How to 3D print brass: Challenges and optimization strategies
With the continuous development of 3D printing technology, brass 3D printing has gradually come into people’s view. This technology can not only greatly shorten the production cycle and reduce costs, but also realize the manufacture of complex structures.
So, how to 3D print brass? What technical challenges will brass encounter in the 3D printing process? How to overcome these challenges by optimizing the process? This article will start from these three aspects to explore in depth how to 3D print brass.
1.Characteristics of brass materials
Brass, composed of copper and zinc alloy, has excellent mechanical properties and corrosion resistance. This material is widely used in many fields because of its beautiful color and good processability.
Brass has a high hardness and is suitable for making various precision parts. At the same time, its corrosion resistance makes it stable in a humid environment, which is very suitable for outdoor decoration and building materials. In addition, brass also has good electrical and thermal conductivity, which makes it also play an important role in the manufacture of electrical and electronic equipment.
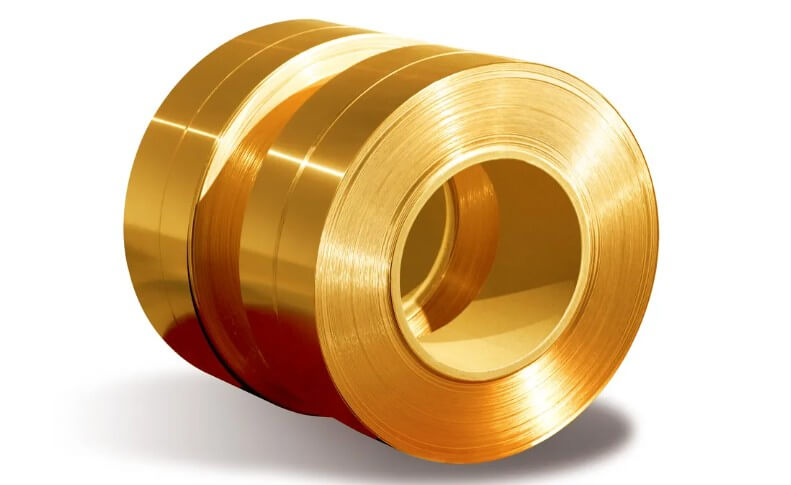
2.Technical Challenges of 3D Printing Brass
(1) Difficulties Caused by Material Properties:
Brass is composed of copper and zinc alloy. It has a low melting point and is easily oxidized during the 3D printing process, resulting in a decrease in the mechanical properties and surface quality of the printed parts. In addition, the high thermal conductivity of brass makes temperature control during printing particularly critical, and temperature fluctuations can affect printing accuracy and structural strength.
(2) Printing accuracy and deformation issues:
Brass materials have a high shrinkage rate and are prone to deformation during the cooling process, which affects the dimensional accuracy and shape consistency of the printed parts. In order to reduce deformation, it is necessary to optimize printing parameters such as layer thickness, printing speed and cooling method, and additional support structures may be required to stabilize the printed parts.
(3) Complex post-processing process:
3D printed brass parts usually require post-processing such as heat treatment, machining and surface treatment to improve their mechanical properties and appearance. Heat treatment can eliminate internal stress, but requires precise control of temperature and time to avoid excessive softening or oxidation. Machining is used to correct size and shape, while surface treatment can enhance corrosion resistance and aesthetics.
(4) Laser reflection problem of brass
The high laser reflectivity of brass is a major challenge in the 3D printing process. During the laser sintering or melting process, the brass material will reflect most of the laser energy, which not only affects the printing efficiency, but also may cause quality problems of the printed parts, such as surface roughness and loose internal structure.
