Panoramic analysis of arc anodizing: principles, characteristics, processes and applications
Arc anodizing is a technology that forms an oxide film on the metal surface through arc discharge and has a variety of excellent properties. This article will systematically analyze the principles, characteristics, process flow and application of arc anodizing in modern industry, with a view to providing a reference for the further promotion and application of this technology.
1.The difference between arc anodizing and anodizing
Arc anodizing and anodic oxidation are two advanced technologies commonly used for metal surface treatment. Although they are similar in purpose and application, there are significant differences in operating principles, film properties and application areas.
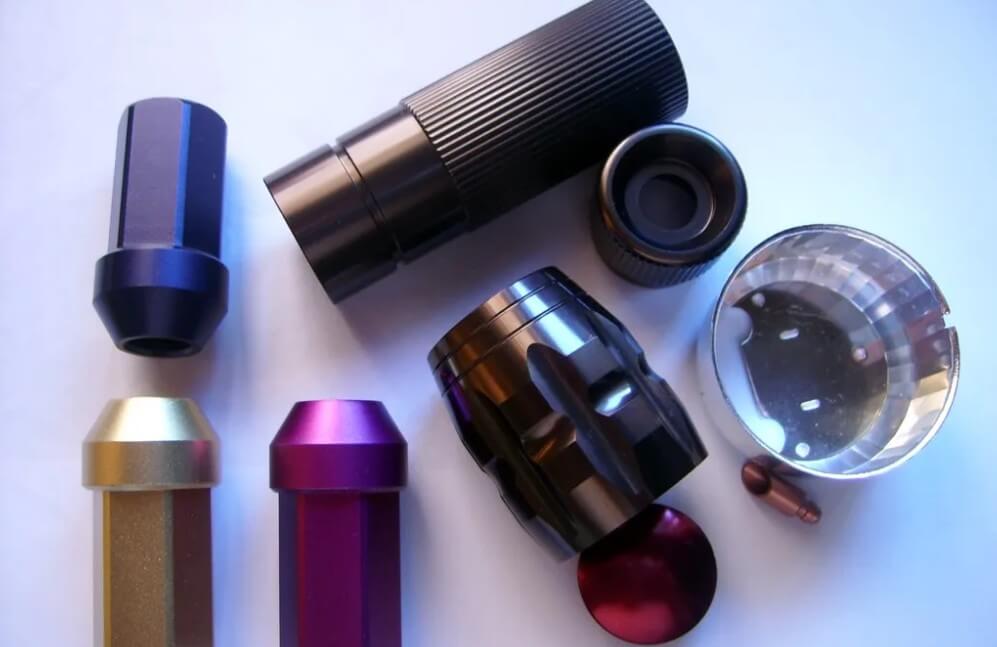
(1) Operating principle:
1) Anodizing
It is an electrochemical process in which a metal is placed in an electrolyte as an anode and direct current is applied to form an oxide film on its surface.
2) Arc anodizing
Also known as micro-arc oxidation, it is a technology developed on the basis of traditional anodizing. It uses higher voltage and more complex electrical parameters (such as AC or pulse current) to generate micro-arc discharge on the metal surface, thereby forming an oxide film.
(2) Electrolyte and working conditions:
1) Anodizing
It is usually carried out in acidic electrolyte, and the working voltage is low, generally around tens of volts.
2) Arc anodizing
It is carried out in a weakly alkaline electrolyte and requires a higher working voltage, which can reach several hundred volts.
(3) Oxide film formation process:
1) During the anodizing process, an oxide film is formed on the metal surface. This process is relatively mild and there is no obvious electrical breakdown.
2) Arc anodization will cause corona, glow, arc discharge and other phenomena to appear on the surface of the substrate, and the oxide film is formed by arc discharge.
(4) Film layer characteristics:
1) Anodizing:
The oxide film formed is relatively thin and has low hardness, but has good adsorption and insulation properties. The thickness of the film layer generally ranges from a few microns to dozens of microns.
2) Arc anodizing:
The formed film layer is thicker and harder, and has excellent wear resistance, corrosion resistance and electrical insulation. The film layer is usually composed of matrix metal oxide and electrolyte components, and has a dense structure and high toughness.
