High-precision machining solutions for the medical sector: integration of 3D printing and CNC precision machining
The rapid development of personalized medical care has put forward higher requirements for high-precision manufacturing technology, and traditional manufacturing methods are often difficult to balance complex structures and precision,
so there is a need to seek high-precision machining solutions for the medical sector.
In recent years, 3D printing (additive manufacturing) and CNC precision machining (subtractive manufacturing) are the core technologies of the manufacturing industry, providing a new high-precision manufacturing model for the medical industry. So what effect will the integration of these two technologies produce?
This article will explore the advantages of 3D printing and CNC precision machining, integrated manufacturing strategies, and the specific application effects of high-precision machining solutions for the medical sector.
1.Introduction to the principles of 3D printing and CNC precision machining
(1) Principle of 3D printing (additive manufacturing):
3D printing is a manufacturing technology based on digital model files that builds three-dimensional objects by stacking materials layer by layer. Its core principles are as follows:
1) Model design:
Use computer-aided design (CAD) software to create a three-dimensional model to define the shape, size, and structure of the object.
2) Model slicing:
Import the 3D model file into the 3D printing software, and the software will slice the model horizontally into several thin layers to generate 2D contour data for each layer.
3) Material accumulation:
Based on the slicing data, the 3D printer controls tools such as the print head or laser beam to accumulate materials (such as plastic, metal, ceramic, etc.) layer by layer to form a 3D object.
4) Post-processing:
After printing, post-processing steps such as removing support materials and surface treatment may be required to obtain the final product.
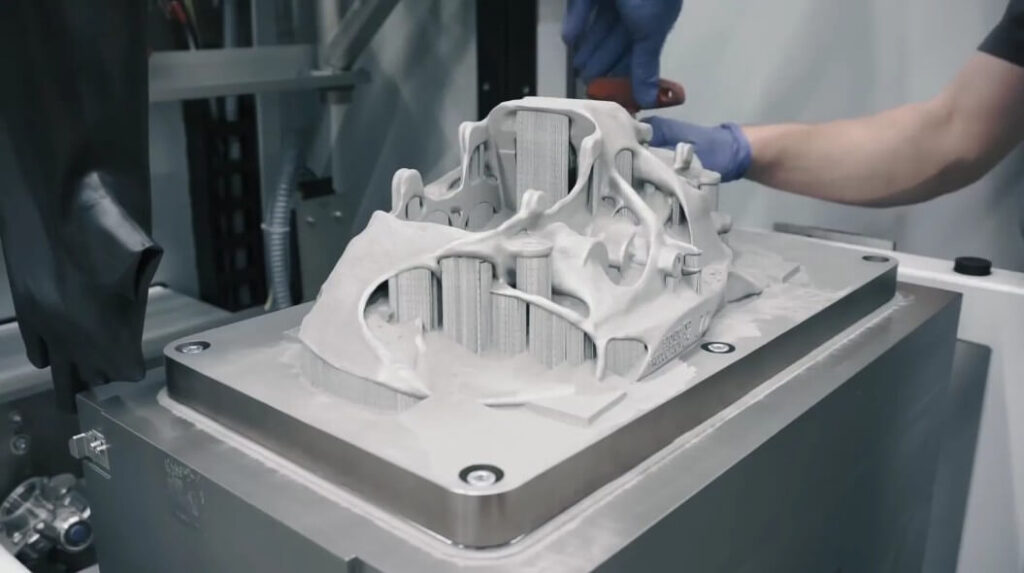
(2) Principle of CNC precision machining (subtractive manufacturing):
CNC precision machining is a technology that uses computer-controlled machine tools to perform cutting, drilling, milling and other operations on materials to produce high-precision parts. Its core principles are as follows:
1) Model design:
Use CAD software to create a 3D model and define the shape, size and processing requirements of the part.
2) Code generation:
Import the 3D model file into CAM (computer-aided manufacturing) software, and the software generates G code that can be recognized by CNC machine tools according to the processing requirements.
3) Machine tool processing:
CNC machine tools control the tool to move along a predetermined path according to G code instructions, and perform precise cutting processing on the workpiece.
