Camshaft parts processing technology based on CNC technology
As one of the key components of the engine, the processing accuracy and efficiency of camshaft parts directly affect the overall performance of the engine. Based on CNC technology, this paper discusses the processing technology of camshaft parts, including part drawing analysis, blank selection, process route planning, machine tool and process equipment selection, cutting amount determination and program compilation.
1.Basic overview of CNC machining camshaft parts
Camshafts are important parts in internal combustion engines, mainly used to drive valves, oil pumps and other components. Their accuracy and surface quality play a vital role in the performance and life of the engine. With the development of CNC technology, CNC machining has become the mainstream method for manufacturing camshaft parts, which has the advantages of high precision, high efficiency and high flexibility. Next, the processing technology of camshaft parts will be discussed in detail from the perspective of CNC machining.
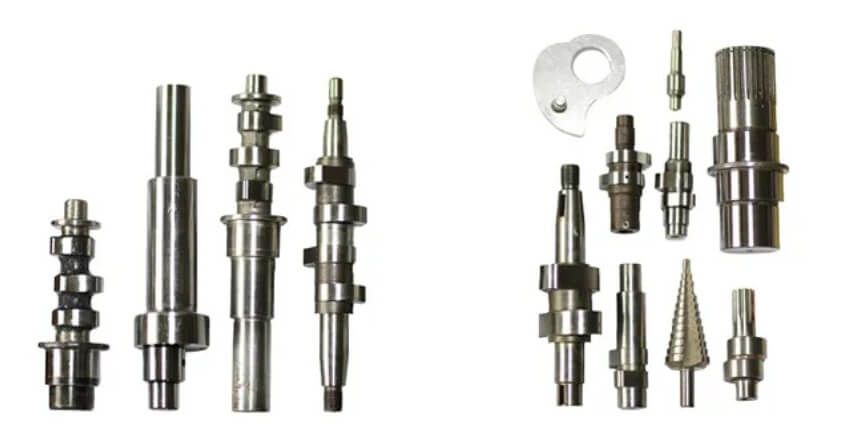
2.Camshaft parts drawing analysis
(1) Parts material and its mechanical properties
Camshaft materials are usually made of 45 steel, which is a high-quality carbon structural steel. After quenching and tempering, 45 steel has good comprehensive mechanical properties, including high strength and hardness, and is suitable for manufacturing important parts that bear alternating loads. Its mechanical properties include tensile strength, yield strength, elongation, etc. These properties directly affect the selection of processing technology and the setting of cutting parameters.
(2) Structural process analysis of parts
Camshaft parts are mainly composed of cylindrical surfaces, end faces, step surfaces, threads, arcs, etc. Its processing accuracy and surface roughness requirements are high, especially the coaxiality between the cylindrical surfaces, the dimensional accuracy and surface roughness of the cam profile, etc. The structural process analysis shows that the part belongs to a short shaft with a stepped structure and is suitable for processing by CNC lathes.
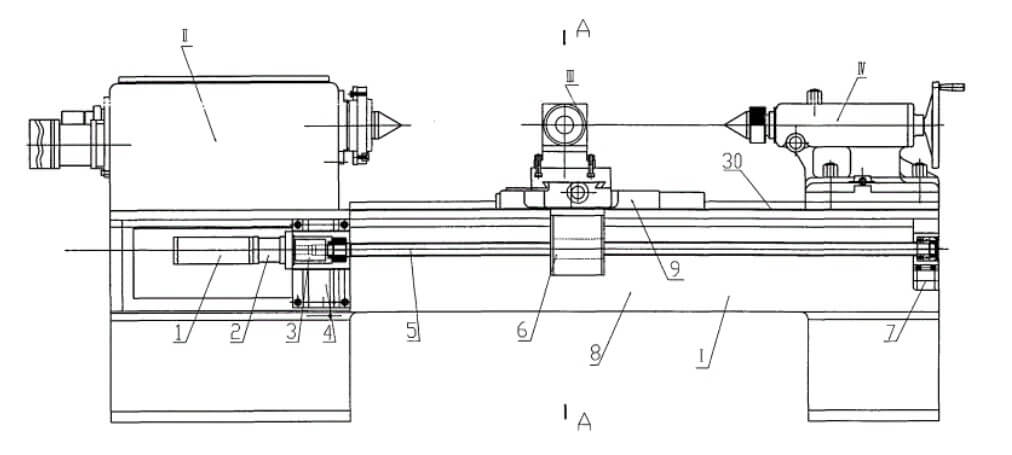
3.Analysis of the blank of camshaft parts
(1) Selection of blanks
According to the characteristics of camshaft parts, it is crucial to select the appropriate blank type. Common blank types include castings, forgings, weldments and profiles. For medium and small camshafts, hot-rolled round steel is usually selected as the blank material. 45 steel has good cutting performance and is suitable for CNC processing.
