Types and applications of superior transmission parts: the key to improving equipment performance
In the field of modern mechanical manufacturing and industrial automation, superior transmission parts are the core elements to ensure the normal operation of equipment. Superior transmission parts can not only improve the operating efficiency of equipment, but also effectively extend the service life and reduce maintenance costs. Therefore, the selection and application of high-quality transmission components are crucial for industrial production.
This article will explore the characteristics, manufacturing processes, and different types of transmission components and applications of superior transmission parts in depth, and will be analyzed in detail below.
1.Characteristics of superior transmission parts
Superior transmission parts usually have the following key characteristics:
(1) High precision and high durability
Adopt high-precision processing technology to ensure dimensional consistency and improve equipment stability.
After strict quality control and testing, reduce errors and improve assembly accuracy.
Wear-resistant materials and optimized design reduce friction and improve transmission efficiency.
(2) Excellent materials and manufacturing processes
Adopt high-performance materials such as high-strength alloy steel, stainless steel, and composite materials to improve fatigue resistance.
Advanced heat treatment (such as carburizing and nitriding) improves the surface hardness of parts.
Precision surface treatment technology (such as chrome plating, electroplating, and anodizing) improves corrosion resistance.
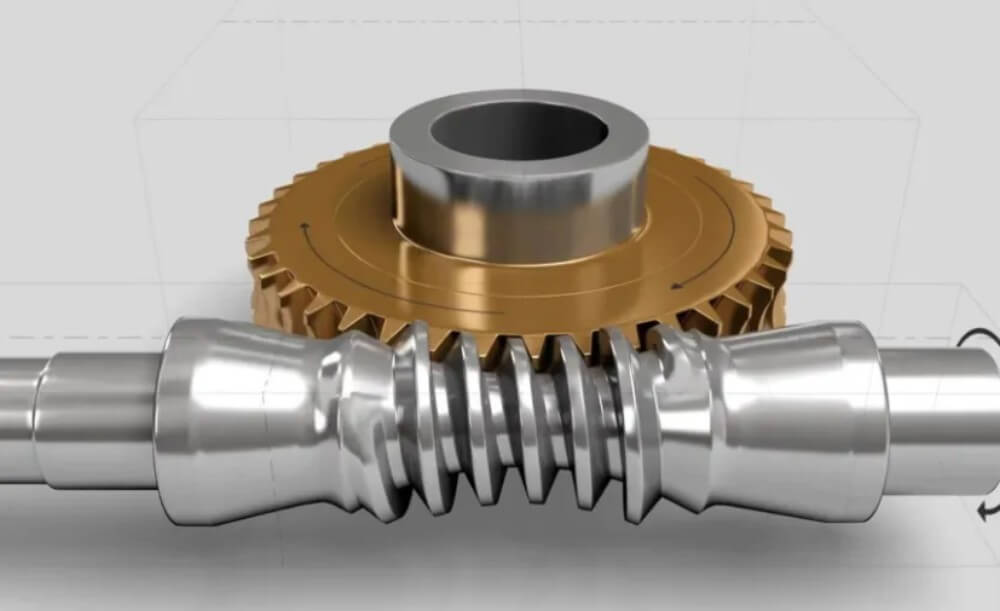
(3) High efficiency and low energy consumption
Reduce friction and improve energy transfer efficiency by optimizing structural design.
The application of lightweight materials reduces unnecessary loads and improves the overall performance of the equipment.
2.Manufacturing and processing technology of superior transmission parts – analysis of CNC processing technology
(1) The role of CNC processing in the manufacturing of superior transmission parts
CNC processing technology is widely used in precision machinery manufacturing, especially in the processing of superior transmission parts. Its main advantages include:
1) Improve processing accuracy: reduce human errors and ensure the consistency of parts.
2) Improve production efficiency: Automated operation increases production speed and is suitable for large-scale manufacturing.
3) Adapt to complex structures: It can realize the processing of difficult tooth shapes, shafts and curved structures.
(2) Key processes of CNC machining
The following are the main processes and their roles in the manufacture of high-quality transmission parts:
1) Turning
Mainly used for machining shaft and cylindrical parts, such as gear shafts.
