Fluid control valve working principle, type characteristics and application details
Fluid control valves are important equipment in industrial automation, petrochemical, energy management and water treatment systems. Their function is to regulate and control the flow, pressure and direction of fluids.
With the development of technology, the application scope of fluid control valves is becoming wider and wider, and the requirements for their performance and intelligence are also increasing. Whether in production and manufacturing, energy transmission, or environmental monitoring systems, fluid control valves are indispensable core components.
This article will discuss in detail the basic structure, working principle, type characteristics, key selection parameters and application fields of fluid control valves.
1.Basic structure of fluid control valves
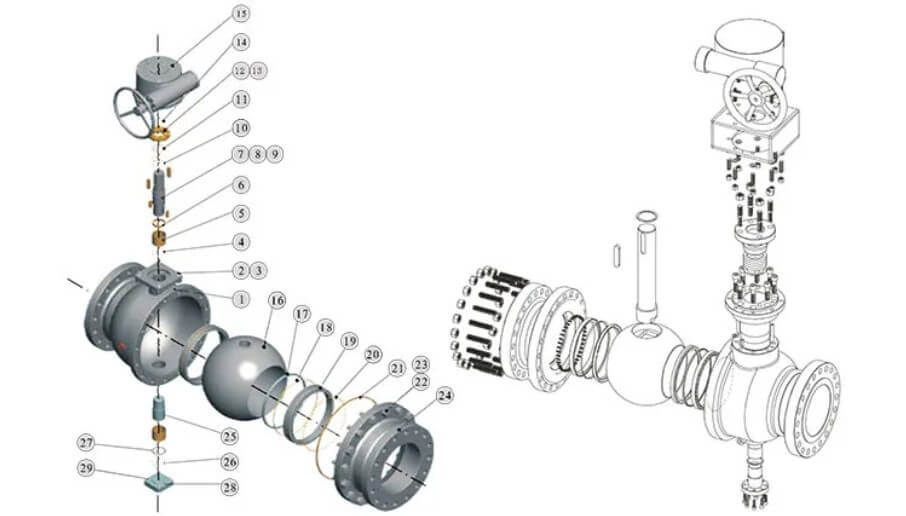
(1) Valve body:
Mainly used to withstand medium pressure and provide fluid channels. It is usually made of metal or plastic to meet different working conditions.
(2) Valve core (valve disc):
Controls the on-off or flow change of fluids and is the core actuator of the valve.
(3) Actuator:
Includes manual, electric, pneumatic or hydraulic drive devices, used to control the opening and closing of the valve core.
Electric actuators are widely used in remote control systems, while pneumatic actuators are mostly used in factory automation control.
(4) Seals:
Ensure that there is no leakage when the valve is closed and improve the sealing performance. Rubber, polytetrafluoroethylene (PTFE) or metal seals are usually used.
(5) Valve stem and connecting parts:
Used to connect the actuator and the valve core and realize the opening and closing action of the valve. Different types of connection methods (such as flange connection, threaded connection, etc.) determine the installation convenience and application scope of the valve.
2.Working principle of fluid control valve
The core function of fluid control valve is to control flow and pressure by adjusting the flow area or changing the flow direction of the fluid. Its working principle can be summarized as follows:
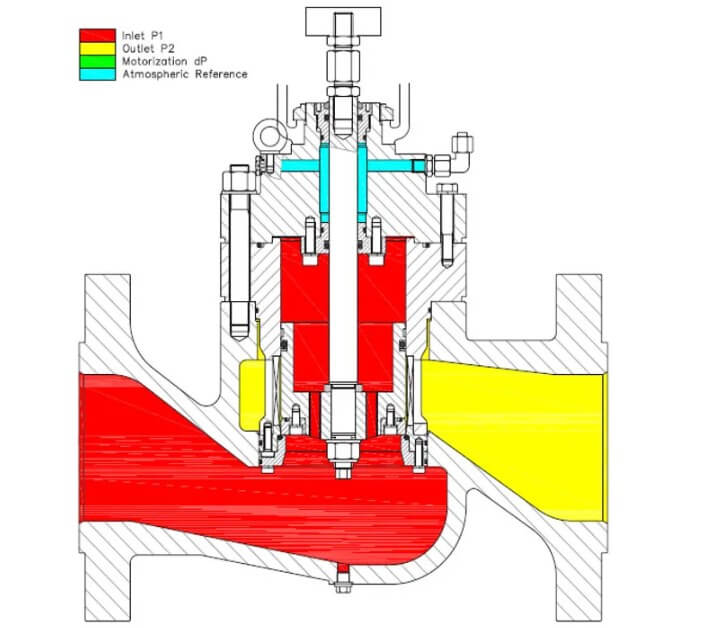
(1) Flow control mechanism:
The flow rate is controlled by changing the position of the valve core to adjust the amount of fluid passing through. Different valve designs determine its flow characteristics, such as linear characteristics, equal percentage characteristics, etc.
