CNC machining center: In-depth analysis of machining technology
CNC machining center controls the movement and operation of machine tools through computer numerical control system (CNC system) to achieve high-precision and high-efficiency machining. Its core lies in converting design drawings into digital instructions to drive machine tools to complete cutting, drilling, milling and other operations.
This article will discuss in detail the definition, composition, machining process, machining route selection, advantages and parts that can be processed of CNC machining center.
1.Overview of CNC machining center
CNC machining center is an advanced machine tool that integrates multidisciplinary technologies such as computer, automatic control and precision measurement. It controls the movement and machining process of the machine tool through digital signals, can perform multi-step machining on the workpiece, and is equipped with a tool magazine to realize automatic tool change. CNC machining center mainly consists of the following parts:
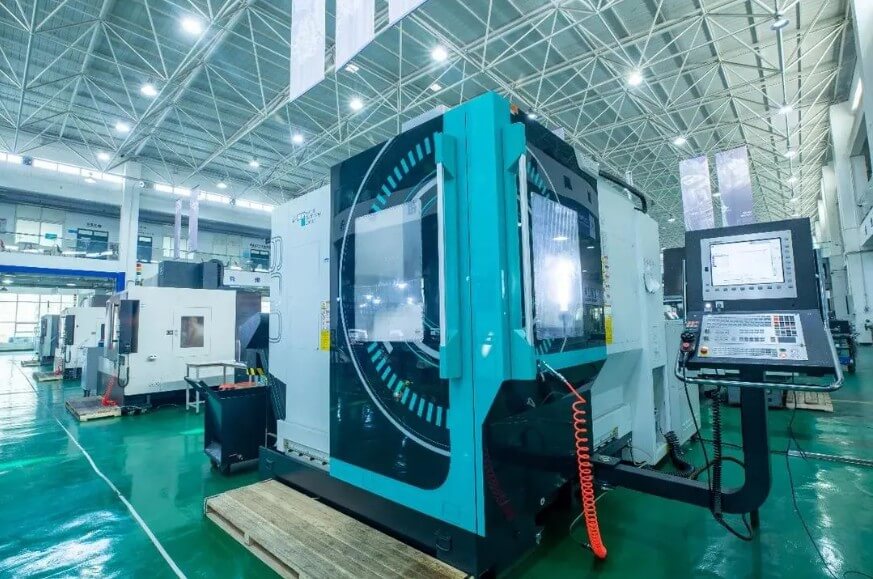
(1) CNC system:
As the core of the entire machine tool, it is responsible for receiving and processing various instructions and controlling the movement of the machine tool.
(2) Servo drive system:
Convert the instructions issued by the CNC system into actual mechanical movement and drive the machine tool axes to move precisely.
(3) Tool magazine:
Stores a variety of tools, and the automatic tool change function improves processing efficiency.
(4) Cooling system:
Used to cool tools and workpieces, reduce thermal deformation and extend tool life.
(5) Machine tool body:
Includes the basic components of the machine tool, such as the bed, column, spindle, etc., which are the mechanical part of the machine tool and are responsible for bearing various forces and completing various movements.
(6) Measurement feedback system:
Real-time monitoring of the movement status of the machine tool, and feedback of information to the CNC system to ensure processing accuracy.
