Manufacturing Machined Parts and Their Applications
Machine-machined parts are everywhere, and for good reason: CNC machining works on a wide variety of metals and plastics, and machined parts can be made quickly, affordably, and without any tooling.
But why should you choose machined parts over molded or 3D printed parts? Sometimes the choice is obvious, but sometimes it’s hard to decide. How do you actually design parts for machining, in-house or outsourced to a manufacturer?
This guide covers the basics of machined parts: what they are, why your company needs them, the best materials to machine, typical tolerances for machined parts, how to design machined parts, and more.
1.What are machined parts?
Machined parts are everywhere. From tiny metal fasteners to aircraft engine components, a wide variety of parts are made through the machining process. But what exactly is machining? And what are machined parts?
When we talk about machined parts, we mean something more specific than an object that is made with a machine. We’re talking about parts that are made using cutting machines like mills, lathes, and planers. These machines work in different ways, but their basic purpose is the same: using a sharp cutting tool, they cut parts from a block of material called a workpiece.
Even within that definition, machined parts can be formed in different ways. The machining process can be manual, with a machinist (a skilled, specialized machine operator) operating a machine such as a milling machine to manually cut the workpiece into the desired shape. Or it can be digital, in which case an electric CNC machine automatically cuts the machined part based on computer instructions.
Today, most complex or custom machine parts are made with CNC machines, but machinists still machine some jobs by hand because it is faster than creating digital designs and programming digital machinery.
Machined parts can be metal or plastic (and sometimes other materials), but they must be made of a material that can be cut and will not deform drastically.
Sometimes, a part is machined after it has been made with another manufacturing process. For example, a cast or molded item may have certain details or features machined in at a later stage. These are called partially machined parts or post-machined parts.
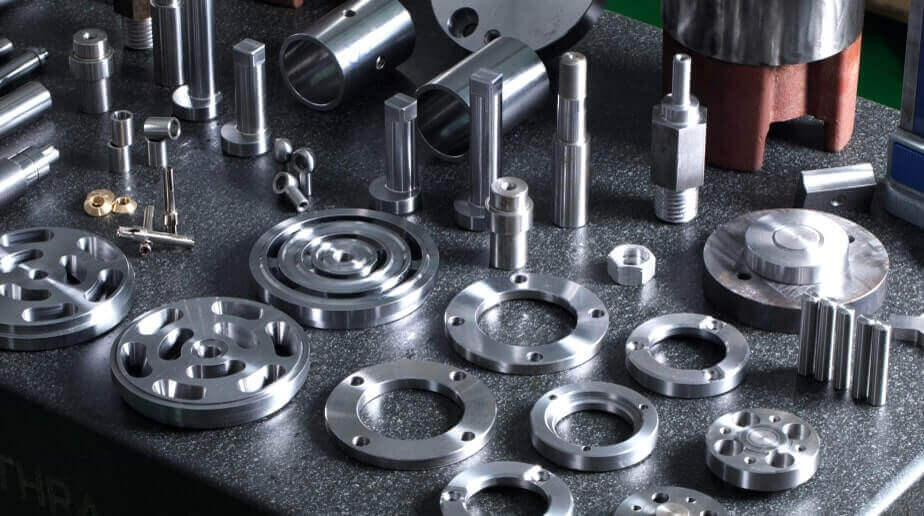
2.Why use machined parts?
There are many reasons why companies, product designers, R&D departments, and other professionals use machined parts, and the following sections cover many of the specific benefits of machined parts.
In short, machined parts have excellent strength because they are made from a solid block of material and can be made in a variety of shapes and thicknesses. They can have very detailed features and can be made from a wide variety of materials. Since no tooling is required, small quantities of machined parts can be made quickly, and tolerances can be very tight if the process speed is reduced.
Companies may also use machined parts because machining is a tried and tested manufacturing technology that has been an industry standard for decades. Therefore, machined parts are likely to meet industry-specific standards and certifications.
3.What are the advantages of machined parts?
Machined parts have certain advantages that cannot be achieved with injection molded parts or 3D printed parts. Listed below are some of the main advantages of machined parts.
1) No Minimum Order Quantity
One of the main advantages of machined parts is that there is no minimum order quantity limit when purchasing. For molded parts, metal molds need to be made – a process that takes a long time and usually costs tens of thousands of dollars.
