A comprehensive analysis of pneumatic solenoid valves: principles, classification and applications
Pneumatic solenoid valves are an automatic control component used to control the flow direction of compressed air. They are widely used in industrial automation, medical equipment, automobile manufacturing and aerospace.
It relies on the electromagnetic coil to generate a magnetic field to drive the valve core to move, thereby controlling the on-off and direction of the airflow. As an indispensable core component in modern industrial control systems, the working principle, classification, application and production and processing methods of pneumatic solenoid valves are crucial to their performance and reliability.
This article will comprehensively introduce the basic principles, classification, main applications, selection and maintenance methods of pneumatic solenoid valves, and explore their production and processing technology to help readers have a deeper understanding of this important component.
1.Basic principles of pneumatic solenoid valves
(1) Structural composition
Pneumatic solenoid valves are mainly composed of the following parts:
1) Electromagnetic coil: generates a magnetic field by energizing to drive the valve core to move.
2) Valve body: used to fix the valve core, with a flow channel structure inside to control the direction of the airflow.
3) Valve core: moves under the action of the magnetic field to control the opening and closing of the air path.
4) Spring: used for resetting, so that the valve core returns to its initial position after power failure.
5) Seal: ensures valve sealing and prevents gas leakage.
(2) Working principle
The working principle of pneumatic solenoid valve is based on electromagnetic force to control the gas circuit switch. Common working modes include:
1) Direct-acting type: the electromagnetic coil directly pushes the valve core to open or close the valve.
2) Pilot-operated type: the solenoid valve controls the pilot air flow and uses the air pressure difference to drive the main valve core to move.
3) Composite type: combines the characteristics of direct-acting type and pilot-operated type, suitable for more complex control scenarios.
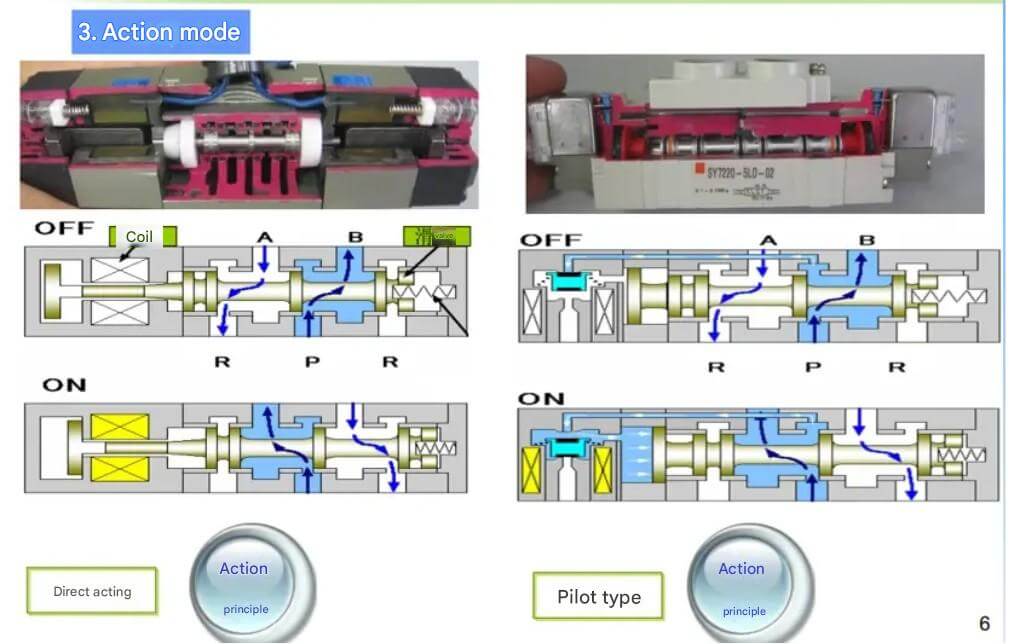
(3) Control method
There are two main control methods for pneumatic solenoid valves:
1) Normally open type: when there is no current, the valve is in the open state and closes after power is turned on.