High-precision CNC lathes are used to ensure coaxiality and surface finish.
2) Milling
Applicable to machining gear tooth profiles, keyways, planes, etc.
CNC milling machines can efficiently complete the machining of complex shapes and improve precision.
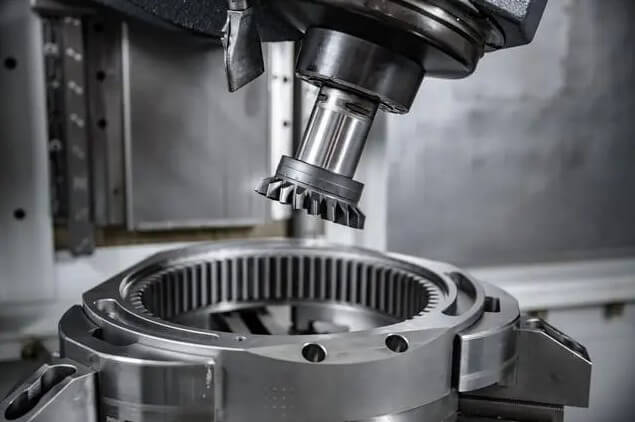
3) Grinding
High-precision grinders are used to finely grind gears and bearings to improve surface finish and reduce friction loss.
Using ultra-precision grinding technology can improve gear transmission efficiency and durability.
4) Drilling and tapping
Used for precise machining of threaded holes and matching holes to improve assembly accuracy.
High-precision drilling machines and tapping machines are used to improve thread quality.
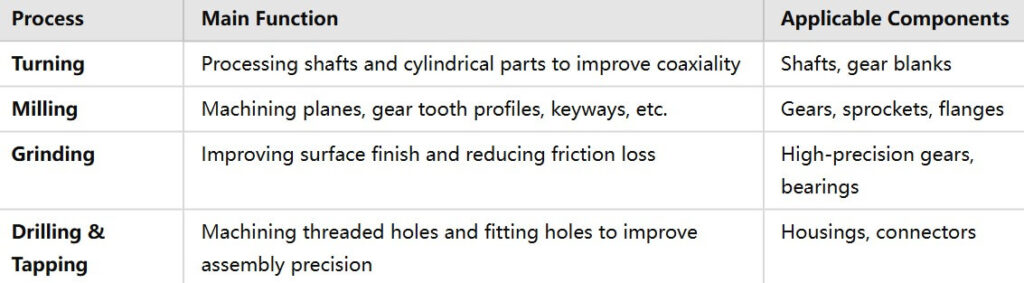
(3) Precision control and quality inspection
In CNC machining, it is crucial to ensure the accuracy of parts. The main methods include:
High-precision measuring instruments: such as three-coordinate measuring machines and laser interferometers.
Online detection and automatic compensation: adjust parameters through real-time monitoring to ensure consistency.
Error analysis and optimization: apply AI and big data analysis to improve processing stability.
(4) Development trend of intelligent CNC machining
Future CNC machining will be more intelligent, mainly reflected in the following aspects:
Adaptive control technology: adjust cutting parameters in real time and optimize the machining process.
5-axis linkage machining: improve the machining capability of complex curved parts.
AI and big data assisted optimization: optimize machining paths based on historical data to improve production efficiency.
3.Types of superior transmission parts and their applications
(1) Gear transmission
1) Features:
Gear transmission transmits power and motion through gear meshing, and has the characteristics of high transmission efficiency, compact structure and strong reliability. It can achieve precise transmission ratio and is suitable for high torque and high precision occasions.
2) Types:
Spur gears: used for parallel shaft transmission, simple structure, but noisy.
Helical gears: smooth transmission, low noise, suitable for high speed and heavy load.
Bevel gears: used for intersecting shaft transmission, commonly seen in automobile differentials.
