The Precision World of Semiconductor Parts: In-depth Analysis from Classification to Manufacturing
Semiconductor parts refer to parts that meet the requirements of semiconductor equipment and technology in terms of material, structure, process, quality and precision, reliability and stability.
Semiconductor equipment is composed of many different types of parts. So what are these parts? How are they manufactured? This article will deeply analyze the five major classifications, main characteristics and application of precision machining in semiconductor parts, and explore the requirements of parts for the development trend of the semiconductor industry.
1.Main classification and characteristics of semiconductor parts
Semiconductor manufacturing equipment is composed of multiple high-precision parts. The quality of these parts directly affects the yield and process stability of chip production. According to functions and application areas, semiconductor parts can be divided into the following five categories:
(1) Power supply and RF control
1) Main functions:
Provide stable power and RF signals to drive processes such as plasma etching and thin film deposition.
2) Typical parts:
RF power supply, DC power supply, RF matching network, high-frequency transformer.
3) Main features:
●High power, high frequency and high stability are required to ensure lossless signal transmission.
●Good electrical conductivity, usually made of high-purity copper and aluminum alloy materials, and gold-plated or anodized on the surface.
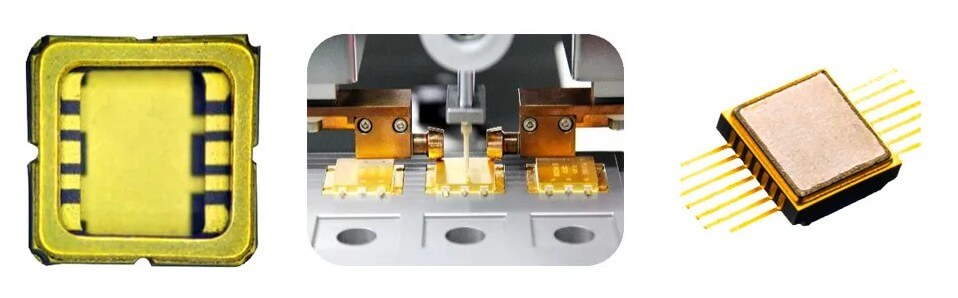
(2) Gas transport
1) Main functions:
●Control gas flow, pressure and purity, used in etching, deposition, lithography and other process links.
2) Typical parts:
●Mass flow controller (MFC), high-precision valve, pressure regulator, gas filter.
3) Main features:
●Requires extremely high flow control accuracy (nanoliter level).
●Use corrosion-resistant materials such as titanium alloy, stainless steel and nickel-based alloy to prevent chemical gas erosion.
●Surface needs to be ultra-precision polished to avoid particle contamination affecting chip manufacturing.
(3) Vacuum control
1) Main functions:
●Maintain a high vacuum state in the semiconductor manufacturing environment to prevent contamination and improve process stability.
2) Typical parts:
●Vacuum pump (dry pump, turbomolecular pump), vacuum valve, pressure sensor, sealing component.
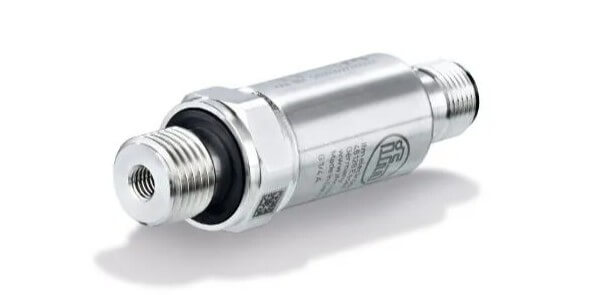
3) Main features:
●Ultra-low leakage rate is required to ensure the stability of high vacuum state.
●High-precision processing technology is used, such as CNC precision processing, laser welding, etc.
●The surface of key sealing components needs to be polished with high precision to reduce microscopic bumps and improve sealing performance.
(4) Temperature control category
1) Main functions:
●Precisely control the temperature of equipment and wafers during the manufacturing process to improve production accuracy and stability.
