Aluminum boiling point: Diverse applications at high temperatures
Aluminum boiling point, signifies the superior performance of this silver metal at extreme temperatures. Aluminum has a boiling point of approximately 2,467° Celsius.At such high temperatures, aluminum is able to transform into a gaseous state and exhibit its unique physical properties. This property makes aluminum especially versatile for use in high temperature environments. In this article, we will discuss the boiling point of aluminum in depth. Understanding the boiling point of aluminum will help you control and optimize the performance of aluminum in various industrial applications.
Metal | Boiling Point (°C) |
Aluminum | 2467 |
Copper | 2595 |
Iron | 2750 |
Lead | 1750 |
Zinc | 907 |
Tin | 2690 |
Silver | 2212 |
Gold | 2500 |
.
Comparison of boiling points of several common metals
.
1.The difference between the boiling point and melting point of aluminum
The boiling point and melting point of aluminum are two important physical properties that play a key role in the processing and application of aluminum. The following is the difference between the boiling point and melting point of aluminum:
(1) Melting point
The melting point of aluminum is about 660°C. This is the temperature at which aluminum changes from a solid to a liquid state. At this temperature, aluminum begins to melt and becomes a liquid metal. The low melting point of aluminum makes it easy to process and manufacture a variety of aluminum products such as aluminum foil and aluminum sheet.
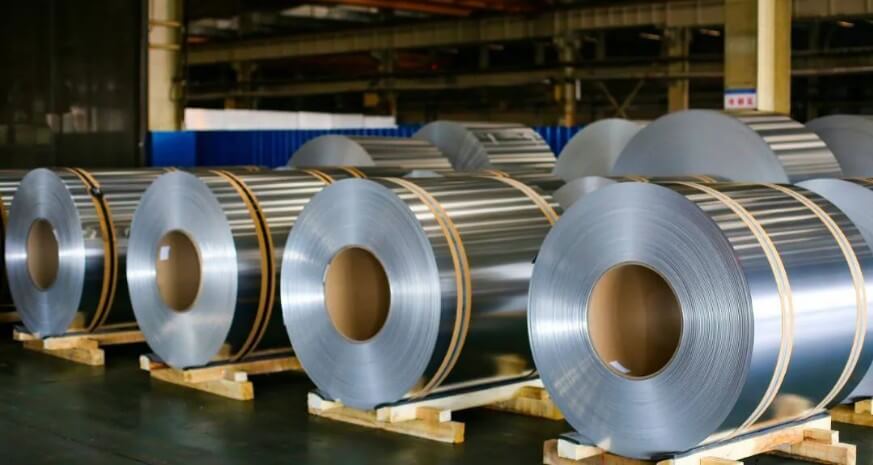
(2) Boiling point
The boiling point of aluminum is about 2467°C. This is the temperature at which aluminum changes from the liquid state to the gaseous state. Aluminum’s boiling point is much higher than its melting point, meaning that it does not evaporate at room temperature. Aluminum’s high boiling point allows it to withstand extremely high temperature environments, making it suitable for use in the manufacture of high-temperature equipment such as aircraft engines and rocket boosters. In addition, aluminum’s high boiling point makes it possible to perform evaporation and deposition processes at high temperatures for the production of high-tech products such as semiconductor devices.
