Precision CNC milling: the core technology of modern manufacturing industry
Precision CNC milling is a milling process controlled by computer numerical control (CNC) technology, which uses rotating tools to perform high-precision machining on workpieces. It can achieve the machining of complex shapes, high-precision dimensions and high-quality surfaces, and is an indispensable machining method in modern manufacturing. The following will introduce it in detail and comprehensively:
1.Definition and characteristics of precision CNC milling
Precision CNC milling is a subtractive manufacturing process that combines traditional milling with computer numerical control technology. It uses a rotating multi-blade tool to cut the workpiece fixed on the worktable to remove excess material, thereby machining the required shape, size and surface quality. The core of CNC milling is to control the movement of the machine tool through a pre-written program (G code) to achieve high-precision and high-efficiency automated machining.
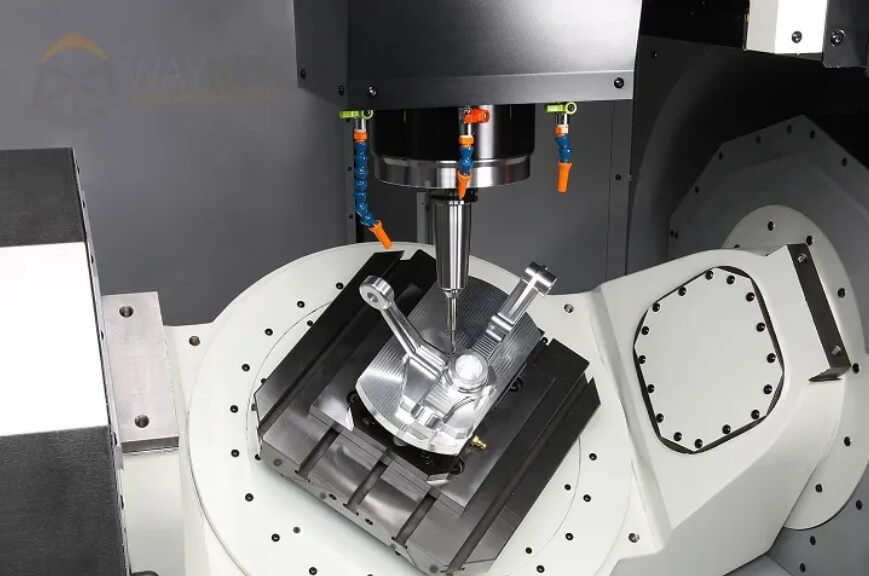
Characteristics of precision CNC milling:
(1) High precision:
The CNC system can accurately control the movement of the tool to achieve micron-level or even higher machining accuracy.
(2) High efficiency:
Automated machining reduces manual intervention and improves production efficiency, which is particularly suitable for mass production.
(3) Flexibility:
Programming can quickly switch processing tasks to meet the needs of multi-variety and small-batch production.
(4) Complex shape processing:
It can process complex geometric shapes such as planes, curved surfaces, grooves, holes, threads, etc.
(5) Wide application:
It plays an important role in aerospace, automobile, electronics, medical equipment and other fields.
2.Process analysis of precision CNC milling parts
(1) Process analysis of part drawings
○ Review the integrity and correctness of the part drawings to ensure that the contour dimensions and geometric relationships are correct.
○ Check whether the dimensioning method is suitable for CNC processing characteristics, and give priority to using the same reference dimensioning or directly giving coordinate dimensions.
○ Ensure that the geometric elements that constitute the contour are sufficient to avoid programming and processing ambiguity.