(2) Pressure regulation principle:
The throttling effect or pressure compensation device is used to adjust the fluid pressure to meet specific process requirements. For example, in the oil pipeline transportation system, valves need to ensure stable pressure to prevent equipment damage.
(3) Temperature regulation principle:
Some special valves are equipped with temperature control function, which can control the fluid temperature by adjusting the flow rate to ensure the stability of the industrial production process.
(4) Valve switch and execution method:
The valve switch can be controlled by manual, electric, pneumatic or hydraulic methods to achieve automatic control. For example, in high temperature and high pressure environment, remote electric control is usually used to ensure the safety of operators.
3.Main fluid control valve types and characteristics
There are many types of fluid control valves, and different types of valves are suitable for different working conditions. The following are several common types of fluid control valves and their characteristics:
(1) Ball valve
●The ball is rotated 90 degrees to control the on and off of the fluid.
●It has the characteristics of rapid opening and closing, good sealing and low flow resistance.
●It is suitable for high pressure, high temperature occasions and application scenarios that require rapid switching, such as gas pipelines, oil transportation systems, etc.
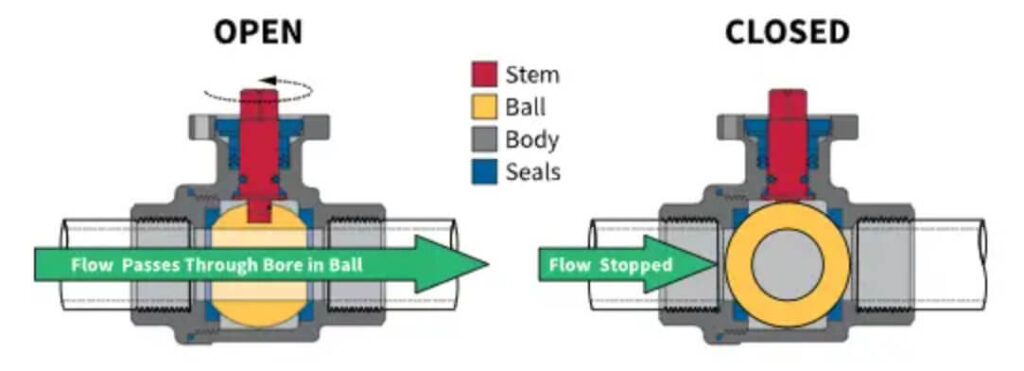
(2) Butterfly valve
●The butterfly plate is rotated to control the fluid flow area.
● Suitable for large-diameter pipes, simple structure and light weight.
● Suitable for low-pressure and medium-pressure systems, such as water supply and HVAC systems.
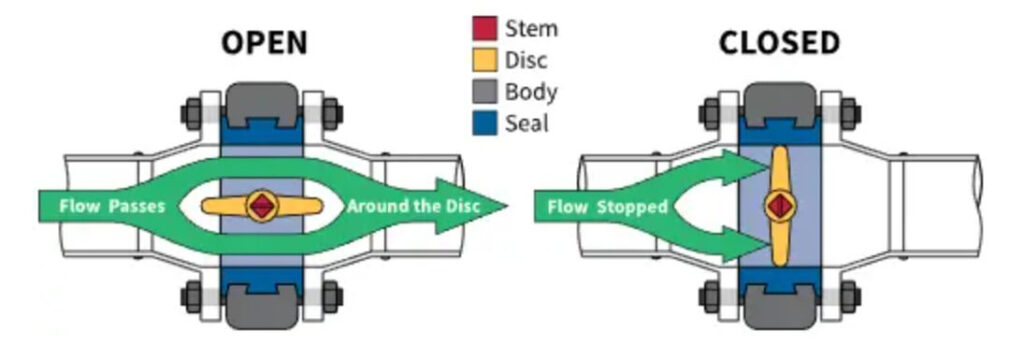
(3) Gate valve
● Open and close the fluid by moving the gate up and down.