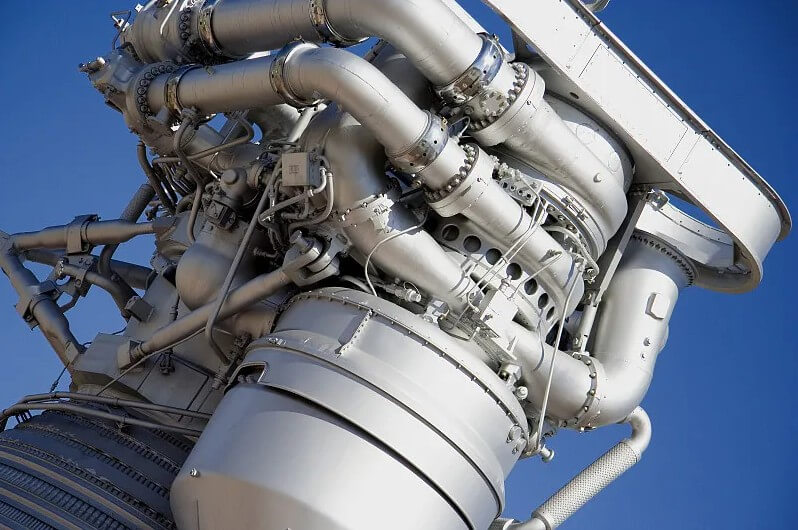
Summary:
In summary, the boiling and melting points of aluminum are significantly different: low melting point for ease of processing and fabrication, and high boiling point for resistance to high temperatures and for the manufacture of special equipment. These two properties together make aluminum in modern industry occupies an important position.
2.What applications are suitable for aluminum’s high boiling point?
Aluminum is a common and widely used metallic element, and its high boiling point gives it unique advantages in many fields. The following are some of the main applications for which aluminum’s high boiling point is suitable:
(1) Aerospace
Aluminum’s high boiling point allows it to remain stable at extreme temperatures and is therefore widely used in the manufacture of structural components for aircraft and rockets. For example, aircraft engine components and rocket fuel tanks require materials that are not easily deformed or damaged in high-temperature environments, and aluminum meets this need.
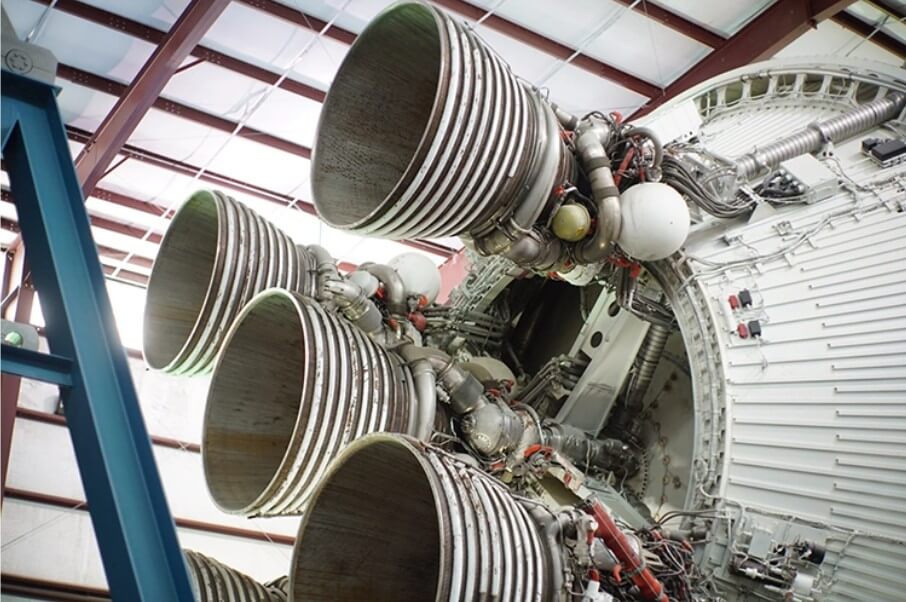
(2) Automotive industry
In automotive manufacturing, aluminum is often used in the manufacture of engine blocks, pistons and other high-temperature parts because of its high boiling point and good heat resistance. These parts need to withstand the impact of high-temperature gases during operation, and aluminum’s high boiling point ensures their reliability and durability.