However, machined parts are cut directly from the stock workpiece, which makes it cost-effective to order very small batches or even one-off parts.
Of course, requiring a large number of (plastic) parts may mean that molding is a better choice. But machining is almost unique in providing high-quality parts without minimum order quantities, making it suitable for smaller companies, small batch production and prototyping.
2) Good prototypes
Some companies choose to order injection molded prototypes, but usually only large companies can afford it. The cost of molds makes prototyping cost-prohibitive.
Machined parts are suitable for use as prototypes and are affordable because they can be made in one-offs. Machining is also much faster than molding, which means that R&D departments can quickly iterate multiple versions of a part and then perform any testing or evaluation required on it before going into production.
The material versatility of machining also means that companies can order machined parts in several different metal alloys or composite plastics to see which material performs best under test conditions.
3) Design freedom
Machined parts can have a wide variety of shapes and sizes. This is because CNC machining is not limited by extreme molding design constraints such as thin walls and tapers; machined parts can be thick and strong, but their features can also be fine and detailed.
Although machined parts have some limitations in areas such as internal sections and deep channels, machining is still one of the manufacturing processes with the highest geometric flexibility.
On the other hand, molded parts must have thin walls and generally meet more stringent design standards. Even 3D printing processes, which are often seen as one of the manufacturing technologies with the highest degree of design freedom, have limitations such as avoiding overhangs. (And more complex and large designs may require a large number of support structures that must be removed in expensive post-processing steps.)
4) Quality
Machinery parts can be manufactured to very high standards. Perhaps more importantly, customers can specify the tolerances that the machinist needs to meet. This means that the machinist or machine operator can spend more time on machined parts and individual features with tight tolerances.
While injection molds can also be manufactured to tight tolerances, it is unlikely that each individual mold will be manufactured to such a high standard. Molds produced near the end of a mold’s life may lack the definition of earlier units.
5) Lead Time
Machine-machined parts can be made faster than parts made by other production processes, such as molding.
This is partly due to the lack of labor-intensive tooling, but the manufacturing process itself is also very efficient: some of the faster machining centers equipped with linear guides can process at speeds of around 4,000 cm per minute (although parts should not actually be machined at such speeds).
The one-step nature of machining combined with the speed of CNC machining centers makes machined parts among the fastest to manufacture (in small batches), which reduces lead time, shortens time to market, and enables practical rapid prototyping.
6) Modifications
Because CNC machined parts are made from a digital CAD file, changes can be made to that digital design before manufacturing. This is very useful during R&D and prototyping, as engineers may want to make minor adjustments to a machined part or create multiple versions.
It also reduces the potential for waste, as there is less chance of producing a defective part. Machined parts have a significant advantage over molded parts: tools are not easily changed, and if a last-minute modification is required, it would be a huge waste of money to create a new mold.
7) Strength
Machinery parts are cut from a solid piece of material called a blank, which is usually cast or extruded. This makes them stronger than, for example, 3D printed parts, which are much weaker along the axis where one layer is stacked on top of another.
Many machined parts are also stronger than molded parts, which have limited mechanical properties because their walls must be thin.
8) Surface Finish
Machinery parts avoid molding-related surface quality issues such as flow lines, jets, and flash at parting lines. With the right amount of post-processing, the surface finish of machined parts can be achieved to a very high standard.
Machining provides a superior surface finish than 3D printing, even before any post-processing. 3D printing (especially FDM printing) leaves visible layer lines on the surface of the part that must be smoothed out by grinding or chemical treatment. Machined parts do not have these layer lines.