● Suitable for high-pressure environments, good sealing performance.
● Suitable for working conditions that require full opening or full closing, not suitable for flow regulation.
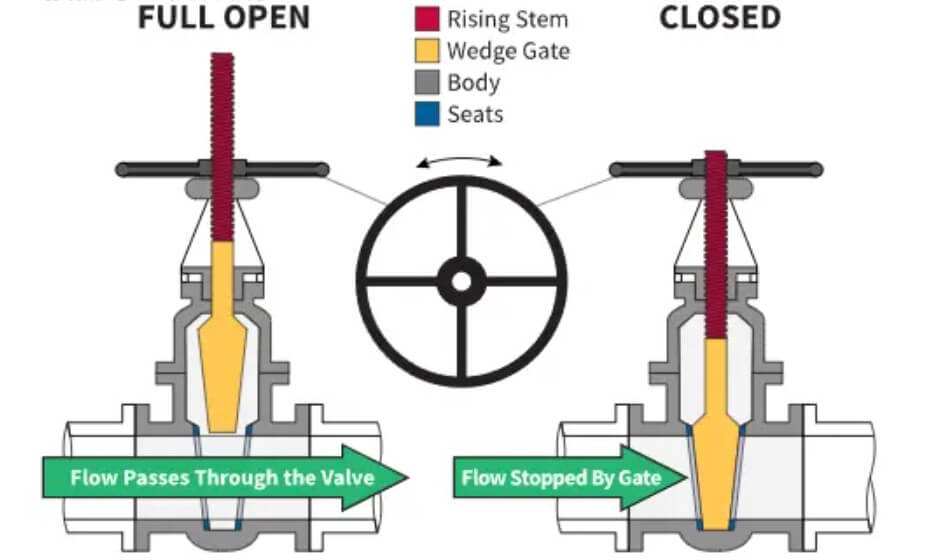
(4) Stop valve
● Uses lifting and lowering valve discs to adjust flow.
● Suitable for occasions that require precise flow control, such as laboratory pipelines.
● However, the flow resistance is large and it is not suitable for the transportation of large flow media.
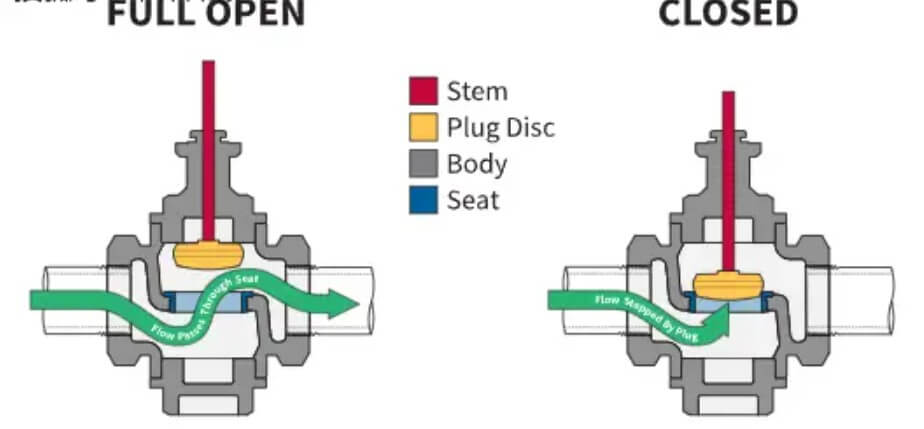
(5) Solenoid valve
The valve is controlled by energizing or de-energizing the electromagnetic coil.
It has a fast response speed and is suitable for automated control systems, such as hydraulic and pneumatic control circuits.
