Vertical machining center vs horizontal machining center: What is the difference?
In modern manufacturing, machining centers are indispensable mechanical equipment. They use CNC technology to achieve highly automated machining, can complete a variety of processes, improve production efficiency and ensure machining accuracy.
Vertical machining centers and horizontal machining centers are two common types, and they have significant differences in many aspects. This article will discuss the differences between the two types of machining centers in detail from the aspects of structure, machining capacity, applicable scenarios, price and operation.
1.Structural differences between vertical machining centers and horizontal machining centers
The main difference between the two lies in the structural design of the spindle and the worktable.
(1) Vertical machining center:
1) Spindle state:
The spindle of a vertical machining center is in a vertical state. This means that the tool processes the workpiece from above.
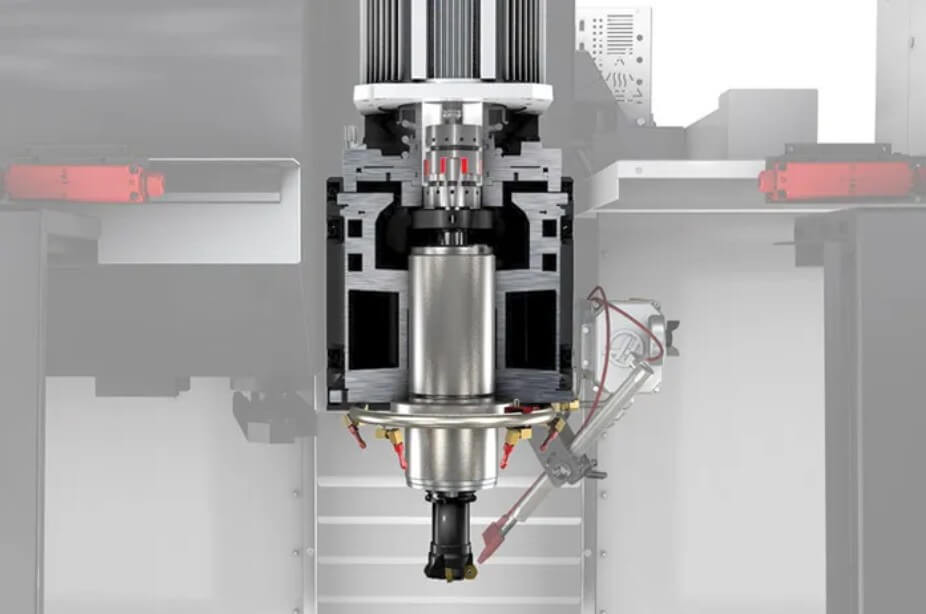
2) Worktable:
The worktable of a vertical machining center is usually a T-slot worktable with a cross slide structure, with two sets of motion mechanisms responsible for movement in perpendicular directions (X and Y). Sometimes, in order to process helical parts, a rotary table that rotates along the horizontal axis can be installed on the worktable.
3) Structural form:
Most of them are fixed column type, that is, the column is fixed, and the worktable and spindle box move on their own guide rails.
(2) Horizontal machining center:
1) Spindle state:
The spindle of the horizontal machining center is in a horizontal state. This allows the workpiece to be processed on a horizontal plane.
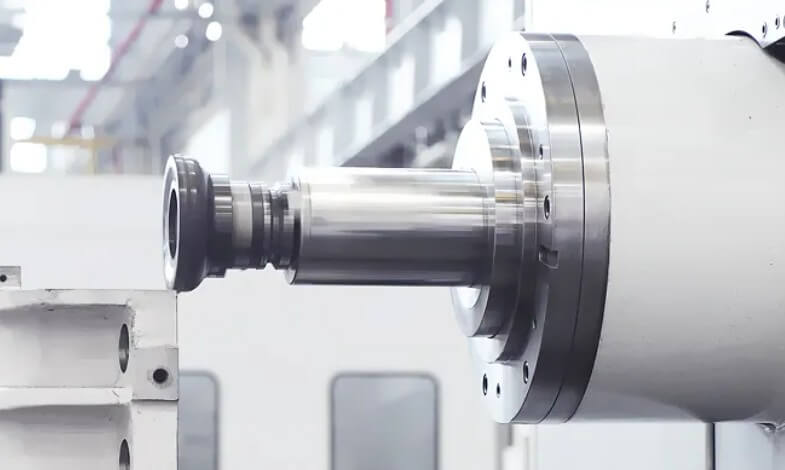
2) Worktable:
Horizontal machining centers usually have a rotary table with automatic indexing. The worktable is only designed to move in the X or Y direction, and the form is generally a rotary table with a dot matrix screw hole table top, which is relatively easy to select an exchangeable double table.
