Precision planting parts: CNC efficient and precise production
With the rapid development of modern agriculture, the demand for precision planting parts continues to increase, and efficient production processes have become the key. This article will analyze the material selection, process flow and key technologies involved in the production of precision planting parts, and explore the role of CNC machining in improving production efficiency and product quality.
1.Overview of precision planting technology
(1) The importance of precision planting technology
As an important part of modern agriculture, precision planting technology has greatly promoted the efficiency and quality of agricultural production. By precisely controlling various aspects such as sowing, fertilization, and irrigation, precision planting technology can significantly increase crop yields, reduce resource waste, and have a positive impact on environmental protection. In the context of growing global food demand, precision planting technology is particularly important. It can not only increase output per unit area, but also reduce dependence on natural resources through scientific management, thereby achieving sustainable development of agriculture.
(2) The role of precision planting parts in precision implant technology
Precision planting parts are the key to realizing precision implant technology. These components include seed meters, fertilizer applicators, sprinkler irrigation systems, etc., which are designed and manufactured with high precision to ensure accuracy and consistency during the planting process. For example, precision fertilizer applicators can accurately control the type and amount of fertilizer according to the needs of the soil and crops, avoiding environmental pollution and resource waste caused by over-fertilization.
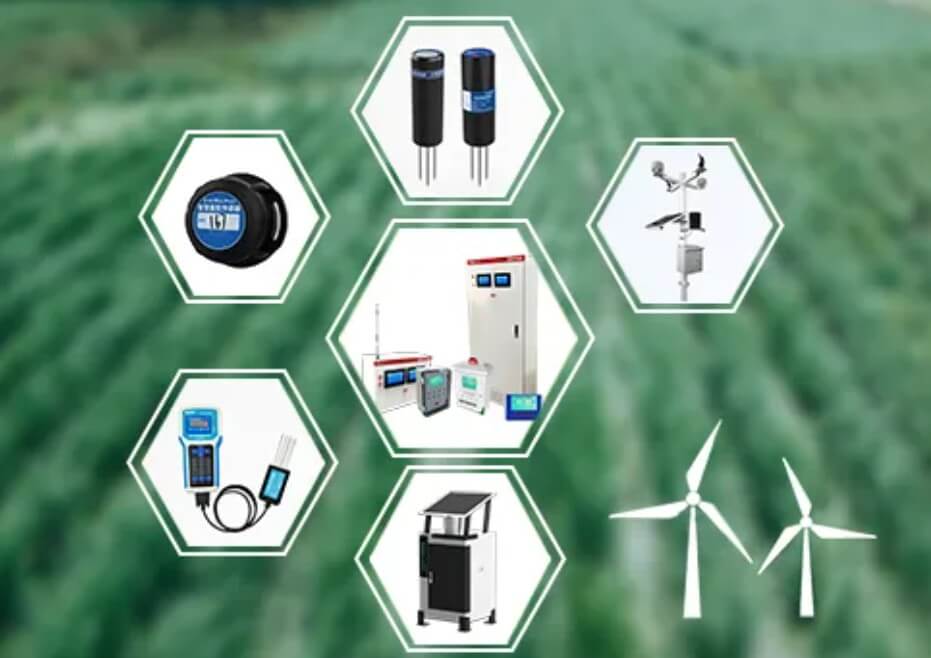
2.Overview of precision planting parts
(1) Types of precision planting parts
There are many types of precision planting parts, each with its own specific functions and application scenarios. Common precision planting parts include:
1) Seed metering device: used for precise sowing to ensure that seeds are distributed at predetermined spacing and depth.
2) Fertilizer: Control the amount and location of fertilizer to meet the needs of different stages of crop growth.
3) Sprinkler irrigation system: Through precise sprinkler head design, uniform irrigation is achieved and water resources are saved.
4) Sensors: used to monitor soil moisture, temperature, nutrient content and other environmental parameters to provide data support for precision agriculture.
