3 axis CNC machining: analysis of operation flow, advantages and limitations
3 axis CNC machining is an efficient machining technology widely used in modern manufacturing. It realizes automated machining of workpieces by precisely controlling the movement of the tool on the three coordinate axes of X, Y and Z. This article will elaborate on the basic concepts, operation flow, advantages, limitations and types of parts suitable for machining of 3 axis CNC machining.
1.Basic concepts
3 axis CNC machining is a CNC technology in which the cutting tool moves only along three linear axes (X, Y, Z) while the workpiece remains fixed. This machining method is suitable for manufacturing parts with simple geometric shapes and is the most basic and common form of CNC machining.
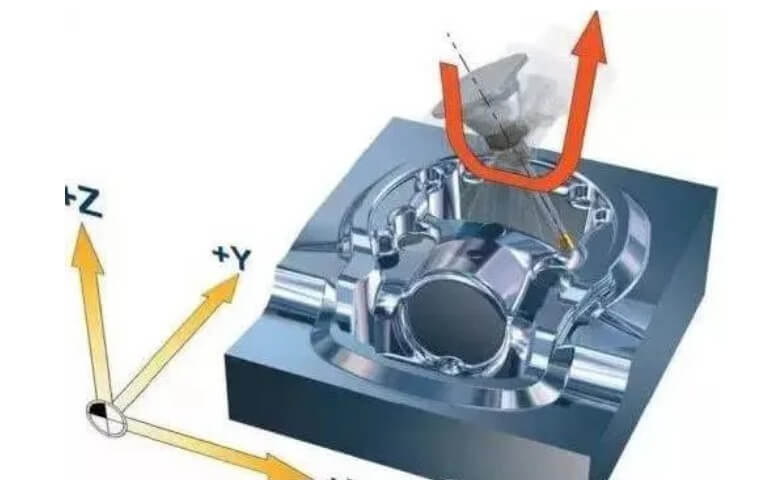
2.3 axis CNC machining operation flow
(1) Preparation
1) Drawing analysis:
Read the machining drawings in detail and clarify the machining requirements, including dimensional accuracy, surface roughness, geometric tolerances, etc.
2) Material preparation:
Select suitable materials according to the drawing requirements and perform necessary pretreatment, such as cutting and heat treatment.
3) Tool selection:
Select appropriate tools according to the processing materials and processing requirements, including tool type, material, geometric parameters, etc.
4) Fixture design:
Design or select appropriate fixtures to ensure that the workpiece is accurately positioned and reliably clamped during the processing.
(2) Programming
1) CAD modeling:
Use CAD software to draw a three-dimensional model of the workpiece and ensure that the model is consistent with the drawing.
2) CAM programming:
Use CAM software to generate CNC machining programs, including tool paths, cutting parameters, feed speeds, etc.
3) Program verification:
Verify the correctness of the program through simulation software to ensure that there are no collisions, overcuts, etc.
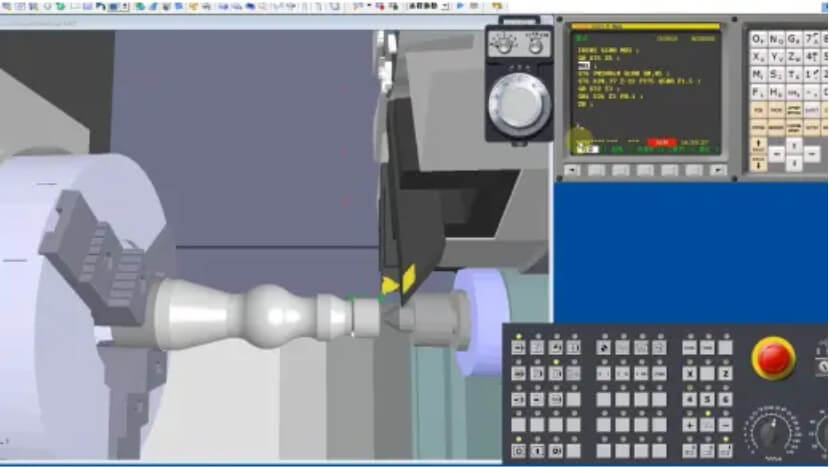
(3) Machine tool settings
1) Workpiece clamping:
Install the workpiece on the fixture to ensure accurate positioning and reliable clamping.