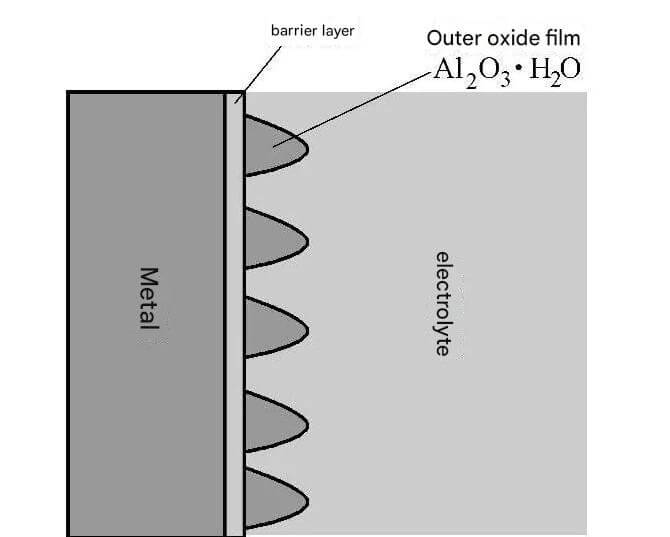
(5)Application fields:
1) Anodizing:
It is widely used in the surface treatment of metals such as aluminum alloys, magnesium alloys and titanium alloys to improve their corrosion resistance, hardness and wear resistance. Commonly used in the manufacture of architectural decoration, automotive parts and electronic products.
2) Arc anodizing:
Due to its superior film properties, it is mainly used in fields that require extremely high surface properties, such as aerospace, marine ships and high-end mechanical equipment. These application scenarios require materials with extremely high wear resistance and corrosion resistance.
(6) Processing speed:
1) Anodizing:
Processing is relatively slow, usually taking several hours.
2) Arc anodizing:
The processing speed is relatively fast and can usually be completed within tens of minutes.
2.Principle of arc anodizing
Arc anodization is an electrochemical process. Its basic principle is to use electrolysis to form an oxide film on the metal surface. Specifically, a metal is placed as an anode in an electrolyte, and high-voltage direct current is passed through to generate an arc discharge phenomenon on the surface of the anode, causing an oxidation reaction on the metal surface to form a dense and hard oxide film. This process not only involves electrochemical reactions, but is also accompanied by thermochemical reactions and plasma chemical reactions, so that the generated oxide film has a variety of excellent properties.
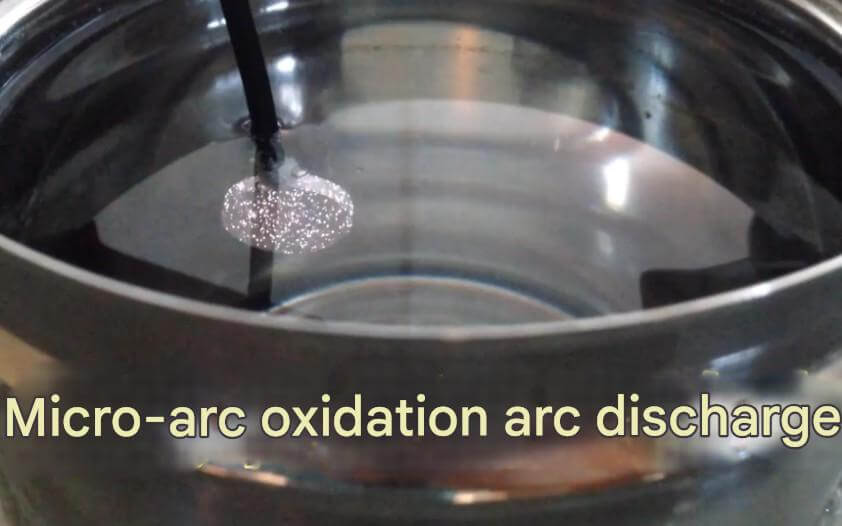
(1) Electrochemical reaction
In the electrolyte, the anode metal loses electrons and is oxidized, forming oxides. These oxides are deposited on the metal surface to form an oxide film. As the oxide film continues to thicken, the resistance of the film gradually increases, and the voltage also increases. When the voltage reaches a certain value, arc discharge will occur on the surface of the oxide film, causing the local temperature to rise sharply, further promoting the oxidation reaction.