2) Typical parts:
●Thermocouples, heating plates, cooling systems, temperature control modules.
3) Main features:
●Temperature control accuracy of ±0.1°C or even higher is required.
●High thermal conductivity materials (such as copper, aluminum, ceramics) are used to ensure uniform temperature distribution.
●Combined with CNC micro-machining technology, the accuracy of cooling channels and fluid mechanics optimization design are ensured.
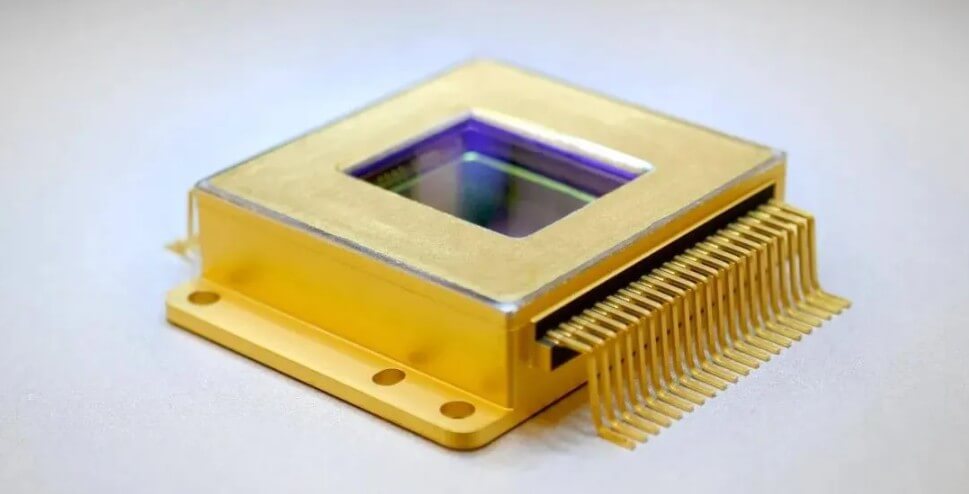
(5) Conveying device category
1) Main functions:
●Precisely transfer wafers and chips in a dust-free environment to improve automated production efficiency.
2) Typical parts:
● Wafer handling robot, track transmission system, vacuum suction cup, robot arm joint.
3) Main features:
● High-precision positioning capability (micrometer level) is required.
● Lightweight and high-strength materials, such as carbon fiber composite materials, are used to reduce motion inertia and increase speed.
● Combine CNC and multi-axis processing technology to ensure high-precision assembly of joint components.
2.Application of precision machining technology in semiconductor parts manufacturing
In semiconductor parts manufacturing, CNC machining and multi-axis machining technology are core processes, which determine the accuracy, surface quality and consistency of parts.
(1) CNC machining technology
1) Characteristics of CNC machining:
● The error can be controlled within ±1μm to ensure high-precision parts processing.
● Suitable for mass production to ensure part consistency.
● Complex shapes can be processed, such as precision flow channels, tiny threads, thin-walled structures, etc.
2) Typical applications:

(2) Multi-axis machining technology
1) Advantages of multi-axis machining:
● Reduce the number of clamping times and avoid secondary positioning errors.
● Improve efficiency, and multiple angles can be processed in one clamping.
● Suitable for complex three-dimensional structures, such as RF cavities and transmission system joints.
2) Typical applications:

3.Typical case analysis of precision machining semiconductor parts
In order to more intuitively demonstrate the application of precision machining in semiconductor parts manufacturing, this article will analyze multiple cases such as RF cavities, gas flow control valves, vacuum cavities, wafer transfer robots, cooling plates, and precision shaft parts.
Case 1: CNC machining of high-precision RF cavities
Challenges:
● The interior of the cavity needs to be highly conductive, with a surface roughness of < Ra 0.2μm, while ensuring the accuracy of the internal conductive channel to avoid signal loss.
Solution:
● Use 5-axis CNC machining to ensure one-time molding of complex internal and external channels to avoid secondary clamping errors;
● Perform anodizing or gold plating to improve conductivity and surface finish and reduce signal loss.