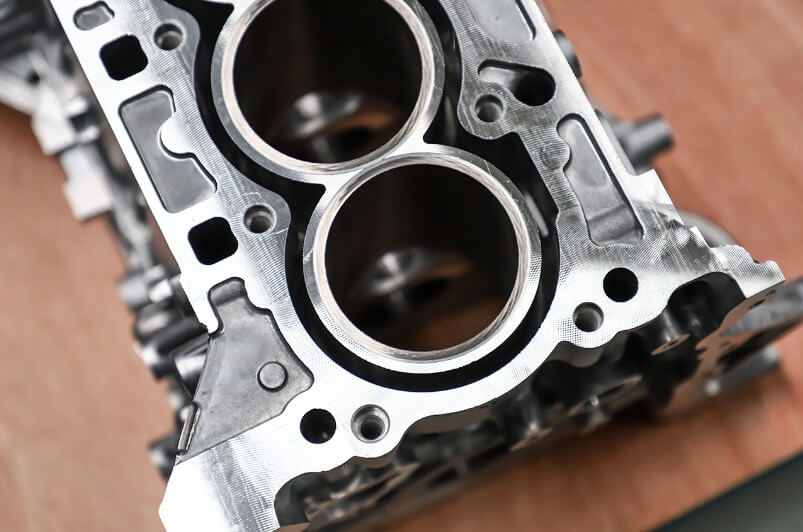
(3) Electronics and Semiconductor Industry
Aluminum’s high boiling point allows it to perform well in high-temperature evaporation and deposition processes, so it is used as a key conductive material in the manufacture of electronic devices and semiconductor chips. Through techniques such as vacuum evaporation, aluminum can be deposited at high temperatures to form thin films that are used to make circuits and connecting wires.
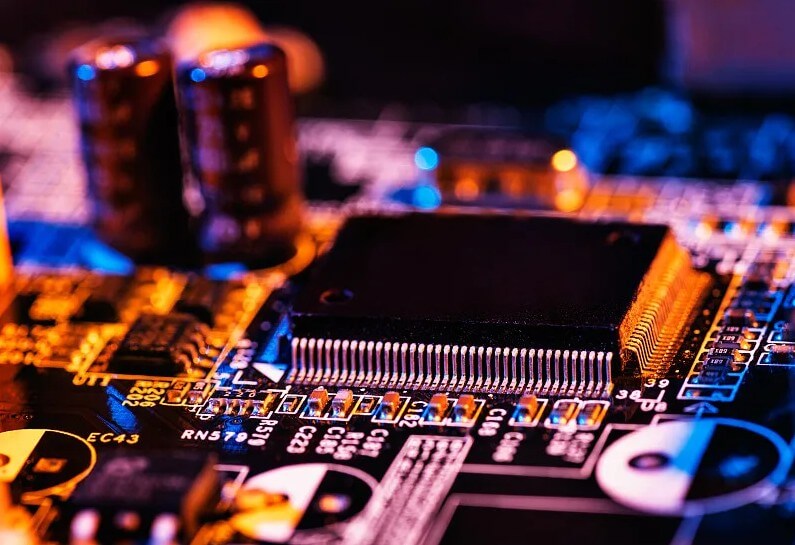
(4) High-temperature corrosion-resistant environment
Because aluminum reacts with oxygen at high temperatures to form a dense protective layer of alumina, it is ideally suited for the manufacture of equipment that operates in high-temperature and corrosive environments. For example, aluminum and its alloy materials are often used in chemical equipment such as reactors and heating elements to resist the erosion of chemicals.
(5) Construction and Decoration Materials
Aluminum’s high boiling point makes it less prone to deformation during processing, so it is often used to make aluminum profiles and decorative materials for construction. These materials are not only beautiful and durable, but also maintain stability in high-temperature environments, making them suitable for the manufacture of curtain walls, door and window frames, and other building components.
(6) High-temperature heat treatment equipment
In industrial production, many heat treatment equipment such as heat treatment furnaces and heating furnaces need to withstand high-temperature environments. Aluminum’s high boiling point makes it an ideal material choice for manufacturing these equipments, which can ensure the normal operation and long life of the equipments under high temperature.
