Processing technology and surface treatment technology of hydraulic flow control valve
Hydraulic flow control valve is a key component for controlling fluid flow and direction in hydraulic system, including throttle valve, speed regulating valve, solenoid valve and other types. Its processing accuracy and surface quality directly affect the performance and service life of the valve.
This article introduces the key points of manufacturing technology of hydraulic flow control valve in detail from the two aspects of processing technology and surface treatment, including the processing flow of key parts such as valve body and valve core, as well as surface treatment technologies such as electroplating, oxidation treatment and surface coating.
By optimizing processing technology and surface treatment technology, the performance and reliability of hydraulic flow control valve can be significantly improved, providing guarantee for the efficient operation of hydraulic system.
1.Overview of hydraulic flow control valve
Hydraulic flow control valve is one of the core components in hydraulic system. Its main function is to control the flow, pressure and direction of fluid by adjusting the relative position between valve core and valve body, so as to meet the working requirements of actuator.
With the continuous improvement of industrial automation level, the performance requirements of hydraulic system for flow control valve are getting higher and higher, especially in terms of high precision, high reliability and long life. The performance of hydraulic flow control valve depends not only on its design structure, but also on its processing accuracy and surface quality. Therefore, in-depth research on the processing and surface treatment technology of hydraulic flow control valves is of great significance for improving the overall performance of hydraulic systems.
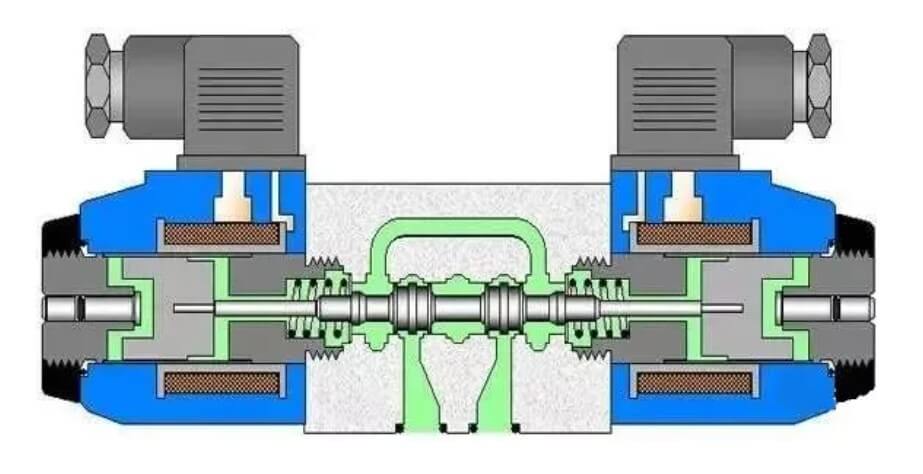
2.Processing technology of hydraulic flow control valves
The main parts of hydraulic flow control valves include valve body, valve core, valve seat and spring, etc. The processing accuracy of these parts directly affects the performance of the valve. The processing technology of valve body and valve core will be introduced below.
(1) Valve body processing
The valve body is the main part of the hydraulic flow control valve. Its inner cavity shape is complex and the processing accuracy requirements are extremely high. The main processes of valve body processing include rough machining, semi-finishing, finishing and deburring.
1) Rough machining
The rough machining of the valve body usually adopts the casting method to manufacture the blank, and then it is preliminarily processed by lathe, milling machine and other equipment to remove most of the excess. The processing focus of this stage is to ensure that the basic shape and size of the blank are close to the design requirements.
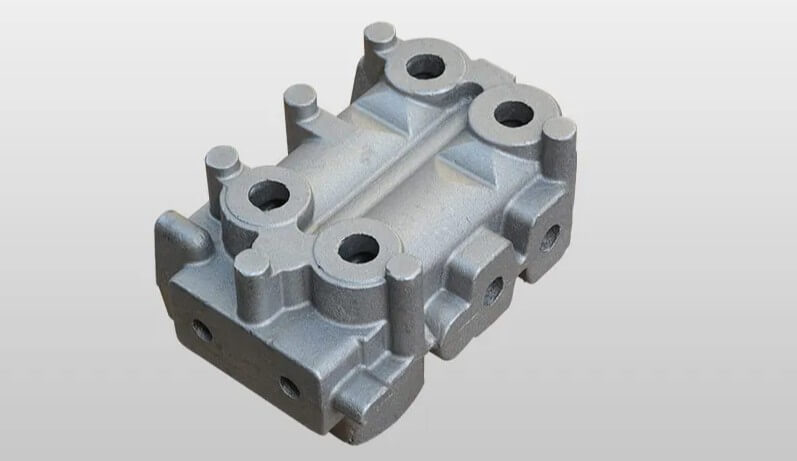
2) Semi-finishing
In the semi-finishing stage, the inner cavity, end face and hole system of the valve body need to be further processed to achieve a certain dimensional accuracy and surface roughness. CNC machine tools are usually used for processing at this stage to ensure the consistency and accuracy of processing.