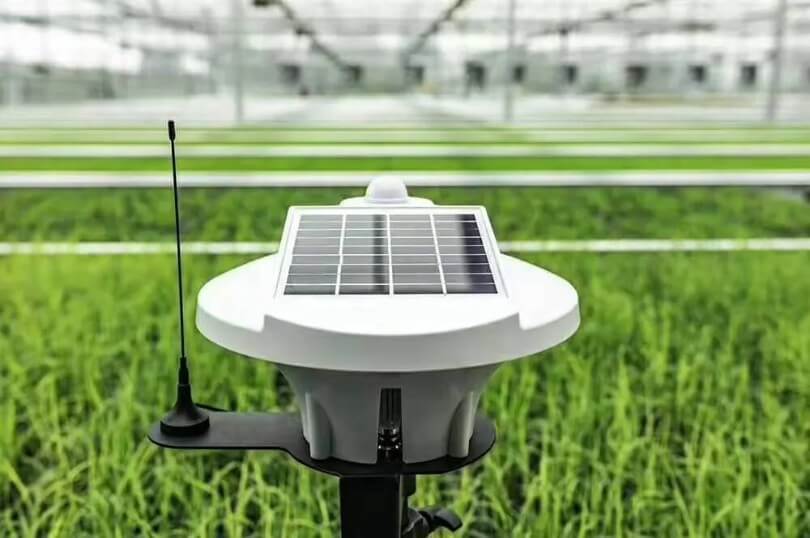
(2) Functions of precision planting parts
The main functions of these components are to improve planting accuracy, reduce resource waste, and improve crop yield and quality. For example, a precision seed meter can ensure that each seed is accurately sown at a predetermined position, reducing seed waste and ensuring uniformity of crop growth; a sprinkler irrigation system improves water utilization efficiency by evenly distributing water and ensuring the required amount of water for crop growth. Water supply; sensors provide scientific basis for agricultural management by monitoring environmental parameters in real time, helping farmers make more accurate decisions.
3.Material selection for precision planting parts
The material selection of precision planting parts is crucial. It is not only related to the durability and functionality of the components, but also directly affects the implant efficiency and cost. Here are several commonly used materials and their properties:
(1) Stainless steel
1) Advantages: Stainless steel has excellent corrosion resistance and oxidation resistance and can be used for a long time in harsh environments. In addition, stainless steel has high strength and hardness and can meet the high-precision requirements of precision planting parts.
2) Disadvantages: The cost is relatively high and the processing is difficult.
3) Application scenarios: Suitable for making precision seeder components, irrigation systems and other key components.
(2) Aluminum alloy
1) Advantages: Aluminum alloy has low density, light weight, good strength and corrosion resistance. In addition, aluminum alloy has excellent processing properties and is easy to form and cut.
2) Disadvantages: The hardness is relatively low and wear may occur in high-intensity working environments.
3) Application scenarios: often used to make components such as planting brackets and greenhouse frames.
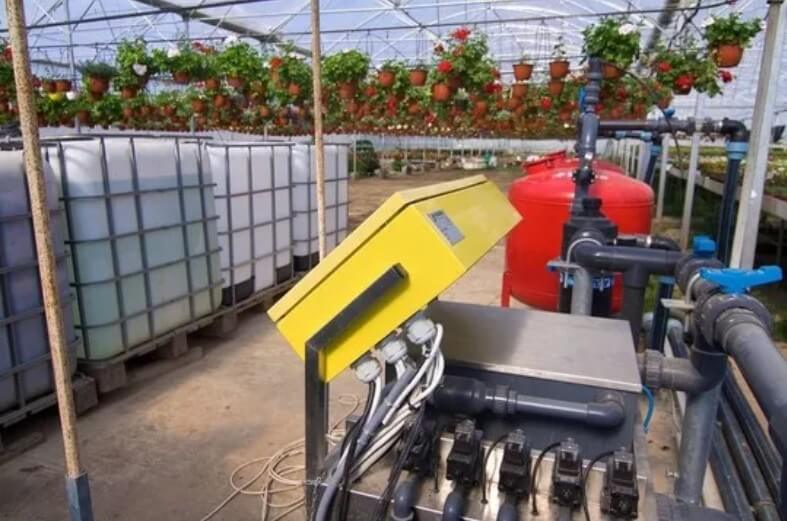
(3) Engineering plastics
1) Advantages: Engineering plastics have good self-lubricating and corrosion resistance, and have low cost. In addition, engineering plastics have excellent processing properties and can meet the molding needs of complex structures.
