Is aluminum ductile: A comprehensive analysis of your doubts
Is aluminum ductile? This is a question worth exploring. Aluminum, as one of the important metal materials in modern industry, has a ductility that directly affects its processing performance and application range. Materials with good ductility can be stretched or rolled into thin sheets or filaments without breaking. So, how does aluminum ductility specifically manifest? What are the factors that affect aluminum ductility? What are its advantages in practical applications? This article will focus on these issues and answer the question “Is aluminum ductile?”.
1.Is aluminum ductile?
Aluminum is a silvery-white light metal that not only has good electrical and thermal conductivity, but also has excellent ductility. This property allows aluminum to be processed into various forms, such as foil, sheet, strip and filament, and is widely used in packaging, construction, aviation and automotive fields.
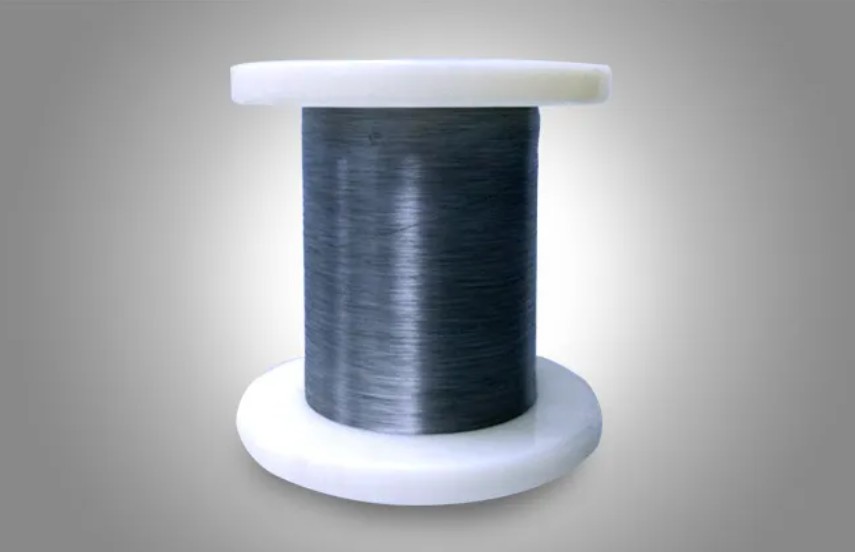
The reason why aluminum has excellent ductility is that it has a low hardness and can withstand large tensile strength and deformation without breaking when subjected to external forces. Because of this, aluminum can be pressed into extremely thin aluminum foil or even drawn into thin cables. So, is aluminum ductile? The answer to this question is that aluminum does have excellent ductility.
2.Is aluminum ductile? –Ductility of aluminum
(1) Definition and measurement criteria of ductility
Ductility refers to the ability of a material to be stretched or rolled into thin sheets or filaments without breaking under the action of external forces. Common standards for measuring the ductility of metals include elongation and cross-sectional reduction.
Elongation refers to the ratio of the maximum elongation of a material before it breaks under tension to its original length, while cross-sectional reduction refers to the ratio of the reduction in cross-sectional area of a material after it breaks under tension to its original cross-sectional area.
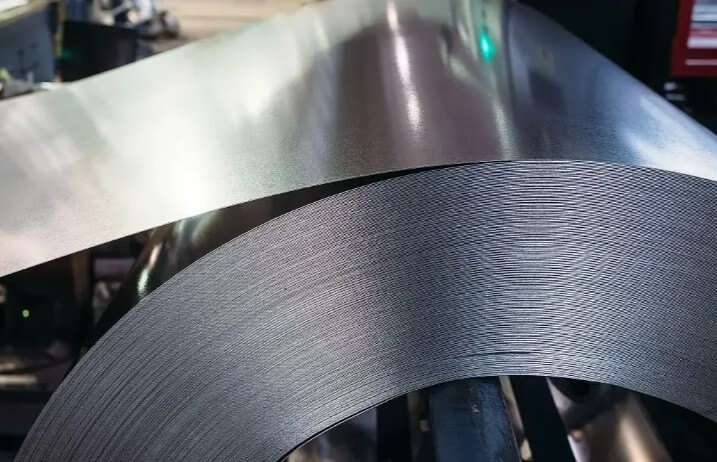
The elongation of aluminum is usually between 20% and 50%, which indicates that aluminum has a large deformation capacity without breaking during stretching. The cross-sectional reduction of aluminum is also high, indicating that aluminum can deform evenly during stretching without local necking. These characteristics make aluminum an ideal choice for manufacturing important materials such as aluminum foil and aluminum wire.