3) Finishing
Finishing is a key link in valve body processing. High-precision CNC lathes and machining centers are mainly used to perform precision processing on the inner cavity and hole system of the valve body.
The goal of finishing is to ensure that the shape accuracy, dimensional accuracy and surface roughness of the valve body fully meet the design requirements. For example, the roundness and cylindricity of the inner cavity of the valve body and the position accuracy of the hole system need to be strictly controlled.
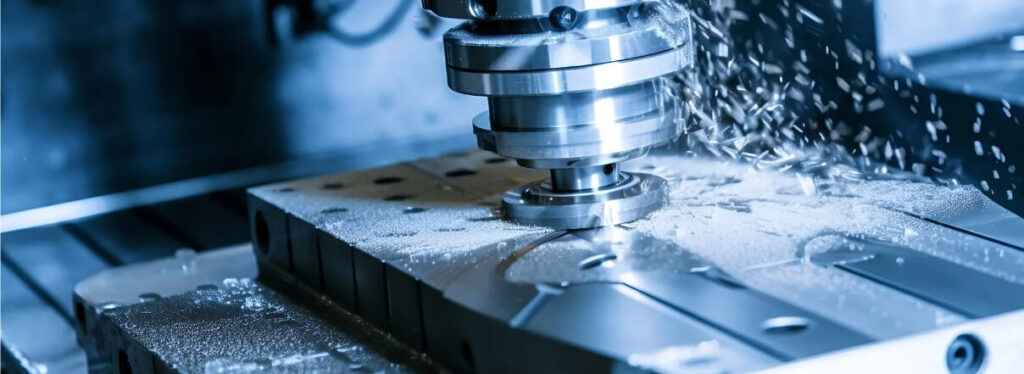
4) Deburring
During the processing, burrs may be generated on the surface of the valve body and the edge of the hole system. If these burrs are not cleaned in time, they may affect the sealing performance and service life of the valve. Therefore, deburring is the last important process of valve body processing.
(2) Valve core processing
The valve core is a key part in controlling the flow of fluid in the hydraulic flow control valve, and its shape accuracy and surface roughness requirements are extremely high. The main processes of valve core processing include rough processing, semi-finishing, finishing and deburring.
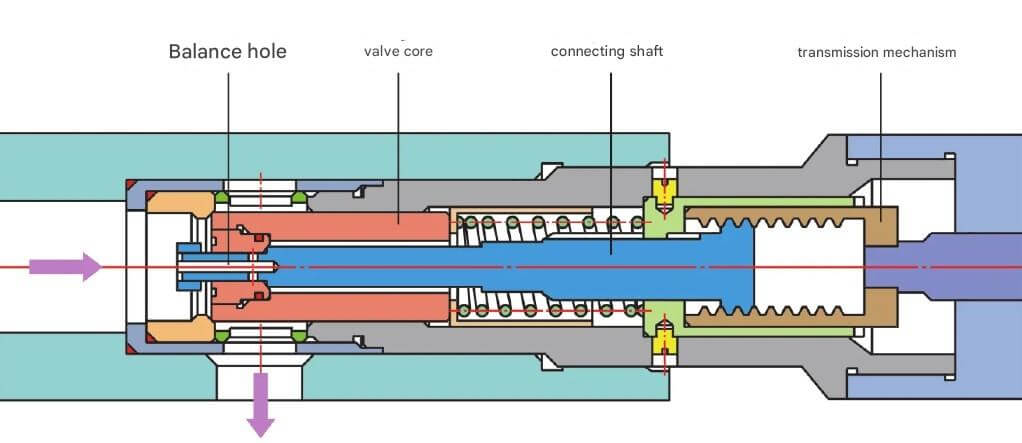
1) Rough machining
Rough machining of valve core usually uses bar stock or forgings for preliminary turning and grinding to remove most of the excess. The focus of machining at this stage is to ensure that the basic shape and size of the valve core are close to the design requirements.
2) Semi-finishing
In the semi-finishing stage, the outer circle, conical surface and groove of the valve core need to be further processed to achieve a certain dimensional accuracy and surface roughness. CNC machine tools are usually used for machining at this stage to ensure the consistency and accuracy of machining.
3) Finishing
Finishing is a key link in valve core machining. Precision grinders and CNC lathes are mainly used to precisely machine the outer circle and conical surface of the valve core.
The goal of finishing is to ensure that the shape accuracy, dimensional accuracy and surface roughness of the valve core fully meet the design requirements. For example, the roundness, cylindricity of the outer circle of the valve core and the angle accuracy of the conical surface need to be strictly controlled.