2) Normally closed type: when there is no current, the valve is in the closed state and opens after power is turned on.
2.Classification of pneumatic solenoid valves
(1) Classification by working principle
1) Direct-acting solenoid valve: suitable for low-pressure and low-flow scenarios, with fast response speed.
2) Indirect pilot solenoid valve: suitable for high-pressure and high-flow systems, with low energy consumption.
3) Compound solenoid valve: suitable for scenarios with large pressure changes, combining the advantages of two valves.
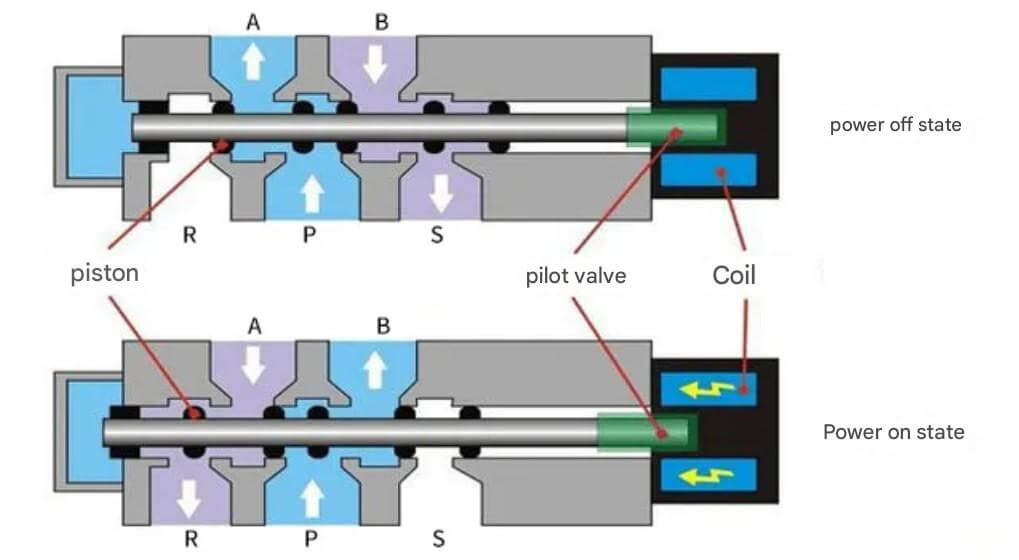
Working principle of pneumatic solenoid valve
(2) Classification by number of channels
1) 2/2-way valve: two ports, controlling gas switches.
2) 3/2-way valve: three ports, usually used for single-acting cylinders.
3) 4/2-way valve and 5/2-way valve: used for double-acting cylinders, controlling bidirectional gas flow.
(3) Classification by voltage type
1) Direct current (DC) solenoid valve: common voltages are 12V and 24V, suitable for low-power applications.
2) Alternating current (AC) solenoid valve: common voltages are 110V and 220V, suitable for high-power applications.
3.Characteristics of pneumatic solenoid valves
(1) Electromagnetic control:
The electromagnetic coil is energized to generate a magnetic field to move the valve core, thereby realizing the on/off and direction control of the airflow.
(2) Fast response:
Compared with mechanical valves, the switching speed of solenoid valves is faster, reaching milliseconds.
(3) Compact structure:
Small size, small footprint, easy to integrate into various automation equipment.
(4) Low energy consumption:
When working, it only consumes electricity when switching, and low energy consumption when maintaining the state.

(5) Strong adaptability:
It is suitable for different environments such as high temperature, high humidity, high pressure, and low pressure, and can withstand certain harsh working conditions.
(6) Multiple control modes:
It can realize multiple control modes such as normally open, normally closed, single electric control, and dual electric control to meet different application requirements.
4.Advantages of pneumatic solenoid valves
(1) High degree of automation:
It can be integrated with control systems such as PLC and single-chip microcomputer to realize remote automatic control and improve production efficiency.
