A complete analysis of the structure, manufacturing and application of threaded flanges
In complex industrial piping systems, how to achieve fast and reliable connections has always been the focus of engineers.
With its unique threaded connection method, threaded flanges have become an ideal choice in many scenarios. This article will comprehensively analyze the advantages and limitations of threaded flanges from structure, manufacturing to application, and provide readers with practical reference information.
1.Overview of threaded flanges
(1) Definition
A threaded flange is a flange with a threaded connection structure. It is directly connected to the pipeline or equipment through threads without welding. It is suitable for low-pressure and small-diameter pipeline systems. The design of threaded flanges is to provide a reliable connection method, especially for occasions where welding is inconvenient or unsafe, such as highly flammable and explosive environments.
(2) Function
The main function of a threaded flange is to connect pipelines and equipment so that fluids can be transported smoothly, while having a certain degree of sealing to prevent leakage. Its threaded structure can achieve a firm connection without welding, and is widely used in pipeline systems that require quick installation and disassembly.
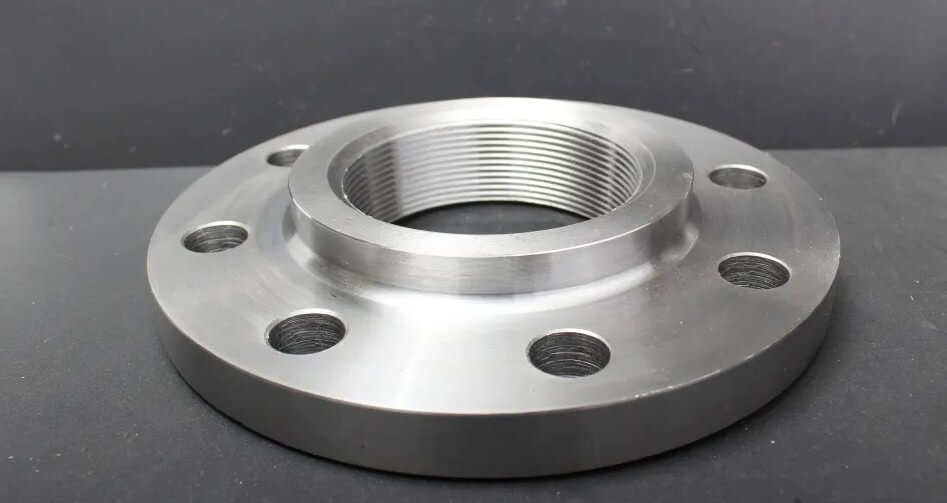
(3) Importance
Threaded flanges play an irreplaceable role in industries such as petroleum, chemical industry, water supply system, and natural gas. Since their connection method does not require welding, it reduces installation time and reduces the impact of high-temperature welding on pipeline materials, making them the first choice for specific industries.
2.Structure and standards of threaded flanges
(1) Basic components
1) Flange body: the main structural part with threaded holes, tightly combined with the pipeline or equipment.
2) Threaded connection part: used to achieve threaded tightening and provide safe and reliable connection.
3) Sealing surface: used to enhance sealing and prevent fluid leakage. The sealing surface usually has a flat surface, a concave and convex surface, a ring connection surface, etc.
4) Bolt hole: Some threaded flanges have bolt holes to facilitate additional reinforcement of the connection and improve safety.
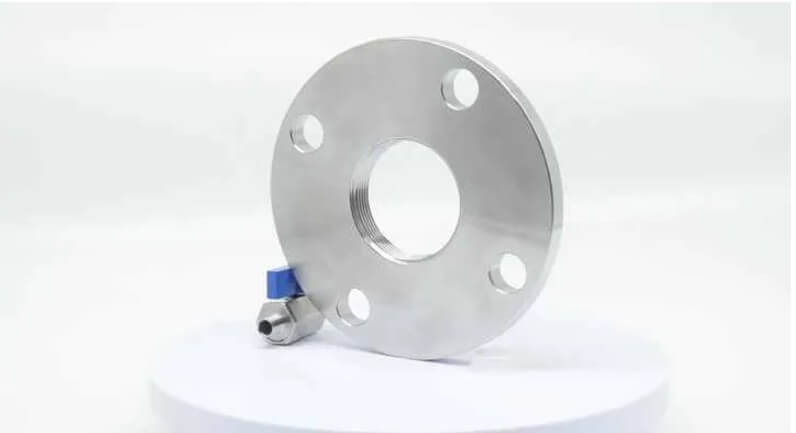
(2) Product specifications and standards
The production of threaded flanges must follow different international and national standards to ensure their quality and compatibility. These standards include but are not limited to:
ANSI (American National Standards Institute): commonly used in pipeline systems in the North American market.