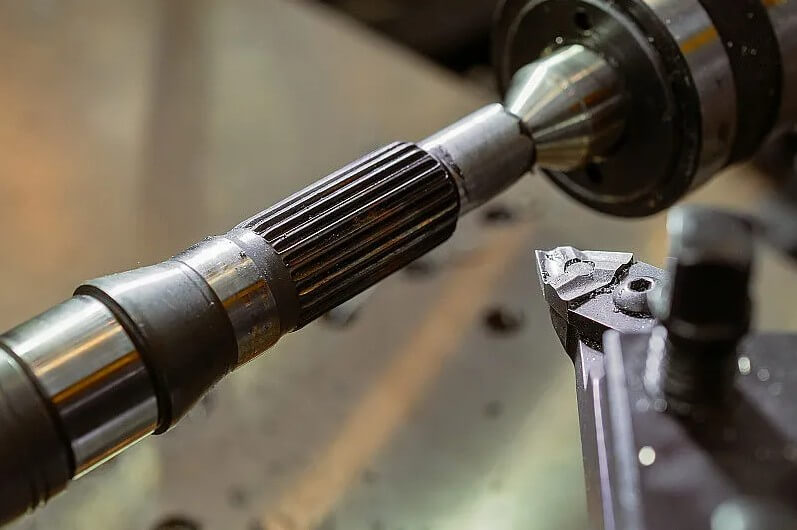
4) Deburring
The burrs generated during the valve core machining process also need to be cleaned in time to prevent them from affecting the performance and service life of the valve.
(3) Processing of other parts
In addition to the valve body and valve core, other parts of the hydraulic flow control valve, such as the valve seat and spring, also need to be precisely processed. For example, the sealing surface of the valve seat needs to meet extremely high surface roughness requirements to ensure the sealing performance of the valve; the spring needs to undergo precise heat treatment and surface treatment to ensure its elasticity and durability.
3.Surface treatment technology of hydraulic flow control valve
Surface treatment is an important part of improving the performance of hydraulic flow control valves. Its main purpose is to enhance the corrosion resistance, wear resistance and sealing performance of parts, thereby extending the service life of the valve. Commonly used surface treatment technologies include electroplating, oxidation treatment and surface coating.
(1) Electroplating
Electroplating is a common surface treatment technology. By electroplating a layer of metal on the surface of hydraulic flow control valve parts, its corrosion resistance and wear resistance can be improved. The specific process and characteristics are as follows:
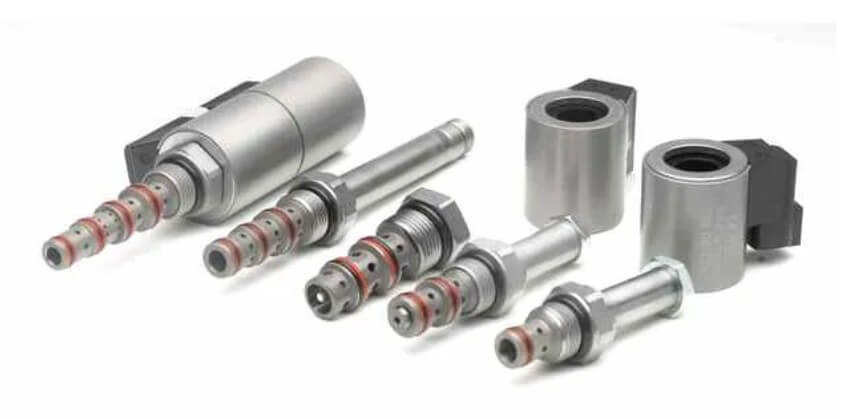
1) Pretreatment
Pretreatment includes degreasing, pickling and activation to remove surface grease, oxide layer and impurities to ensure that the coating is firmly bonded to the substrate.
2) Electroplating process
The part is placed in the electrolyte as the cathode, and a metal coating is deposited on the surface through an electrolytic reaction. Commonly used coating materials include chromium, nickel, etc.
3) Post-treatment
Post-treatment includes cleaning and drying to remove residual electrolyte on the surface and ensure that the coating surface is smooth and pollution-free.
4) Advantages
The chrome plating layer has high hardness and good wear resistance, and is suitable for the surface treatment of valve cores and valve bodies; the nickel plating layer has excellent corrosion resistance and is often used to improve the appearance and performance of parts. Electroplating technology can significantly improve the durability and corrosion resistance of parts.