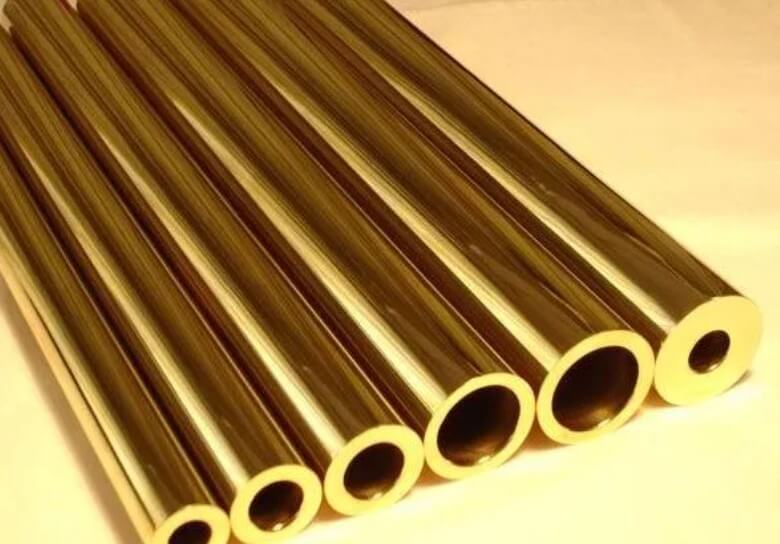
To solve this problem, it is usually necessary to adjust the laser parameters, such as laser power and scanning speed, and use special coatings to reduce the laser reflectivity. In addition, optimizing the particle size and morphology of brass powder can also increase the absorption rate of laser energy, thereby improving the printing quality.
Summary:
Brass 3D printing faces the above-mentioned challenges, but at the same time, the emergence of 3D printing technology has also provided more possibilities for the application of brass, which can be said to have more advantages than disadvantages, because these challenges have corresponding solutions. The following will introduce in detail how to 3D print brass, including material selection, printing technology, printing process, post-processing and other aspects.
3.How to 3D print brass——material selection
(1) Brass powder
Brass powder is the main material for 3D printing brass. Its particle size, purity and composition ratio have a significant impact on the printing effect. The commonly used brass powder particle size range is between 15-53 microns.
The smaller the particle size, the higher the printing accuracy, but the printing speed will be reduced accordingly. In terms of purity, high-purity brass powder (such as 85% copper content and 15% zinc content) can provide better mechanical properties and surface finish.
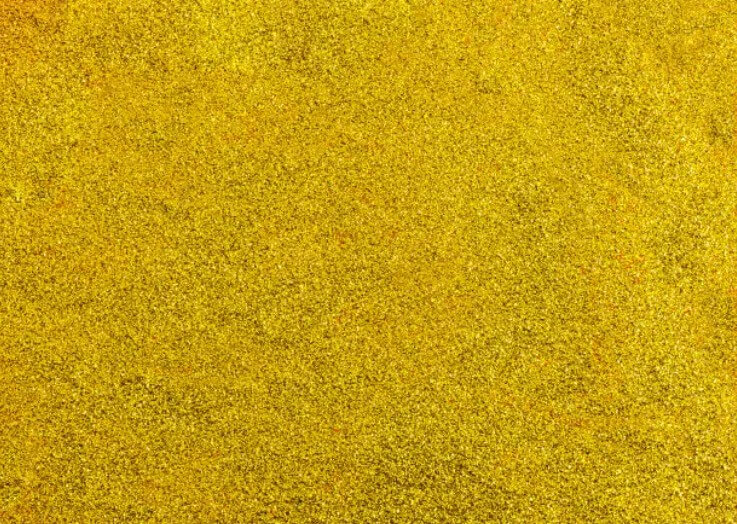
(2) Print bed material
The selection of print bed material is equally important because it needs to withstand high temperatures and prevent brass from adhering. Commonly used print bed materials are stainless steel, ceramic and graphite.
Stainless steel print beds are low in cost, but brass is easily adhered. Ceramic print beds are resistant to high temperatures and not easy to adhere, but they are expensive. Graphite print beds have both high temperature resistance and low adhesion characteristics, but need to be replaced regularly.