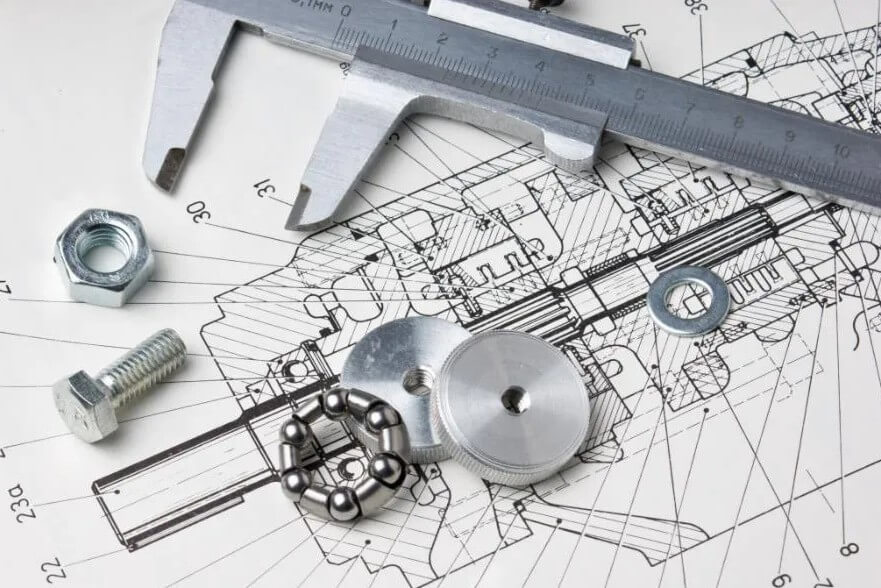
(2) Planning of processing process routes
○ Divide the processing stages according to the requirements of the part drawings, usually divided into rough processing, semi-finishing and finishing.
○ Determine the processing sequence according to the principle of roughing first and then finishing, such as rough milling the outer contour, rough milling the inner contour, and finally drilling.
(3) Selection of CNC machining tools
○ Select appropriate tools according to the machining stage, large diameter tools for rough machining, and small diameter tools for fine machining.
○ Tool selection needs to consider the cutting performance of the workpiece material, such as end mills and end mills commonly used for steel parts.
(4) Selection of cutting parameters
○ Determine the back cutting amount or side cutting amount, such as the rough milling depth and fine milling depth.
○ Determine the spindle speed and feed speed according to the material properties and tool type.
(5) Clamping scheme
○ Select appropriate fixtures to ensure the positioning and clamping of the workpiece during machining, such as using a machine vise.
○ Ensure that the clamping mechanism does not affect the feed, and the machining part should be open.
(6) Determine the tool path
○ Design a reasonable tool path to improve machining efficiency and surface quality, such as using the circular cutting method to mill the contour line.
○ Ensure that the tool cuts in and out reasonably to avoid cutting marks.
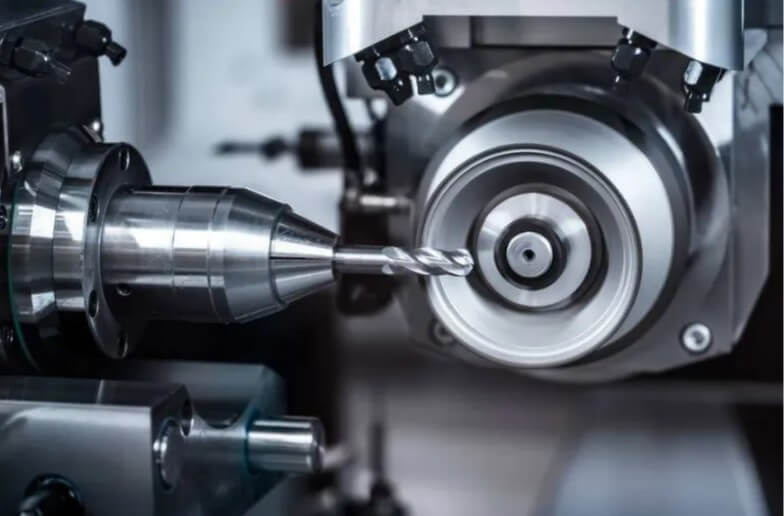
(7) CNC programming
○ Generate CNC machining programs based on part drawings and process analysis, and automatically program.
○ Use CAM software to simulate and verify the machining process and adjust the machining program.
(8) Machining implementation and inspection
○ Perform machining according to the CNC program, monitor the machining process, and adjust parameters in time.
○ Perform dimensional and surface quality inspection after machining to ensure that it meets the requirements of the drawings.
3.Introduction to types of CNC milling machines
(1) Vertical CNC milling machine
1) Structural features:
The spindle axis of the vertical CNC milling machine is perpendicular to the horizontal plane. This layout makes the vertical CNC milling machine easy to observe and operate during machining.
2) Scope of application:
Vertical CNC milling machines have the widest application range and are suitable for machining workpieces with relatively small dimensions in the height direction, such as molds, cams, blades, etc.
3) Coordinate linkage:
Vertical CNC milling machines can generally perform 3-axis linkage machining, and some machine tools support 4-axis or 5-axis linkage machining, which can complete the machining of complex curved surfaces.