(2) Thermochemical reaction
The high temperature generated by arc discharge will cause thermal decomposition of some materials in the oxide film to generate new oxides. These newly generated oxides combine with the original oxide film to form a denser and harder oxide film layer.
(3) Plasma chemical reaction
During the arc discharge process, water molecules in the electrolyte are decomposed into hydrogen ions and oxygen ions, and these ions form plasma under the action of the electric field. The active particles in the plasma react with the metal surface to generate new oxides, further enhancing the performance of the oxide film.
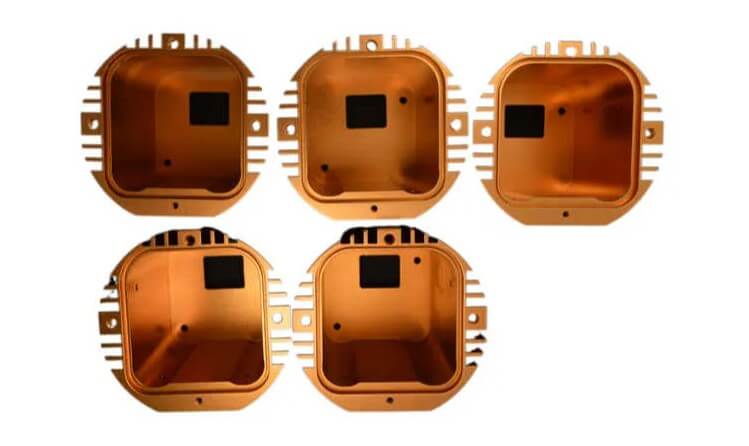
3.Characteristics of arc anodizing
(1) High hardness:
The hardness of the oxide film formed by arc anodization is much higher than that of traditional anodized films, and can even reach the hardness of ceramics. This gives arc anodizing technology significant advantages in the field of wear resistance.
(2) High thickness:
Arc anodizing can form a thicker oxide film, which can reach tens of microns or even hundreds of microns. This not only improves the material’s corrosion and wear resistance, but can also be used as an insulating layer in some special applications.
(3) High uniformity:
Since the high temperature generated by arc discharge instantly melts the aluminum surface, the oxide film is formed more uniformly and densely, reducing surface defects and unevenness.
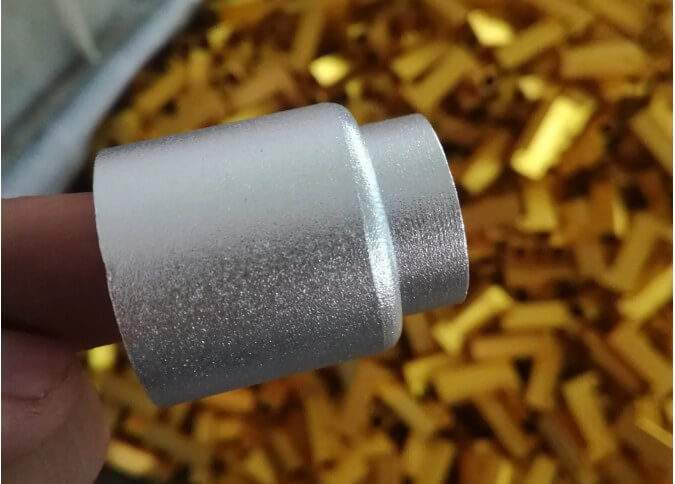
(4) Environmental protection:
The electrolyte used in the arc anodization process is usually an environmentally friendly solution, which reduces the emission of harmful substances and meets the environmental protection requirements of modern industry.
4.Application effect of arc anodizing
(1) Improve corrosion resistance:
The oxide film formed by arc anodization has high density and stability, which can effectively block the erosion of the substrate by water and corrosive media, and significantly improve the corrosion resistance of aluminum and its alloys.