(2) The performance of aluminum ductility in practical applications
The ductility of aluminum allows it to be rolled into aluminum foil with a thickness of only a few microns, which is widely used in the packaging of food and medicine. Aluminum foil not only has good barrier properties and can effectively prevent the penetration of oxygen and water vapor, but also can maintain the fragrance and freshness of the items. In addition, the glossiness and printability of aluminum foil also make it occupy an important position in packaging and decoration.
In the field of construction, aluminum products such as aluminum plates and aluminum profiles are made into components of various shapes through processes such as rolling and bending, and are used in curtain walls, doors and windows, roofs and other parts. The lightness and good ductility of aluminum materials make their application in construction more flexible and diverse, which not only improves the beauty of the building, but also enhances the durability and safety of the building.

(3) Comparison of ductility with other metals
The ductility of aluminum is at an upper-middle level among metals. Although it is slightly inferior to precious metals such as gold and silver, it is far better than common metals such as iron and copper. Gold and silver have excellent ductility and can be drawn into very fine wires or pressed into very thin foils, but their high cost limits their widespread use in practical applications. In contrast, aluminum not only has good ductility but also has relatively low cost, making it the material of choice in many applications.
Iron has poor ductility and is prone to breakage during stretching, so it is not suitable for making thin sheets or filaments. Copper has good ductility, but also has problems such as high cost and easy oxidation. Aluminum, on the other hand, has both good ductility and low cost, and the oxide film formed on its surface can effectively prevent further oxidation, making it unique in many applications.
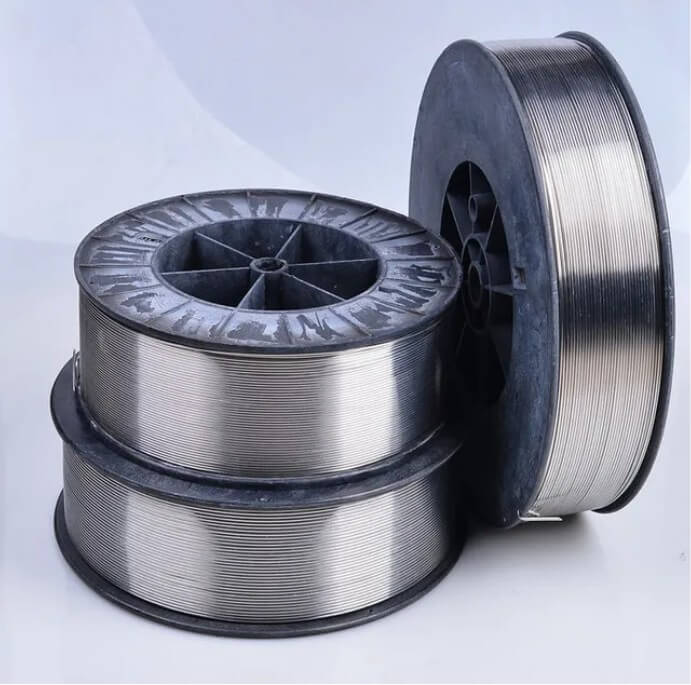
3.Is aluminum ductile? – Factors affecting aluminum ductility
(1) The relationship between aluminum purity and ductility
The purity of aluminum has a significant effect on its ductility. High-purity aluminum has better ductility because impurities hinder the sliding of aluminum atoms and increase the resistance of aluminum during deformation. For example, the elongation of 99.99% high-purity aluminum at room temperature can reach more than 50%, while the elongation of industrial aluminum containing impurities is lower.