(3) Auxiliary materials
In addition to brass powder and print bed materials, some auxiliary materials are also required, such as degreasers, adhesives, etc. Degreasing agent is used to remove grease and impurities on the surface of the printed part, while the binder is used to enhance the adhesion between brass powders, thereby improving the strength and precision of the printed part.
4.How to 3D print brass——Printing technology
How to 3D print brass? The choice of 3D printing technology is an important part of it. The following will introduce three main technologies:
(1) Selective laser melting (SLM)
Selective laser melting is one of the most commonly used brass 3D printing technologies. This technology uses a high-power laser beam to melt brass powder layer by layer to form a dense metal structure.
The advantages of SLM technology are high printing accuracy, good surface finish, and excellent mechanical properties. However, its disadvantages are slow printing speed, high cost, and the need for professional equipment and operating skills.
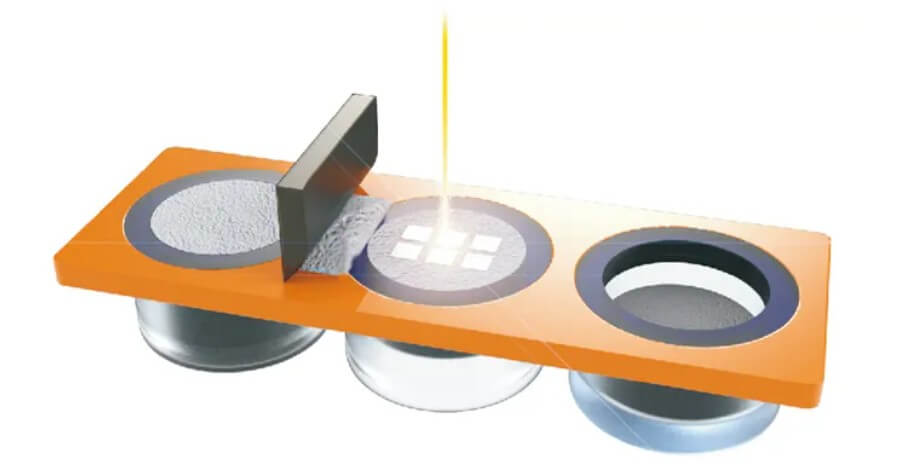
(2) Electron beam melting (EBM)
Electron beam melting technology uses electron beams instead of laser beams for melting. Compared with SLM technology, EBM technology is carried out in a vacuum environment, which can effectively reduce oxidation and improve the purity and performance of printed parts.
In addition, EBM technology has a faster printing speed, but the equipment cost is also higher, and the accuracy and surface finish of the printed parts are slightly inferior to SLM technology.
(3) Laser Metal Deposition (LMD)
Laser metal deposition technology sprays brass powder into a laser molten pool for melting and deposition, and then accumulates layer by layer to form a printed part.
The advantages of this technology are fast printing speed, high material utilization rate, and the ability to perform repair and additive manufacturing. However, its disadvantages are low printing accuracy and surface finish, which require post-processing.