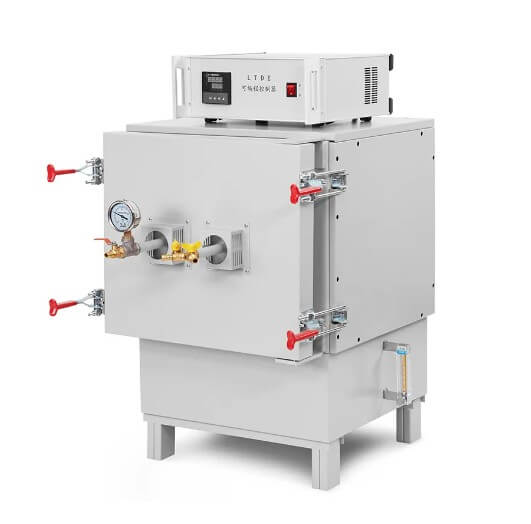
3.Relationship between aluminum boiling point and heat treatment process
Aluminum boiling point is one of its physical properties, refers to the standard atmospheric pressure, aluminum from the liquid state into a gaseous state temperature, the boiling point of aluminum is about 2467 ℃. And the heat treatment process is a method to change the properties of aluminum and aluminum alloy, mainly including heating, holding and cooling process. The relationship between the two is mainly reflected in the following aspects:
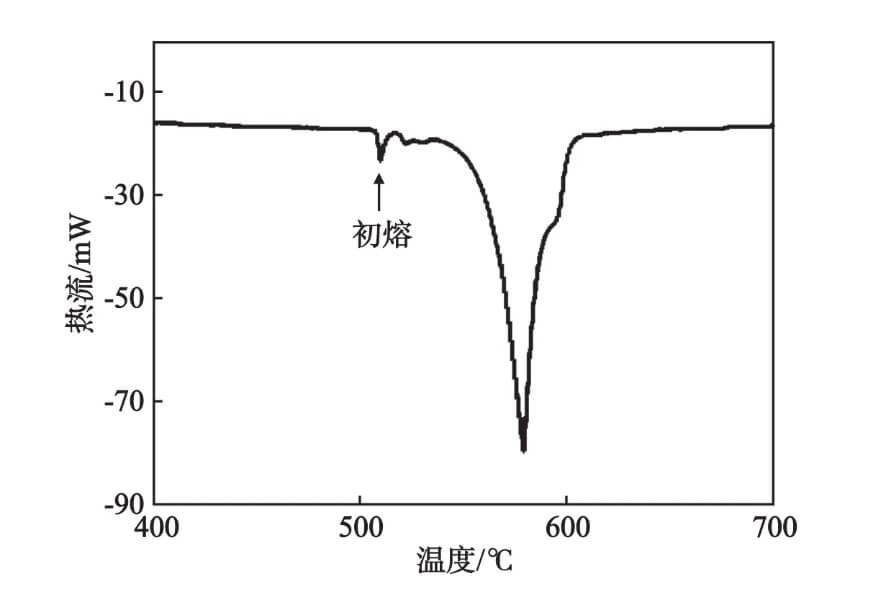
.
Effect of T6 Heat Treatment on Microstructure and Hardness of Cast Al-Si Alloy
.
(1) Heat treatment temperature limit:
The aluminum boiling point determines the upper limit of temperature during heat treatment. During heat treatment, the temperature must be controlled between the melting point (660.24°C) and the boiling point (2467°C) of aluminum to ensure that the aluminum is in a solid state and to avoid evaporation or unnecessary physical changes due to excessively high temperatures.
(2) Quenching process:
Quenching is an important step in the heat treatment of aluminum alloys and involves heating the alloy to a certain temperature and then cooling it rapidly. During the quenching process, the cooling rate must be fast enough to maintain the supersaturated solid solution state in the alloy so that properties can be realized in subsequent aging treatments. The quenching temperature is usually above the melting point of aluminum but well below the boiling point to ensure that the alloy can cool rapidly without melting.