2) Disadvantages: The strength and heat resistance are relatively low, and deformation or damage may occur in high-temperature or high-intensity working environments.
3) Application scenario: Suitable for making non-critical components such as irrigation pipes and seeding trays.
(4) Ceramic materials
1) Advantages: Ceramic materials have high hardness, good wear resistance, and excellent high temperature resistance and corrosion resistance.
2) Disadvantages: It is relatively brittle, easy to break, and difficult to process.
3) Application scenarios: often used to make key components such as precision nozzles and sensors.
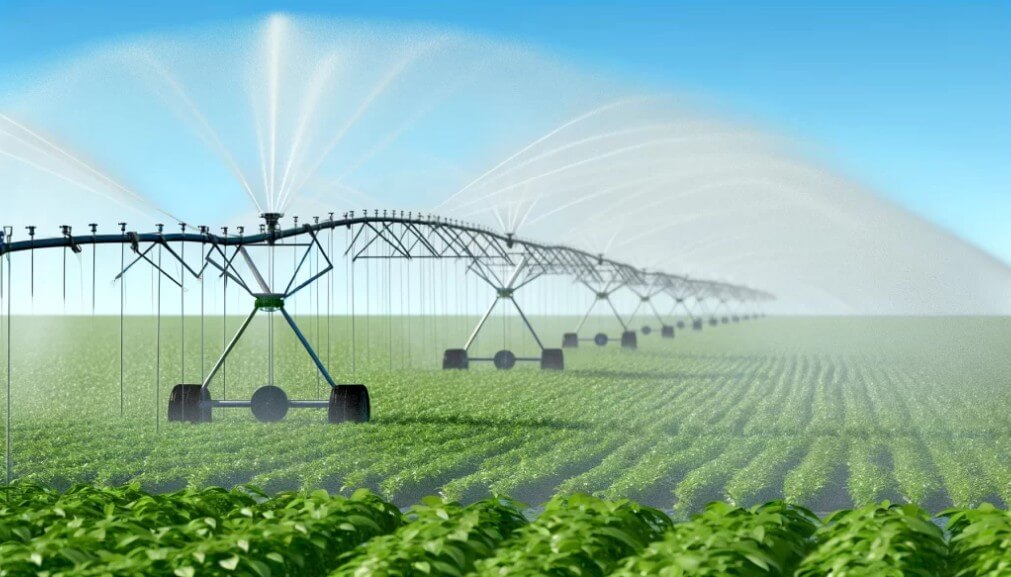
(5) Composite materials
1) Advantages: Composite materials have excellent comprehensive properties and can be customized according to specific needs. For example, carbon fiber composites have extremely high strength and stiffness while weighing much less than metal materials.
2) Disadvantages: The cost is higher, and processing and maintenance are difficult.
3) Application scenarios: Suitable for making high-strength, high-precision planting machinery components, such as drone frames, high-precision seeders, etc.
4.Precision planting parts production process
Precision planting parts are an important part of modern agricultural equipment, and the optimization of their processing technology is directly related to the improvement of planting efficiency and crop yield. Below is a detailed exploration of the design and manufacturing process of precision planting parts.
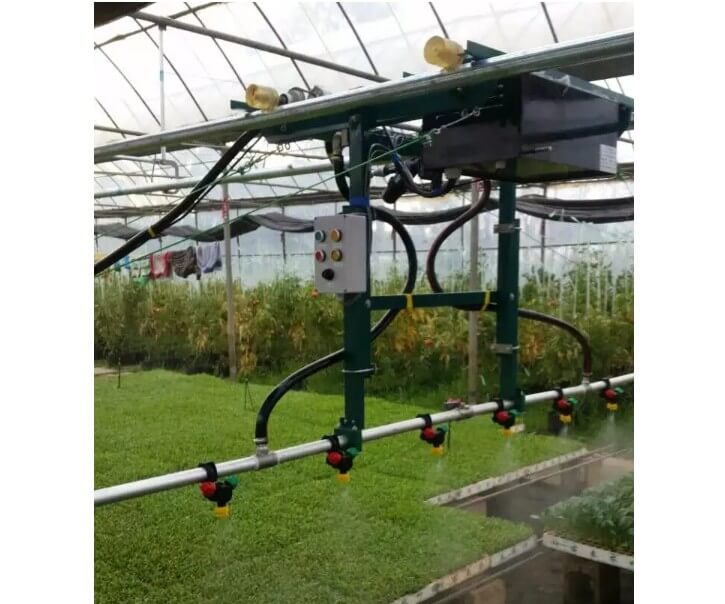
(1) Design of precision planting parts
1) Need analysis:
First, according to different planting environments and crop needs, the functional requirements of precision planting parts are clarified, such as sowing accuracy, fertilizer amount control, etc. At the same time, user feedback and market information are collected to provide data support for design.