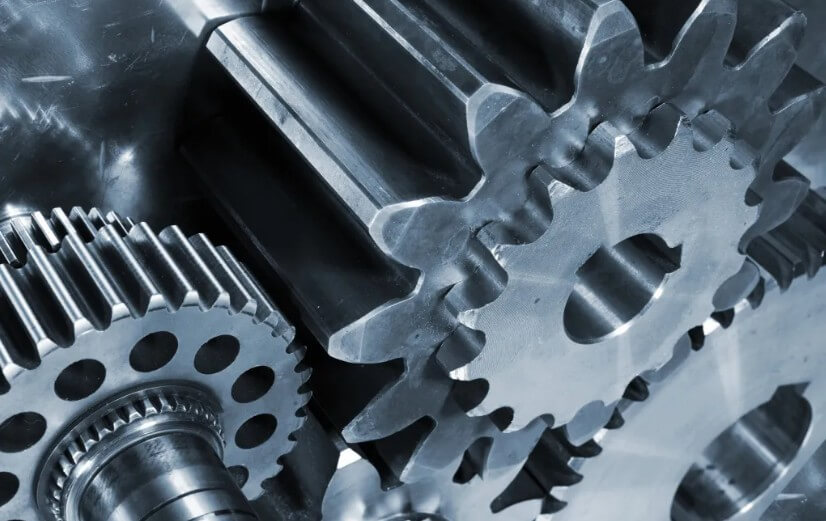
3) Applications:
Automobile gearboxes, industrial machine tools, robot joints, clocks, etc.
For example, automobile gearboxes use gear sets to achieve different gear shifts.
(2) Belt drive
1) Features:
Belt drive relies on the friction between the belt and the pulley to transmit power, and has the advantages of buffering vibration, low noise, and simple maintenance. It is suitable for long-distance transmission, but the transmission ratio is not accurate enough.
2) Types:
Flat belts: used for low speed and light load occasions.
V-belts: high friction, suitable for small and medium power transmission.
Synchronous belts: transmit power through tooth meshing, with accurate transmission ratio.
3) Applications:
Washing machines, fans, conveyor belts, printers, etc.
For example, the crankshaft of a car engine drives the water pump and generator through a belt.
(3) Chain drive
1) Features:
Chain drive transmits power through the meshing of the chain and the sprocket. It has the advantages of accurate transmission ratio, strong load-bearing capacity, and suitability for harsh environments. However, it is noisy and requires regular lubrication.
2) Types:
Roller chain: the most common type, used for bicycles, motorcycles, etc.
Silent chain: low noise, used for high-precision transmission.
3) Applications:
Bicycles, motorcycles, cranes, conveying equipment, etc.
For example, the pedals of a bicycle drive the rear wheel through a chain.
(4) Hydraulic drive
1) Features:
Hydraulic drive uses liquid pressure to transmit power. It has the advantages of stepless speed regulation, strong load-bearing capacity, and fast response speed. However, the system is complex and the cost is high.
2) Types:
Hydraulic pump: converts mechanical energy into hydraulic energy.
Hydraulic motor: converts hydraulic energy into mechanical energy.
3) Application:
Engineering machinery (such as excavators, bulldozers), aerospace, ship steering gear, etc.
For example, the hydraulic cylinder of the excavator drives the bucket to complete the excavation action.
(5) Worm gear transmission
1) Features:
The worm gear transmission transmits power through the meshing of the worm and the worm wheel, and has the advantages of large transmission ratio, compact structure, and self-locking function. However, the efficiency is low and it is suitable for low speed and heavy load.
