Analysis of black anodized aluminum process: from principle to application
Are you curious about those black metal products with a deep appearance and unique texture?
The surface treatment technology behind them is black anodized aluminum. This technology not only changes the appearance of aluminum, but also gives it many excellent properties. This article will give you an in-depth understanding of the definition, production process, process selection, advantages and disadvantages, and application analysis of black anodized aluminum.
1.Definition of black anodized aluminum
Black anodized aluminum refers to an aluminum material that generates an aluminum oxide film on the aluminum surface through an anodizing process and is dyed black through an electrolytic coloring process. This film is dense and has high hardness, wear resistance, fire resistance and corrosion resistance. It can effectively prevent further oxidation of aluminum. It has the dual characteristics of decoration and protection. It is widely used in architectural decoration, home appliances, lamps, precision Instruments and other fields.
2.Is black oxidation of aluminum the same as black anodized aluminum?
Black anodized aluminum and natural oxidation of aluminum are two different metal surface treatment processes, with significant differences in many aspects:
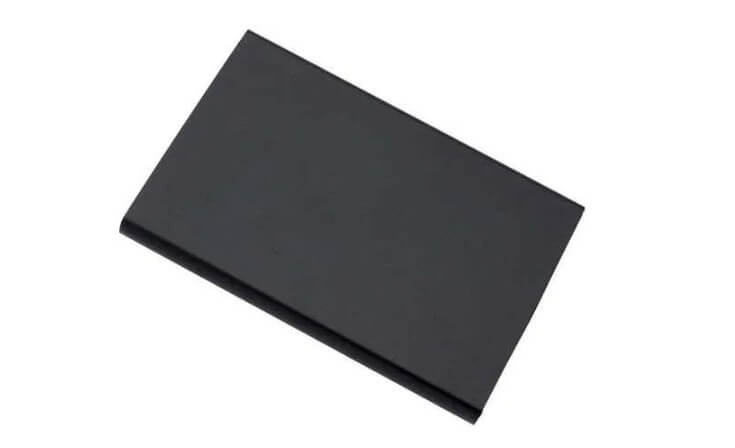
(1) Process principle:
1) Black anodized aluminum: Through the principle of electrochemistry, an aluminum oxide film is formed on the surface of aluminum and aluminum alloys, and then dyed and sealed to make it appear black.
2) Natural blackening of aluminum: Usually due to long-term exposure of aluminum to the air, an oxide film naturally forms on the surface, causing the aluminum surface to gradually darken.
(2) Film layer characteristics:
1) Black anodized aluminum: The generated oxide film layer is thicker, has excellent wear resistance and corrosion resistance, and the color is uniform and long-lasting.
2) Natural blackening of aluminum: The naturally formed oxide film layer is thin, the anti-corrosion performance is relatively weak, and the color change is uneven.
(3) Application scenarios:
1) Black anodized aluminum: widely used in aluminum alloy products with high requirements on appearance and protective performance, such as electronic product casings, decorative parts, etc.
2) Natural blackening of aluminum: It is more common in aluminum products that do not have high requirements for appearance, or is a surface effect naturally formed in certain specific environments.
(4) Controllability:
1) Black anodized aluminum: The process parameters are controllable and the required film thickness and color can be obtained.
2) Aluminum naturally turns black: the process is difficult to control, and the color and film quality are greatly affected by the environment.
3.The production process of black anodized aluminum
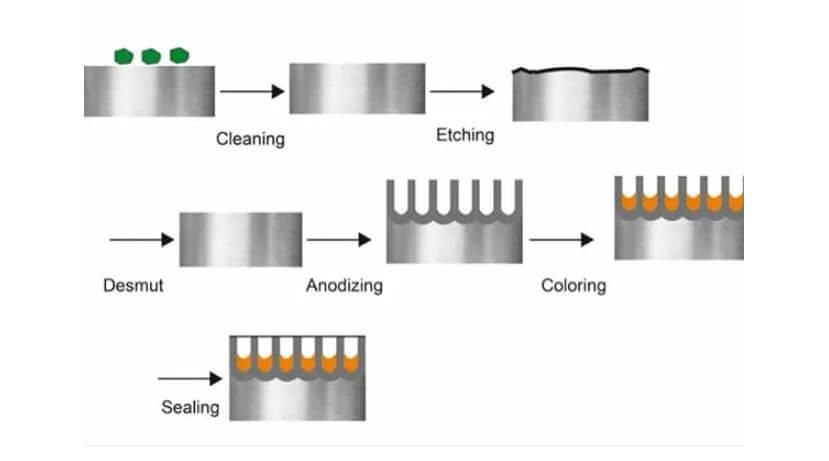
(1) Pretreatment
1) Surface cleaning:
First, the surface of the aluminum needs to be cleaned to remove oil, dust and other impurities. Organic solvents or alkaline cleaning agents are usually used for cleaning to ensure that the surface is clean and free of contamination.