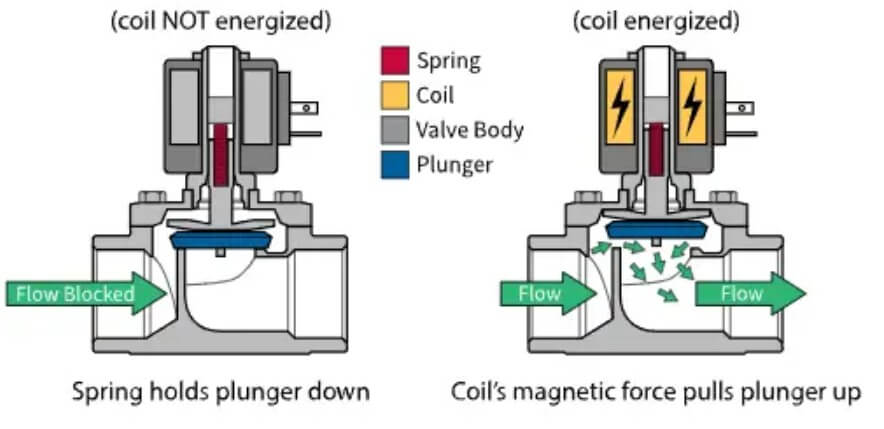
4.Comparison of advantages and disadvantages of different types of fluid control valves
In order to more intuitively understand the performance of different types of fluid control valves, the following table summarizes their main advantages and disadvantages:
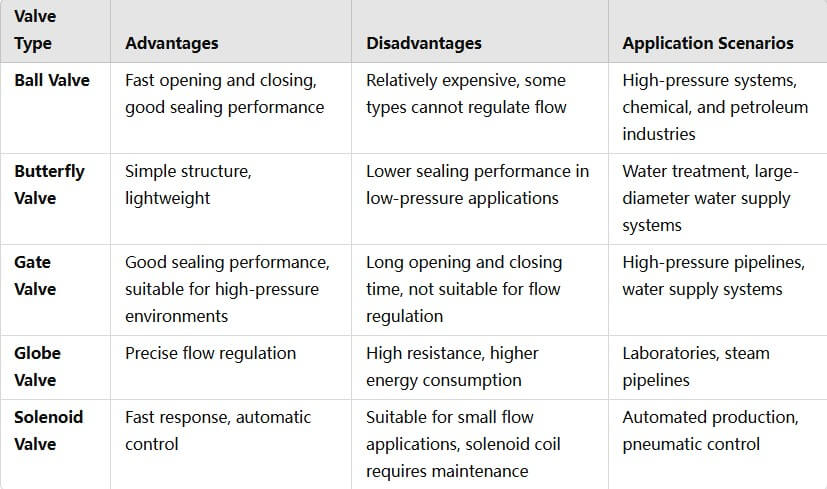
5.Application fields of fluid control valves
Fluid control valves play an irreplaceable role in many industries, such as:
(1) Petrochemical industry:
Used to control the flow of high temperature, high pressure, and corrosive media, such as refineries, chemical plants, etc.