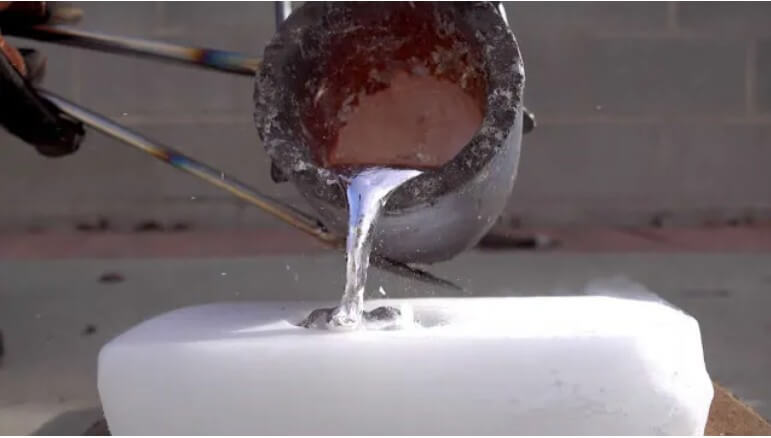
(3) Aging treatment:
Aging treatment is an important step after quenching that enhances the strength and hardness of the alloy by promoting the polarization and precipitation of solute atoms in the alloy through heating and holding at lower temperatures. The aging temperature is usually well below the boiling point of aluminum to avoid unwanted phase or structural changes in the alloy.
4.Factors affecting the boiling point of aluminum
Aluminum is an important industrial metal with a boiling point of 2467°C. In practice, however, the boiling point of aluminum is affected by a variety of factors. The following are a few key factors:
(1) Pressure
Aluminum boiling point varies with external pressure. In a high-pressure environment, the boiling point of aluminum will increase, and conversely, in a low-pressure environment, the boiling point will decrease. This phenomenon is particularly important in vacuum metallurgy, where the boiling point of aluminum can be adjusted by controlling the pressure, thus realizing the purification and separation of aluminum.
(2) Impurity content
Purity has a significant effect on the boiling point of aluminum. Even trace amounts of impurities may cause changes in the boiling point of aluminum. In industrial production, in order to obtain high purity aluminum, the content of impurities must be strictly controlled to avoid affecting the aluminum boiling point and its related properties.
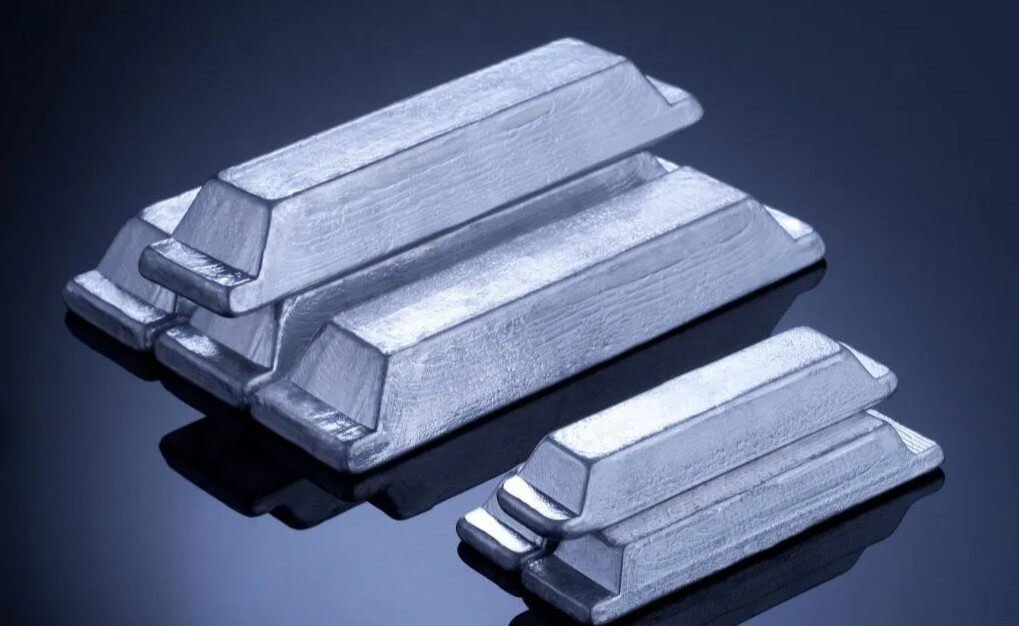
(3) Alloy composition
The alloys formed by aluminum and other metals will also affect its boiling point. Different alloy compositions can lead to different degrees of change in the boiling point of aluminum. For example, the boiling point of aluminum alloys is usually lower than that of pure aluminum, which makes aluminum alloys more fluid and workable in a specific temperature range for processes such as casting and welding.
