Best feeds and speeds for milling aluminum: optimizing processing efficiency and quality
In modern manufacturing, aluminum is widely used due to its light weight, corrosion resistance and good mechanical properties.
However, in the execution of aluminum milling process, choosing the best feeds and speeds for milling aluminum is a key factor to ensure processing efficiency, part accuracy and tool life. This article will explore in depth the best feeds and speeds for milling aluminum to help manufacturers optimize the processing process and improve production efficiency.
1.Importance and application areas of milling aluminum
Milling aluminum plays a vital role in modern industry, especially in industries with high precision requirements such as aerospace, automotive manufacturing and electronics. Aluminum has become one of the preferred materials in these industries due to its light weight, high strength and good machinability. Aluminum alloys have a wide range of applications, from aircraft structural components to automobile body frames to electronic product housings. Therefore, the technology of milling aluminum directly affects the quality and performance of the product.
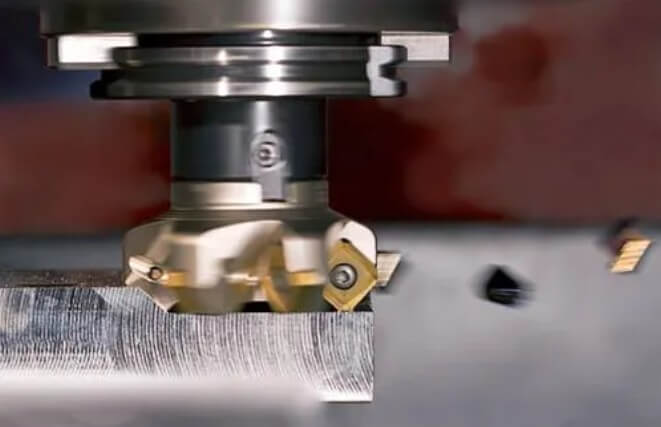
2.Basic principles of aluminum milling and challenges in the processing process
(1) Basic principles
The basic principle of aluminum milling is to use the rotation of the milling cutter combined with the relative feed motion of the workpiece to remove excess material from the surface of the aluminum workpiece. The milling cutter usually has multiple cutting edges and cuts the aluminum part by high-speed rotation. During the milling process, the relative motion between the tool and the workpiece includes the rotation of the milling cutter and the linear or curved movement of the workpiece, thereby realizing the processing of various shapes such as planes, grooves, and molded surfaces.
When milling aluminum, it is necessary to pay attention to selecting appropriate cutting parameters, such as cutting speed, feed rate, and cutting depth, to ensure processing efficiency and surface quality. In addition, the use of cooling lubricants can also effectively reduce tool wear and improve workpiece accuracy.
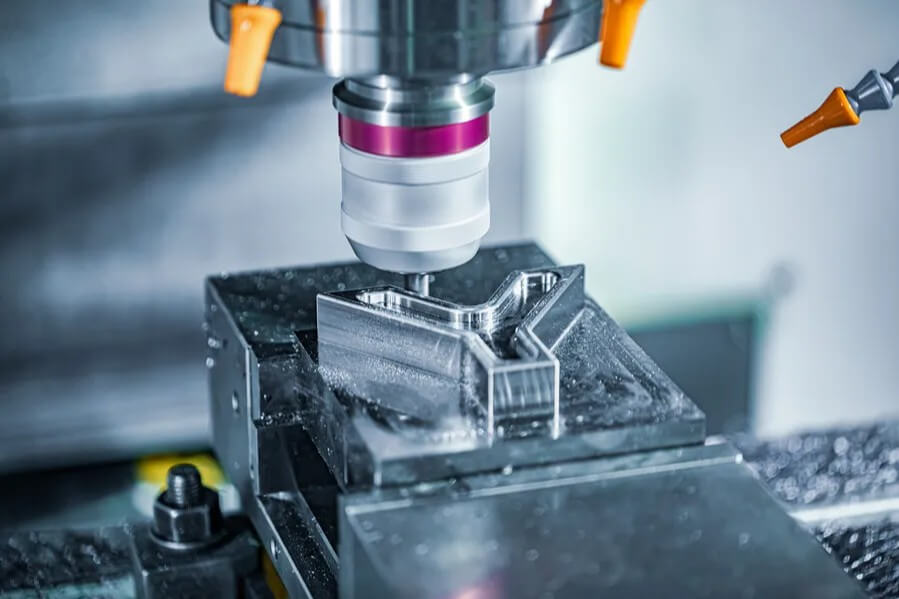
(2) Challenges in the processing process
Although aluminum has good machinability, it still faces many challenges in the milling process, such as tool wear, machining accuracy control, and surface finish. These problems directly affect processing efficiency and cost. For example, tool wear will lead to reduced machining accuracy and increase production costs; while insufficient surface finish may affect the appearance and service life of the product.