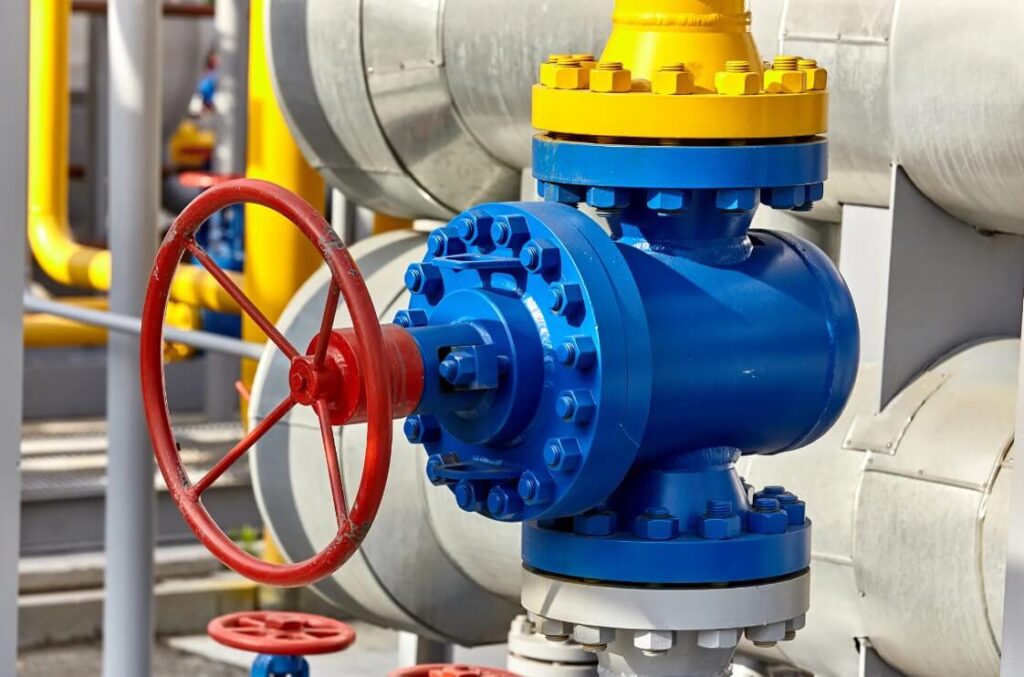
(2) Water treatment system:
Control the distribution and pressure regulation of water flow, widely used in sewage treatment plants, water plants, etc.
(3) Power industry:
Applied in boilers, cooling systems and steam transportation to ensure the safe operation of generator sets.
(4) Shipbuilding and marine engineering:
Used in ship fuel delivery systems and ballast water treatment systems to meet the harsh marine environment requirements.
(5) Food and pharmaceutical industry:
Sanitary valves are required to ensure the sterility and safety of the production process.
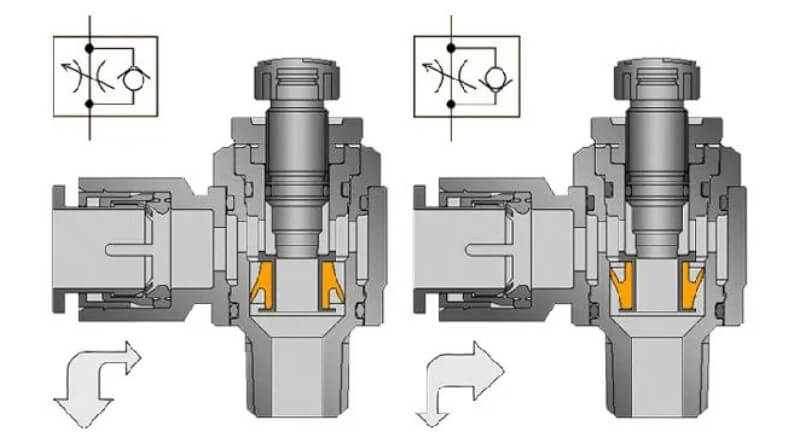
(6) Industrial production:
Widely used in automated assembly lines, hydraulic control systems and mechanical equipment manufacturing to improve production efficiency and system stability.
(7) Intelligent manufacturing:
Intelligent control valves are crucial in Industrial 4.0 factories and can achieve remote monitoring and automatic adjustment.
6.Key parameters for selecting fluid control valves
When selecting fluid control valves, the following key parameters need to be considered:
(1) Medium type:
Liquid, gas, corrosive medium, etc. Different types of fluids will have different requirements for the material and sealing of the valve.
For example, corrosive media require the selection of valves made of anti-corrosion materials, while high-viscosity liquids may require specific valve structures to prevent clogging.
(2) Working pressure and temperature:
The valve needs to be able to withstand the pressure and temperature required by the working conditions. In high temperature and high pressure environments, special materials that are resistant to high temperature and high pressure should be selected.
Such as stainless steel or high alloy steel valves, the sealing material also needs to be able to withstand extreme working conditions.
(3) Flow requirements:
Different types of valves have different flow capacities, and the appropriate diameter should be selected according to the flow requirements.
If the valve diameter is too small, it may cause insufficient flow, while if the diameter is too large, it may increase the equipment cost and affect the adjustment accuracy.