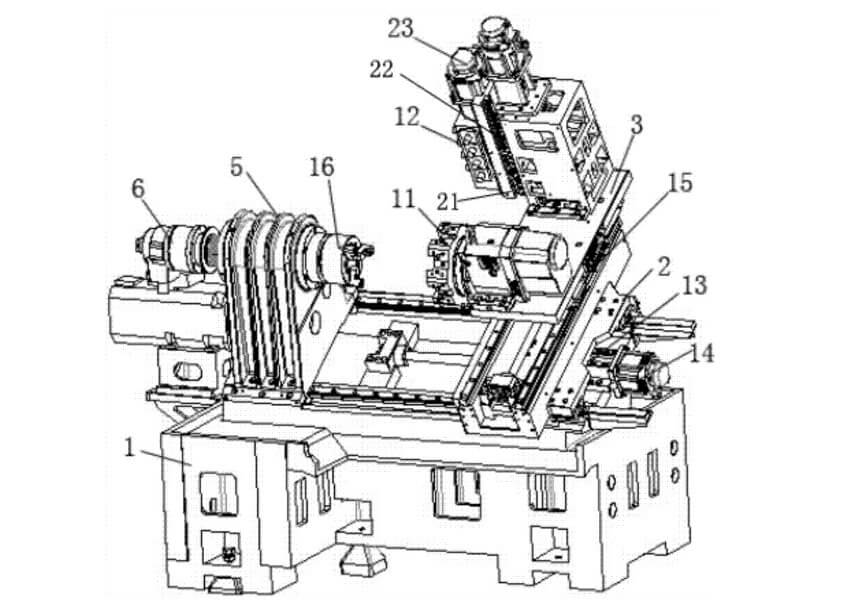
(2) Horizontal CNC milling machine
1) Structural features:
The spindle axis of the horizontal CNC milling machine is parallel to the horizontal plane, and it is usually equipped with a CNC turntable or a universal CNC turntable to achieve 4-axis or 5-axis machining.
2) Machining capacity:
Horizontal CNC milling machines are suitable for machining large or box-type parts, and can perform multi-faceted machining in one installation, thereby improving production efficiency.
3) Scope of application:
Due to their complex structure and large footprint, horizontal CNC milling machines are usually used in production workshops that require high-precision, multi-faceted machining.
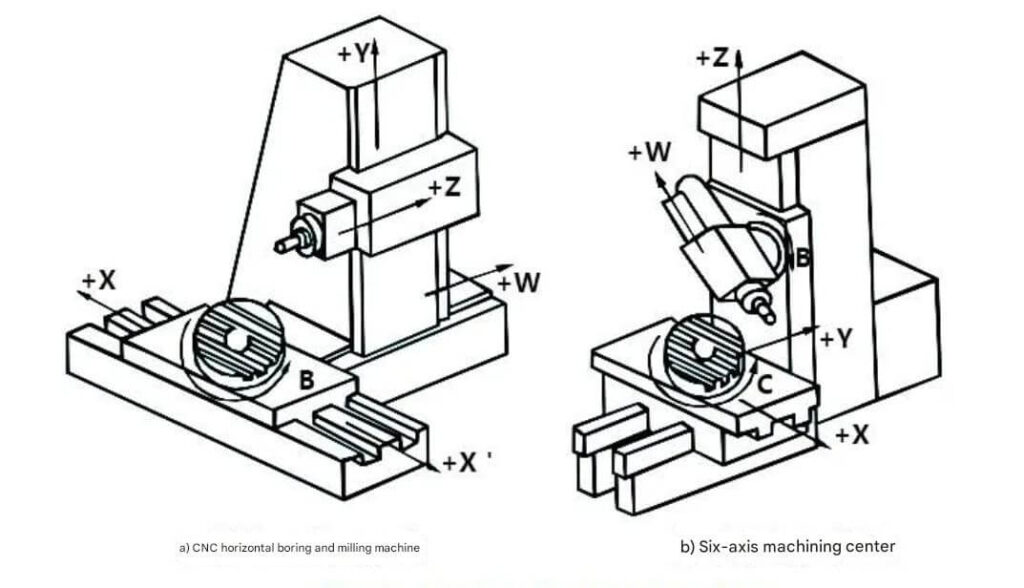
(3) Multi-axis CNC milling machines
1) 3-axis CNC milling machine:
The 3-axis CNC milling machine has a simple and efficient structure and is suitable for machining more conventional parts. The workpiece is machined at a fixed position, and a variety of machining requirements are achieved through the linkage of the three axes of X, Y, and Z.