4) Quality inspection:
After processing, the parts are inspected using measuring instruments to ensure that their dimensional accuracy and surface quality meet the requirements.
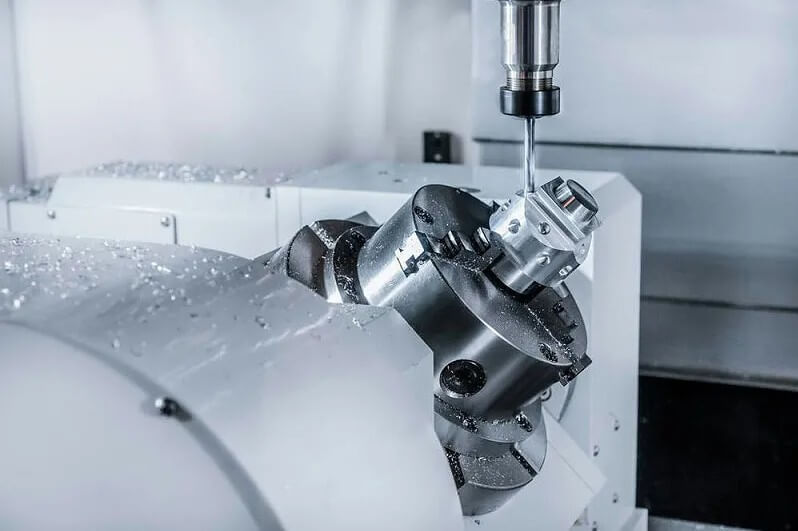
Summary:
3D printing and CNC precision machining are two completely different manufacturing technologies. 3D printing builds objects by stacking materials layer by layer, while CNC machining forms parts by cutting materials to remove excess parts. The two technologies each have their own advantages and limitations, which will be analyzed in detail below.
2.Comparison of technical characteristics and advantages of 3D printing and CNC precision machining
(1) 3D printing:
Advantages:
1) Manufacturing capability of complex geometric structures:
3D printing can easily realize complex structures that are difficult to manufacture with traditional machining, such as hollow mesh bone scaffolds, which helps to lighten and optimize the functions of medical devices.
2) Rapid prototyping:
Compared with CNC machining, 3D printing does not require complex fixtures and tools, and is suitable for personalized customized medical products.
3) High material utilization rate:
3D printing uses a layer-by-layer stacking method to reduce material waste and help reduce manufacturing costs.
4) Compatibility with multiple materials:
Metals (titanium alloys, stainless steel), ceramics and biocompatible polymers can all be used for 3D printing to meet different medical needs.
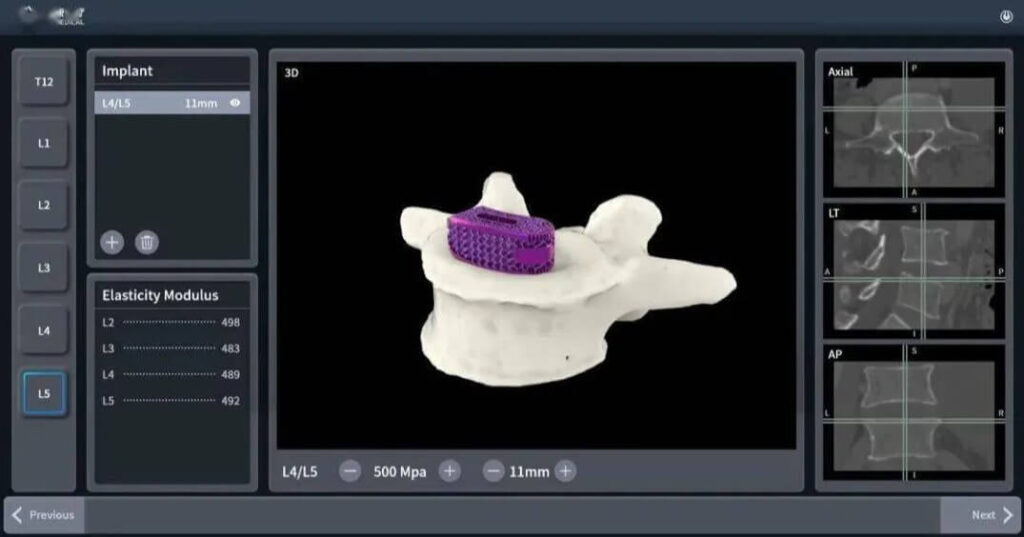
Limitations:
1) Surface finish:
The surface roughness is high and requires subsequent processing.