ASME (American Society of Mechanical Engineers): used for mechanical and pressure piping systems.
GB (China National Standard): covers domestic industrial applications in China .
DIN (German Industrial Standard): Applicable to the European market.
JIS (Japanese Industrial Standard): Widely used in the Japanese and East Asian markets.
3.Working principle of threaded flange
Threaded flange mainly relies on threaded connection of pipes and can be installed without welding. Its working principle includes:
(1) Locking by thread:
The internal thread part of the threaded flange matches the external thread of the pipe and forms a firm connection after tightening.
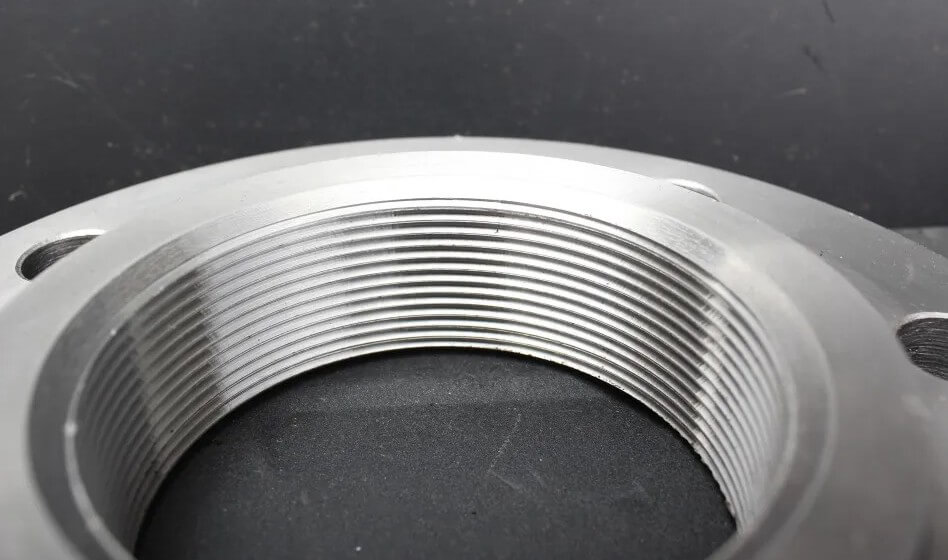
(2) Combined sealing material:
In some cases, it is matched with sealing gaskets or thread sealants to prevent fluid leakage.
(3) Additional reinforcement Method:
Some applications also use bolts or other fasteners to improve the connection strength.
4.Advantages and disadvantages of threaded flanges
(1) Advantages:
●Easy to install and disassemble, reducing construction time.
●Applicable to flammable and explosive environments, no high-temperature welding required.
●Low maintenance cost, easy to replace damaged parts.
●Applicable to highly corrosive environments, stainless steel threaded flanges have strong tolerance in acid and alkali media.
●Compact structure, suitable for installation environments with limited space.
●Not easily affected by temperature, compared with welded flanges, the thermal expansion and contraction of threaded flanges have less effect on their connections.
●Applicable to detachable connection occasions, such as frequently maintained pipeline systems.
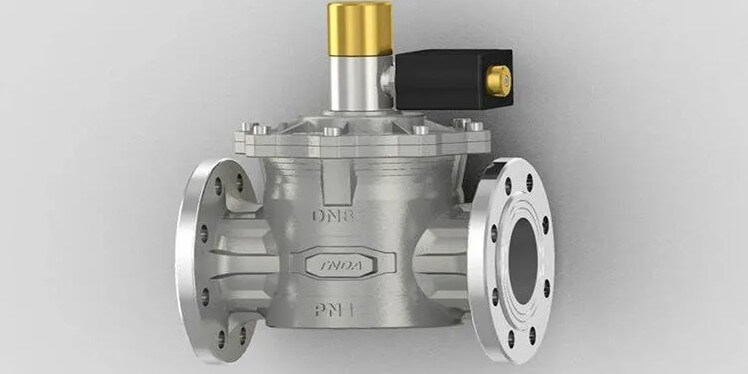
(2) Disadvantages:
●Low pressure bearing capacity, generally suitable for working conditions with pressure ≤2.5MPa.