(2) Long service life:
Due to the use of gas drive, compared with hydraulic or electric valves, it has less wear and tear and longer service life.
(3) Low maintenance cost:
The internal structure is relatively simple, easy to disassemble and maintain, and the maintenance cost is low.
(4) High safety:
The pneumatic system does not generate electric sparks and is suitable for explosion-proof occasions, such as chemical, petroleum and other industries.
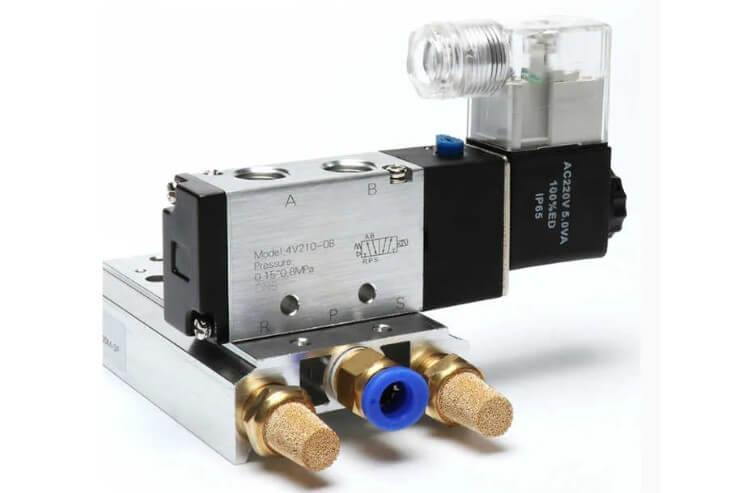
(5) Environmental protection and cleanliness:
Gas is used as a driving force and does not cause pollution. It is suitable for industries with high environmental requirements such as food, medical, and electronics.
(6) Suitable for large flow control:
In some large flow and high frequency applications (such as spraying, pneumatic clamps), it has more advantages than other types of valves.
5.Disadvantages of pneumatic solenoid valves
(1) High requirements for air source:
A stable compressed air supply is required, and the quality of the air source (such as air pressure and dryness) will directly affect the working state of the valve.
(2) Susceptible to pollution:
If the air source contains moisture or impurities, it may cause the valve core to jam or the seal to fail, and an air filtration system is required.
(3) Limited control accuracy:
Compared with electric valves, pneumatic solenoid valves have lower flow control accuracy and are not suitable for precise metering control.
(4) Limited working pressure range:
Usually suitable for medium and low pressure systems, not suitable for ultra-high pressure occasions (such as hydraulic control systems).
(5) The electromagnetic coil may heat up:
Long-term continuous operation may cause the coil to heat up, affecting performance and even shortening service life.
6.Production and processing of pneumatic solenoid valves
(1) Material selection
1) Stainless steel: corrosion-resistant, suitable for high-demand environments.
2) Aluminum alloy: light weight, suitable for general industrial applications.
3) Brass: good conductivity, suitable for electrical control systems.
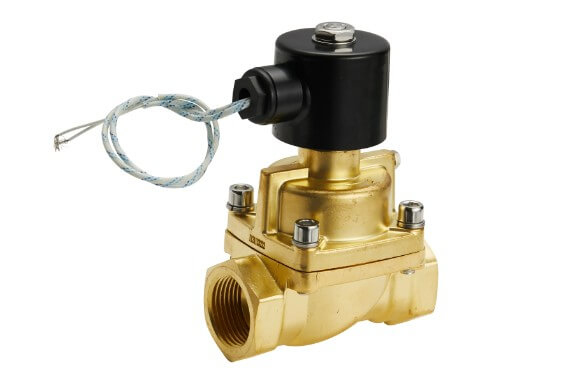
(2) Precision machining
CNC machining is a key process in the manufacture of pneumatic solenoid valves, with the following advantages:
1) High precision: ensure the machining accuracy of the valve core and valve body, and reduce gas leakage.
2) High efficiency: automated processing, improve production efficiency, and reduce labor costs.