The increase in purity can not only enhance the ductility of aluminum, but also improve its electrical conductivity and thermal conductivity. Therefore, in some fields with high requirements for material performance, such as electronic components and high-precision instrument manufacturing, high-purity aluminum is usually used. However, the production cost of high-purity aluminum is high, so in practical applications, it is necessary to select suitable aluminum materials according to specific needs.
(2) The influence of alloying elements on the ductility of aluminum
Aluminum can be alloyed by adding other elements to improve its strength or corrosion resistance. However, the addition of alloying elements usually reduces the ductility of aluminum. For example, aluminum-copper alloys and aluminum-magnesium alloys have higher strength but poorer ductility.
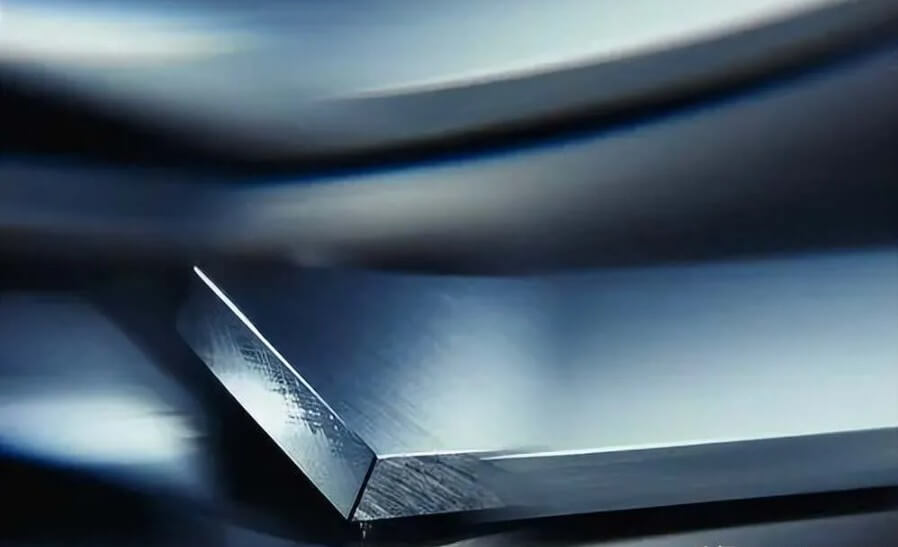
In aluminum alloys, the type and content of alloying elements have an important influence on ductility. Through reasonable alloy design and heat treatment process, it is possible to minimize the adverse effects on ductility while maintaining high strength. For example, by adding lithium, aluminum-lithium alloys improve their strength while maintaining good ductility and low density.
(3) The effect of processing technology on aluminum ductility
The processing technology of aluminum also has an important influence on its ductility. Appropriate processing temperature, speed and method can significantly improve the ductility of aluminum. For example, hot rolling and annealing can increase the ductility of aluminum because these processes can reduce the stress inside the aluminum and improve its plasticity.