3) Structural form:
Horizontal machining centers are divided into fixed column type and mobile column type according to whether the column moves. Fixed column type includes worktable cross motion, spindle box cross motion and spindle box side hanging and column; mobile column type includes planing table type, column cross motion type and spindle slide feed type.
2.Differences in processing capabilities and applicable scenarios
(1) Vertical machining center:
1) Processing capabilities:
Vertical machining centers are mainly suitable for processing complex parts such as plates, discs, molds and small shells. It can complete milling, boring, drilling, tapping and thread cutting processes.
Due to the vertical arrangement of the spindle, it is difficult for the vertical machining center to discharge chips when processing cavities or concave surfaces, which may damage the tool and the processed surface.
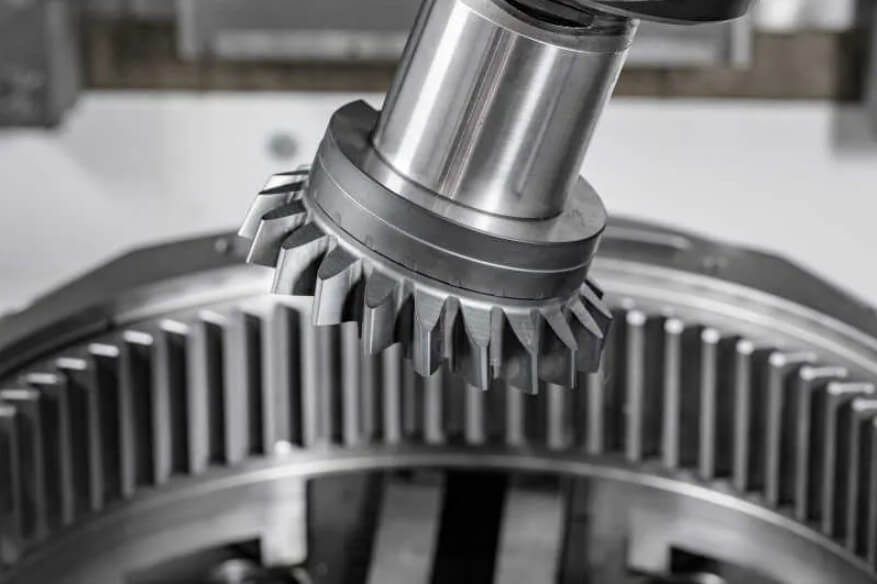
2) Applicable scenarios:
Vertical machining centers are easy to install and operate, easy to observe the processing status, and easy to debug the program. Therefore, it is suitable for processing parts with relatively small volume and high precision requirements. In addition, vertical machining centers have a small footprint and are suitable for production environments with limited space.
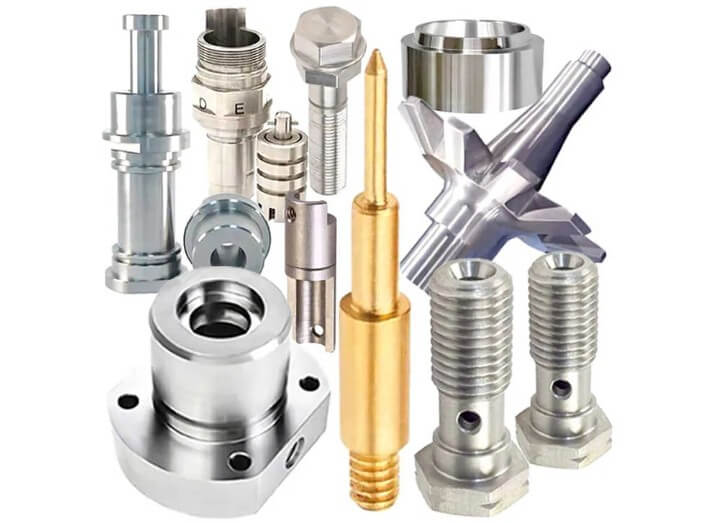
(2) Horizontal machining centers:
1) Processing capabilities:
Horizontal machining centers are particularly suitable for processing large and heavy workpieces, as well as complex parts that require multi-station processing. Because its spindle is arranged horizontally and the workpiece is processed on a horizontal plane, it has a larger working space and can accommodate larger workpieces.