2) Accuracy and tolerance:
The accuracy and tolerance are relatively low, making it difficult to meet high-precision requirements.
3) Production efficiency:
The production efficiency is low, making it difficult to meet large-scale production needs.
(2) CNC precision machining:
Advantages:
1) Ultra-high precision:
Machining can achieve micron-level or even nanometer-level machining accuracy, meeting the strict requirements of medical devices for dimensional tolerances.
2) Excellent surface quality:
3D printed products usually require additional post-processing, while CNC machining can directly provide a smooth surface and improve the biocompatibility of implants.
3) Stable mechanical properties:
After removing redundant materials, CNC processing will not affect the internal structure of the material, thereby maintaining its original strength and durability.
4) Suitable for high-strength materials:
The processing of high-hardness materials such as titanium alloys and ceramics can be achieved through CNC, while 3D printing may have the problem of insufficient material strength.
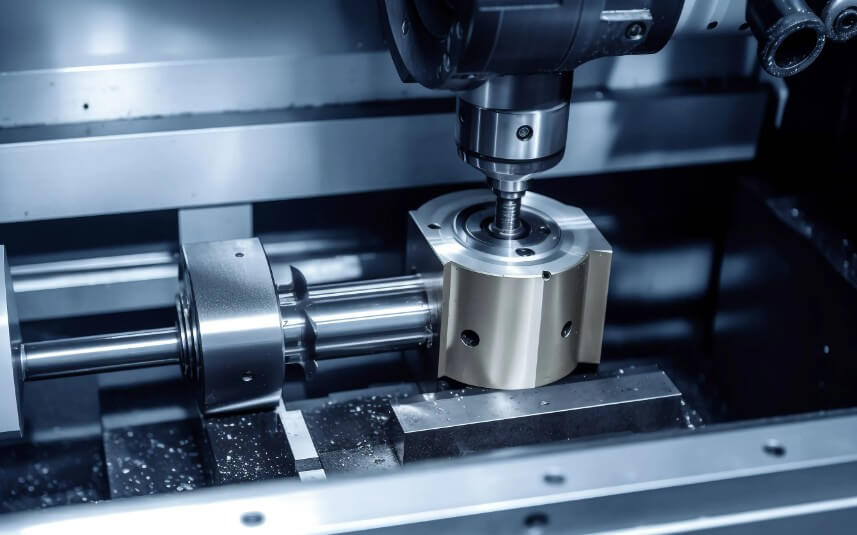
Limitations:
1) Limited design freedom:
It is difficult to manufacture parts with very complex geometries.
2) Material waste:
A large amount of material waste will be generated during the processing process.
3) High cost:
The equipment and processing costs are high.
(3) Complementarity between the two
3D printing can manufacture complex structures, but the surface accuracy is low and CNC post-processing is required.
CNC processing has high accuracy, but is not suitable for manufacturing products with complex internal structures.
Combining the advantages of the two, it can meet the core needs of high-precision machining solutions for the medical sector.
3.High-precision machining solutions for the medical sector: the integrated application strategy of 3D printing and CNC precision processing
The combination of 3D printing and CNC precision processing can give full play to their respective advantages, make up for each other’s shortcomings, and achieve synergistic efficiency.
(1) Hybrid manufacturing method of 3D printing + CNC post-processing
1) Process flow:
3D printing is used to manufacture complex structures, such as orthopedic implants with porous features.
CNC precision processing is used to refine key parts to improve dimensional accuracy and surface finish.
Post-processing technology (such as polishing, electrolytic polishing, and sandblasting) improves the quality of the final product.

2) Typical applications:
● Orthopedic implants:
Use 3D printing to generate bone scaffolds, and then CNC fine-process the joint surface to improve the mobility after implantation.
● Dental implants:
CNC is used to ensure high-precision matching of the implant base to improve the success rate of implantation.