3) Consistency: ensure the quality stability of each batch of products.
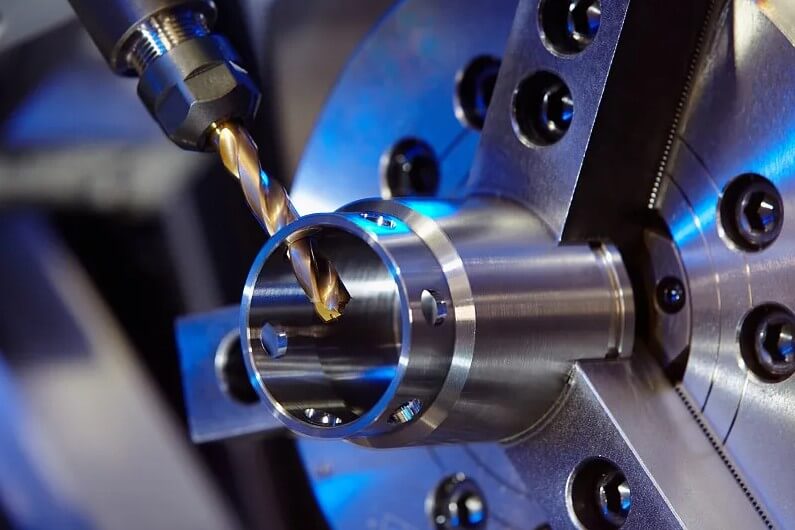
(3) Assembly process
1) Automated assembly line: reduce human errors and improve production efficiency.
2) Manual assisted assembly: used for high-precision or small-batch production.
(4) Quality inspection
1) Pressure test: ensure that the valve operates normally within the working pressure range.
2) Sealing test: check for small leaks.
3) Durability test: simulate long-term use environment and evaluate product life.
(5) Surface treatment
1) Electroplating: improve corrosion resistance.
2) Spraying: enhance appearance and protective performance.
3) Anti-corrosion treatment: suitable for special environments, such as the chemical industry.
7.Main application areas of pneumatic solenoid valves
(1) Industrial automation
1) Robotic arm:
On the automated production line, pneumatic solenoid valves are used to control the pneumatic actuators of the robot arm, enabling it to accurately grasp, move and release workpieces, thereby improving production efficiency.
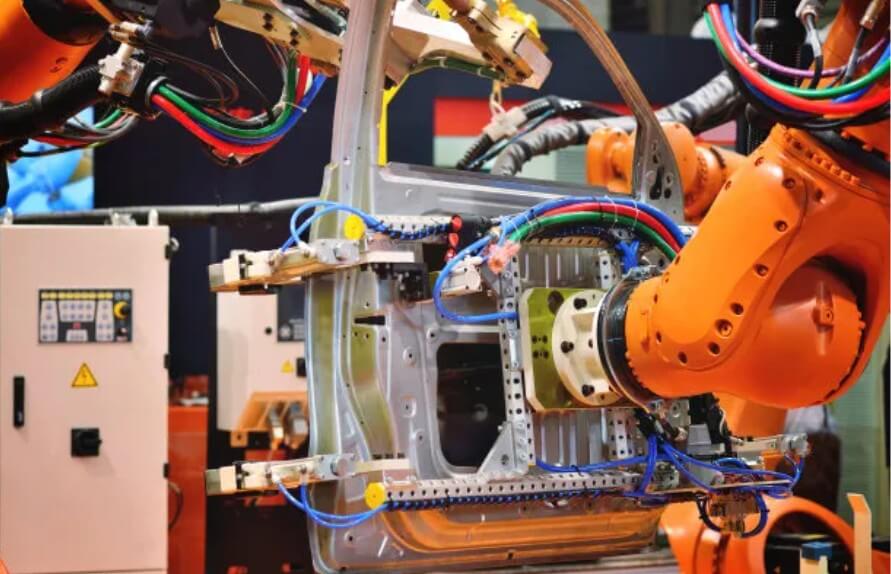
2) Pneumatic clamps:
Used to fix and position workpieces. The opening and closing of the clamps are controlled by pneumatic solenoid valves to ensure processing accuracy.