Horizontal machining centers usually use a high-rigidity bed, column and spindle structure that can withstand heavy cutting and ensure machining accuracy. It also has a multi-axis linkage function and can complete complex three-dimensional surface machining.
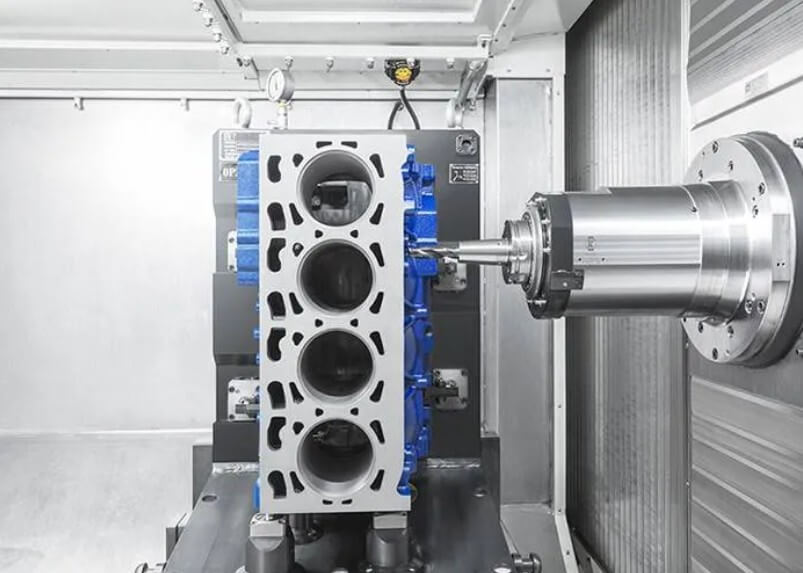
2) Applicable scenarios:
Horizontal machining centers are suitable for processing box-type parts, such as engine cylinders, gearbox housings, etc. Due to easy chip removal, horizontal machining centers have advantages when processing complex dents and mold cavities. In addition, horizontal machining centers can further improve machining efficiency by adding automatic indexing rotary tables or exchangeable double workbenches.
3.Price and complexity differences
Generally speaking, horizontal machining centers are relatively expensive due to their complex structure. Vertical machining centers are relatively simple in structure, occupy a smaller area, and are more affordable.
(1) Vertical machining center:
1) Price:
The price of vertical machining centers is relatively low, which is suitable for small and medium-sized enterprises or production needs with limited budgets.
2) Complexity:
The structure of vertical machining centers is relatively simple, and operation and maintenance are relatively easy. Therefore, its training cost and maintenance cost are also relatively low.
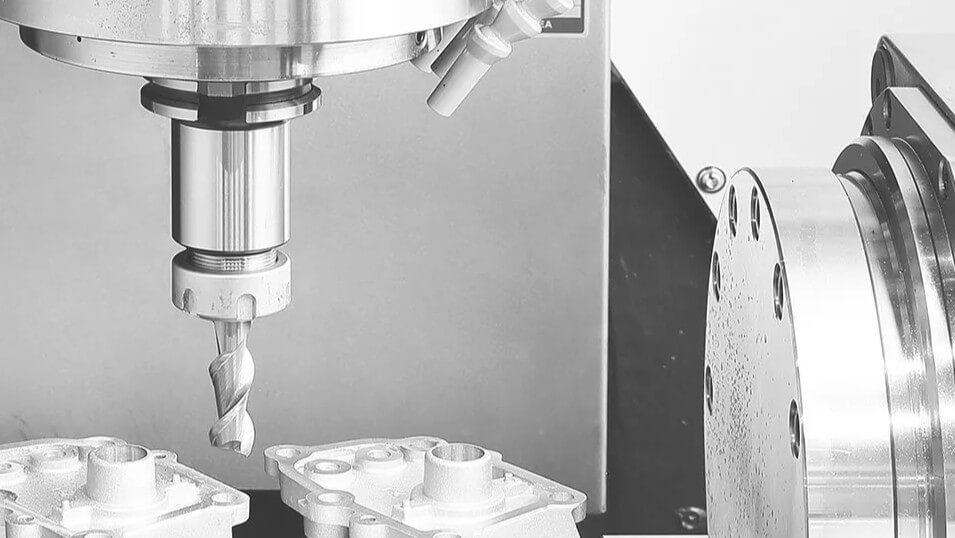
(2) Horizontal machining center:
1) Price:
The price of horizontal machining center is relatively high due to its complex structure. This makes it more common in large enterprises and heavy industry.