(2) Design of blank drawing
The blank drawing design needs to consider the machining allowance and dimensional accuracy. By consulting relevant manuals, determine the reasonable blank size, including length and diameter, to ensure sufficient allowance during processing and avoid material waste.
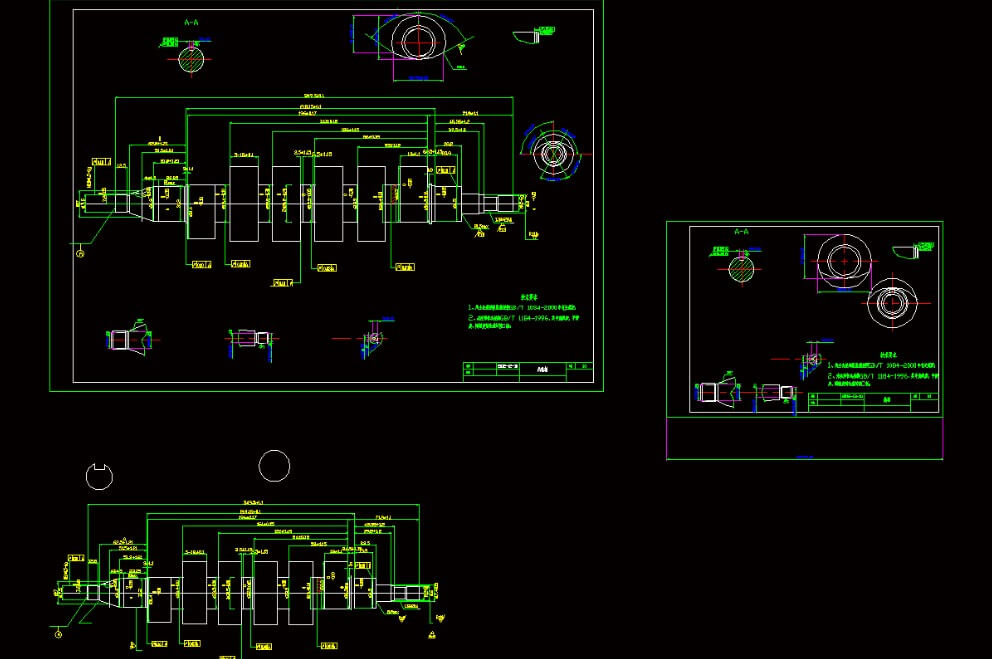
4.Drafting of the processing route for camshaft parts
(1) Selection of positioning datum
The selection of positioning datum is one of the key steps in drafting the process route. The rough datum usually uses the unprocessed surface on the blank, while the fine datum uses the processed surface. When selecting the fine datum, the principles of datum coincidence and datum unification should be followed to ensure processing accuracy and efficiency.
(2) Selection of processing method
The processing methods of camshaft parts mainly include turning, milling, grinding, etc. Turning is mainly used to process cylindrical surfaces, end faces and threads, milling is used to process cam profiles, and grinding is used to improve surface accuracy and roughness. According to the structural characteristics and accuracy requirements of the parts, select the appropriate processing method.