3) Packaging equipment:
On the automated packaging line, pneumatic solenoid valves control the movement of the cylinders to complete packaging, packaging and handling.
(2) Medical equipment
1) Ventilator:
Control the flow of oxygen and air to ensure that patients receive adequate oxygen supply.
2) Blood analyzer:
Used to control the flow of reagents and samples to ensure the accuracy of the experiment.
3) Laboratory automation equipment:
In liquid handling systems, pneumatic solenoid valves control the air path to achieve precise proportioning.
(3) Automotive industry
1) Spraying equipment:
Control the air pressure of the spray gun to achieve uniform spraying and improve the quality of automotive coatings.
2) Transmission system:
In automatic transmissions, pneumatic solenoid valves are used to switch gears and optimize power output.
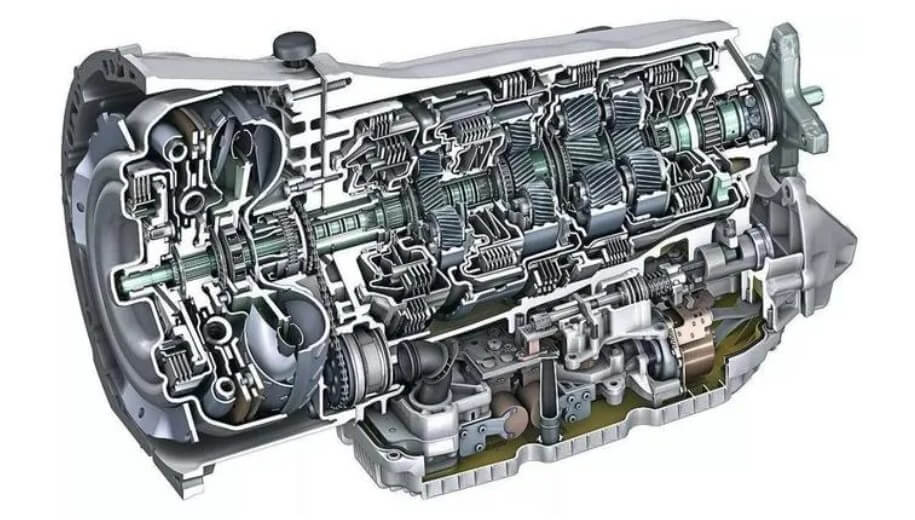
3) Air suspension system:
Used to adjust the height of the car and improve driving stability and comfort.
(4) Aerospace
1) Landing gear control:
Control the flow of the hydraulic system during takeoff and landing to ensure reliable retraction and extension of the landing gear.
2) Fuel delivery system:
Precisely control the fuel supply to improve fuel efficiency.
3) Cabin pressure regulation:
Control the cabin air pressure to ensure the comfort of pilots and passengers.
(5) Food and packaging industry
1) Filling equipment:
Control the liquid flow to ensure that the filling amount of each container is consistent.
2) Packaging machinery:
Pneumatic solenoid valves control the pneumatic components of the sealing equipment to ensure that the packaging is firm.
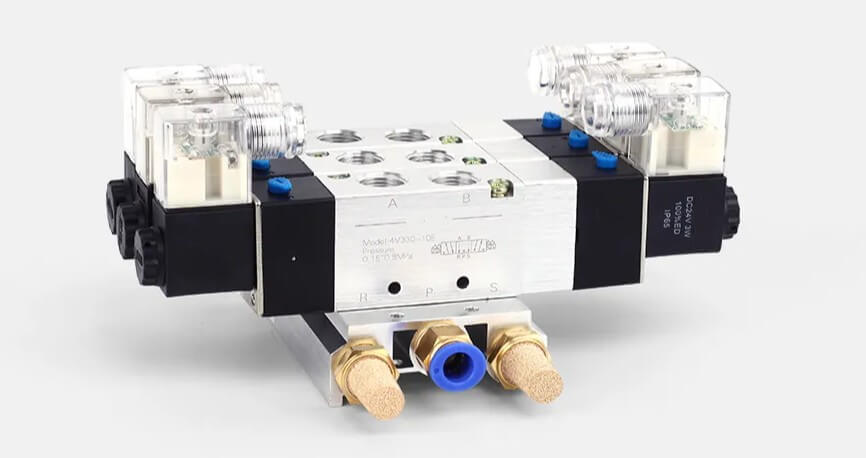
3) Sorting system:
Used to control the pneumatic push rod to realize automatic sorting of food packaging.