(2) Improve wear resistance:
The arc anodized film has extremely high hardness and good wear resistance, which can significantly improve the wear resistance of aluminum and its alloys and extend their service life. Especially in the fields of mechanical parts, cutting tools and molds, the application effect of arc anodizing is particularly significant.
(3) Improve decoration:
By adjusting the composition and process parameters of the electrolyte, oxide films of different colors and textures can be prepared to improve the decorative properties of metals and are widely used in architectural decoration, furniture, electronic products and other fields.
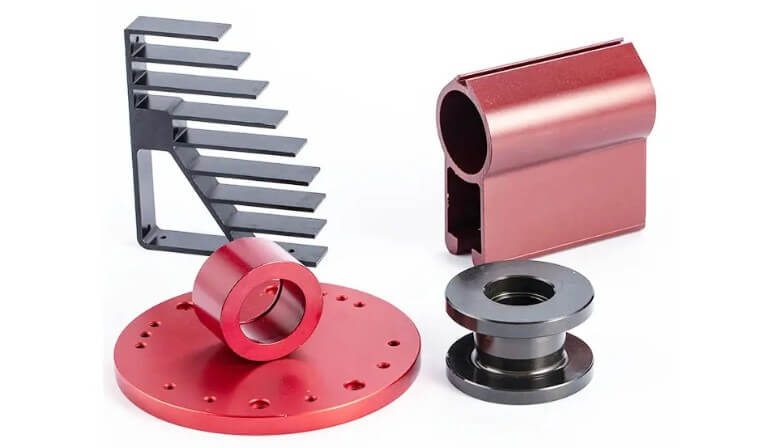
(4) Insulation performance:
Under certain conditions, arc anodized films can have good insulating properties and can be used to prepare insulating materials and electronic devices.
(5) Other applications:
In addition to the above applications, this process can also be used to prepare anti-counterfeiting signs, optical components and other fields.
5.Arc anodizing process
The process flow of arc anodizing mainly includes three steps: pre-treatment, anodizing and post-treatment:
(1) Pretreatment
Pretreatment is a key step to ensure the quality of anodizing, which mainly includes oil removal, rust removal, polishing and other processes. The purpose of these processes is to remove oil, rust spots and impurities from the metal surface, making the metal surface smooth and flat, in preparation for subsequent anodizing.
(2) Anodizing
The pre-treated metal is placed in the electrolyte as an anode, and high-voltage direct current is passed through to generate arc discharge on the anode surface and form an oxide film. The composition, concentration, temperature, current density, voltage and other parameters of the electrolyte have an important impact on the quality of the oxide film and need to be optimized according to specific materials and requirements.
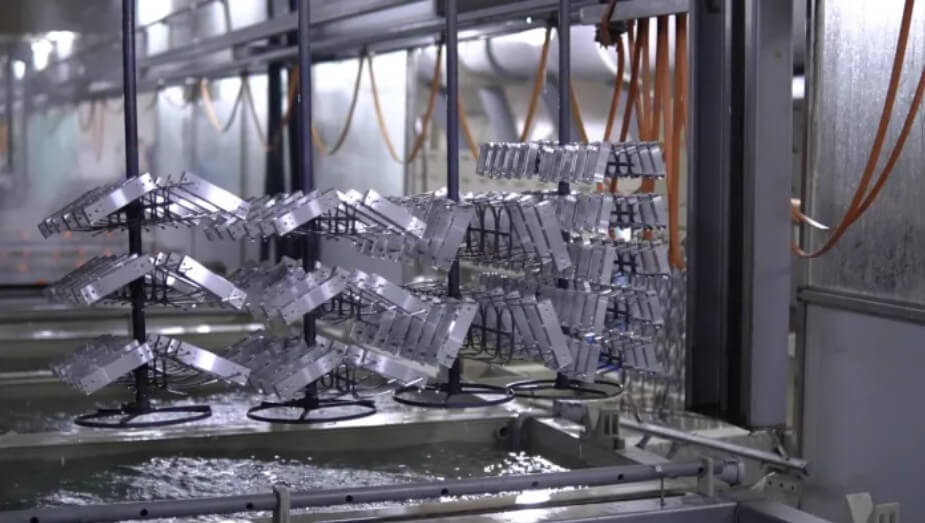
(3) Post-processing
Post-processing mainly includes sealing, dyeing, painting and other processes. The purpose of sealing is to close the pores in the oxide film and improve the protective performance of the film. Dyeing can make the oxide film show different colors to meet decorative requirements. Coating can apply an organic coating on the surface of the oxide film to further improve the corrosion resistance and wear resistance of the material.