2) 4-axis CNC milling machine:
The 4-axis CNC milling machine adds a rotating axis to the 3-axis, which improves machining flexibility and production capacity. Requires high-end software for control and is suitable for more complex machining tasks.
3) 5-axis CNC milling machine:
5-axis CNC milling machine can move cutting tools or parts along five axes at the same time. It has extremely high machining flexibility and precision. It can perform precision CNC milling of various complex and precise parts and is widely used in the field of high-precision machining.
4.Operation types of precision CNC milling
(1) Plane milling
○ Plane milling is mainly used to machine the plane of the workpiece. The axis of the cutting tool is parallel to the surface being machined.
○ Use a plane milling cutter with peripheral teeth, which is suitable for rapid material removal.
○ Commonly used to machine the top or bottom plane of a part to ensure the flatness and precision of the plane.

(2) Face milling
○ Face milling is used to create a flat surface perpendicular to the axis of rotation of the tool.
○ Face milling cutters have multiple interchangeable blades and can efficiently machine large surfaces.
○ Suitable for machining the end faces of parts or planes that require high finish.
(3) Angle milling
○ Angle milling processes features at specific angles, such as chamfers and grooves, by placing the tool axis at a certain angle to the workpiece surface.
○ Use a milling cutter with a specific angle, such as a conical cutting head or a dovetail groove cutter.
○ Commonly used to process the edges of parts to increase the strength and aesthetics of the parts.
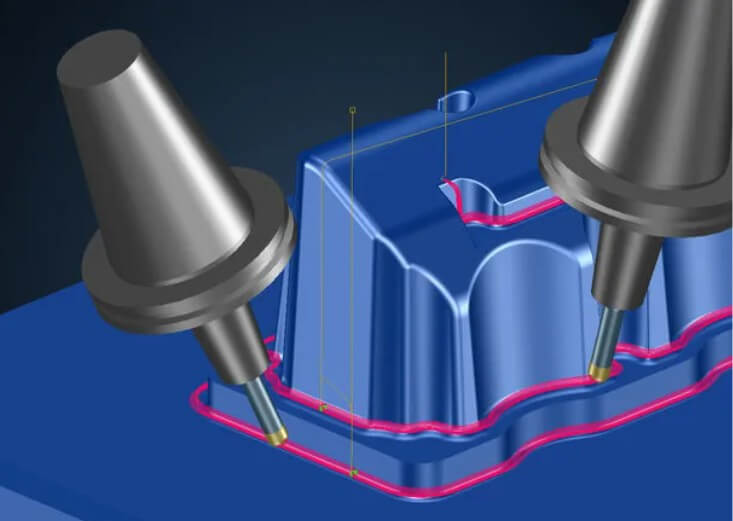
(4) Forming milling
○ Forming milling is used to process complex contours, such as circular edges, grooves, etc., using tools with special shapes.
○ Use concave, convex or specially shaped forming tools.
○ Suitable for processing molds, models and other parts that require complex shapes.
(5) Copy milling
○ Copy milling copies the shape of the template by moving the tool along an inclined or vertical path on the workpiece surface.
○ Use a copy milling cutter that matches the shape of the template.
○ Commonly used to process decorative parts or replicate complex shapes.
5.Material selection and considerations for precision CNC milling
(1) Precision CNC milling is applicable to a variety of materials. Common ones include:
○ Metal products: aluminum, titanium, stainless steel, tool steel. Low carbon steel, brass, copper
○ Plastics: ABS, polycarbonate, nylon
○ Others: ceramics, composite materials, phenolic plastics
(2) Considerations for selecting materials for precision CNC milling
1) Material properties
○ Hardness: Harder materials require more wear-resistant tools and lower cutting speeds.
○ Toughness: High-toughness materials are prone to cutting vibration, affecting machining accuracy.
○ Wear resistance: Directly affects the service life of the workpiece.
2) Processing requirements
○ Precision requirements: High-precision machining requires the selection of materials with uniform texture and good material stability.
○ Surface roughness: Workpieces requiring high surface finish should choose materials that are easy to obtain good surface quality.