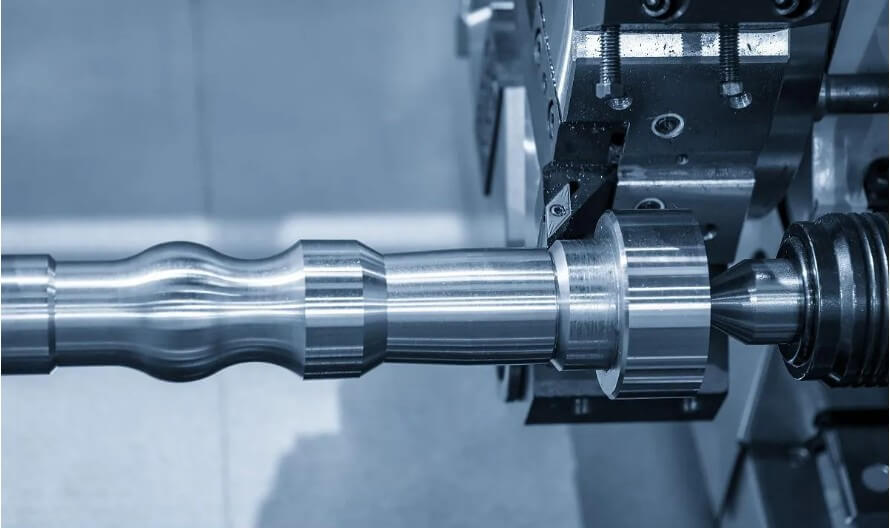
5.Arrangement of the processing sequence of camshaft parts
The arrangement of the processing sequence should follow the principle of roughing first and then fine, primary first and then secondary, and surface first and then hole. First, rough machining is performed to remove most of the excess, and then semi-finishing and finishing are performed to gradually improve the accuracy and surface quality of the parts.
6.Determination of machining allowance and process size of camshaft parts
(1) Machining allowance
Machining allowance refers to the thickness of the material layer removed in each process to achieve the final size of the part. Reasonable determination of machining allowance can reduce machining time and material consumption and improve production efficiency. The determination of machining allowance needs to consider factors such as material properties, machining methods, and machine tool accuracy.
(2) Process size
Process size refers to the size that the part should reach after each process. The determination of process size needs to consider factors such as machining allowance and tolerance to ensure that the final part meets the design requirements.
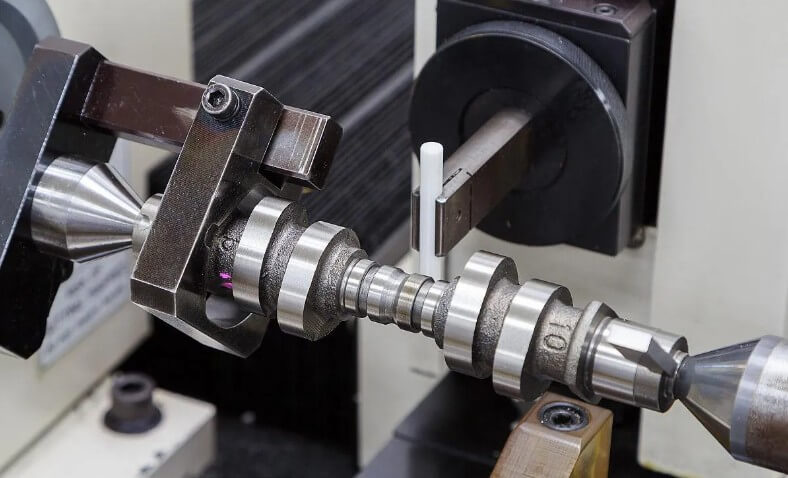
7.Selection of machine tools and process equipment
(1) Selection of machine tools
CNC lathes are the main equipment for camshaft parts processing. When selecting machine tools, factors such as machine tool accuracy, rigidity, and degree of automation should be considered. High-precision CNC lathes can ensure the machining accuracy and surface quality of parts and improve production efficiency.
(2) Selection of fixtures
The fixture is used to position and clamp the workpiece. Its selection should take into account the structural characteristics of the workpiece, the requirements for machining accuracy, and other factors. Common fixtures include three-jaw chucks, four-jaw chucks, and special fixtures.
(3) Selection of tools
The selection of tools directly affects the machining efficiency and surface quality. According to the machining materials and process requirements, select appropriate tool materials and tool types, including turning tools, milling cutters, drill bits, etc.