2) Tool installation:
Install the selected tool on the machine tool spindle and measure and compensate the tool length and radius.
3) Tool setting operation:
Use a tool setting instrument or manual tool setting method to determine the relationship between the origin of the workpiece coordinate system and the machine tool coordinate system.
(4) Processing process
1) Program loading:
Load the verified CNC program into the machine tool control system.
2) Trial cutting:
Perform trial cutting to check the processing effect and adjust the program or process parameters if necessary.
3) Formal processing:
After confirmation, perform formal processing, monitor the processing process and ensure the processing quality.
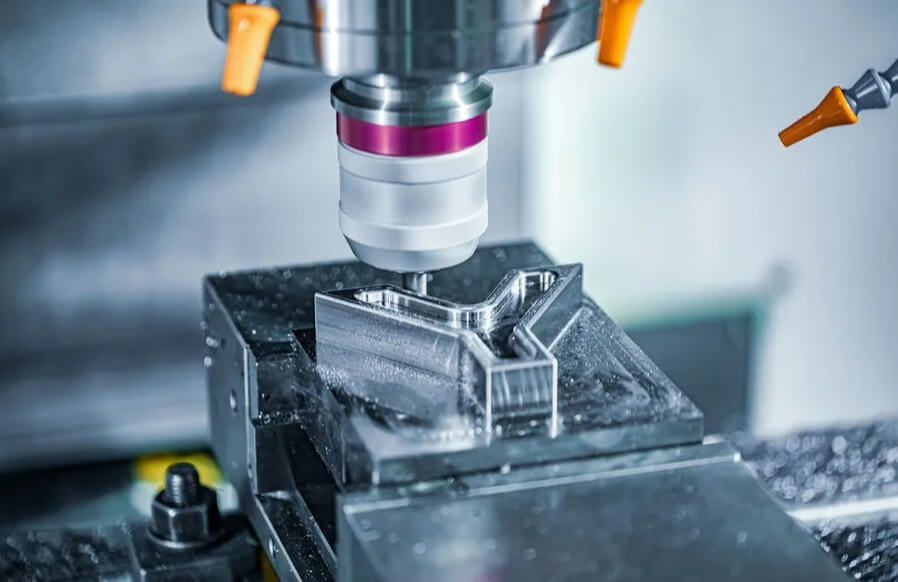
(5) Post-processing
1) Workpiece inspection:
Use measuring tools to inspect the processed workpiece to ensure that it meets the requirements of the drawing.
2) Surface treatment:
Perform surface treatment as needed, such as polishing, sandblasting, electroplating, etc.
3) Cleaning and maintenance:
Clean the machine tool and work area, perform necessary machine tool maintenance, and ensure that the equipment is in good condition.
3.Analysis of the advantages of 3 axis CNC machining
(1) High precision
3 axis CNC machining can achieve high-precision machining of workpieces through the linkage of three linear axes, X, Y, and Z. The high precision of CNC machine tools ensures that every action in the machining process is strictly carried out according to the preset path, thereby ensuring the high quality of the final product.
(2) Versatility
3 axis CNC machining machine tools can handle a variety of materials and geometric shapes and are suitable for multiple industries and applications. By replacing different types of tools, 3-axis machine tools can perform a variety of operations such as drilling, milling, and turning to meet different machining needs.
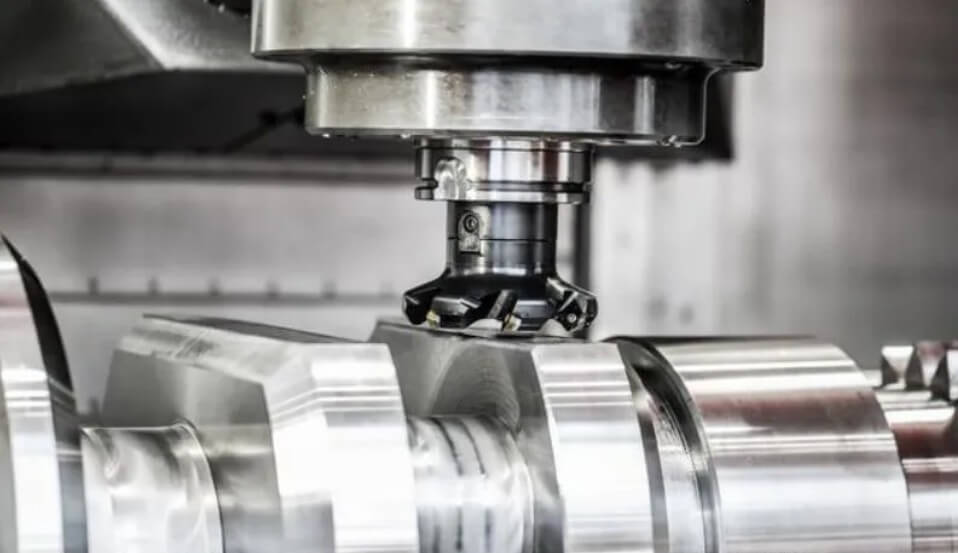
(3) High degree of automation
3 axis CNC machining is controlled by a computer numerical control (CNC) system, which greatly reduces the need for manual intervention. Automated machining not only improves production efficiency, but also reduces human errors and improves product consistency and quality.