2) Concept design:
Based on demand analysis, preliminary conceptual design is carried out, including the overall structure of components, material selection and application of key technologies. Use CAD software to conduct three-dimensional modeling, simulate the working status of components, and conduct preliminary interference inspection and motion simulation.
3) Detailed design:
Based on the conceptual design, detailed parts design is carried out to determine the technical requirements such as size, tolerance and surface roughness of each part. Consider the convenience and economy of processing and assembly, and optimize the design plan.
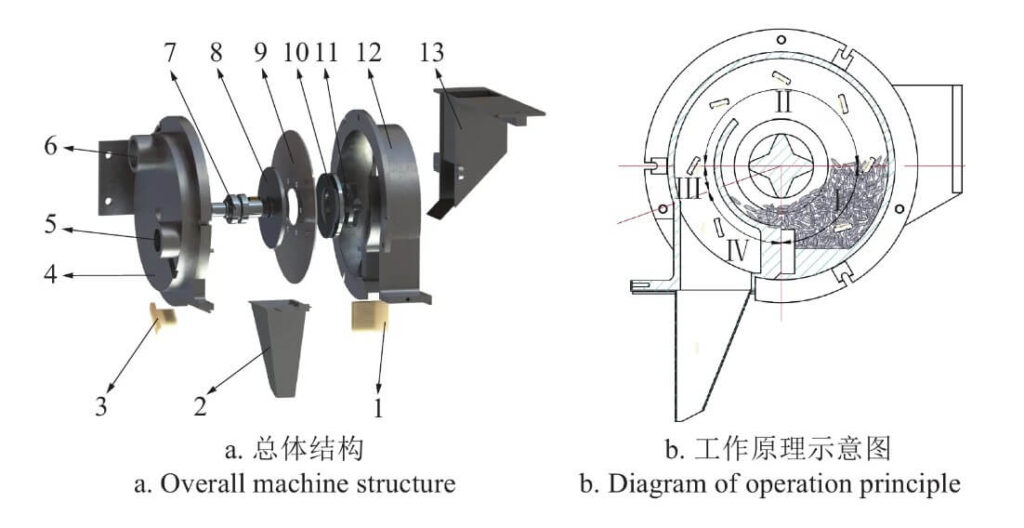
(2) CNC machining process planning
1) Process analysis:
Conduct process analysis on each part of the planting components to determine the processing content, processing sequence and processing method. Select the appropriate CNC machine tool and processing tool according to the material, shape and accuracy requirements of the part.
2) CNC programming:
Use CAM software for CNC programming to generate tool paths and processing codes. When programming, it is necessary to consider the selection of cutting parameters, optimization of tool paths and error control during processing to ensure processing efficiency and accuracy.
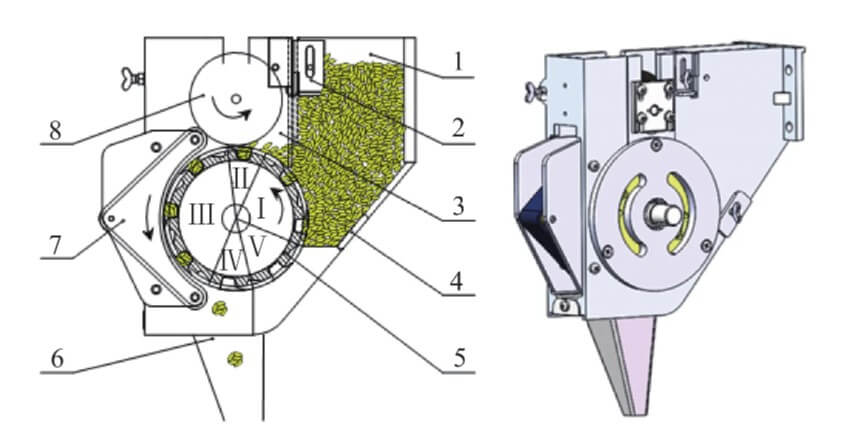
(3) CNC manufacturing process
1) Raw material preparation:
According to the design requirements, select appropriate raw materials and perform necessary pretreatment, such as cutting or heat treatment, to ensure that the material properties meet the processing requirements.