●Applicable to small-diameter pipes, usually below DN100.
●Long-term use may cause the threads to loosen due to vibration or impact, affecting the sealing performance.
●In high-temperature environments, threaded connections may affect the sealing due to thermal expansion and contraction.
● The thread size needs to be accurately matched during the installation process, otherwise the connection strength may be affected.
5.Manufacturing and quality control of threaded flanges
(1) Material selection
The manufacturing materials of threaded flanges need to have good pressure resistance, corrosion resistance and mechanical properties. Commonly used materials include:
1) Carbon steel (such as A105): suitable for general working conditions, low price and good mechanical properties.
2) Stainless steel (such as 304, 316): strong corrosion resistance, suitable for special environments such as chemical and food processing.
3) Alloy steel (such as F11, F22): suitable for high temperature and high pressure conditions, suitable for the petrochemical industry.
(2) Production process
The manufacturing of threaded flanges involves multiple process steps, including:
1) Casting: The metal is melted and cast into shape, which is suitable for mass production and has relatively low cost. The casting process can produce flanges with complex shapes, but its internal structure may have defects and require further processing and testing.
2) Rough machining: After casting, preliminary machining, such as turning and milling, is performed to remove the rough layer on the surface of the blank and prepare for subsequent fine machining.
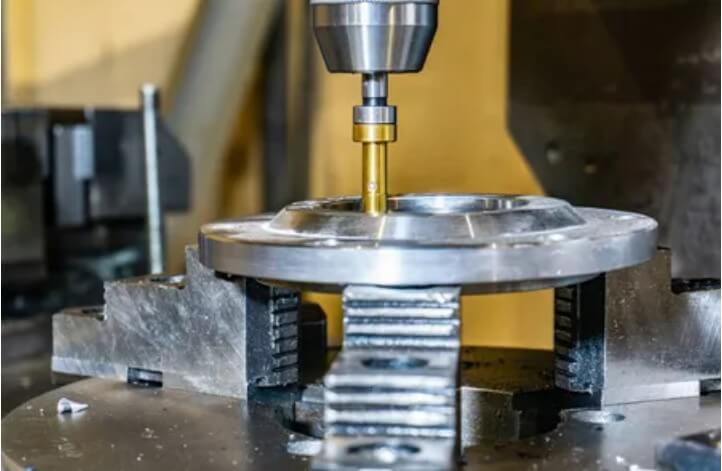
3) Thread machining: Use a thread lathe or special thread machining equipment to ensure the accuracy of the thread size and ensure that the thread matches the pipe.
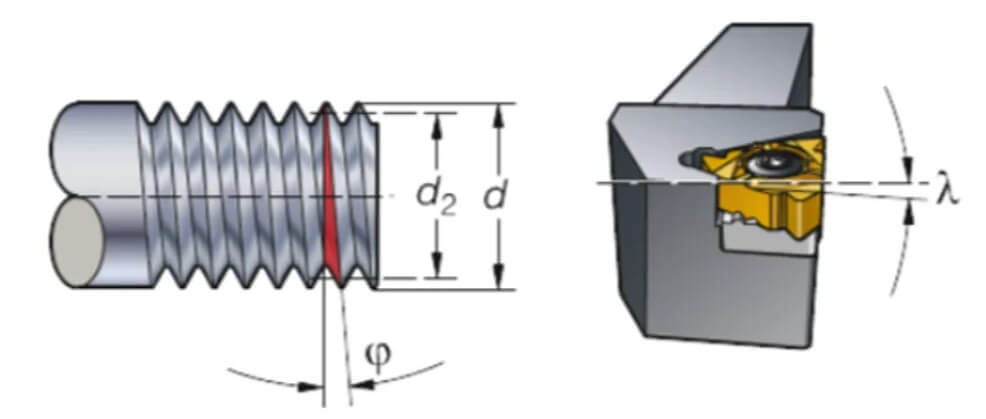
4) Fine machining: Through drilling, fine turning, polishing and other processes, the flange size meets the standard requirements and the surface finish is improved.