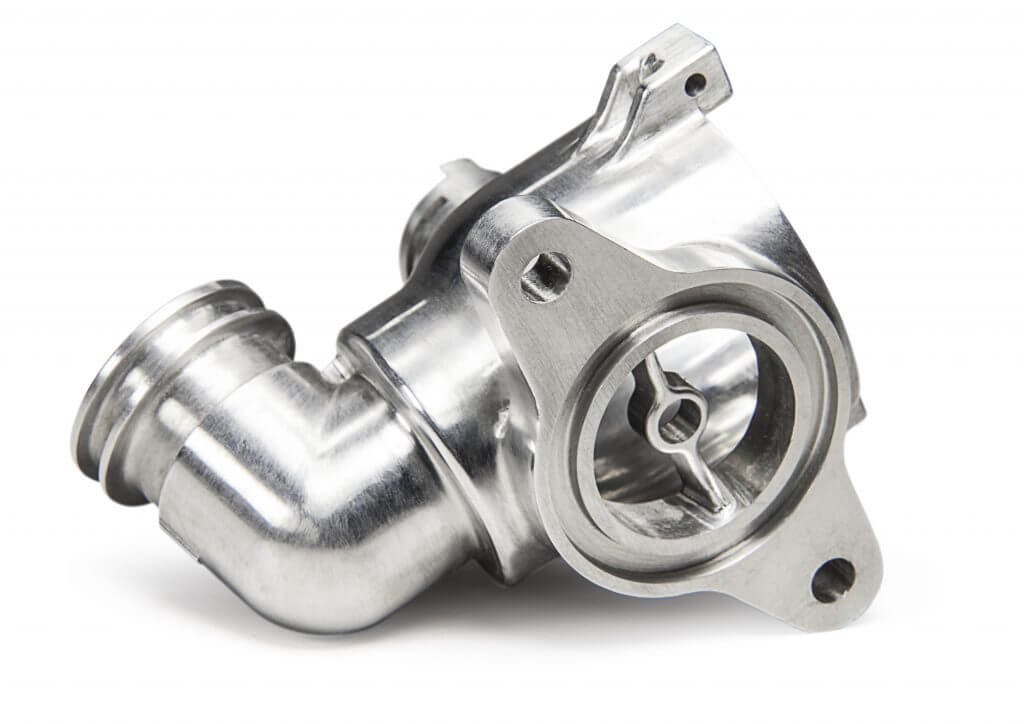
4.How to design machined parts?
It is always best to apply Design for Manufacturing (DfM) principles: design the part based on the manufacturing process it will be used in. Machined parts need to be designed differently than, say, 3D-printed parts.
Fortunately, the design of machined parts is not particularly difficult as long as certain rules are followed. These rules are outlined below.
1) Undercuts
Undercuts are cuts in the workpiece that cannot be made with a standard cutting tool (because part of the part is in the way). They require special cutting tools (such as T-cutters) and special machining design considerations.
Because cutting tools are manufactured to standard sizes, undercut dimensions should be in whole millimeters to match the tool. (For standard cuts, this is not critical because the tool can move back and forth in tiny increments.) Undercut widths range from 3 to 40 millimeters, depending on the cutting tool, and can be up to twice the width deep.
If undercuts can be avoided entirely, the part can be machined faster and with less effort.
2) Wall Thickness
Unlike molded parts, which deform when the wall thickness is too thick, machined parts cannot handle particularly thin walls. Designers should avoid thin walls or, if thin walls are integral to the design, use processes such as injection molding. When machining, the wall thickness should be at least 0.8 mm (metal) or 1.5 mm (plastic).
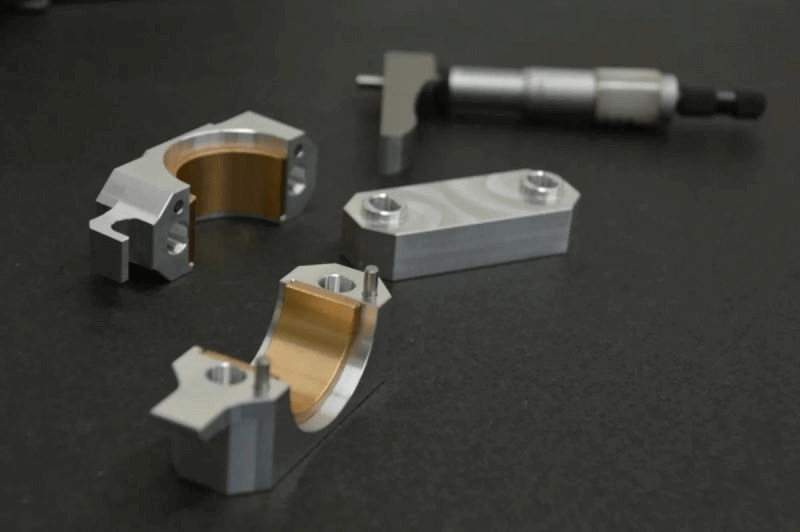
3) Protrusions
Like thin walls, high protrusions are difficult to machine because vibrations from the cutting tool can damage the part or cause reduced precision. The height of a protruding feature should not be greater than four times its width.