2) Rough machining:
Use CNC machine tools for rough machining to quickly remove most of the allowance to prepare for subsequent finishing. When roughing, appropriate cutting parameters should be selected to improve processing efficiency.
3) Finishing:
On the basis of rough machining, finish machining is performed to ensure that the dimensional accuracy, shape accuracy and surface roughness of the parts meet the design requirements. During finishing, appropriate tools and cutting parameters should be selected, and strict online testing and quality control should be carried out.
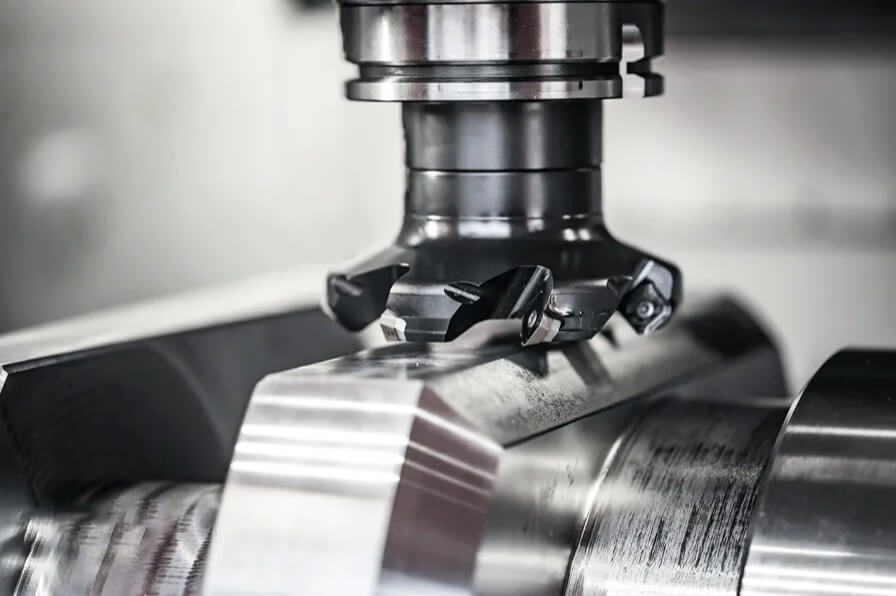
4) Surface treatment:
As needed, perform surface treatment on the parts, such as nickel plating, oxidation or sandblasting, etc., to improve the wear resistance, corrosion resistance and aesthetics of the parts.
5) Assembly and debugging:
The processed parts are assembled according to the design requirements to form complete precision planting components. After assembly is completed, debugging and performance testing are carried out to ensure that the functional indicators of the components meet the design requirements.
6) Quality inspection:
Conduct comprehensive quality inspection on the assembled precision planting components, including dimensional inspection, geometric tolerance inspection, surface quality inspection and performance testing, etc. Ensure that all indicators comply with national standards and user requirements.
5.Key production technologies for precision planting parts
(1) CNC processing technology
CNC machining technology is an integral part of modern manufacturing, especially in the production of precision planting parts. CNC processing uses computer programs to control machine tools for automated processing, which can achieve high-precision and high-efficiency processing effects. Here are several key advantages of CNC machining technology in the production of precision planting parts:
1) High-precision processing:
CNC machine tools are capable of micron-level processing to ensure the size and shape accuracy of implant components. This is critical for precision planting parts that require a precise fit, such as planting drills, planters, etc.