3) Cutting process
○ Cutting speed: The optimal cutting speed for different materials is different.
○ Feed rate and back cutting depth: need to be adjusted according to the mechanical properties of the material.
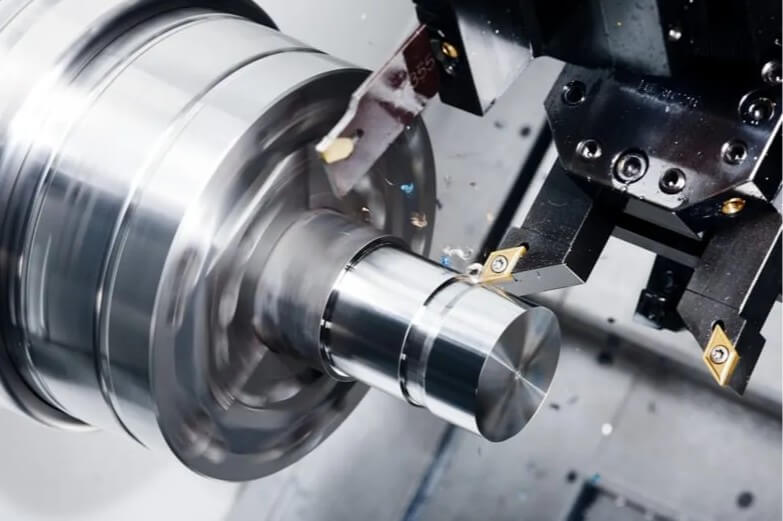
4) Economic efficiency
○ Material cost: Choosing cost-effective materials can reduce production costs.
○ Processing efficiency: Efficient processing can reduce time and machine tool usage costs.
6.Types of parts that precision CNC milling is good at processing
(1) Planar parts
○ Use face milling cutters or end mills for plane milling. Rough milling, semi-finishing milling and finishing milling can be achieved through multiple passes.
○ Generally can reach IT7-IT9 level (±0.025-±0.1mm).
(2) Contour parts
○ Through two-axis or three-axis linkage control, use end mills or ball-end milling cutters for contour milling, which can process internal and external contours, bevels, grooves, etc.
○ Can reach IT8-IT10 level (±0.05-±0.2mm).
(3) Surface parts
○ Use multi-axis CNC milling machines and ball-end milling cutters or drum milling cutters for surface milling, which is suitable for complex surface parts such as molds and blades.
○ Depending on the complexity of the surface, it can reach IT8-IT12 level (±0.05-±0.3mm).
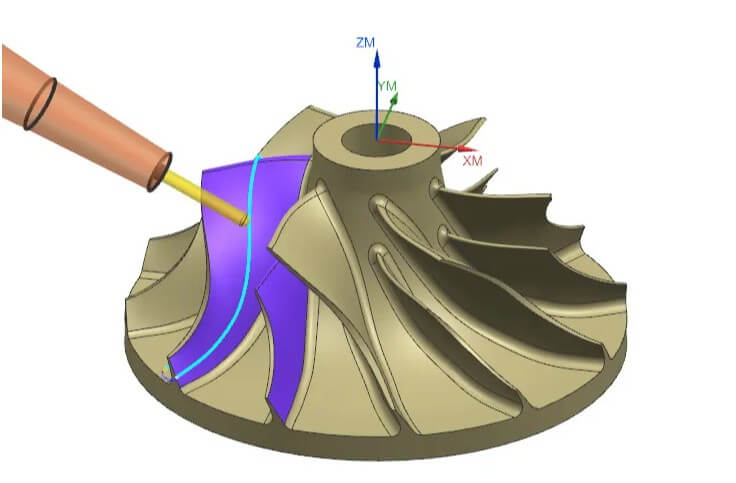
(4) Hole parts
○ Use drills, reamers, boring cutters and other tools for drilling, reaming and boring, which is suitable for high-precision hole processing.
○ Usually it can reach IT6-IT8 level (±0.01-±0.05mm).
(5) Variable bevel parts
○ Use four-axis or five-axis CNC milling machines to achieve variable bevel surface milling through multi-angle processing.
○ It can reach IT8-IT11 level (±0.05-±0.25mm).
7.Application of precision CNC milling technology
(1) Aerospace field
Aerospace parts usually require extremely high precision, strength and high temperature resistance.