(4) Temperature environment
The stability of the temperature environment can also have an effect on the aluminum boiling point. In environments with large temperature fluctuations, the aluminum boiling point may become unstable. Therefore, when performing high temperature processes involving aluminum, it is necessary to maintain a stable temperature environment to ensure stable aluminum properties.
(5) Physical state
The physical state of aluminum, such as particle size and surface state, also has an effect on its boiling point. For example, aluminum powder usually has a lower boiling point than bulk aluminum due to its large specific surface area. This characteristic has important applications in fields such as powder metallurgy and surface treatment.
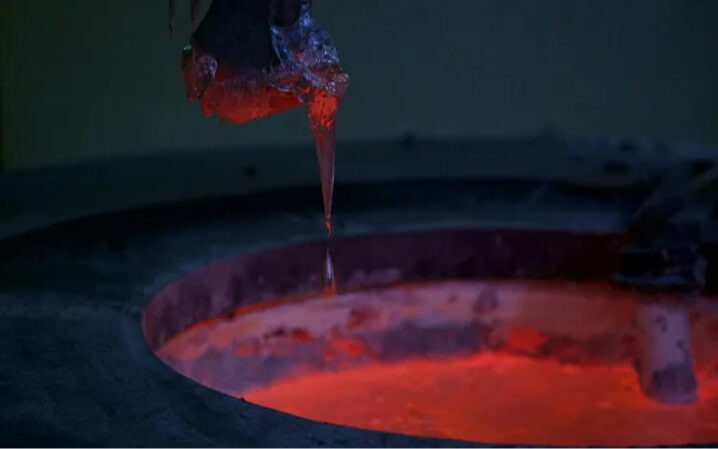
5.Impact of Aluminum Boiling Point on Production and Processing
(1) Selection of thermal processing temperature range:
The boiling point of aluminum is about 2467 ° C, much higher than its melting point of 660 ° C. In the thermal processing process, such as casting, forging, etc., the aluminum must be heated to above its melting point, but need to be far below its boiling point temperature. Too high a temperature will lead to aluminum evaporation loss, affecting the size and performance of the finished product. Therefore, a reasonable choice of heating temperature range is the key to ensure the quality of processing.
(2) Advantages of processing under vacuum environment:
Since aluminum is easy to evaporate at high temperatures, thermal processing in a vacuum environment can effectively reduce the evaporation loss of aluminum. The vacuum environment can reduce the boiling point temperature of aluminum, making aluminum evaporate at a lower temperature, thus reducing material waste and improving processing efficiency. In addition, the vacuum environment also helps to reduce oxidation and improve the surface quality of aluminum products.