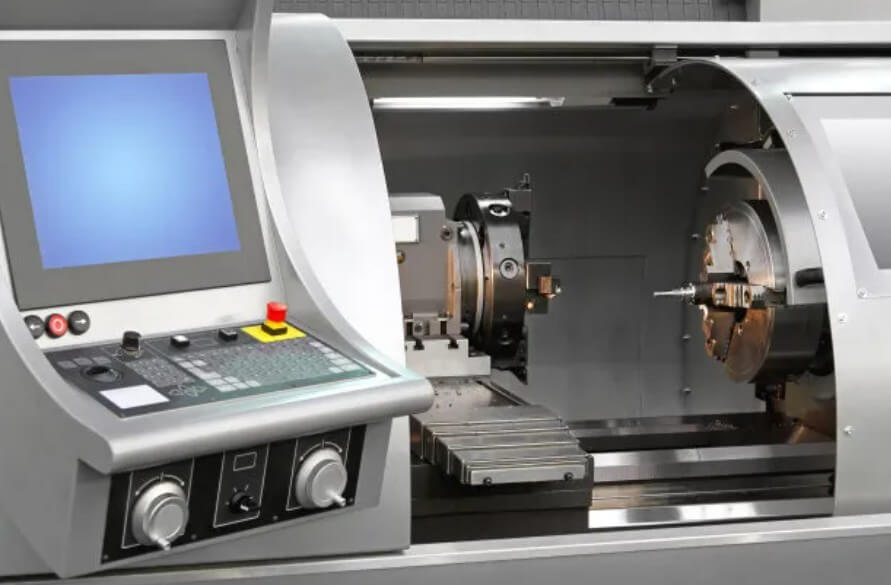
2.Workflow of CNC machining center
(1) Design drawings and programming:
Use CAD software to design parts, and generate machining programs (G code) through CAM software.
(2) Program input:
Input the machining program into the CNC system, the system parses the instructions and prepares to execute.
(3) Workpiece clamping:
Fix the workpiece on the workbench to ensure accurate positioning.
(4) Tool selection and clamping:
According to the processing requirements, select the appropriate tool from the tool magazine and install it on the spindle.
(5) Processing execution:
The CNC system controls the movement of each axis of the machine tool and drives the tool to perform cutting, drilling, milling and other operations according to the program path.
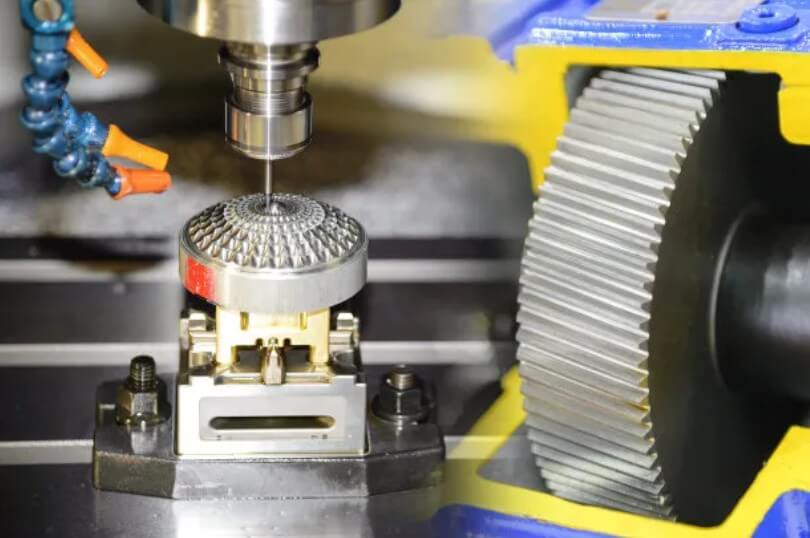
(6) Automatic tool change:
During the processing, the CNC system automatically changes the tool according to the program instructions to complete multiple processing steps.
(7) Cooling and chip removal:
The cooling system works continuously, and the chip removal device removes the chips to ensure a clean processing environment.
(8) Inspection and adjustment:
The inspection system monitors the processing accuracy in real time and makes adjustments when necessary.
(9) Processing completion:
After the program runs, the machine tool stops working and the finished workpiece is removed.
3.Processing route selection of CNC machining center
The selection of processing route is a crucial link in CNC machining, which directly affects the processing accuracy and efficiency of the workpiece. The following are the route selection principles for several common processing methods:
(1) Selection of turning processing route
● During rough turning, the tool path can be selected according to the cutting position, such as reducing the number of radial or axial layers.
● During fine turning, the final processing accuracy of the part should be ensured, the feed and retract positions should be clear, and the last processing should be completed continuously.
● The tool change position should be outside the workpiece and fixture to avoid touching other parts, and the tool change route should be short.
● The retract route should be determined according to the processing position, such as using oblique retract for external cylindrical surface processing and radial-axial retract for grooving.