2) Washing:
After cleaning, rinse the aluminum thoroughly with clean water to ensure there are no residual cleaning agents.
3) Pickling:
Then pickling is carried out, usually using a sulfuric acid solution, to remove the oxide layer and slight corrosion on the surface of the aluminum material. This step requires strict control of time and acid concentration to prevent excessive corrosion.
(2) Anodizing
1) Electrolyte preparation:
Aluminum is used as an anode and placed in an electrolytic bath containing sulfuric acid or other electrolytes. The composition and concentration of the electrolyte are crucial to the quality of the oxide film.
2) Power on processing:
An aluminum alloy workpiece is used as an anode, and electrical treatment is carried out in an electrolyte solution. During the electrolysis process, the aluminum on the anode is oxidized to form a porous aluminum oxide film. Electrolysis parameters such as voltage, current density, temperature and time need to be strictly controlled to ensure the quality and thickness of the oxide film.
3) Generate oxide film:
During the electrolysis process, the hydroxide ions in the water release electrons at the anode to become water and new ecological oxygen, oxidizing aluminum into a thick aluminum oxide film. This membrane is porous and provides a good foundation for subsequent dyeing.
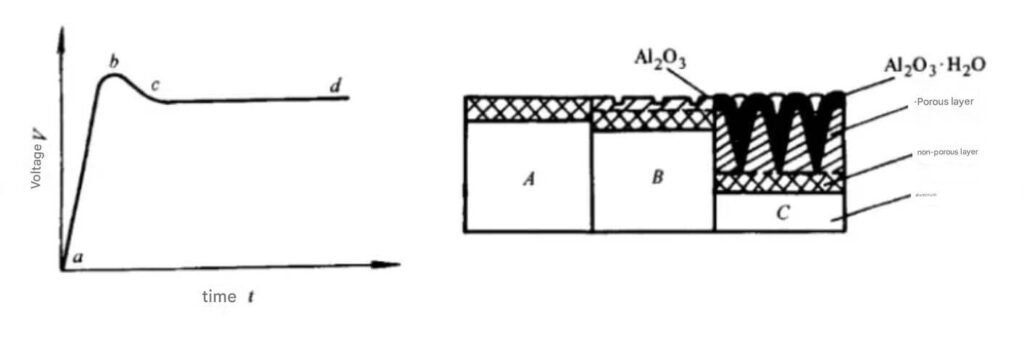
.
Schematic diagram of anodizing characteristic curve and oxide film growth process
.
(3) Dyeing
1) Dye selection:
Choose a dye suitable for forming a black oxide film. Commonly used dyes include black organic dyes or metal salts. Black organic dyes are typically used in more decorative applications, while metallic salts are used where greater weather resistance is required.
2) Dyeing process:
The anodized aluminum alloy workpiece is immersed in the dye, allowing the dye to penetrate into the porous structure inside the oxide film. By controlling the dyeing time and temperature, the depth and uniformity of the color can be adjusted.
(4) Closed pores
1) Closed processing:
After the dyeing is completed, the aluminum alloy surface needs to be sealed to improve the sealing and corrosion resistance of the oxide film. Sealing is usually done using hot water, steam or chromate solutions.
2) Cleaning and drying:
After the sealing process is completed, the workpiece is thoroughly cleaned to remove residual dye and sealer, and then dried to prevent moisture residue from causing corrosion.