5) Deburring: Deburr and chamfer the threads and sealing surfaces to prevent the sealing and connection performance from being affected during installation.
6) Surface treatment: Including galvanizing, painting, phosphating or passivation treatment to improve the corrosion resistance of the flange.
7) Final inspection: Perform dimensional inspection, pressure test, thread matching test, etc. to ensure that the product quality meets the standard.
(3) Key points of quality control
Quality control of threaded flanges includes:
1) Dimension tolerance inspection: Ensure that the flange meets the standard requirements and use measuring tools such as calipers and micrometers for accuracy inspection.
2) Thread accuracy test: Use thread gauge to check accuracy to ensure that the thread and the matching pipe can accurately match.
3) Pressure test: Verify the sealing of the flange under rated pressure, usually using hydraulic test or air pressure test.
4) Standard certification: Ensure that the product complies with international standards such as ISO and ASME to improve market recognition.
6.Application of threaded flanges
(1) Applicable working conditions
1) Low-pressure pipeline system (≤2.5MPa).
2) Corrosive fluid transportation.
3) Pipeline system that requires rapid installation and disassembly.
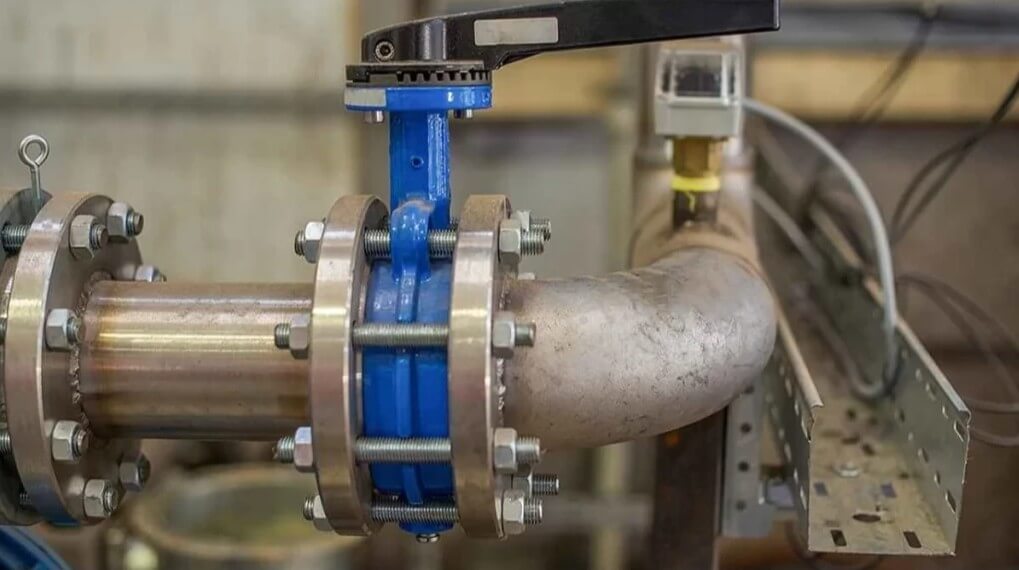
(2) Main application areas
1) Water supply pipeline:
Urban tap water network, rural water supply system, etc., threaded flange can provide reliable connection and facilitate maintenance and replacement.
2) Drainage system:
Applicable to industrial and municipal drainage pipelines to ensure that there will be no leakage problems during sewage transportation.
3) Natural gas transportation:
In low-pressure natural gas transmission pipelines, threaded flanges are widely used, especially in gas pipelines in residential and commercial buildings.
4) Industrial chemical equipment:
Used to connect various chemical liquid delivery pipelines, suitable for the transportation of corrosive media such as acid and alkali solutions.
5) Valve connectors:
Widely used for the installation and connection of valves (such as ball valves, solenoid valves, etc.), so that the pipeline system can flexibly adjust the flow and pressure.
6) Storage tank and container accessories:
Used for the storage tank interface in the petroleum, chemical, food processing and other industries, providing reliable sealing to prevent medium leakage.