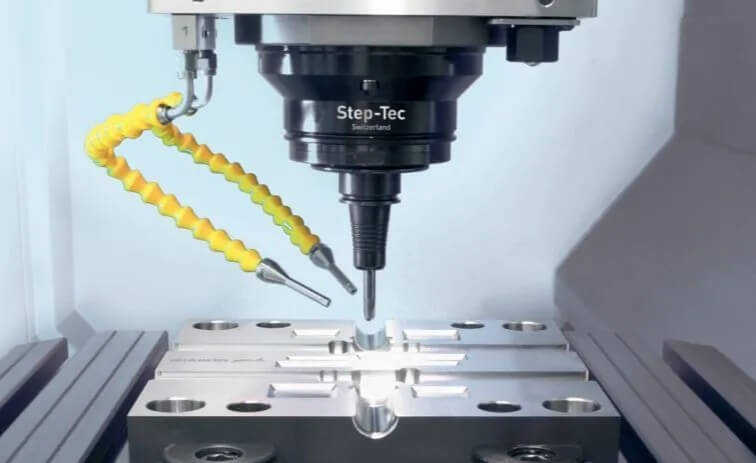
2) Flexibility:
CNC processing technology can quickly adjust processing parameters by modifying computer programs to adapt to the production of different types and specifications of planting components, greatly shortening the production cycle.
3) Wide adaptability of materials:
CNC machine tools can process various metal materials, such as stainless steel, aluminum alloys, composite materials, etc. These materials are widely used in precision planting parts and have different performance advantages.
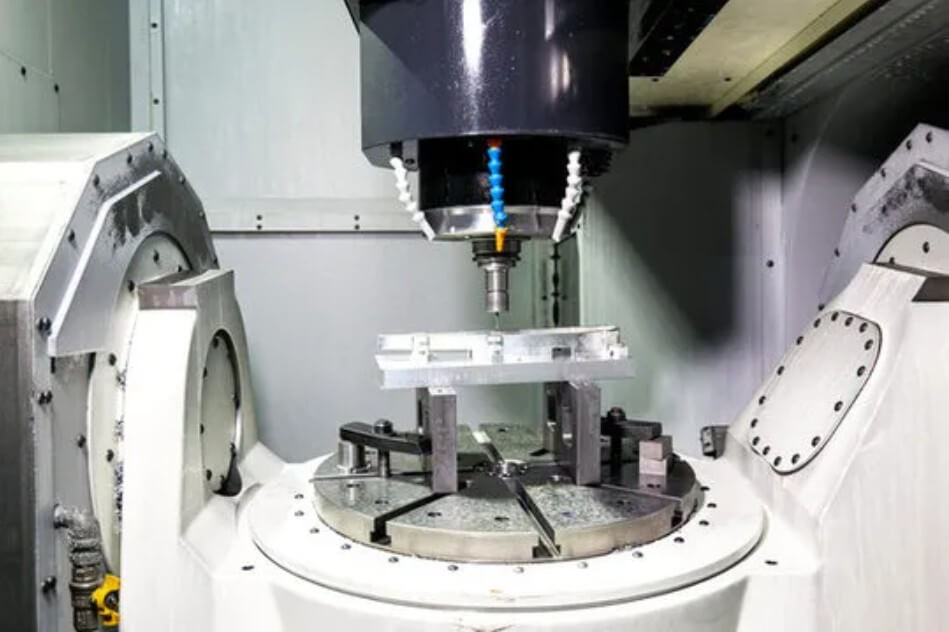
(2) Surface treatment technology
Surface treatment technology is an important means to improve the performance of precision planting parts. Through different surface treatment methods, the wear resistance, corrosion resistance and aesthetics of components can be significantly enhanced. The following are several commonly used surface treatment technologies:
1) Nickel plating:
Nickel plating is a common electroplating process. By plating a layer of nickel on the surface of planting components, its wear resistance and corrosion resistance can be significantly improved. Nickel plating is smooth and hard, which can effectively extend the service life of components.