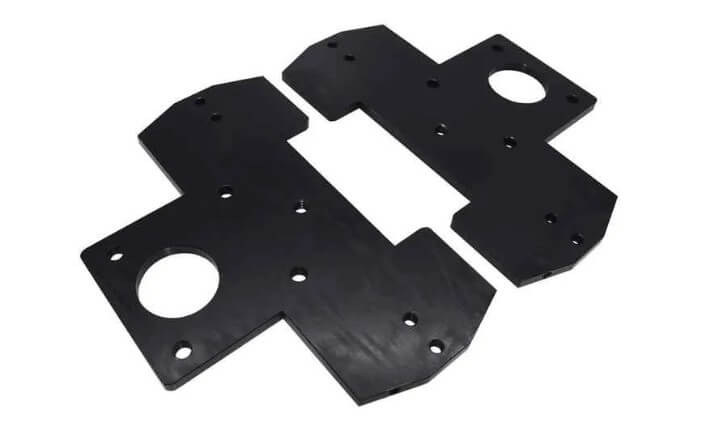
4.Classification of Anodizing and Which Type of Black Anodized Aluminum Is Most Suitable for?
(1) Sulfuric acid anodizing:
This is one of the most widely used anodizing methods. Using sulfuric acid as the electrolyte, the oxide film produced has high transparency, high hardness and good wear resistance, and is suitable for a variety of aluminum alloys. The film thickness is about 5-20 microns, easy to color, and suitable for decorative and functional needs.
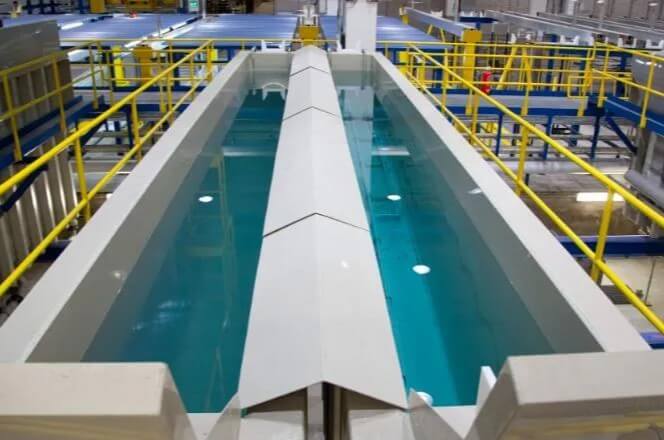
(2) Oxalic acid anodizing:
Using oxalic acid as the electrolyte, the oxide film generated is thick (up to 60 microns), transparent and yellow, with small porosity, high hardness and good corrosion resistance. Suitable for occasions requiring higher wear resistance and insulation.
(3) Chromic acid anodizing:
Using chromic acid as the electrolyte, the oxide film generated is thin (2-5 microns), opaque, and gray or milky white. Although the wear resistance is poor, the film layer is dense and the corrosion resistance is good, making it suitable for parts with higher fatigue performance requirements.
(4) Hard anodizing:
The oxide film generated by this method has extremely high hardness (HV300 or above), and the film thickness is generally 25-150 microns. It is suitable for engineering or military purposes and has excellent wear resistance and corrosion resistance.
(5) Phosphoric acid anodizing:
Using phosphoric acid as the electrolyte, the oxide film generated is porous, has larger pore size, and has better corrosion resistance, making it suitable for certain specific functional applications.
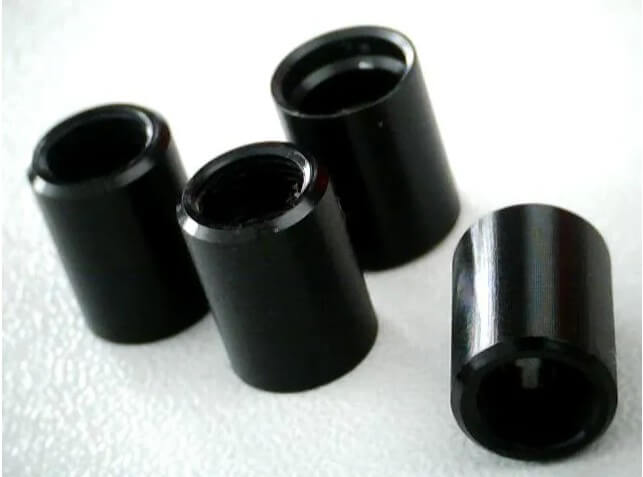
○ The most suitable type of black anodized aluminum:
For anodized aluminum that requires a black appearance, sulfuric acid anodizing is the most suitable type. Through the adsorption coloring method, black dye can be adsorbed in the film layer after sulfuric acid anodization to obtain a uniform and lasting black effect. In addition, the sulfuric acid anodized film has high transparency and can better display the color of the dye, making the black deeper and more uniform.