3.The significance and role of determining the best feeds and speeds for milling aluminum
Based on the challenges in the milling process mentioned above, determining the best feeds and speeds for milling aluminum is of vital significance and role in addressing and solving these challenges. The following is a detailed explanation of its importance:
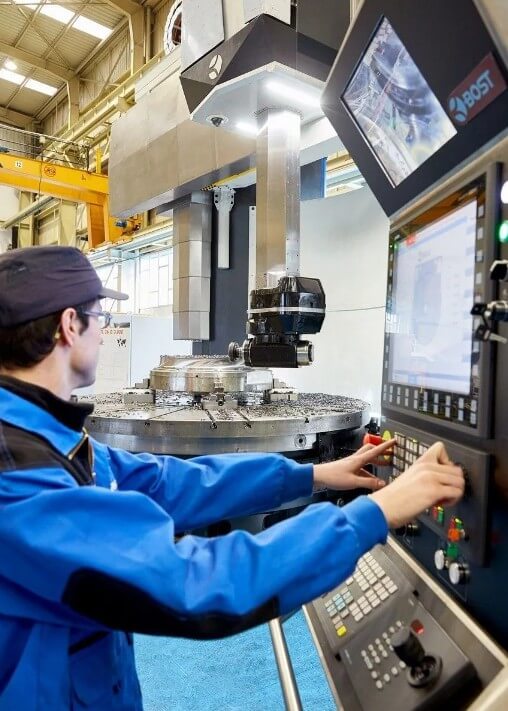
(1) Improving processing efficiency:
By optimizing the best feeds and speeds for milling aluminum, the processing time can be minimized. The optimal feed speed can enable the machine tool to complete the cutting action at the fastest speed while ensuring the tool life, thereby improving production efficiency.
(2) Ensuring processing quality:
The appropriate best feeds and speeds for milling aluminum can effectively reduce vibration and heat accumulation during the cutting process, avoid workpiece deformation and increase surface roughness, ensure processing accuracy and surface finish, and improve the quality of the workpiece.
(3) Extending tool life:
Improper feed and speed settings will cause the tool to bear excessive cutting force and heat, accelerate tool wear or even damage. Reasonable parameter selection can reduce the load on the tool, extend its service life, and reduce the frequency and cost of tool replacement.
(4) Reduce production costs:
By setting the best feeds and speeds for milling aluminum, tool consumption and machine maintenance costs can be reduced, while rework caused by machining quality issues can be avoided, thereby effectively reducing overall production costs.
(5) Improve safety:
Appropriate best feeds and speeds for milling aluminum can reduce unstable factors in the processing process, improve operational safety, and reduce the risk of accidents.
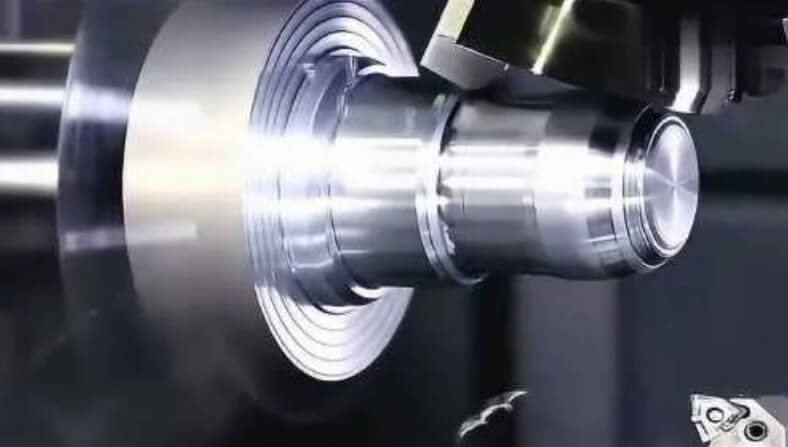
4.How to determine the best feeds and speeds for milling aluminum? What factors need to be considered?
When milling aluminum, choosing the right feed rate and cutting speed is the key to ensuring processing efficiency, workpiece quality and tool life. The following are the main factors and specific suggestions for determining the best feeds and speeds for milling aluminum:
(1) Workpiece characteristics
1) Material hardness and composition:
Different aluminum alloys have different hardness, strength and chemical composition, which have a greater impact on cutting parameters. For example, hard aluminum (2xxx series) is more difficult to process than pure aluminum (1xxx series) and requires lower cutting speeds and feeds.
2) Workpiece size and shape:
Large workpieces or thin-walled parts may require lower feed rates to avoid vibration and deformation.
(2) Tool type and condition
1) Tool material:
High-speed steel and carbide tools are common choices. Carbide tools usually allow higher cutting speeds and feeds.
2) Tool geometry:
The geometric parameters of the tool, such as the number of edges, rake angle, and back angle, will affect the cutting performance. For example, multi-edge tools can allow higher feeds per tooth.