(2) Reverse manufacturing with CNC machining + 3D printing and post-finishing
In some cases, CNC machining first and then 3D printing for local structural optimization is also an important strategy for high-precision machining solutions for the medical sector.
Application cases:
● Customized surgical guides:
CNC precision machining of the skeleton, 3D printing to generate auxiliary structures, and improving adaptability.
● Ophthalmic implants:
CNC manufacturing of high-precision matrix, 3D printing of microstructure modification, and improved biocompatibility.
● Complex medical tools:
For example, the instruments required for minimally invasive surgery can be precisely manufactured by CNC machining, and 3D printing is used to add auxiliary functions, such as handle optimization or anti-slip structure.
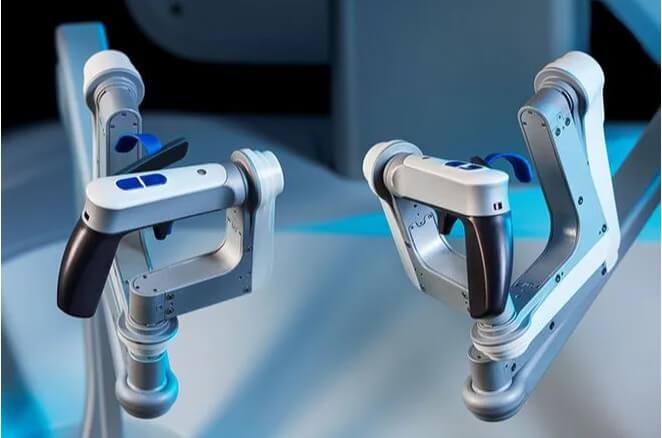
● Preoperative planning models:
3D printing technology can quickly manufacture patient-specific preoperative planning models, and CNC machining can perform additional finishing on these models to ensure the surgeon’s operating accuracy.
4.Analysis of typical application scenarios
(1) Personalized implants
●Case: Personalized hip implants
3D printing: Based on the patient’s CT scan data, 3D prints a hip implant that fully matches the patient’s bone structure.
CNC precision machining: Fine-finishing the 3D-printed implant to improve its surface finish and precision, ensuring its perfect fit with the bone.
●Advantages:
Improve the biocompatibility and service life of the implant.
Reduce surgical time and postoperative complications.
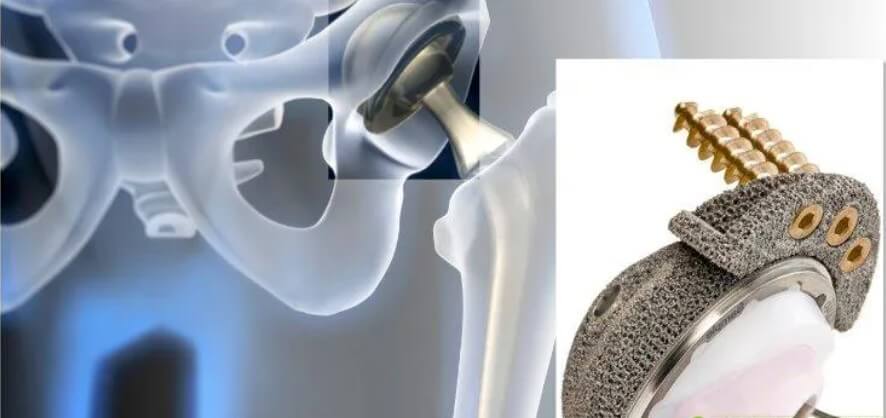
(2) Complex surgical instruments
●Case: Minimally invasive surgical robot
3D printing: Manufacture minimally invasive surgical robot parts with complex internal structures and flow channels.
CNC precision machining: Fine-finishing the 3D-printed parts to improve their precision and surface finish, ensuring their flexibility and precision of movement.
●Advantages:
Improve the precision and safety of surgery.
Reduce surgical trauma and postoperative recovery time.
(3) Biological tissue engineering
●Case: Artificial bone scaffold
3D printing: Using biocompatible materials, 3D print artificial bone scaffolds with porous structures.