5.Analysis of the advantages and disadvantages of black anodized aluminum
(1) Advantages:
The black anodized aluminum plate has a bright surface and uniform color. It is highly decorative and can enhance the overall aesthetics of the product.
2) Strong wear resistance:
After anodizing treatment, a hard oxide film is formed on the surface of the aluminum plate, which greatly improves its wear resistance and makes it less likely to be scratched.
3) Good corrosion resistance:
The oxide film can effectively resist the erosion of general corrosive substances, allowing the aluminum plate to maintain stable performance in most environments.
4) Thermal emissivity
If metal parts are frequently dyed black, the thermal emissivity can be increased. This is common for radiator and satellite component applications.
5) Not easy to fade:
Black anodized aluminum panels do not discolor for a long time when used indoors and can maintain their beautiful appearance for a long time.
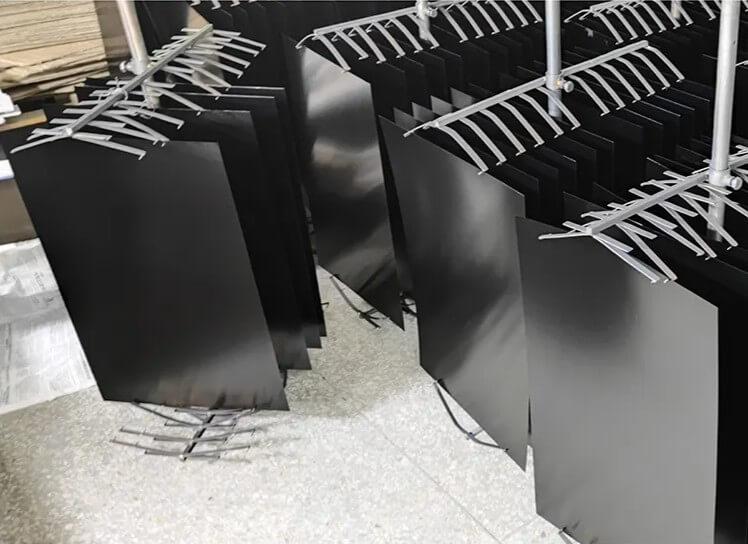
(2) Disadvantages
1) Limited materials
Not all aluminum materials are suitable for black coating, only some materials can, such as 5xxx, 6xxx and 7xxx aluminum series can be dyed black. Most commonly the 6xxx aluminum series is dyed black.
2) Surface cracking
In some cases, the surface of the aluminum will begin to crack. This happens during repeated thermal cycles and cracks occur due to the temperature difference between the substrate and the black coating.
6.Application of black anodized aluminum
(1) Aerospace industry:
Black anodized aluminum is commonly used in the aerospace industry to manufacture interior and exterior aircraft components. Its high hardness and corrosion resistance can not only extend the service life of parts, but also reduce the overall weight of the aircraft and improve fuel efficiency.
(2) Automobile industry:
In the automotive manufacturing industry, black anodized aluminum is used to make trim strips, wheel hubs and other components. Its wear resistance and aesthetics add a premium feel to the car, while its corrosion resistance ensures the stability of the components in various climate conditions.