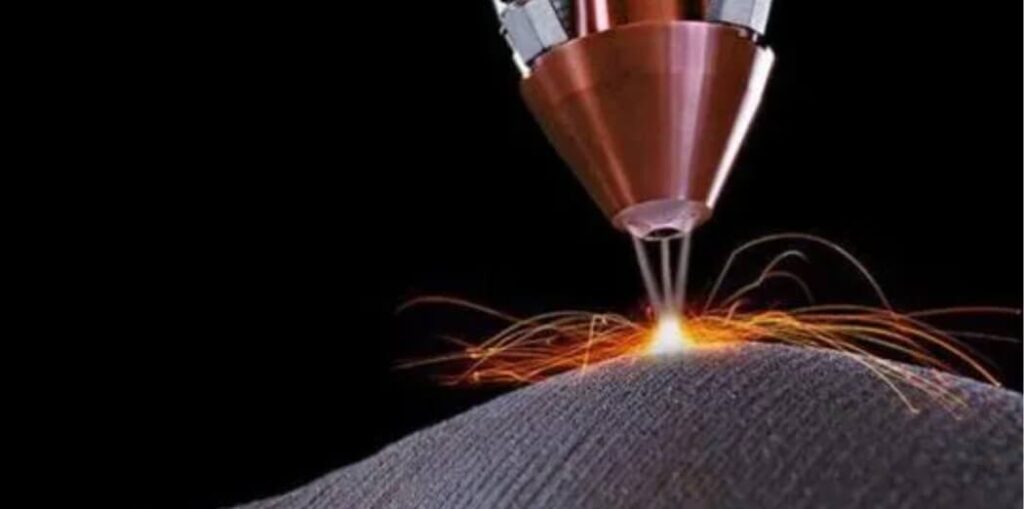
5.How to 3D print brass——Preparation before printing
(1) CAD modeling
How to 3D print brass? First, you need to use computer-aided design (CAD) software to design the required brass part model. The design of the model should take into account the structural strength, dimensional accuracy, and support structure of the printed part during the printing process.
The support structure is a part temporarily added during the printing process to support overhanging parts and complex structures to ensure the smooth progress of the printing process.
(2) Slicing
After designing the model, you need to use slicing software to cut the model into thin slices so that the 3D printer can print layer by layer. The slicing software can set printing parameters such as layer thickness, laser power, scanning speed, etc. The settings of these parameters have an important impact on the printing effect.
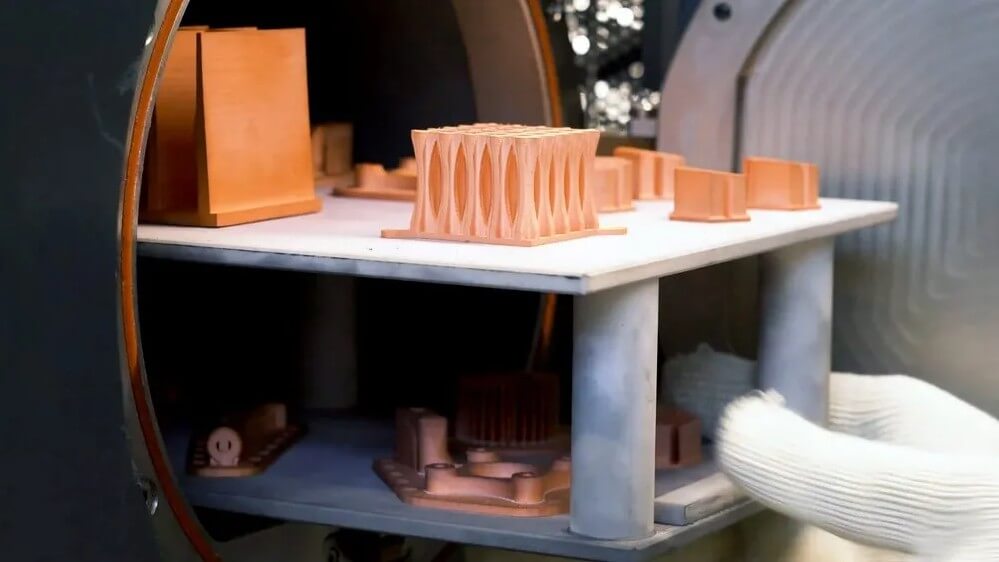
Generally speaking, the smaller the layer thickness, the higher the printing accuracy, but the printing time will increase accordingly. The laser power and scanning speed need to be optimized according to the characteristics of the brass powder and the printing equipment to ensure that each layer can be fully melted without defects.
(3) Print bed preparation
Before printing, the print bed needs to be prepared. First, heat the print bed to an appropriate temperature (generally between 150-200℃) to reduce thermal stress and prevent deformation of the printed part.
Second, apply a layer of degreaser on the print bed to remove grease and impurities on the surface. Finally, spread the brass powder evenly on the print bed and prepare for printing.