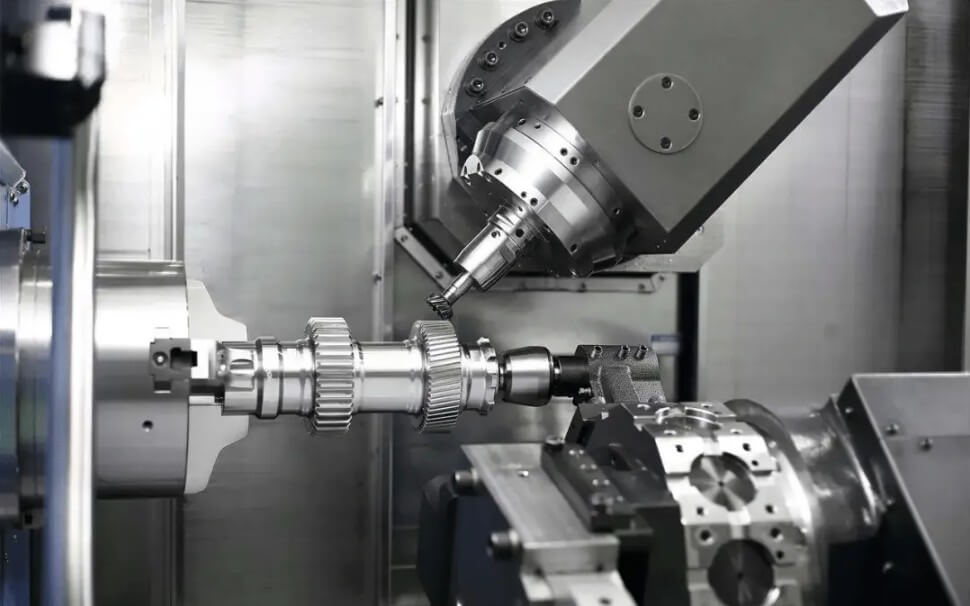
(2) Selection of milling processing route
● First, determine whether the workpiece is milled forward or reverse. The selection criteria are whether there is clearance in the feed mechanism of the machine tool and whether there is hard skin on the workpiece surface.
● When milling the outer contour, the cut-in and retract should be made along the extension line of the cutting contour.
● When milling the inner contour, if the contour does not allow extension, the cut-in and retract should be made in the normal direction.
● When milling inner grooves, the line cutting method or the ring cutting method can be used. The appropriate processing method is selected according to the surface roughness requirements.
● When milling curved surface contours, the spherical knife line cutting method is usually used to control the distance between lines to meet the accuracy requirements.
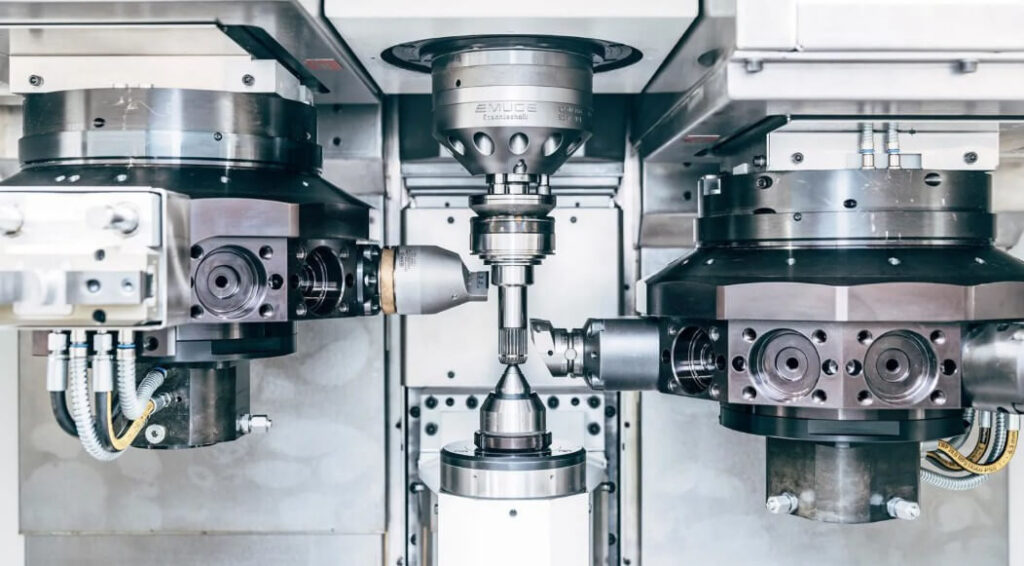
(3) Drilling processing route selection
● For holes with high precision requirements, the basic positioning direction of each hole must be consistent during drilling to avoid positioning errors.