2) Complexity:
The operation and maintenance of horizontal machining center are relatively complex and require a higher level of technology. Therefore, its training cost and maintenance cost are also relatively high.
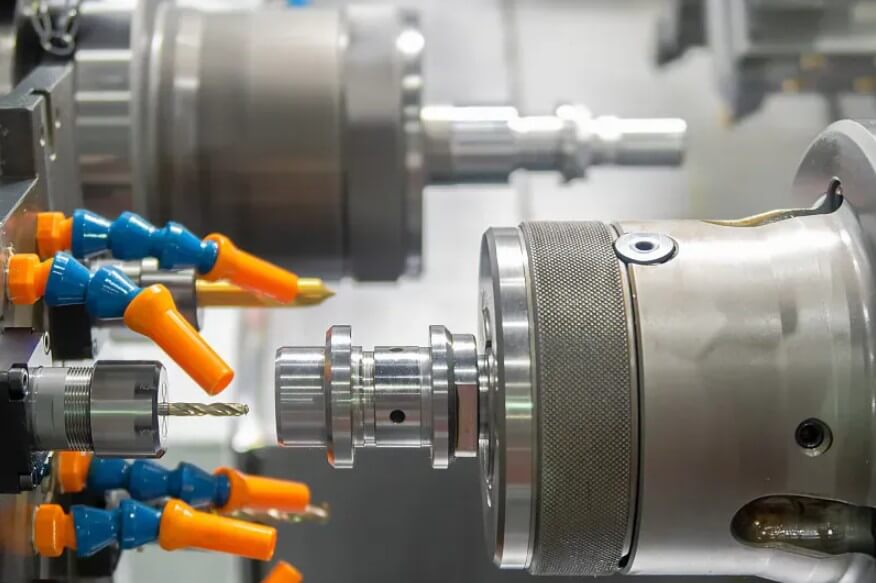
4.Differences in operation and observation
(1) Vertical machining center
1) Operation:
The operation of vertical machining center is relatively simple. The workpiece and tool move on three axes (X, Y and Z axes) and process the fixed workpiece from above. Since the processing is carried out from above, it is easy to check the cutting situation.
2) Observation:
The processing process of vertical machining center is easy to observe, which is convenient for timely detection of problems and shutdown or modification.