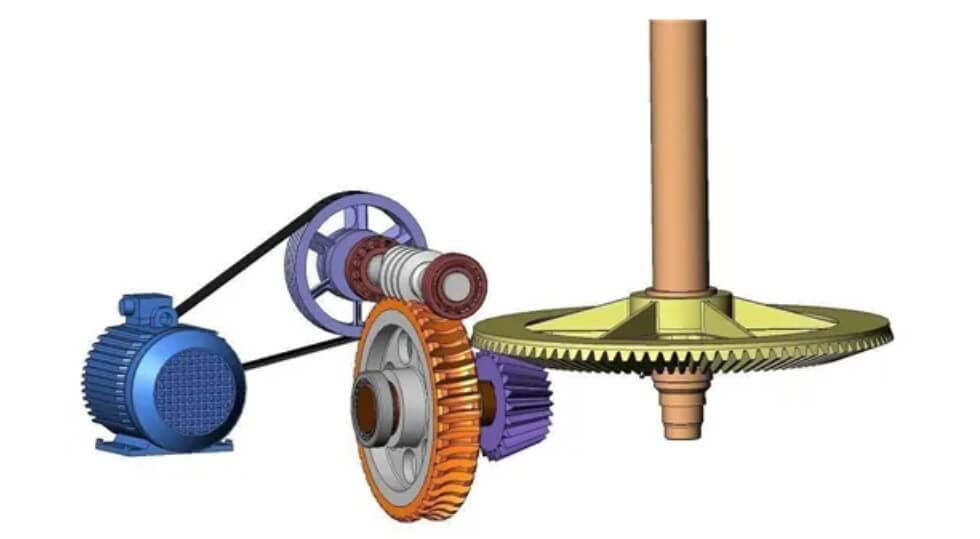
2) Application:
Elevators, steering systems, winches, etc.
For example, the drive system of elevators often uses worm gear transmission to achieve smooth lifting.
(6) Universal joint transmission
1) Features:
Universal joint transmission allows a certain angle deviation between the axes, and has the advantages of high flexibility and strong adaptability. However, the transmission efficiency is low and it is suitable for complex space layout.
2) Types:
Cross-axis universal joint: simple structure, widely used.
Ball cage universal joint: smoother transmission, used for high-performance vehicles.
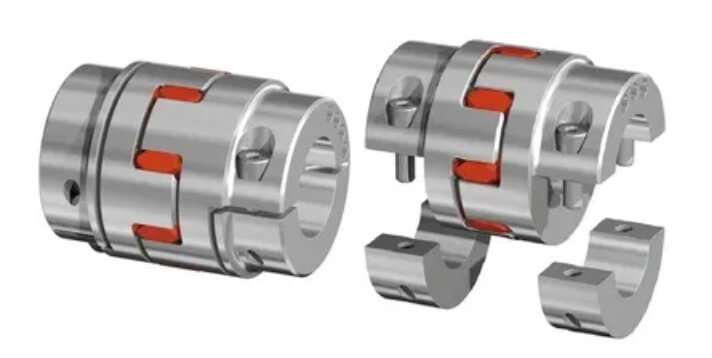
3) Application:
Automobile transmission shaft, machine tools, robots, etc.
For example, the transmission shaft of an automobile connects the gearbox and the drive wheel through a universal joint.
(7) Coupling transmission
1) Features:
The coupling is used to connect two shafts and transmit torque. It has the advantages of compensating for inter-shaft deviation and buffering vibration. Depending on the type, it is suitable for different occasions.
2) Type:
Rigid coupling: used for high-precision transmission, without buffering function.
Elastic coupling: can buffer vibration, suitable for general transmission.
3) Application:
Motor and equipment connection, pump and fan, compressor, etc.
For example, an industrial motor drives a water pump through a coupling.
4.How to achieve the high-precision requirements of superior transmission parts?
Superior transmission parts (such as gears, worms, couplings, etc.) have extremely high requirements for dimensional accuracy, shape accuracy and position accuracy, usually requiring micron level or even higher.
(1) Challenges in machining superior transmission parts:
1) High-precision requirements:
Transmission components need to achieve micron-level precision, which is affected by machine tool precision, tool wear and thermal deformation.
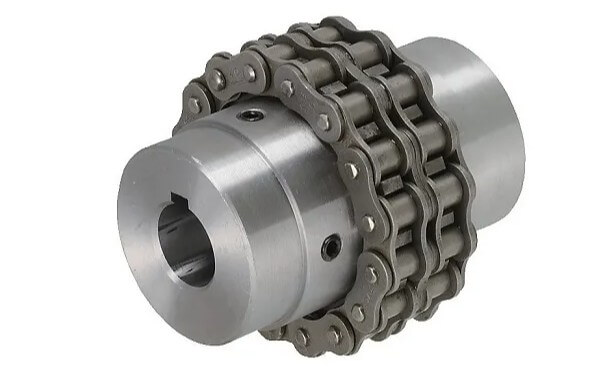
2) Complex geometric shapes:
Complex shapes such as helical gears and worm gears require multi-axis linkage machining and precision programming.