● When processing multiple holes, the processing path must be optimized to ensure the shortest path and improve drilling efficiency.
4.Analysis of the advantages of CNC machining centers
The CNC machining center itself is a very demanding processing method. It can achieve better results than traditional processing methods and has many advantages that other processing methods do not have. The following is a detailed analysis of its main advantages:
(1) High-precision processing:
The CNC machining center adopts an advanced digital control system to achieve high-precision processing through precise coordinate positioning and tool path control. Its accuracy can reach tens of microns, which meets the processing needs of parts with extremely high precision requirements, such as aerospace and medical equipment manufacturing.

(2) High-efficiency production:
The equipment has automated processing capabilities and can achieve continuous and high-speed processing operations through preset programs and tool paths. This not only significantly shortens the processing cycle, but also improves production efficiency, and is particularly suitable for mass production.
(3) Versatility:
The CNC machining center integrates multiple processing functions such as milling, drilling, boring, and tapping, and can complete the processing tasks of complex parts. This versatility reduces equipment switching time and improves production flexibility.
(4) Reduced manual intervention:
High automation reduces the need for operators and reduces labor costs, while reducing errors caused by manual operations, ensuring the consistency and stability of product quality.
(5) Flexibility and adaptability:
The CNC machining center can be programmed and adjusted according to different processing requirements and part designs. This flexibility enables it to quickly adapt to the production needs of different varieties and small and medium batches, and is suitable for new product development and modification.
(6) Complex parts processing capability:
CNC machining centers can process complex surfaces and internal structures that are difficult to process with traditional methods, expanding the processing range and meeting the needs of modern industry for complex parts.
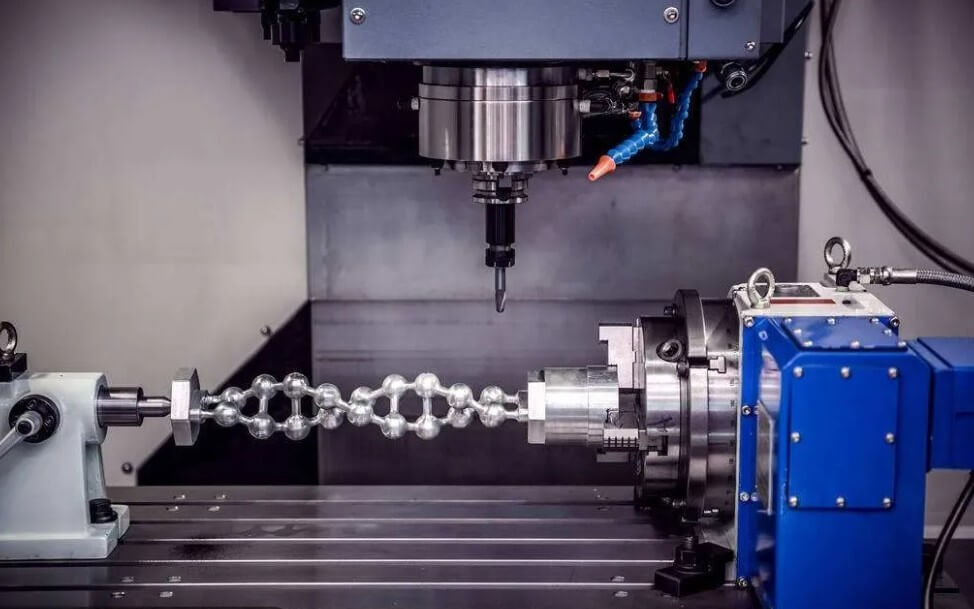
5.Applicable materials and types of parts that can be processed by CNC machining centers
CNC machining centers are powerful automated machine tools that are widely used in the processing of various materials. The following is a detailed description of their applicable materials and the types of parts that can be processed:
(1) Applicable materials:
1) Metal materials:
Including steel, cast iron, aluminum alloy, copper alloy, stainless steel, cemented carbide (such as tungsten steel), titanium alloy, etc. These materials are widely used in the automotive, aerospace, machinery manufacturing and other industries.