(2) Oxidation treatment
Oxidation treatment is mainly used for the surface treatment of aluminum alloy valve bodies. A dense oxide film is formed on the surface of the valve body through anodizing, thereby improving its surface hardness and corrosion resistance. The specific process and characteristics are as follows:
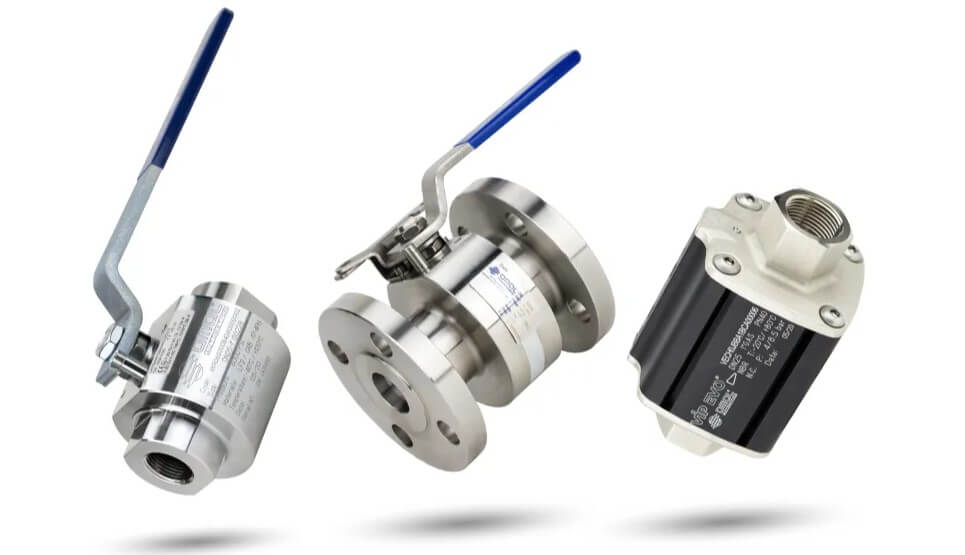
1) Pretreatment
Pretreatment includes degreasing, alkaline washing and acid washing to remove surface grease, oxide layer and impurities and ensure uniform adhesion of the oxide film.
2) Anodizing
The valve body is placed in the electrolyte as the anode to generate an oxide film through electrolytic reaction. The thickness of the oxide film is usually 5-25 microns and can be adjusted according to needs.
3) Post-treatment
Post-treatment includes sealing and dyeing. Sealing closes the pores of the oxide film through hot water or steam treatment to improve corrosion resistance; dyeing is used to improve appearance.
4) Advantages
Oxidation treatment significantly improves the corrosion resistance, surface hardness and aesthetics of the aluminum alloy valve body, and is suitable for high-precision hydraulic flow control valves.
(3) Surface coating
Surface coating technology can improve the wear resistance and sealing performance of hydraulic flow control valve parts by spraying a layer of special materials on the surface of the parts. The specific process and characteristics are as follows:
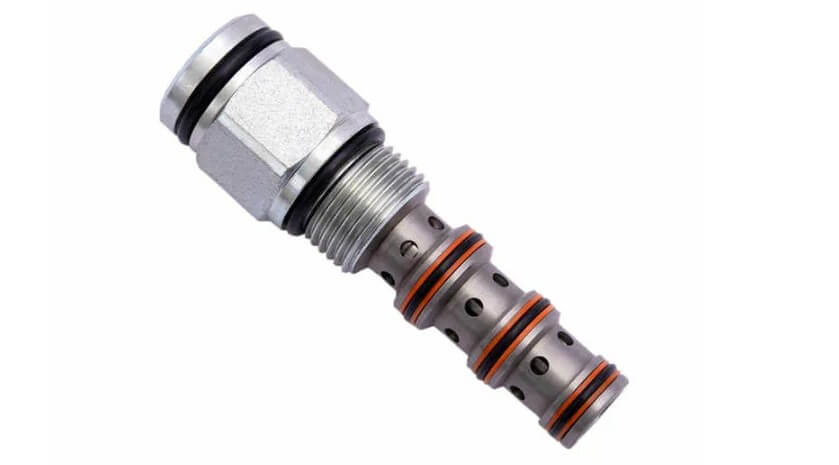
1) Pretreatment
Pretreatment includes sandblasting and cleaning to increase surface roughness and remove grease to ensure uniform adhesion of the coating.
2) Coating spraying
Use electrostatic spraying or air spraying technology to evenly spray Teflon and other coating materials on the surface of the parts.
3) High temperature curing
The coating is firmly bonded to the substrate by heating, and the curing temperature and time are adjusted according to the characteristics of the coating material.
4) Advantages
Teflon coating has an extremely low friction coefficient and excellent corrosion resistance. It is suitable for the surface treatment of valve cores and valve bodies, and can significantly improve wear resistance and sealing performance.
4.Summary
The processing and surface treatment of hydraulic flow control valves are key links to ensure their performance and service life. By optimizing the processing technology and surface treatment technology, the accuracy, wear resistance and corrosion resistance of hydraulic flow control valves can be significantly improved, thereby extending their service life.