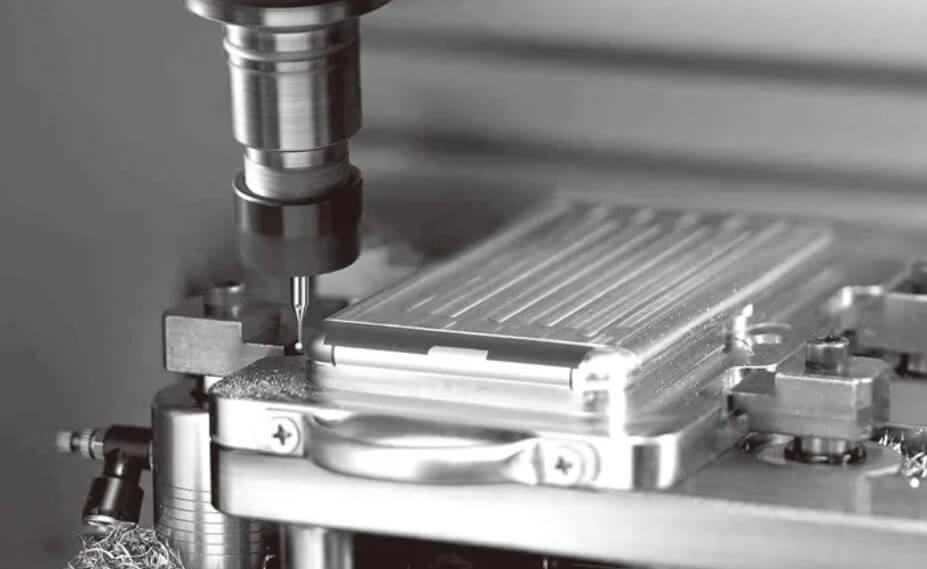
Case 2: Multi-axis machining of high-purity gas flow control valve
Challenge:
● The flow channel finish must be extremely high to prevent particle contamination, while meeting corrosion resistance to ensure long-term stable operation.
Solution:
● Use 4-axis CNC machining to manufacture complex flow channels, combine ultrasonic deburring technology to ensure that there are no particles left in the flow channel, and use PVD coating treatment to improve corrosion resistance.
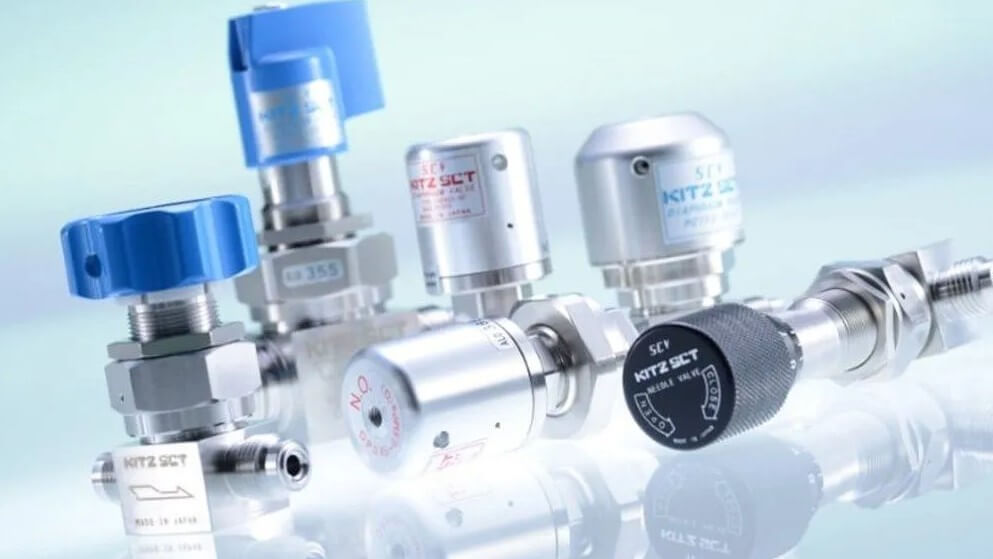
Case 3: High-precision machining of vacuum chambers
Challenge:
● The chamber must achieve ultra-high sealing performance, the leakage rate must be extremely low, and the flange, thread and other structures must be highly matched to ensure assembly accuracy.