Material is mostly high-strength alloy that is difficult to process (such as titanium alloy, nickel-based alloy).
Parts suitable for production:
○ Engine parts: such as turbine blades and compressor blades, which require complex curved surfaces and high surface quality.
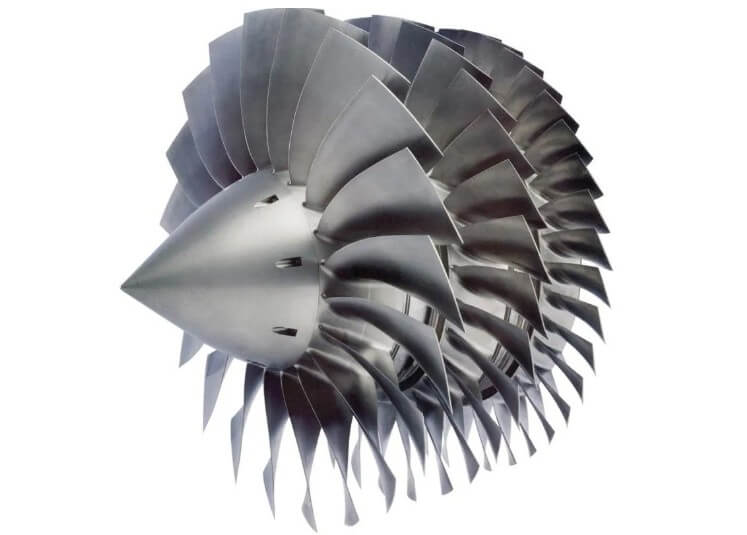
○ Structural parts: such as fuselage frames and wing ribs, which require high strength and lightweight design.
○ Hydraulic system parts: such as valve bodies and joints, which require high precision and sealing.
(2) Automobile manufacturing field
Automobile parts require high precision, high consistency and mass production capacity.
Material includes aluminum alloy, steel and composite materials.
Parts suitable for production:
○ Engine parts: such as cylinder blocks and cylinder heads, which require high-precision holes and complex inner cavities.
○ Transmission parts: such as gears and housings, which require high-precision tooth shape and surface finish.
○ Chassis parts: such as suspension brackets and steering knuckles, which require high strength and wear resistance.
(3) Medical device field
Medical device parts require high precision, high surface quality and biocompatibility.
Material is mostly stainless steel (such as 316L) and titanium alloy.
Parts suitable for production:
○ Surgical instruments: such as scalpels and tweezers, which require high precision and sharpness.
○ Implants: such as artificial joints and bone plates, which require complex curved surfaces and high surface finish.
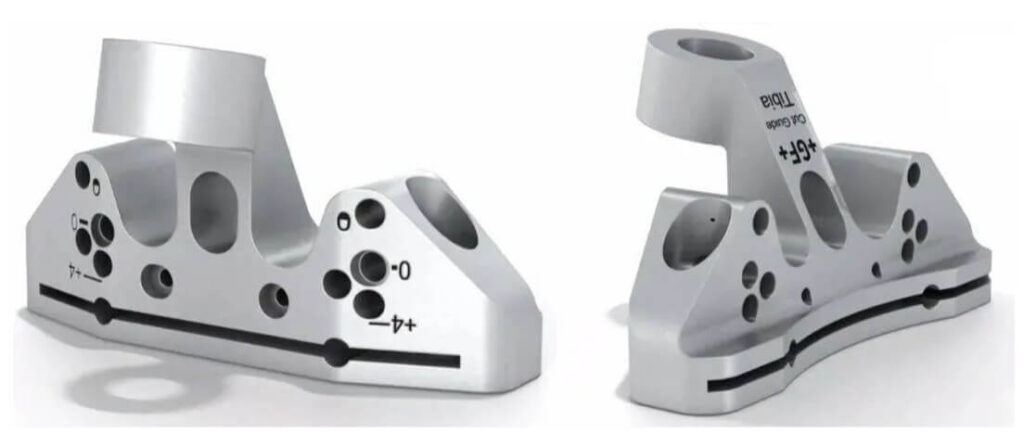
○ Equipment housing: such as medical instrument housing, which requires high-precision assembly and aesthetics.
(4) Electronic industry field
Electronic parts are usually small in size and high in precision, and the materials are mostly aluminum alloy and copper alloy.