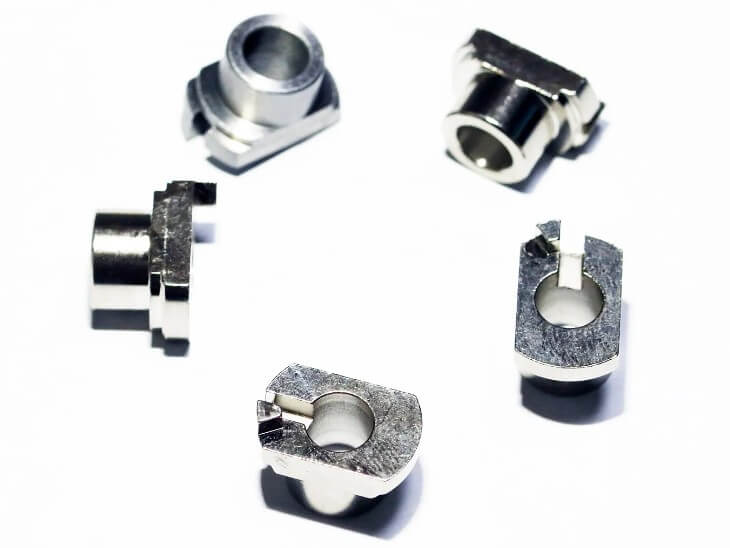
2) Oxidation treatment:
Oxidation treatment is mainly used for planting parts of aluminum and its alloy materials. A dense oxide film is formed on the surface of the component through chemical reaction, which not only improves the corrosion resistance, but also increases the surface hardness and wear resistance.
3) Sand blasting:
Sandblasting is the process of impacting the surface of components by spraying fine abrasives at high speed to remove surface impurities and increase surface roughness. This treatment method not only improves the adhesion of the component, but also improves its mechanical properties to a certain extent.
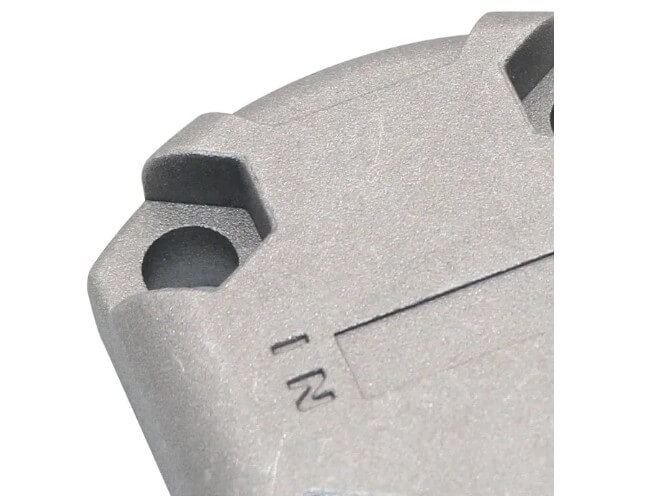
(3) Comprehensive application case analysis
Taking the production of precision seeder components as an example, CNC processing technology is first used to process the core components of the seeder, such as seeding wheels and seed meters, to ensure their dimensional accuracy and shape accuracy. Subsequently, surface treatment techniques such as nickel plating and oxidation treatments are applied to these parts to enhance their resistance to corrosion and wear. After these treatments, the seeder can not only work stably in various harsh environments, but also significantly extend its service life and reduce maintenance costs.
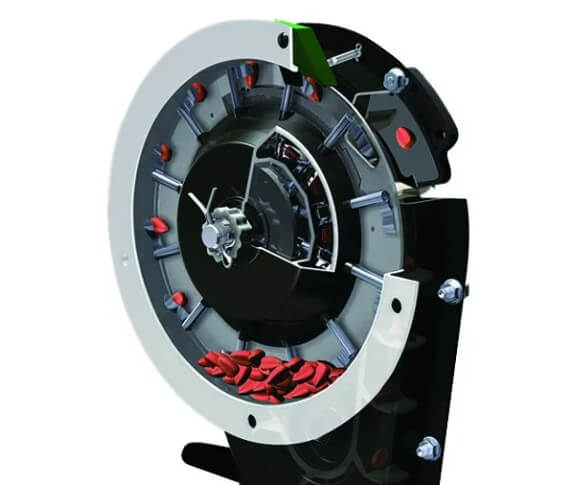
In addition, surface treatment technologies such as sandblasting are also widely used in the production of vulnerable parts such as planting drill bits. Through sandblasting, the surface roughness of the drill bit is improved, enhancing its cutting performance, while improving wear resistance and extending service life.
6.Summary
Through the implementation of the above processing paths, the production technology of precision planting parts will be significantly improved, meeting the needs of modern agricultural production, and also promoting the widespread application and sustainable development of precision planting technology.