3) Material machining difficulty:
High-strength alloy steel, titanium alloy and other difficult-to-machine materials lead to rapid tool wear and difficult surface quality assurance.
4) Surface quality requirements:
Surface roughness affects performance and is prone to defects such as burrs and chatter marks.
5) Thermal deformation and residual stress:
Processing heat and cutting force cause deformation and stress, affecting dimensional stability and life.
6) Mass production consistency:
Machine tool stability, tool life and process parameter control affect mass production consistency.
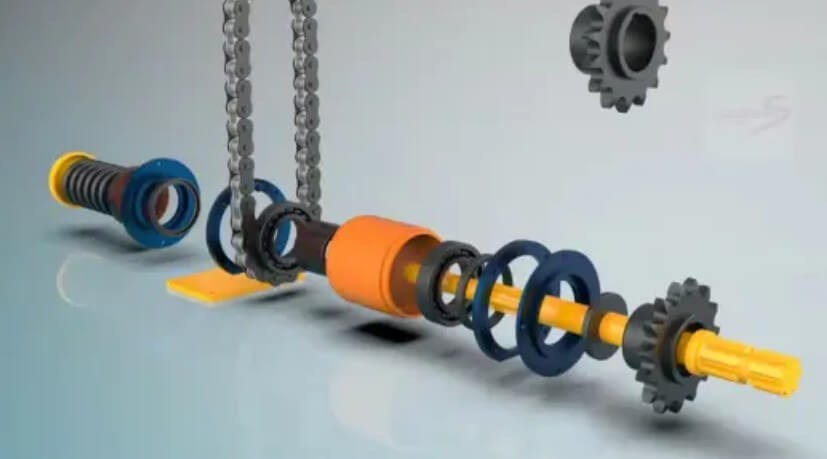
(2) Solutions for achieving high-quality transmission component machining:
1) Select high-precision CNC machine tools:
Use high-end machine tools with temperature compensation and vibration suppression functions to ensure the accuracy and stability of the machine tools themselves.
2) Optimize tool management:
Select tool materials with good wear resistance (such as cemented carbide, ceramics) and use coating technology (such as TiN, TiAlN coating), regularly check tool wear and replace in time.
3) Control thermal deformation:
Reduce the processing temperature through efficient coolant and lubrication systems, or use micro-lubrication (MQL) technology to reduce the impact of thermal deformation on precision.
4) Staged processing:
Use roughing, semi-finishing and finishing in stages to gradually improve accuracy and reduce error accumulation.
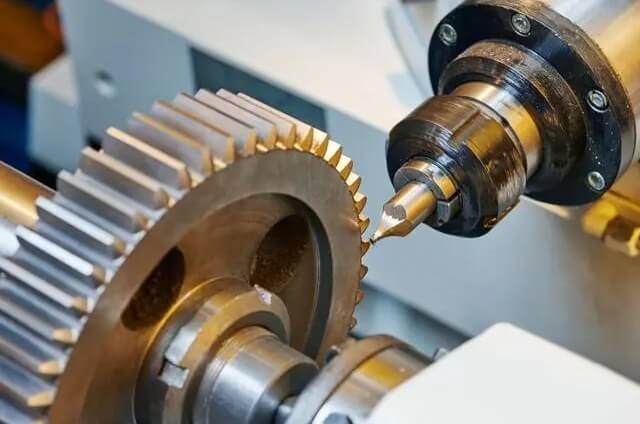
5) Online measurement and feedback:
Use online measurement systems to monitor the size and shape accuracy of workpieces in real time, adjust processing parameters in time, and ensure that the processing accuracy meets the requirements.
5.Summary
Superior transmission parts are the core of efficient operation of equipment, and their performance directly determines the reliability, accuracy and efficiency of the equipment. Whether it is precision machine tools, heavy machinery or automated production lines, the optimized design and high-precision manufacturing of superior transmission parts are the key to improving overall performance.