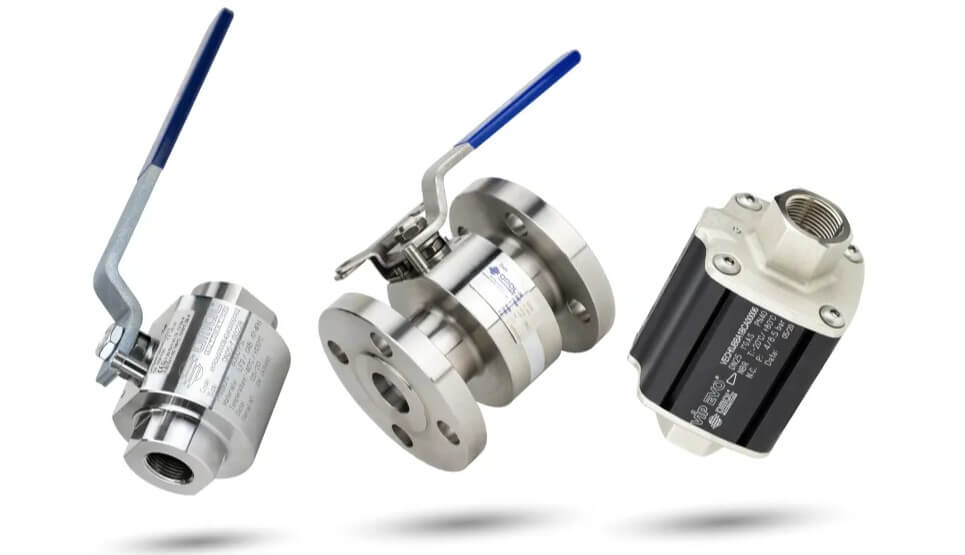
(4) Control method:
Select manual, electric or pneumatic control methods according to automation requirements.
For systems that require remote monitoring, electric or pneumatic valves should be given priority, and combined with intelligent control modules to achieve automated management.
(6) Use environment:
Consider special requirements such as corrosion resistance, high temperature resistance, and explosion resistance. For example, in flammable and explosive environments, explosion-proof electric valves or pneumatic valves should be selected to ensure safe operation.
At the same time, in environments with high humidity or high dust, the sealing and protection level of the valve are also important considerations for selection.
7.Technical features of intelligent fluid control valves
(1) Remote monitoring and control:
Remote adjustment is achieved through sensors and communication modules. Intelligent fluid control valves can be integrated with Internet of Things technology, allowing users to monitor the status of the valve in real time through mobile devices or computers and perform remote operations.
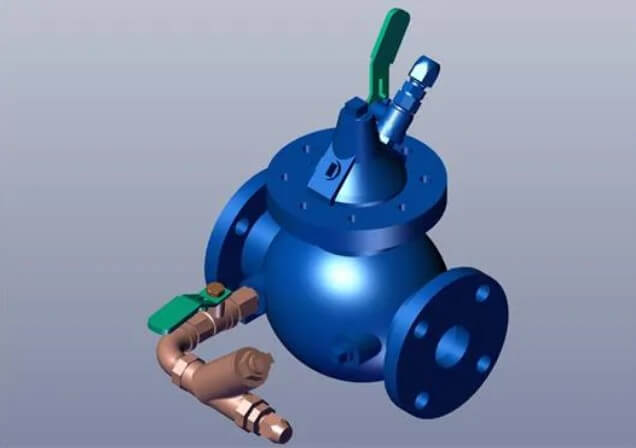
(2) Data analysis and fault prediction:
Combined with big data technology, analyze the operating status of the valve and warn of faults in advance. Modern intelligent control valves are equipped with sensors that can collect temperature, pressure, flow and other data in real time, and analyze the health status of the equipment through cloud computing.
(3) Automatic adjustment and optimization:
Based on real-time data, automatically optimize flow and pressure to improve system efficiency. Intelligent valves can automatically adjust the opening according to preset parameters and sensor feedback to optimize energy consumption.
- Summary
Fluid control valves play a key role in industrial production and automation systems. Traditional control valves are relatively mature in structure and performance, and the emergence of intelligent fluid control valves has brought more possibilities to industrial control systems.