3) Tool wear:
The cutting performance of new tools is different from that of worn tools. Worn tools may require adjustment of cutting parameters.
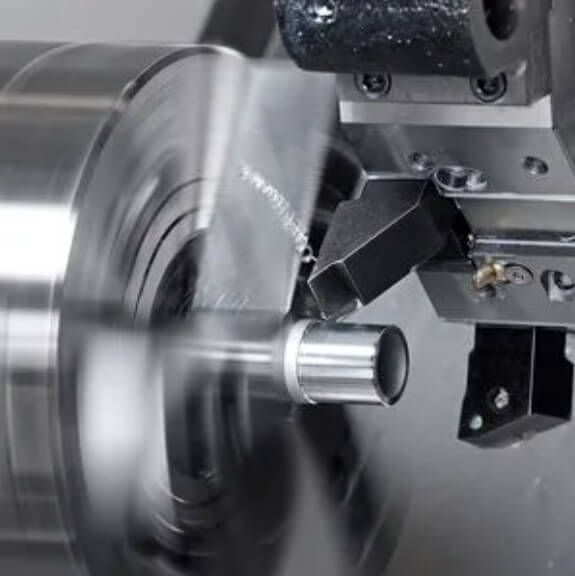
(3) Machine tool performance
1) Machine tool power and rigidity:
The power and rigidity of the machine tool limit the maximum cutting speed and feed. High-power, high-rigidity machines can withstand higher cutting loads.
2) Spindle speed range:
The maximum and minimum speeds of the machine tool spindle limit the range of cutting speed selection.
(4) Processing requirements
1) Surface roughness:
Higher surface roughness requirements usually require lower feed and cutting speeds.
2) Processing accuracy:
High-precision processing may require multiple passes, with lower cutting speeds and feeds used for each pass.
(5) Cooling and lubrication conditions
1) Coolant type:
Using appropriate coolants (such as emulsions or vegetable oils) can improve cutting conditions, tool life and processing quality.
2) Coolant supply method:
Sufficient coolant supply can reduce cutting temperature and improve cutting efficiency.
(6) Best feeds and speeds for milling aluminum Specific parameter recommendations
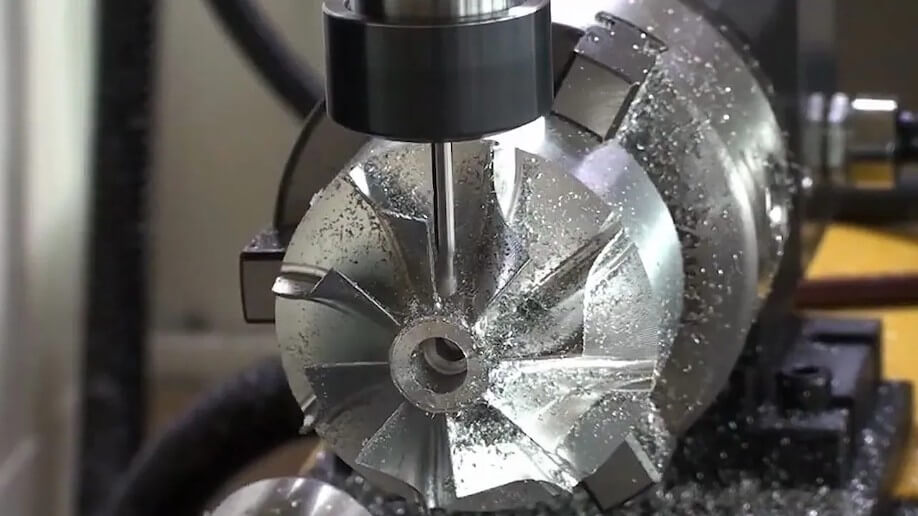
1) Cutting speed:
Usually selected between 3000 and 6000 revolutions per minute (rpm), depending on the tool diameter and workpiece hardness. When a carbide tool with a diameter of 10 mm is used to process hard aluminum, the cutting speed can be set to 400 to 500 meters per minute (m/min).
2) Feed speed:
The feed per tooth is usually between 0.1 and 0.3 mm/tooth (mm/tooth), and the feed per minute is between 100 and 300 mm/minute (mm/min). For rough machining, a higher feed rate can be selected; for finishing, the feed rate should be appropriately reduced.
3) Back cutting depth and side cutting depth:
During rough machining, the back cutting depth can be set to 2 to 5 mm (mm), and the side cutting depth is about 50% to 60% of the tool diameter; during finishing, the back cutting depth is about 0.1 to 0.5 mm (mm), and the side cutting depth should be appropriately adjusted according to the machining accuracy and surface quality requirements.