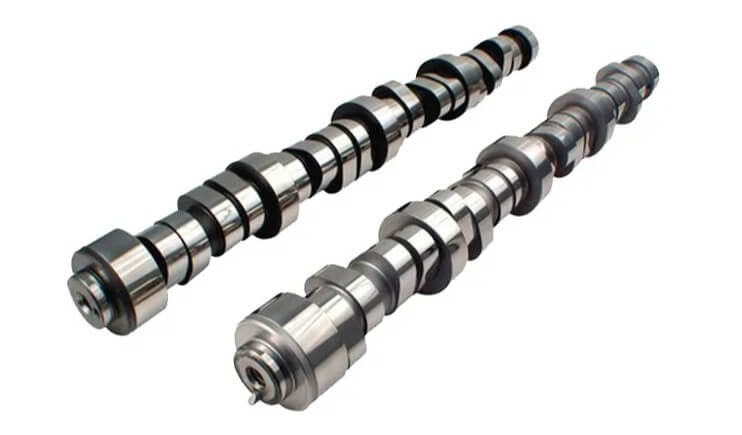
8.Selection of cutting parameters for machining camshaft parts
(1) Cutting parameters for rough machining
Cutting speed: Generally selected at 80-120 m/min, adjusted appropriately according to the tool material and camshaft material.
Feed rate: Take 0.2-0.4 mm/rev to ensure a high metal removal rate.
Cutting depth: According to the camshaft blank allowance, 2-4 mm is usually selected for layered cutting.
(2) Cutting parameters for semi-finishing
Cutting speed: Increase to 100-150 m/min to improve the machining surface quality.
Feed rate: Reduce to 0.1-0.2 mm/rev to ensure machining accuracy.
Cutting depth: Reduce to 1-2 mm to further remove material.
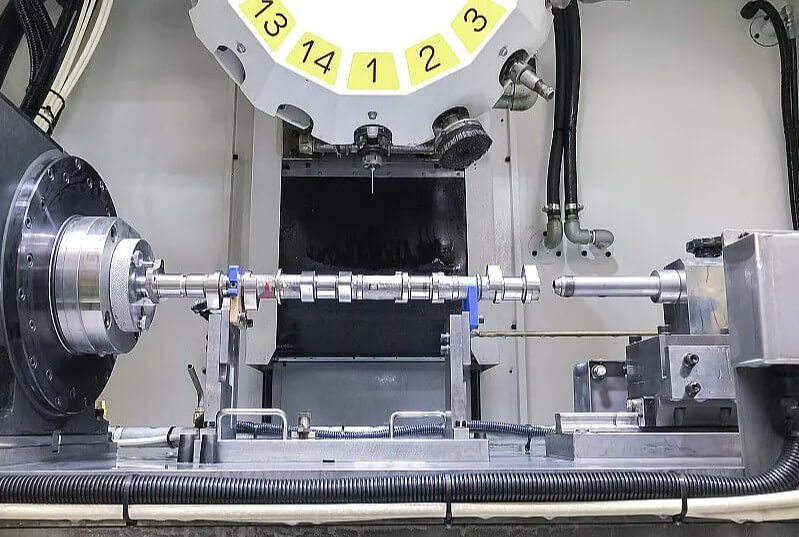
(3) Finishing cutting amount
Cutting speed: Can be further increased to 150-200 m/min, using high-performance tools.
Feed rate: Take 0.05-0.1 mm/rev to ensure surface roughness requirements.
Cutting depth: Usually choose 0.5-1 mm for fine machining.
9.Programming
CNC machining program is the key to achieving automated machining. Programming includes process analysis, tool path planning, code generation and other steps. Using CNC programming software, machining programs can be quickly generated and simulated to ensure the correctness and feasibility of the program.
10.Conclusion
The camshaft parts machining process based on CNC technology can achieve high-precision and high-efficiency machining through reasonable part drawing analysis, blank selection, process route planning, machine tool and process equipment selection, cutting amount determination and program compilation.
CNC machining technology is widely used in the manufacturing of automotive parts, mainly including engine cylinders, chassis parts, tire valve stems and other parts. The application of this technology not only improves the processing quality of automotive parts, but also shortens the production cycle and reduces production costs, and has important practical application value.