(6) Chemical and environmental protection industry
1) Exhaust gas treatment system:
Control the direction of air flow to ensure that polluted gases are effectively filtered and discharged.
2) Chemical reaction equipment:
Used to accurately control the flow of different chemical substances and improve reaction efficiency.
3) Water treatment equipment:
Control the flow of water and gas to achieve purification, filtration and other functions.
8.Selection and maintenance of pneumatic solenoid valves
(1) The following factors need to be considered when selecting pneumatic solenoid valves:
1) Working pressure: Different valves are suitable for different air pressure ranges.
2) Flow requirements: The flow rate determines the diameter of the valve.
3) Response speed: For high-speed control systems, it is necessary to select a solenoid valve with a short response time.
4) Medium characteristics: Different gases (such as oxygen and nitrogen) have different requirements for valve materials.
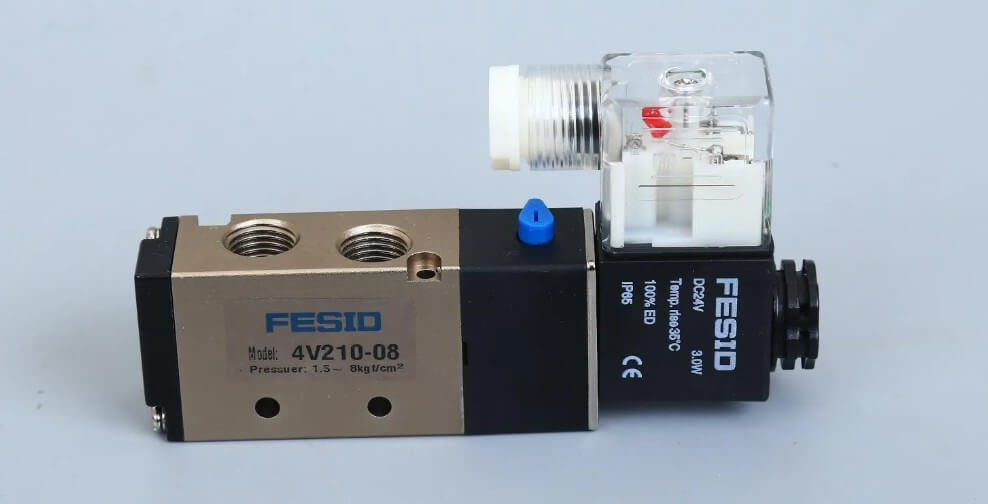
(2) Maintenance and common troubleshooting
1) Solenoid coil failure: Check the voltage and resistance to avoid overheating and burning.
2) Valve core stuck: Clean the inside regularly to avoid impurities accumulation.
3) Leakage problem: Check whether the seal is damaged or aged.
4) Slow response: Check whether the solenoid coil current is stable and ensure that the air pressure is sufficient.
9.Conclusion
Pneumatic solenoid valves play a key role in modern industry. Their working principle, classification, application field and maintenance methods have an important impact on their performance.
At the same time, the production and processing methods directly determine the quality and life of pneumatic solenoid valves. The development of precision manufacturing technologies such as CNC machining has continuously improved the performance, accuracy and reliability of pneumatic solenoid valves.
In the future, with the improvement of industrial automation, the application scope of pneumatic solenoid valves will be more extensive.