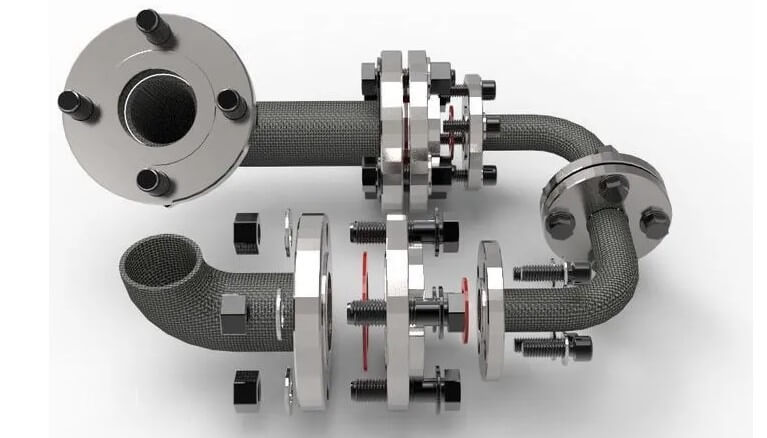
7) Food processing pipelines:
In the food manufacturing industry, threaded flanges are used to transport liquid foods and ingredients, meet hygiene standards, and are easy to clean and maintain.
8) Refrigeration equipment:
In refrigeration and air-conditioning systems, threaded flanges are used for refrigerant delivery pipelines to ensure the sealing and safety of the system.
9) Pharmaceutical production pipelines:
Widely used in the pharmaceutical industry to transport purified water, solvents, etc. to ensure the cleanliness requirements of pharmaceutical production. Threaded flanges provide stable connections in these systems and are easy to maintain and replace regularly.
7.Performance comparison between threaded flanges and other flanges (welded flanges)
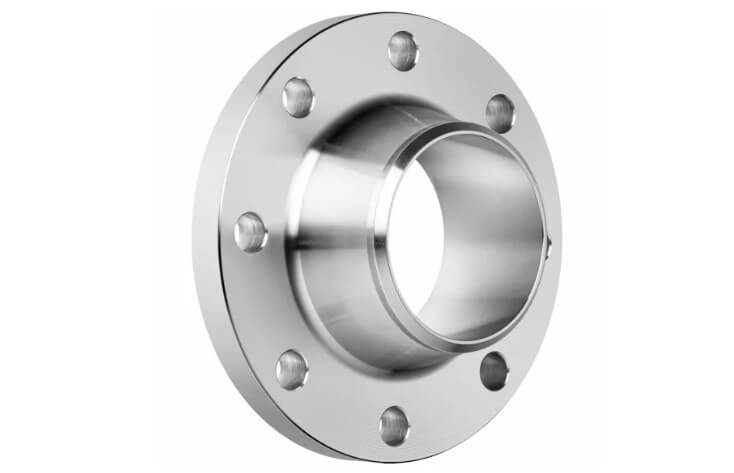
(1) Strength and pressure bearing capacity
The pressure bearing capacity of threaded flanges is relatively low and is suitable for low-pressure occasions (≤2.5MPa), while welded flanges can withstand higher pressures and temperatures and are suitable for high-pressure and large-diameter pipelines.
(2) Applicable media and environment
Threaded flanges are suitable for ordinary liquid and gas transportation systems, while welded flanges are suitable for high-temperature, high-pressure and corrosive fluid environments, such as the petroleum and chemical industries.
(3) Difficulty of installation and maintenance
Threaded flanges are easy to install and do not require welding. They are suitable for fast loading and unloading needs, while welded flanges are complex to install and require welding operations, but have stronger sealing performance.
(4) Cost comparison
The manufacturing and installation costs of threaded flanges are low and are suitable for small projects. Although the initial cost of welded flanges is high, they are suitable for long-term use in high-pressure environments.
8.Conclusion
(1) Advantages and limitations of threaded flanges
Threaded flanges are easy to install and simple to maintain, but their scope of application is limited. They are mainly suitable for low-pressure and small-diameter pipelines.
(2) How to choose the right flange type
High-pressure working conditions: choose welded flanges.
Corrosive environments: choose stainless steel flanges.
Easy to disassemble: choose threaded flanges.