High surface quality and dimensional consistency are required.
Parts suitable for production:
○ Radiator: such as CPU heat sink, which requires high-precision fins and complex flow channels.
○ Connector: such as plugs and sockets, which require high-precision dimensions and surface finish.
○ Precision structural parts: such as mobile phone housings and camera brackets, which require high precision and light weight.
(5) Mold manufacturing field
Mold parts require high precision, high surface quality and complex geometric shapes.
The materials are mostly tool steel and cemented carbide.
Suitable parts for production:
○ Injection molds: such as cavities and cores, which require high precision and complex curved surfaces.
○ Die-casting molds: such as mold cores and sliders, which require high wear resistance and heat resistance.
○ Stamping molds: such as upper molds and lower molds, which require high precision cutting edges and surface hardness.
(6) Energy industry field
Energy equipment parts usually require high precision, high strength and corrosion resistance.
Materials include stainless steel, titanium alloys and nickel-based alloys.
Suitable parts for production:
○ Turbine blades: such as gas turbine blades, which require complex curved surfaces and high surface quality.
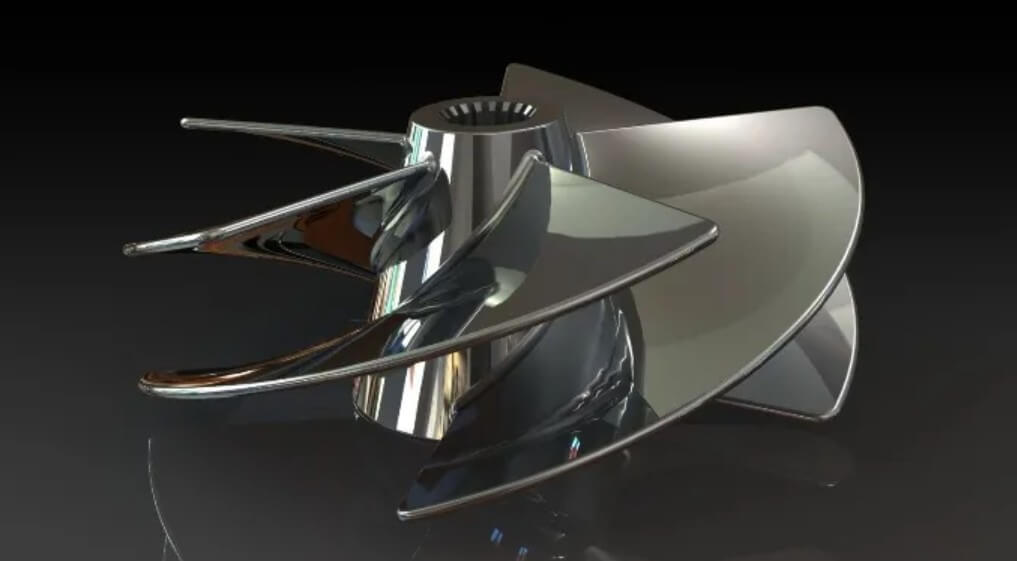
○ Pump body parts: such as impellers and pump casings, which require high precision flow channels and corrosion resistance.
○ Valve parts: such as valve bodies and valve cores, which require high-precision matching and sealing.
8.Advanced precision CNC milling technology
(1) Multi-axis machining
1) Definition and characteristics
Multi-axis machining refers to the simultaneous cutting of multiple directions (usually more than 3 axes) by CNC machine tools.
Common multi-axis machine tools include four-axis and five-axis CNC milling machines.
2) Advantages
○ Complex surface machining: It can complete the machining of complex surfaces in one go, reducing the number of clamping times.
○ High precision: High-precision machining is achieved through multi-axis linkage, reducing error accumulation.
○ High efficiency: Shorten machining time and improve production efficiency.
3) Application scenarios
○ Aerospace: Machining of complex curved surface parts such as turbine blades and engine parts.
○ Mold manufacturing: Machining of complex cavities of injection molds and die-casting molds.
○ Medical devices: Machining of high-precision parts such as artificial joints and surgical instruments.