CNC precision machining: Fine-finishing the 3D-printed scaffolds to improve their surface finish and precision, promote cell growth and tissue regeneration.
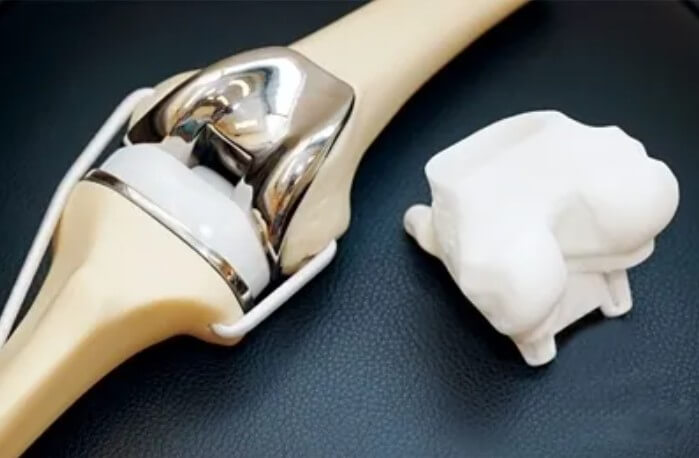
●Advantages:
Promote the regeneration and repair of bone tissue.
Provide new solutions for tissue engineering.
5.Technical challenges
The integrated application of 3D printing and CNC precision machining is a high-precision machining solution that can be implemented in the medical field in recent years. Although it has broad prospects, it also faces many technical challenges:
(1) Software compatibility issues:
It is necessary to develop a software platform that can seamlessly connect 3D printing and CNC machining to achieve the unification of data formats and automation of process flows.
(2) Material compatibility issues:
Different medical applications have strict requirements on materials. It is necessary to ensure that 3D printing and CNC machining materials match to ensure that the final product has excellent biocompatibility.
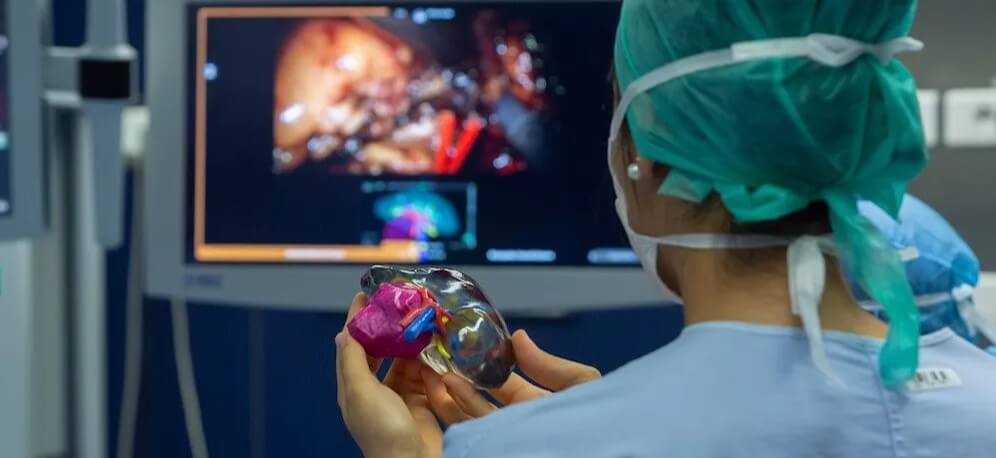
(3) Processing accuracy control:
3D printing layer by layer may affect the accuracy, CNC post-processing requires fine adjustment, especially when manufacturing complex structures, how to ensure accuracy is still an important challenge.
(4) Cost and efficiency balance:
High-precision processing costs are high, and it is necessary to optimize the process to reduce production costs. For example, through intelligent manufacturing technology to improve production efficiency to reduce resource waste.
6.Summary
The proposal of high-precision machining solutions for the medical sector aims to optimize the manufacturing process of medical devices and improve the biocompatibility, complexity and accuracy of products.
Especially in the context of personalized medicine, the physiological structures of different patients are different, and standardized products cannot meet the needs of all patients. Therefore, the combination of 3D printing and CNC processing provides an efficient and accurate solution.