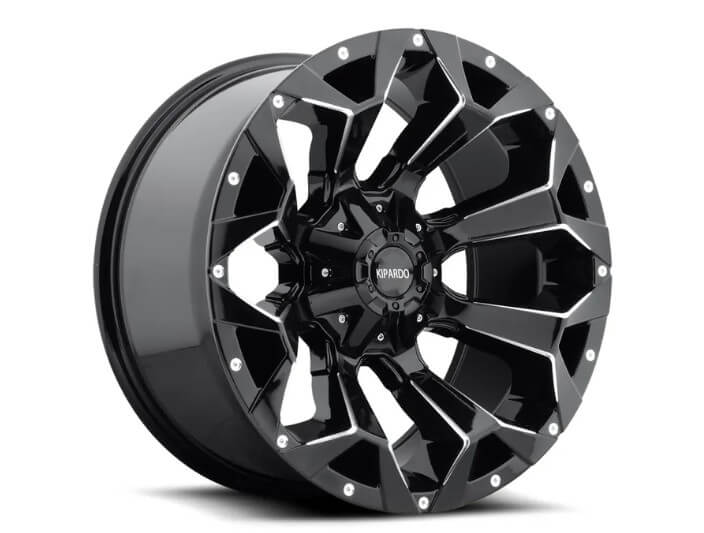
(3) Electronic products:
The casings of electronic products such as mobile phones and computers are often made of black anodized aluminum, which not only looks stylish, but also effectively prevents scratches and corrosion, improving the durability of the product.
(4) Architectural decoration:
In the field of construction, black anodized surfaces are often used as curtain walls, door and window frames and other materials because of their strong decorative properties and good weather resistance. They are both beautiful and durable.
(5) Medical tools and equipment
Surgical tools, walkers, wheelchairs, and oxygen tanks are all made with a black anodized finish. Anodized to form a sterilizable black coating with high chemical resistance.
(6) Optical equipment:
The application of black anodized aluminum in optical equipment mainly benefits from its good anti-reflective properties, and is often used to manufacture camera lenses, telescopes and other components.
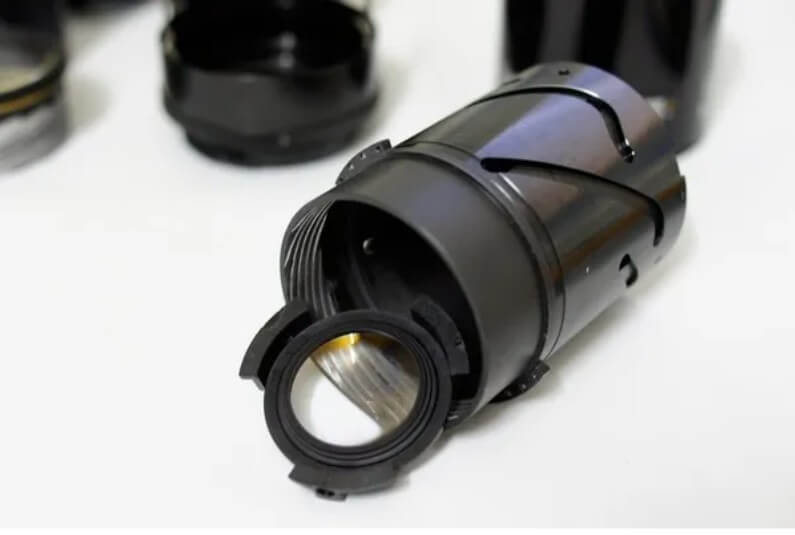
(7) Sports equipment:
Sports equipment such as golf clubs, bicycle frames, etc. are often made of black anodized aluminum, which not only improves the aesthetics of the product, but also enhances durability and impact resistance.
(8) Military and defense equipment
The hardness and heat dissipation of the black coating are excellent. Firearms, tactical equipment, and flashlights are common applications in military equipment.
7.Cost analysis of black anodized aluminum
Typically, black anodized aluminum will cost less than color anodized aluminum. The color surface treatment process is complex, requires multiple dyeing and sealing, takes a long time, and the cost of pigments and sealants is high. In contrast, the surface treatment process of black anodized aluminum is relatively simple. It mainly generates an oxide film through electrolytic oxidation and then dyes it. The pigment cost is low. Black anodized aluminum surfaces are more resistant to wear and corrosion than colored aluminum surfaces, and long-term maintenance costs may be lower.
8.Summary
Through the introduction of this article, I believe you have a deeper understanding of black anodized aluminum. The black surface treatment not only improves the appearance of the product, but also provides reliable performance guarantee. It has been widely used both in daily life and industrial production.