Summary:
In the actual machining process, the cutting parameters can be gradually adjusted by trial cutting, and the cutting effect (such as surface quality, tool wear, cutting force, etc.) can be observed to determine the best feeds and speeds for milling aluminum.
5.Calculation formula for the best feeds and speeds for milling aluminum
(1) Calculation of cutting speed
The calculation formula for cutting speed is Vc=π×D×N/1000
Where Vc is the cutting speed (m/min), D is the tool diameter (mm), N is the spindle speed (r/min).
(2) Calculation of spindle speed
The spindle speed can be derived from the cutting speed formula: N = 1000 × Vc / (π × D).
(3) Calculation of feed speed
The feed speed calculation formula is Vf = f × N
Where Vf is the feed speed (mm/min), f is the feed per tooth (mm/tooth), and N is the spindle speed (r/min).
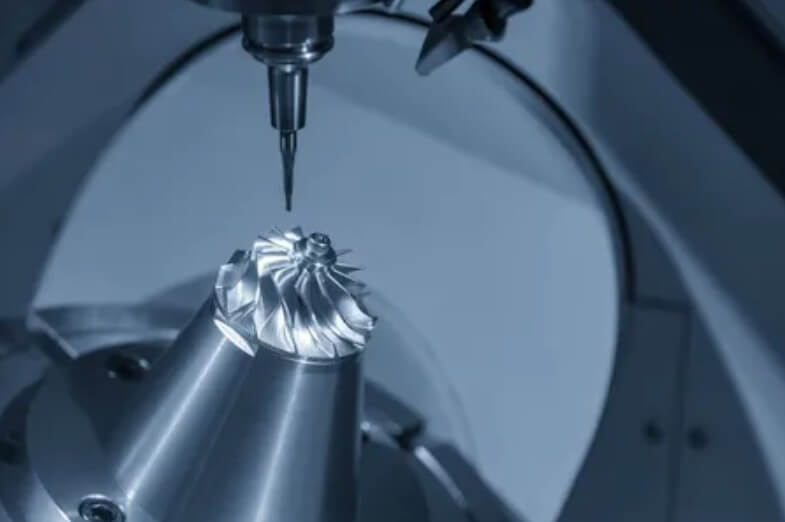
6.Case analysis of high-precision and high-efficiency milling by determining the best feeds and speeds for milling aluminum
(1) High-precision milling example
In high-precision milling aluminum applications, such as the manufacture of aviation parts, precise control of cutting parameters is crucial. For example, when machining aircraft wing ribs, extremely high surface finish and dimensional accuracy can be achieved by using polycrystalline diamond tools and optimized cutting parameters. Specifically, a surface roughness of Ra 0.8 μm can be achieved by using a cutting speed of 800 m/min and a feed speed of 0.1 mm/s.
(2) High-efficiency milling example
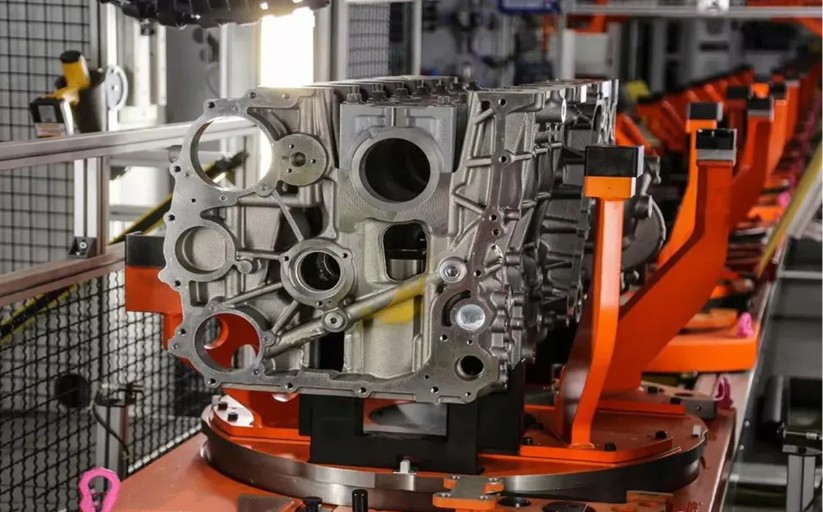
In the automotive manufacturing industry, high-speed milling technology is often used to improve production efficiency. For example, when machining an automobile engine block, the material removal rate can be significantly improved by using carbide tools and optimized milling parameters. Specifically, the use of parameters such as a cutting speed of 1200m/min and a feed speed of 0.5mm/s can reduce the machining time by 30%.
7.Summary
By rationally selecting the best feeds and speeds for milling aluminum, manufacturers can not only improve machining efficiency, but also extend tool life and ensure the accuracy and quality of machined parts. In actual production, continuous testing and adjustment of these parameters, combined with advanced CNC technology and high-quality cutting tools, will enable manufacturers to gain an advantage in the highly competitive market.