Solution:
● Use 5-axis CNC machining to manufacture sealing surfaces and complex flanges and thread structures, and then perform ultra-precision grinding and helium leak detection tests to ensure the sealing and reliability of the vacuum chamber.
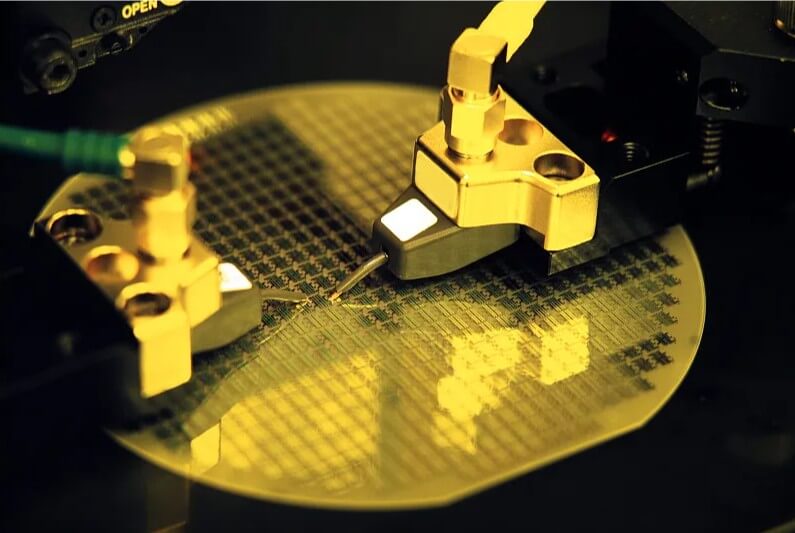
Case 4: High-precision manufacturing of wafer transfer manipulators
Challenges:
● The manipulator needs to maintain a positioning accuracy of ±5μm when running at high speed, and maintain a lightweight design to reduce the impact of vibration.
Solution:
● Use 5-axis CNC machining to manufacture key components, and choose carbon fiber composite materials to improve rigidity while reducing weight;
● And perform high-precision polishing and anti-static coating on the surface to reduce particle adhesion.
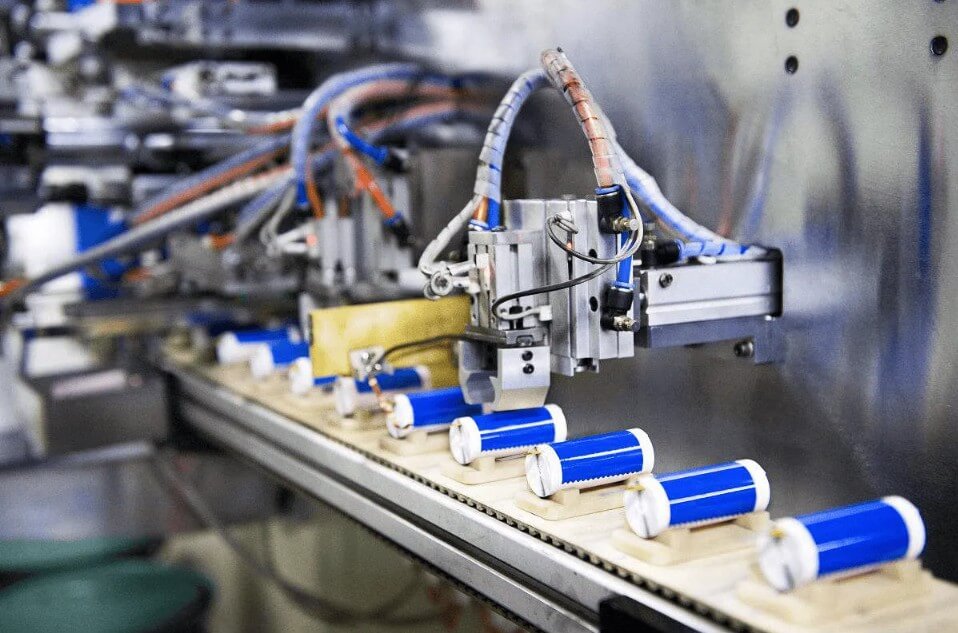
Case 5: Multi-axis precision machining of efficient cooling plates
Challenges:
● The dimensional error of the microchannel needs to be controlled within ±5μm, while ensuring that the coolant flows evenly to ensure efficient heat dissipation.