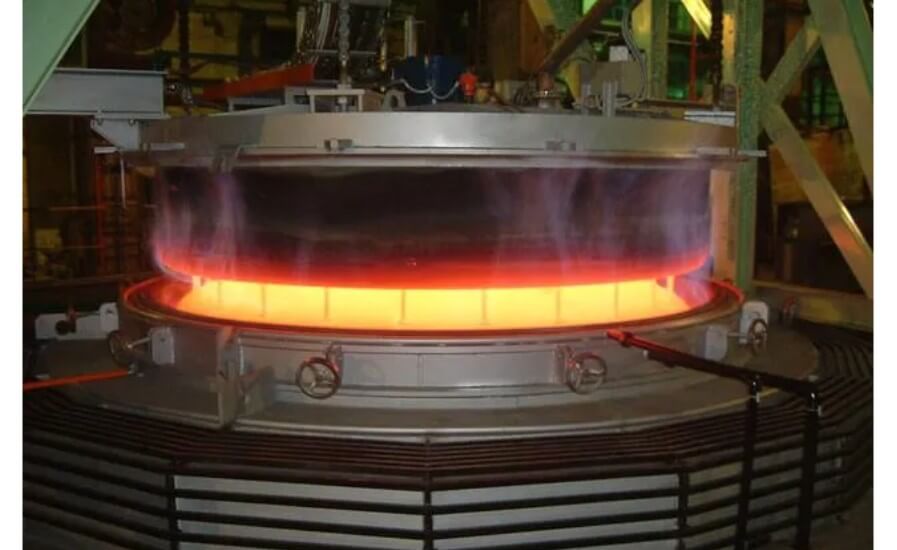
(3) Coordination of evaporation rate and processing speed:
Aluminum has a high boiling point, but its evaporation rate is significantly affected by temperature. In the rapid heating process, such as laser welding or electron beam welding, need to accurately control the heating speed and temperature, in order to avoid aluminum too fast evaporation leads to weld discontinuity or porosity and other problems. Coordinate the evaporation rate and processing speed can ensure the stability of the process and the mechanical properties of the finished product.
(4) The selection and proportion of alloying elements:
Adding other elements in aluminum to form aluminum alloy can change its boiling point temperature and other thermophysical properties. Appropriate alloying element ratios can reduce the evaporation rate of aluminum and improve its stability during high-temperature processing. For example, aluminum-silicon alloys show better resistance to thermal cracking in the casting process, partly because the addition of silicon reduces the evaporation loss of aluminum.
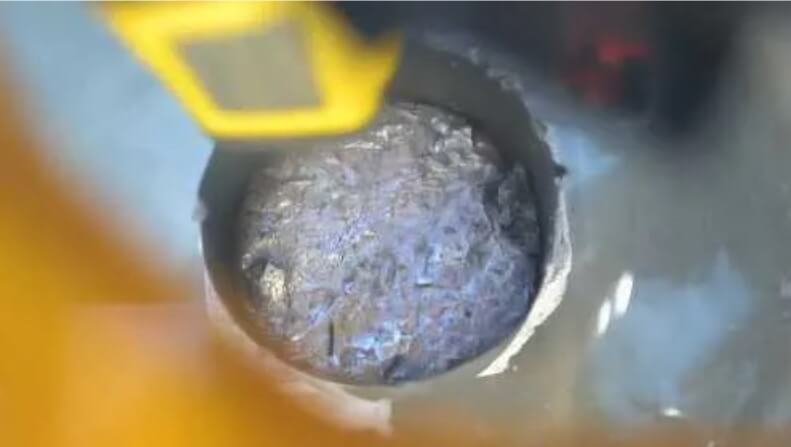
(5) Control during cooling:
The high boiling point of aluminum means that its cooling process takes a long time to release heat. In the heat treatment process, reasonable control of the cooling rate can avoid excessive stress inside the aluminum product and prevent deformation and cracking. At the same time, rapid cooling can refine the grain and improve the mechanical properties of aluminum, but care should be taken to avoid surface defects caused by excessive cooling.
6.Summarize
In summary, the boiling point of aluminum not only determines its excellent performance in high-temperature environments, but also greatly promotes the wide application of aluminum in many industries. From everyday objects to aerospace, the unique properties of aluminum make it an irreplaceable material in modern industry.
1 Comment