(4) Cost-effectiveness
Compared with more advanced 4-axis and 5-axis CNC machining machine tools, 3-axis machine tools have a relatively simple structure and lower manufacturing and maintenance costs. This makes 3 axis CNC machining the first choice for small and medium-sized enterprises and projects with limited budgets.
In addition, due to its relatively simple operation, the requirements for operators are also low, further reducing training costs.
(5) High processing efficiency
3 axis CNC machining improves the efficiency of the manufacturing process by optimizing the use of resources and energy. The machine tool can move the tool quickly and accurately, reducing processing time and material waste.
In addition, 3 axis CNC machining can also improve efficiency through mass production and is suitable for standardized parts that need to be produced in large quantities.
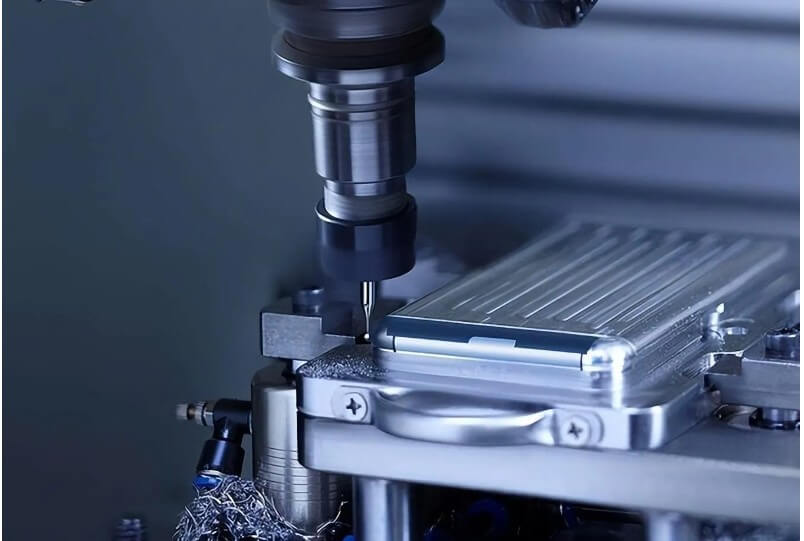
4.Limitations of 3 axis CNC machining
(1) Design limitations
3 axis CNC machining machine tools can only process one surface at a time and cannot process multiple surfaces at the same time. This means that for parts with complex geometric shapes, multiple clamping and adjustment of the workpiece position are required, which increases the processing time.
In addition, since the tool direction remains unchanged during the processing, the processing of some complex shapes may not be possible or require additional auxiliary equipment.
(2) Positioning limitations
In 3 axis CNC machining, the workpiece is usually fixed on the worktable of the machine tool, and the worktable cannot move freely. Therefore, in order to process different surfaces of the workpiece, the operator needs to adjust the direction of the workpiece multiple times.
(3) Poor surface finish
Since the tool is long in 3 axis CNC machining and the tool direction cannot be adjusted in real time during machining, vibration may occur when machining complex surfaces, affecting the surface finish. Especially when machining deep cavities or complex contours, the vibration of the tool may cause surface roughness and require additional finishing processes.