Solution:
● Use 5-axis CNC machining to manufacture microchannels, and cooperate with laser micromachining technology to ensure high-precision channel structure.
● And perform vacuum brazing and ultrasonic sealing tests to ensure that the cooling plate is leak-free and improve heat dissipation efficiency.
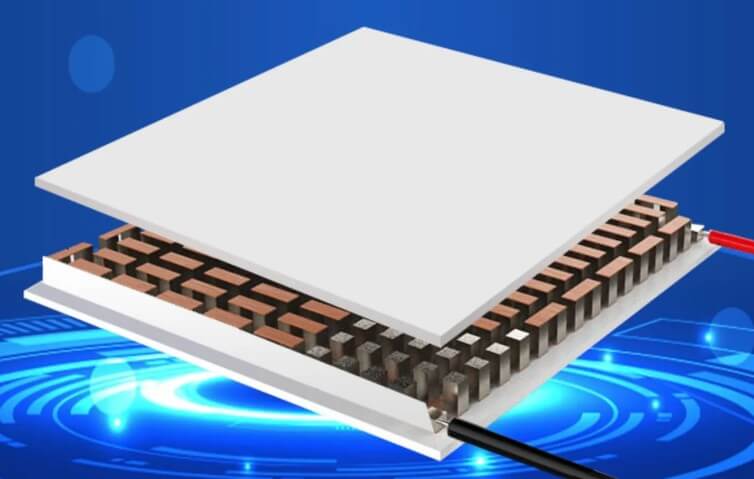
Case 6: CNC machining of precision shaft parts
Challenges:
●Precision shaft parts require high surface accuracy and dimensional tolerance (such as ±0.002mm), and the roundness and coaxiality of the parts must meet extremely high standards.
Solution:
●Use a combination of CNC turning and grinding to machine the shape of shaft parts through high-precision CNC turning, and use grinders to fine-tune the bearing seats and key surfaces to ensure that the roundness and coaxiality requirements meet ±0.001mm, and the surface roughness is less than Ra 0.1μm.
●Use laser scanners to inspect machined parts to ensure that dimensional and shape errors are within the minimum range.