2) Non-metallic materials:
Such as plastics, wood, composite materials, etc. These materials are often used to manufacture electronic product housings, furniture, decorations, etc.
(2) Types of parts that can be processed:
1) Complex shape parts:
Including special-shaped parts, multi-surface parts (such as molds, cams, propellers) and parts with complex spatial surfaces (such as integral impellers and turbine blades of aircraft engines).
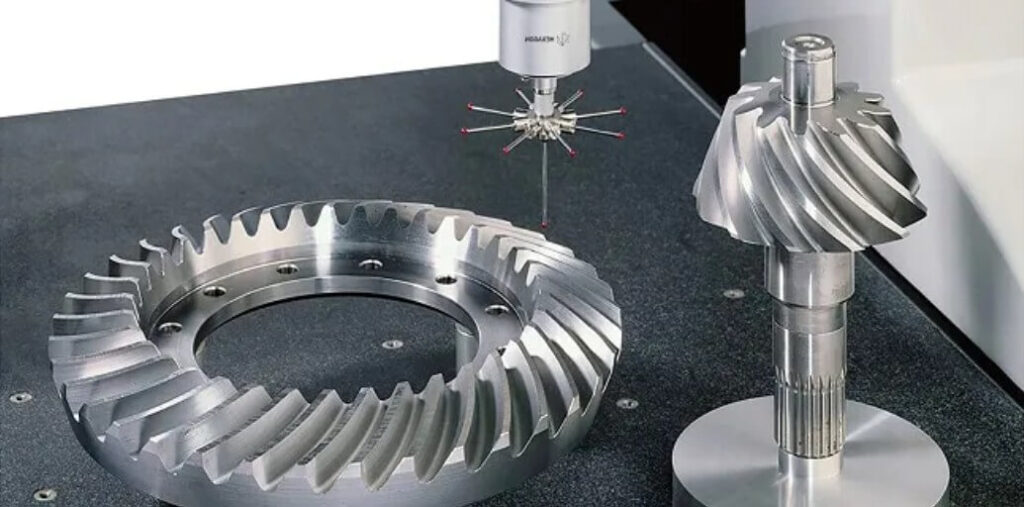
2) High-precision parts:
Such as precision mechanical parts, high-precision molds and cutting tools. Such parts have extremely high precision requirements and are commonly found in the fields of clocks, instruments, optical equipment, etc.
3) Box parts:
For example, machine tool spindle boxes, automobile engine cylinder blocks, gearbox bodies, etc. These parts usually have multiple hole systems and internal cavities.
4) Disk, sleeve, and plate parts:
Including disk and sleeve parts with keyways and radial holes, and plate parts with more hole processing, such as motor covers.
5) Mass production parts:
Various parts suitable for mass production, such as automotive parts, home appliance parts, etc. The high efficiency of CNC machining centers makes them perform well in mass production.
6) Parts made of difficult-to-process materials:
For example, high-strength and high-hardness materials can be processed efficiently and with high quality through CNC machining centers.
7) Personalized customized parts:
Parts that can be customized according to customer needs, such as customized aerospace parts, customized automotive parts, etc.
6.Summary
To sum up, it can be seen that CNC machining center is a highly integrated and intelligent manufacturing equipment, which is not only applicable to a wide range of materials, but also can process a variety of parts. It has the characteristics of high precision, high efficiency and high reliability, providing strong support for modern manufacturing industry.
5 Comments