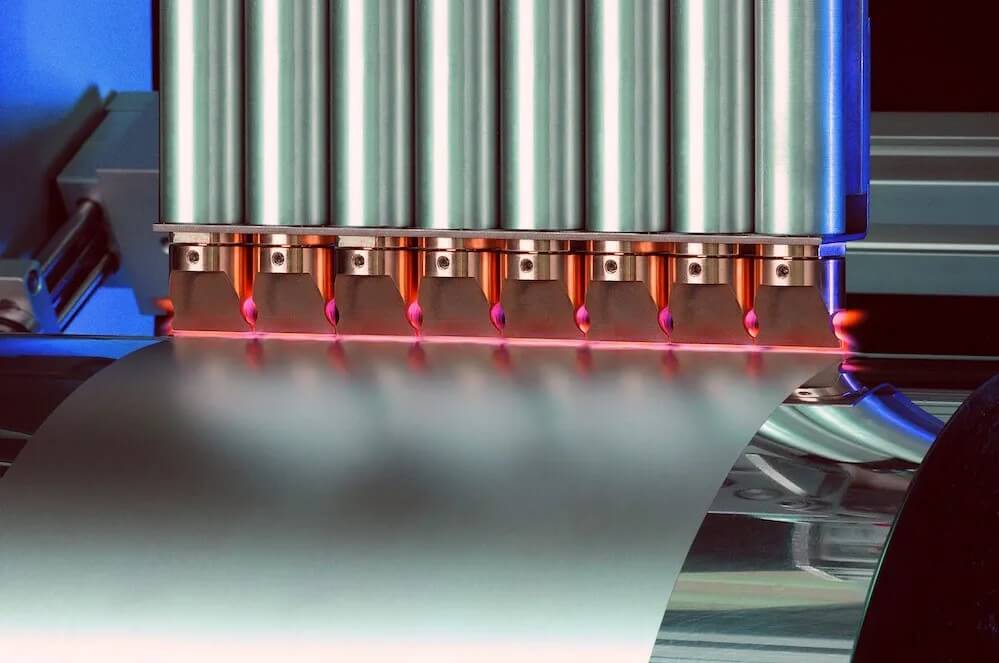
Cold processing, such as cold rolling and cold drawing, can increase the strength of aluminum, but it also reduces its ductility. Therefore, after cold processing, annealing is usually required to restore the ductility of aluminum. Annealing heats the aluminum material to a certain temperature and keeps it for a period of time, so that its internal structure recovers and recrystallizes, thereby eliminating internal stress and improving plasticity.
4.Is aluminum ductile? – Application of aluminum ductility in industry
(1) The relationship between the production of aluminum foil and ductility
The ductility of aluminum is a key factor in the production of aluminum foil. Aluminum foil is widely used as a thermal insulation material for food and pharmaceutical packaging and electronic products. The production process of aluminum foil requires that the aluminum ingot be rolled multiple times to gradually reduce its thickness to a few microns. This process relies on the excellent ductility of aluminum.
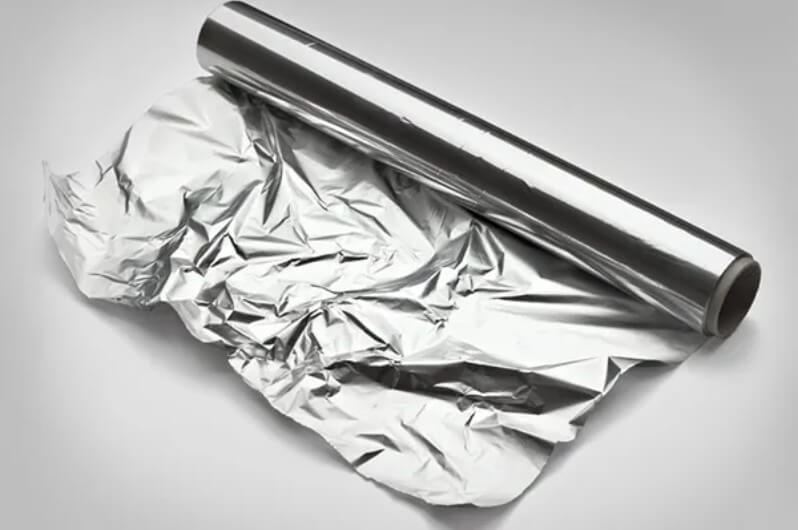
In the production process of aluminum foil, rolling temperature and lubrication conditions have an important influence on the quality of aluminum foil. By optimizing the rolling process parameters, the surface quality and mechanical properties of aluminum foil can be further improved. For example, high-temperature rolling can reduce the surface roughness of aluminum foil and improve its gloss and ductility. In addition, annealing treatment is required during the production process of aluminum foil to eliminate internal stress and improve the softness and ductility of aluminum foil.
(2) Application of aluminum alloys in the aerospace field
Aluminum alloys are widely used in the aerospace field due to their high strength, low density and good ductility. Structural components of aircraft and spacecraft are often made of aluminum alloys to reduce weight and improve fuel efficiency.