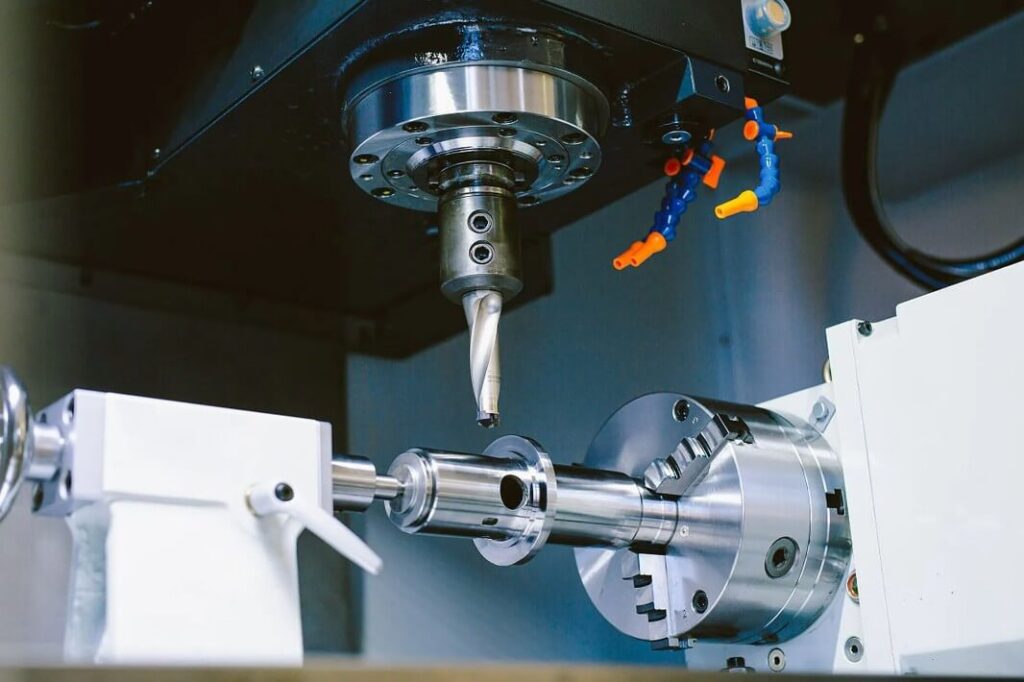
4.Requirements for parts in the development trend of the semiconductor industry
With the continuous development of semiconductor technology, the requirements for semiconductor parts are also getting higher and higher, which are mainly reflected in the following aspects:
(1) Continuous miniaturization of process technology:
As semiconductor process nodes move towards 3nm, 2nm or even smaller sizes, the requirements for part accuracy, cleanliness, reliability, etc. will become more stringent.
(2) Emerging application fields continue to emerge:
Emerging application fields such as artificial intelligence, 5G communications, and the Internet of Things have put forward higher requirements on the performance, power consumption, and size of semiconductor equipment, which also poses new challenges to semiconductor parts.
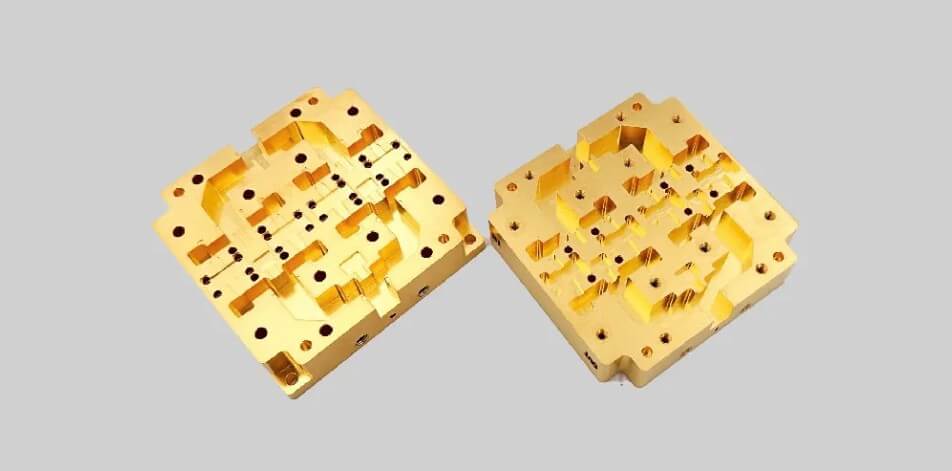
(3) Material innovation and process upgrade:
In order to meet higher performance requirements, the semiconductor parts industry needs to continuously develop new materials and advanced manufacturing processes.
(4) Intelligent manufacturing and green manufacturing:
With the advent of the Industrial 4.0 era, intelligent manufacturing and green manufacturing have become important development directions for the semiconductor parts industry.
5.Summary
As the basic support of the semiconductor industry, the importance of semiconductor parts is self-evident. With the continuous development of semiconductor technology, the requirements for semiconductor parts are also getting higher and higher. As a key technology for semiconductor parts manufacturing, precision machining technology will play a more important role in the future.