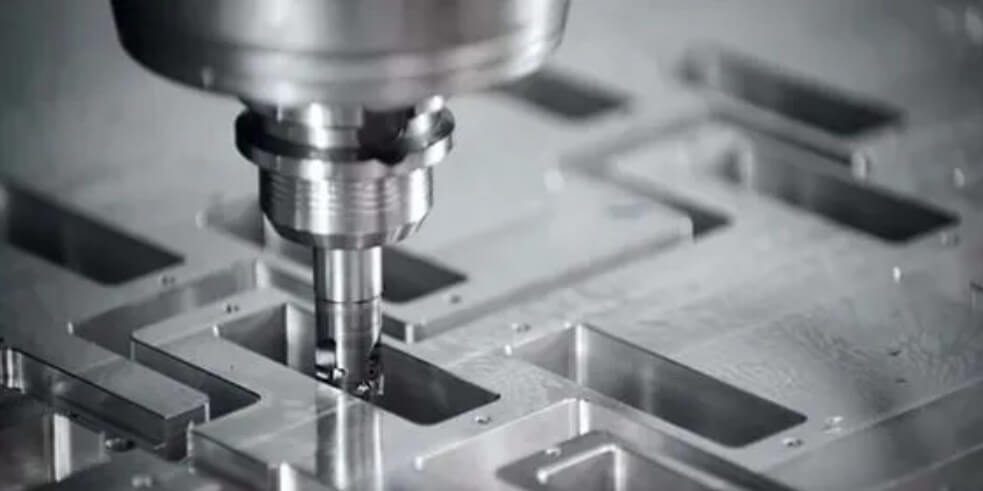
(4) Limited machining range
The machining range of 3-axis machine tools is mainly limited to the top or side surfaces of the workpiece. For parts that need to be machined on the bottom surface or complex spatial surfaces, 3 axis machine tools may not meet the requirements. This limits the application of 3 axis CNC machining in certain high-end manufacturing fields, such as aerospace and precision mold manufacturing.
(5) Reduced efficiency
For complex parts, multiple clamping and adjustments lead to reduced machining efficiency. In modern manufacturing industries that require high precision and high efficiency, these limitations may affect production efficiency and cost-effectiveness.
5.Types of parts suitable for 3 axis CNC machining
(1) Planar parts:
The machining surface of this type of part is parallel or perpendicular to the horizontal plane, and is suitable for milling, drilling and other operations using 3-axis machine tools. For example, simple plate parts, cover plates, etc.
(2) Rotating parts:
Suitable for processing on 3-axis lathes, such as shaft and sleeve parts. These parts can be efficiently cut by rotating around the main axis.
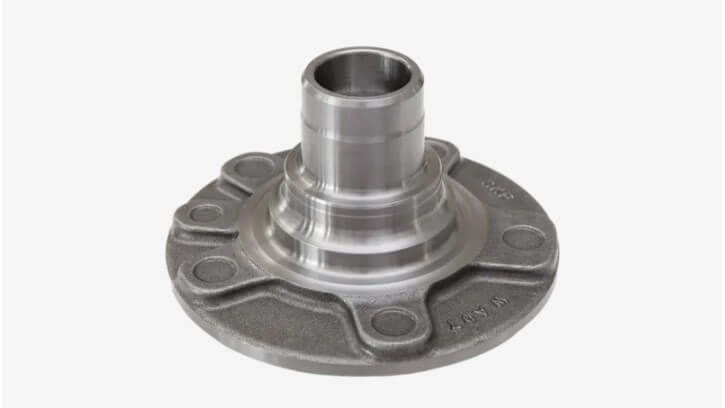
(3) Parts with simple surfaces:
Although 3 axis CNC machining has some limitations in processing complex surfaces, it can still process some parts with simple surfaces, such as mold parts or housing parts with shallow surfaces.
(4) Box parts:
For some box parts with relatively simple structures, 3 axis CNC machining can process planes and hole systems, such as distribution box housings, simple pump bodies, etc.
(5) Special-shaped parts:
Special-shaped parts with irregular shapes but relatively simple machining surfaces are also suitable for 3 axis CNC machining, such as some brackets and buckle parts.
6.Summary
As a mature and widely used manufacturing technology, 3 axis CNC machining has the advantages of high precision, versatility, high degree of automation and cost-effectiveness. However, its limitations such as design limitations, positioning limitations, poor surface finish and limited processing range cannot be ignored.
Therefore, when choosing processing technology, the advantages and limitations of 3 axis CNC machining should be weighed according to the specific processing requirements and part characteristics, and the appropriate processing solution should be selected.