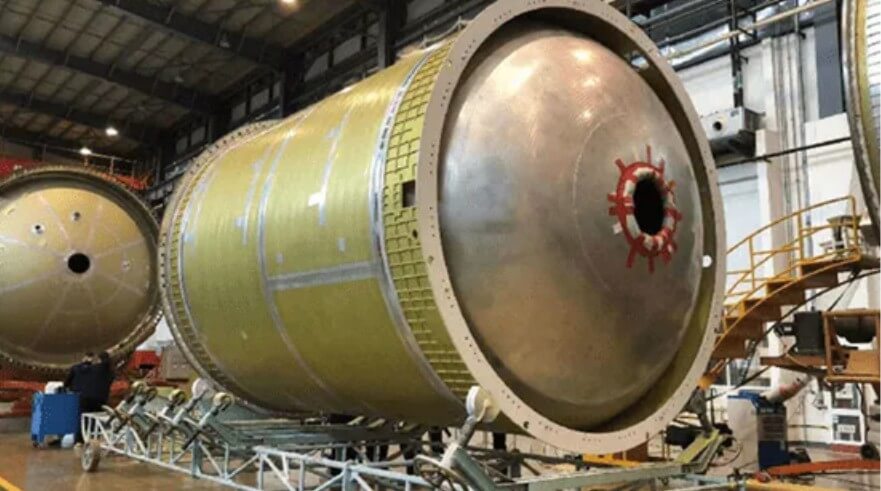
In the aerospace field, aluminum-lithium alloys are increasingly used. By adding lithium elements, aluminum-lithium alloys not only improve strength, but also maintain good ductility and low density, making them an important material in the aerospace field. The application of aluminum-lithium alloy can significantly reduce the weight of aircraft and improve its fuel efficiency and flight performance. For example, modern civil aircraft such as Airbus A380 and Boeing 787 use a large amount of aluminum-lithium alloy materials.
(3) Application of aluminum in packaging materials
The ductility of aluminum makes it an ideal choice for packaging materials. Packaging materials such as aluminum cans and aluminum bottles are not only light, but also have good sealing and corrosion resistance. They are widely used in the packaging of beverages, food and other products.
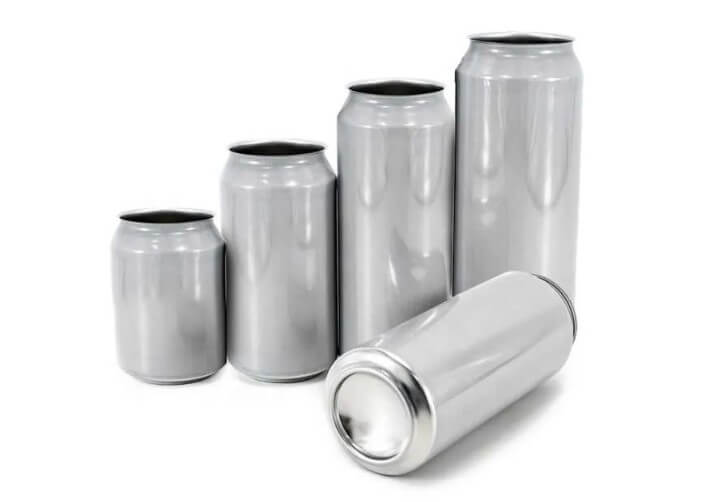
The application of aluminum packaging materials not only improves the protection and preservation of products, but also enhances the aesthetics and market competitiveness of products. For example, the application of aluminum cans in beverage packaging is not only light and easy to carry, but also has good sealing and corrosion resistance, ensuring the quality and taste of beverages. In addition, the recyclability of aluminum materials also makes its application in packaging materials more environmentally friendly and sustainable.
5.Summary
In summary, is aluminum ductile? Yes, aluminum does have good ductility. This makes aluminum perform well in the manufacture of products such as aluminum foil, aluminum plate, and aluminum profiles, and is widely used in construction, aerospace, packaging and other industries.