6.How to 3D print brass——printing process
(1) SLM printing process
During the SLM printing process, a high-power laser beam melts the brass powder layer by layer according to the path generated by the slicing software. After each layer is melted, the printing platform drops one layer of thickness, continues to spread the powder and melt, and repeats until the printing is completed. During the printing process, it is necessary to monitor the printing status in real time and adjust the printing parameters in time to ensure the printing quality.
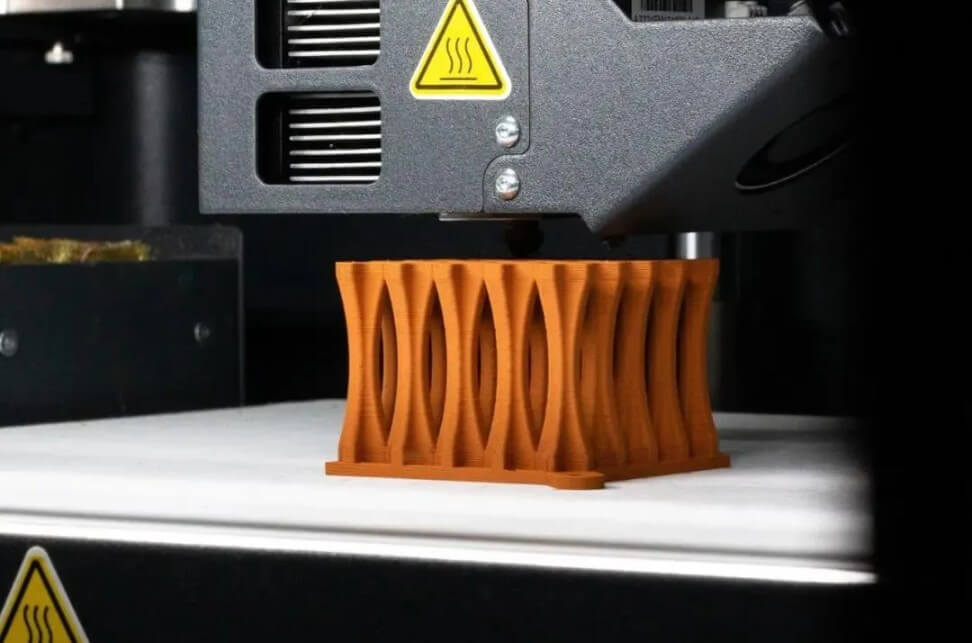
(2) EBM printing process
The EBM printing process is similar to SLM, but uses an electron beam instead of a laser beam. Electron beams melt in a vacuum environment, which can effectively reduce oxidation and improve the purity and performance of printed parts. During the printing process, it is also necessary to monitor the printing status in real time and adjust the printing parameters.
(3) LMD printing process
During the LMD printing process, the laser beam sprays brass powder into the molten pool for melting and deposition, and then accumulates layer by layer to form a printed part. During the printing process, it is necessary to control the amount of powder sprayed and the laser power to ensure that each layer can be fully melted without defects.