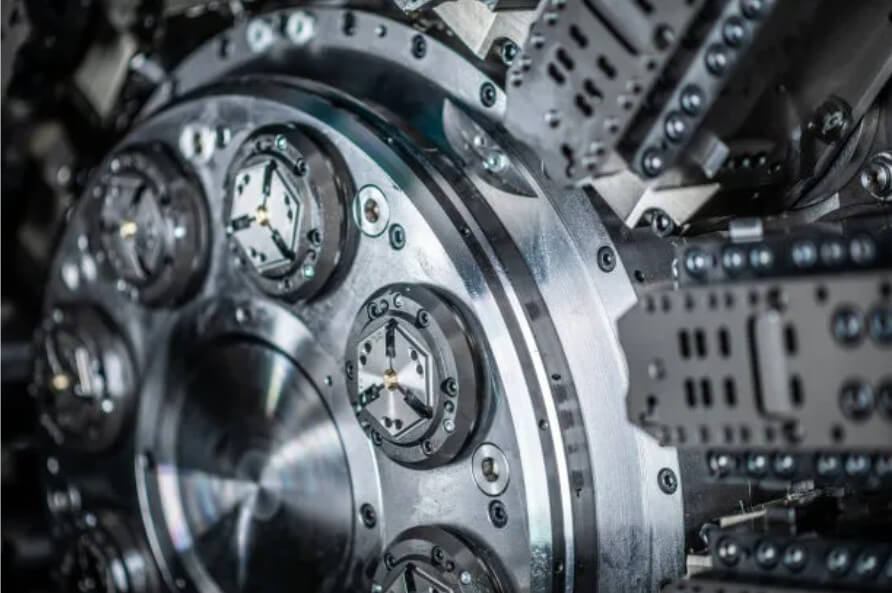
(2) High-speed machining (HSM)
1) Definition and characteristics
High-speed machining refers to milling at high speed (usually more than 10,000 rpm) and high feed rate.
A cutting strategy with small cutting depth and fast feed rate is adopted.
2) Advantages
○ High surface quality: reduce cutting force and thermal deformation, improve surface finish.
○ High efficiency: significantly shorten processing time and improve production efficiency.
○ Suitable for thin-walled parts: reduce vibration and deformation, suitable for processing thin-walled and complex structural parts.
3) Application scenarios
○ Aerospace: processing lightweight and high-strength materials such as aluminum alloy and titanium alloy.
○ Automobile manufacturing: processing complex parts such as engine cylinder block and gearbox housing.
○ Electronic industry: processing small parts such as precision radiators and connectors.
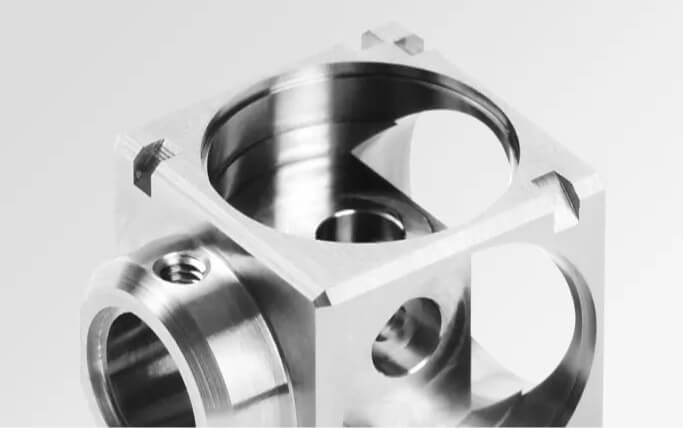
(3) Micro-milling
1) Definition and characteristics
Micro-milling is a CNC milling process specially used for processing tiny parts, with processing accuracy up to micron level.
Use tiny diameter tools (usually less than 1 mm) for high-precision cutting.
2) Advantages
○ High precision: Able to achieve micron-level or even nanometer-level processing accuracy.
○ Complex shape processing: Suitable for processing small and complex shape parts.
○ Material diversity: Can process a variety of materials such as metals, plastics, and ceramics.
3) Application scenarios
○ Medical devices: Processing micro surgical instruments, implants, etc.
○ Electronics industry: Processing precision parts such as micro connectors and sensors.
○ Optical devices: Processing optical components such as micro lenses and prisms.
9.Summary
Precision CNC milling technology has become an indispensable core technology in modern manufacturing with its high precision, high efficiency and high flexibility.
By rationally selecting equipment, optimizing processing technology and materials, it can meet diverse and high-precision processing needs.
In the future, with the development of multi-axis processing, high-speed processing and intelligent processing technology, precision CNC milling will play an important role in more fields.