6.Main application areas of arc anodizing
(1) Aerospace:
Arc anodizing is widely used in the aerospace field for surface treatment of aircraft structural parts and engine components. Because the oxide film it generates has extremely high corrosion resistance, wear resistance and anti-corrosion properties, it can effectively meet the use requirements of aviation materials in extreme environments and improve flight safety and component service life.
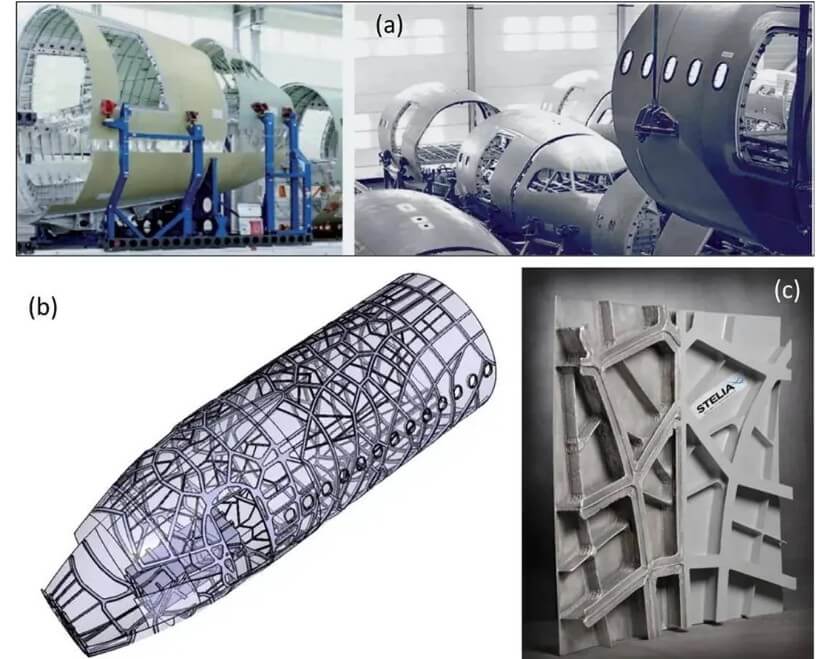
(2) Ocean ships:
In the field of marine ships, arc anodizing technology is mainly used for surface treatment of hull structures, decks and various types of marine engineering equipment. This technology significantly enhances the material’s resistance to seawater corrosion, extending the service life of ships and equipment while reducing maintenance costs.
(3) High-end machinery and equipment:
Arc anodizing plays an important role in the manufacturing of high-end machinery and equipment, such as precision machine tools, medical equipment, etc. Through this technological treatment, the parts of the equipment not only have increased hardness and wear resistance, but can also maintain stable performance in harsh environments such as high temperature and high pressure, ensuring long-term and efficient operation of the equipment.
7.Main problems and challenges faced by arc anodizing
(1) Process complexity and cost issues:
The arc anodizing process is relatively complex and involves multiple parameters such as voltage, current density, oxidation time, etc. These parameters need to be precisely controlled to ensure the quality of the oxide film.

In addition, equipment investment and maintenance costs are high, which limits its popularity among small and medium-sized enterprises. The growth rate of the oxide film is relatively slow, which also increases production time and cost.
(2) Film quality issues:
In some cases, the arc anodized coating may have problems such as excessive porosity and uneven hardness, affecting its performance. The quality of the film layer is affected by many factors, including the properties of the matrix material, pretreatment effect, process parameter control, etc. Therefore, improving the stability of film quality is a technical problem.
8.Summary
Arc anodizing technology has a significant effect in improving the performance of metal materials, and its application fields are also constantly expanding. In the future, the cost issues and film quality issues of this technology need to be solved, and it will play an important role in more fields.