4) Cavities, holes, and threads
When designing mechanical parts, it is important to remember that holes and cavities are dependent on the cutting tool. Cavities and grooves can be machined into a part to a depth of four times the width of the cavity. Deeper cavities will inevitably end up with fillets (rounded edges rather than sharp edges) due to the required cutting tool diameter.
The depth of a hole drilled with a drill should also not exceed four times the width of the drill. The diameter of the hole should match the standard drill size as closely as possible. The depth of threads used to attach fasteners such as screws does not have to exceed three times the diameter.
5) Size
CNC machined parts are limited in size because they are made within the manufacturing confines of the machine. Milled parts should not exceed 400 x 250 x 150 mm; turned parts should not exceed Ø 500 mm x 1000 mm. Larger sizes are possible with larger machines, but this should be discussed with the machinist prior to fabrication.
5.Material of machined parts
Machined parts can be made from a number of different materials, including metals and plastics. However, some materials are easier to machine than others. Very hard materials can be difficult to penetrate with a cutting tool and can cause the tool to vibrate more (thus reducing quality). Very soft materials and those with very low melting points can deform when in contact with a cutting tool.
The most common materials for machined parts are listed below. Other materials can also be machined based on the manufacturer’s requirements.
- Metals: Aluminum, steel, stainless steel (17-4, Inconel 625 and 718), magnesium, titanium, zinc, brass, bronze, copper.
- Plastics: ABS, PC, ABS+PC, PP, PS, POM, PMMA (acrylic), PAGF30, PCGF30, Teflon, DHPE, HDPE, PPS, PEEK. (Less common: PA GF50, PPS GF50.)
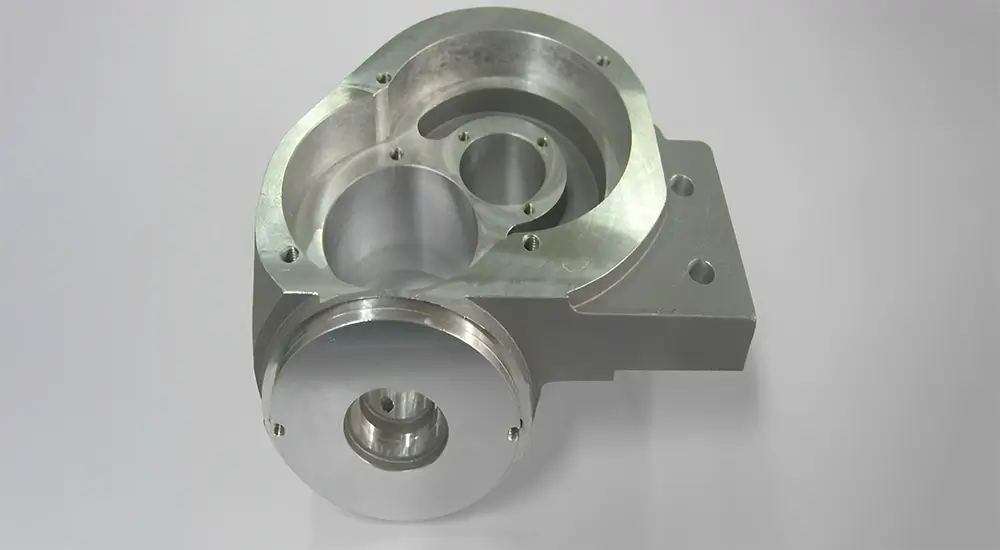
6.Surface finish of machined parts
Machined parts can be treated after machining to change their surface texture and appearance. Surface treatments can be functional or decorative.
- As machined: No surface treatment added. Suitable for many internal, non-decorative functional parts.
- Sandblasting: The sandblasting process involves spraying abrasives at the machined part to give it a matte appearance. The process can be adjusted to achieve a specific roughness. It may not be suitable for fine features because sandblasting removes material, which affects the geometry of the machined part.
- Anodizing: The anodizing electrolytic passivation process is suitable for aluminum machined parts to form a scratch-resistant, colorful coating. Type II anodizing creates a corrosion-resistant coating; Type III anodizing is thicker and offers wear resistance in addition to corrosion resistance.
- Powder coating: During powder coating, a powder coating (in a color chosen by the designer) is sprayed onto the machined part and then baked in an oven. This creates a strong, wear- and corrosion-resistant coating that outlasts standard paint finishes.