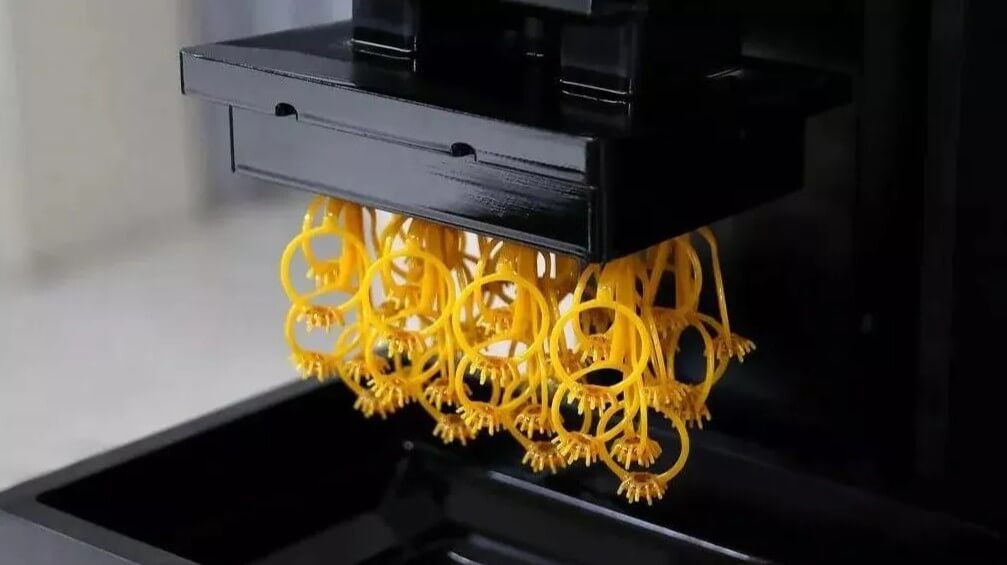
7.How to 3D print brass——post processing
(1) Removal of support structure
After printing, the support structure on the printed part needs to be removed. Common removal methods include machining, heat treatment and chemical corrosion.
Mechanical processing is suitable for cases where the support structure is relatively simple; heat treatment can soften or melt the support structure by heating, making it easier to remove; chemical corrosion is suitable for removing support structures of complex structures, but it is necessary to control the corrosion time and solution concentration to avoid damage to the printed part.
(2) Surface treatment
After removing the support structure, the printed part needs to be surface treated to improve its surface finish and performance. Common surface treatment methods include grinding, polishing, and electroplating.
Grinding and polishing can remove the rough parts of the surface and improve the surface finish; electroplating can form a protective film on the surface to improve corrosion resistance and aesthetics.
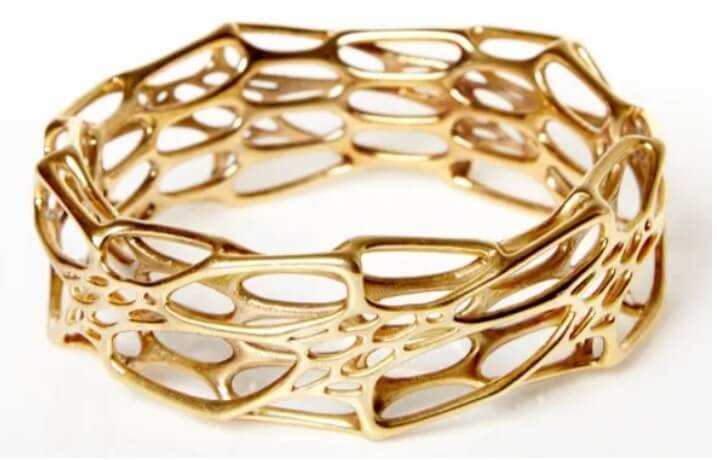
(3) Heat treatment
Heat treatment is an important step to improve the mechanical properties of brass 3D printed parts. Through appropriate heat treatment processes, the internal stress during the printing process can be eliminated and the strength and toughness of the printed part can be improved. Common heat treatment methods include solution treatment and aging treatment.
Solution treatment is to heat the printed part to a high temperature (generally between 800-950℃), keep it warm for a period of time, and then quickly cool it to form a supersaturated solid solution. Aging treatment is to heat the printed part to a lower temperature (generally between 150-300℃) after solution treatment, and keep it warm for a period of time to precipitate the strengthening phase and improve the mechanical properties.
8.Summary
Facing the various challenges of brass 3D printing, we can significantly improve the printing effect and efficiency through reasonable optimization strategies. I believe that through the analysis of this article, you already know how to 3D print brass? And have a certain understanding of the material selection, process flow, technology and post-processing process of 3D printing brass. Mastering the optimization strategy will enable you to go further on the road of brass 3D printing.
1 Comment