinding parameters and the characteristics of the grinding wheel itself. For example, grinding high-hardness materials will lead to faster wear of the grinding wheel; too high a grinding speed will cause heat accumulation on the grinding wheel and accelerate wear; insufficient hardness and bond strength of the grinding wheel will lead to increased wear of the grinding wheel. Therefore, in actual use, it is necessary to reasonably select and use the grinding wheel according to the specific situation to reduce wear and extend the service life of the grinding wheel.
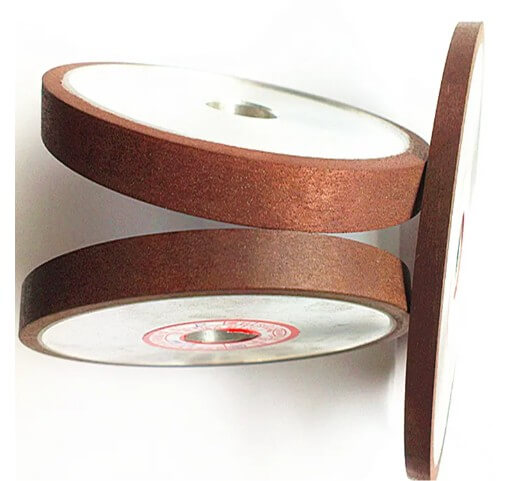
7.Dressing technology and frequency of metal grinding wheels
(1) Dressing technology
In order to maintain the grinding performance of the metal grinding wheel, the grinding wheel needs to be dressed regularly. Dressing methods include diamond pen dressing, rolling dressing and laser dressing. Diamond pen dressing is suitable for micro-dressing of the grinding wheel to restore the sharpness of the grinding wheel; rolling dressing is suitable for large-scale dressing of the grinding wheel to restore the shape accuracy of the grinding wheel; laser dressing is suitable for high-precision dressing of grinding wheels with complex shapes.
(2) Dressing frequency
The dressing frequency depends on the use and wear of the grinding wheel. Generally speaking, when the grinding efficiency of the grinding wheel drops significantly and the surface quality of the workpiece cannot meet the requirements, the grinding wheel needs to be dressed. In addition, for high-precision grinding applications, the grinding wheel needs to be dressed more frequently to ensure grinding accuracy and surface quality. In actual use, it is necessary to formulate a reasonable dressing plan according to the specific situation to ensure the grinding performance and service life of the grinding wheel.
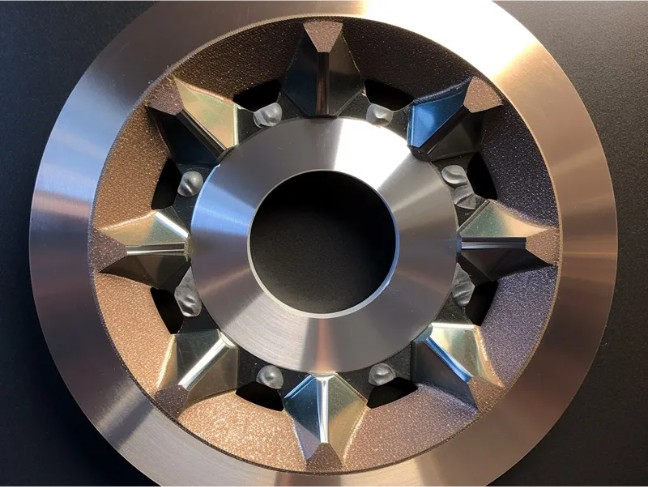
8.Summary
In summary, metal grinding wheels play an important role in the processing of different fields and different materials with their excellent grinding performance. By selecting the appropriate grinding wheel type and grinding parameters, efficient and high-precision processing effects can be achieved to meet various processing needs.