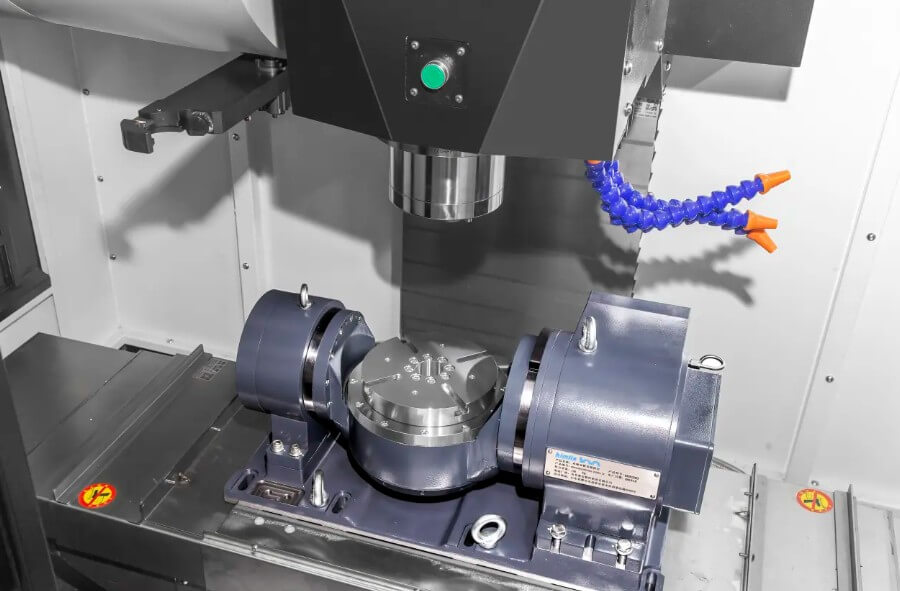
(2) Horizontal machining center:
1) Operation:
The programming and processing technology of horizontal machining center are relatively complex and usually require a higher level of technology. The workpiece is processed on a horizontal plane, and more attention and skills are required during operation.
2) Observation:
The machining process of a horizontal machining center is relatively difficult to observe, especially when machining large or complex parts. However, due to its easy chip removal, the chips have less interference with the machining process.
5.Other differences
(1) Floor space:
Vertical machining center: Small footprint, suitable for production environments with limited space.
Horizontal machining center: Large footprint, requiring more installation space.
(2) Positioning accuracy:
Vertical machining center: Generally, the positioning accuracy is higher, suitable for parts with higher machining accuracy requirements.
Horizontal machining center: Due to its complex structure, the positioning accuracy may be slightly lower than that of a vertical machining center, but it performs well in heavy cutting and high-precision machining.
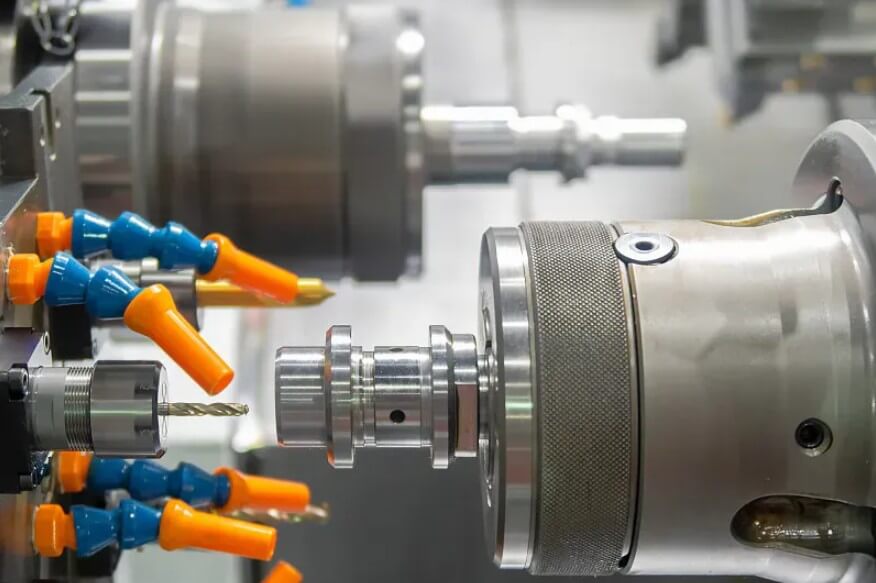
(3) Optional configuration:
Vertical machining center: Relatively few optional configurations, mainly concentrated in tools and accessories.
Horizontal machining center: Rich optional configurations, including automatic exchange worktable, multi-axis linkage function, etc., can meet more complex machining needs.
6.Conclusion
Vertical machining centers and horizontal machining centers have obvious differences in structure, processing capacity, applicable scenarios, price and operation. The choice of which type of machining center depends on factors such as specific processing requirements, workpiece type and budget.
Vertical machining centers are suitable for processing small parts with high precision requirements, while horizontal machining centers are suitable for processing large and heavy workpieces and complex parts that require multi-station processing. In practical applications, manufacturers should choose the appropriate machining center according to their own situation to improve production efficiency and economic benefits.