7.Machined Part Tolerances
Machined parts can be manufactured to tight tolerances, which may be necessary for critical mechanical parts that interact with other components. For prototypes and non-mechanical parts, looser tolerances may be selected.
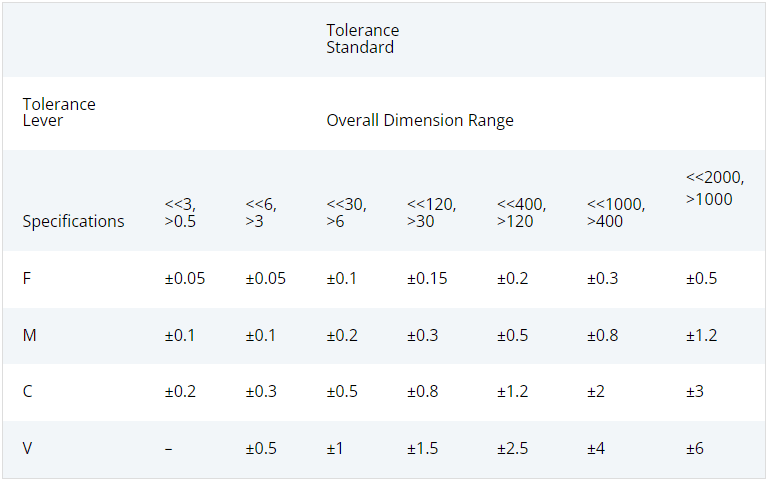
8.What are the applications of machined parts?
Machine parts are used in almost all industries, from aerospace to medicine. Below is a list of some common everyday parts and industry-agnostic parts, followed by industry-specific applications.
Common machined parts:
- Fasteners
- Valve bodies
- Ball joints
- Gears
- Shafts
- Housings
- Brackets
- Rollers
1) Aerospace
Aerospace parts that can be machined include prototype engine parts, fuel plates, landing gear components, and engine mounts.
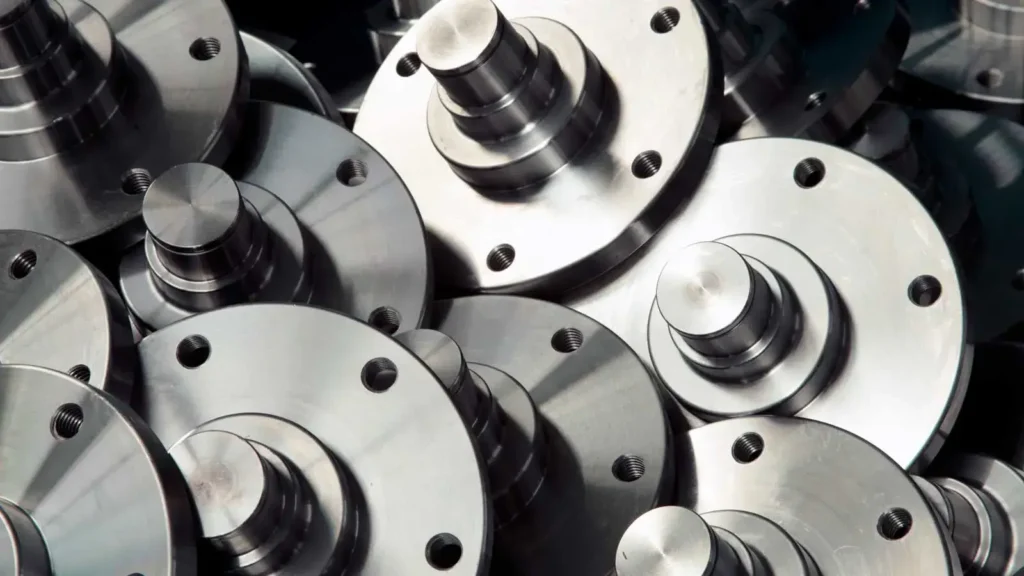
2) Automotive
Automotive machined parts include functional test parts such as lighting, engines, transmissions, and steering systems, as well as one-off custom parts.
3) Medical
Machined titanium and stainless steel parts include implants, medical devices, and surgical tools such as scalpels.
4) Consumer products
Machined parts can be found in household items and appliances. Sporting equipment can also be CNC machined, while many machined metal and plastic parts can be found in consumer electronics. Items such as laptop cases, connectors, and sockets can all be machined.