A Detailed Introduction to Standard Machining Tolerances
Standard machining tolerances are important parameters that must be considered no matter what product is being manufactured. Most consumer products today require micro-consistency.
Therefore, manufacturers often look at various types of manufacturing processes and compare them, with machining tolerances as a major factor.
To understand the machining tolerances of different processes, it is important to understand what machining tolerances are, how they are measured, and the different types of tolerances that exist.
This article will cover all of this information and more. Finally, we will provide some tips to help you improve machining tolerances in your own industry.
1.What is machining tolerance?
Machining tolerance is the limit of dimensional variation allowed relative to the ideal blueprint value. Machining tolerance describes the accuracy of any manufacturing process.
To achieve high accuracy and precision, the value of machining tolerance should be minimal. Simply put, machining tolerance is inversely proportional to the precision of the process.
Since there is no perfect process, it is virtually impossible for the machining tolerance value to be zero. However, modern manufacturing technologies such as CNC machining have reduced this value to a minimum.
Typically, tolerances for CNC machining are measured in the format of ±0.x”.
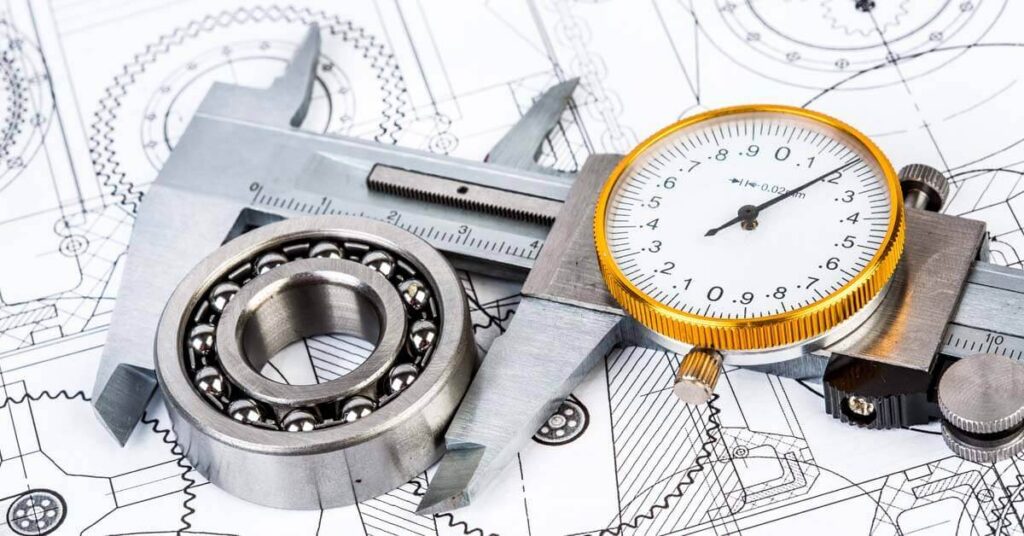
2.Calculation and Expression of Machining Tolerances
Before understanding how to calculate machining tolerances, it is important to understand the various terms associated with the subject.
Here are some of the terms you should be familiar with:
1) Basic Dimensions
The basic dimensions of a workpiece are the dimensions marked on the drawing. Manufacturers and designers know that the manufacturing process will have certain tolerances. Therefore, designers take into account the possible deviations in the manufacturing process when selecting basic dimensions.
2) Actual Dimensions
The actual dimensions are the dimensions of the final product after the machining process is completed. While the basic dimensions are theoretical values, the actual dimensions are the actual realization of the finished product. While it is almost impossible to make the actual dimensions exactly the same as the basic dimensions, the goal of manufacturers is to make the two values as close as possible.
3) Limits
The limits are the maximum and minimum dimensions allowed for a part. The maximum dimension allowed is called the upper limit, and the minimum dimension allowed is called the lower limit. If the actual dimensions of a part exceed these two limits, the part is considered unusable and is rejected.
4) Deviations
The deviation is the difference between the maximum allowable dimension and the basic dimension. Since the maximum allowable dimensions are of two types – Upper and lower limits, so the resulting deviations are also of two types: upper deviation and lower deviation.
The calculation of these deviations is simple:
- Upper deviation = upper limit – basic size
- Lower deviation = lower limit – basic size
5) Datum
In physics, a datum is an arbitrarily selected imaginary line or plane that serves as a reference point for measuring tools. The concept of datum is also used in many types of geometric dimensioning and tolerance fields, which will be discussed in later sections.
6) Maximum Material Requirements and Minimum Material Requirements
When a feature or part of a workpiece contains the maximum amount of material at all locations, a maximum material condition (MMC) occurs. Examples of MMCs can be the smallest hole or the largest pin in a workpiece. The presence of MMCs provides additional tolerances available.
Similarly, when a feature or part of a workpiece contains the least amount of material at all locations, a minimum material condition (LMC) occurs. Examples of NMCs can be the largest hole or the smallest pin in a workpiece.
The use of MMC and NMC determines the clearance fit of a component. MMC is the worst case in which the parts can still fit. Anything beyond the MMC of the size will not allow the product to be assembled.
The shift from MMC to LMC allows for a larger allowable tolerance in the workpiece area, which is called the compensation tolerance. The calculation of the compensation tolerance depends on how much the material of the actual part is reduced compared to the maximum material.
Therefore,
Bonus Tolerance = MMC – Actual Size
Since the minimum value of the actual size is the LMC limit, the maximum bonus tolerance will be:
Bonus Tolerance (Maximum) = MMC – LMC
7) Decimal Places
In high-precision processes such as CNC machining, the tolerances are very small. The actual values of tolerances in CNC machining are so small that decimal places are required to measure them. The more decimal places there are, the tighter the tolerance and the higher the accuracy.
To better understand, let’s take the example of manufacturing process A, which has a tolerance of ±0.2″, B has a tolerance of ±0.1″, C has a tolerance of ±0.01″, and D has a tolerance of ±0.001″. In terms of accuracy, process D is the most accurate, followed by C, B, and A.
8) Calculating Tolerances
To calculate machining tolerances, we need to know the upper and lower limits of the machining process.
For example, let us consider a screw with an actual diameter of 10 mm, whose acceptable variance is between the following ranges:
- Upper limit: 12 mm
- Lower limit: 8 mm
The tolerances of the machining process are:
- Tolerance (t) = Upper limit – Lower limit
- t = 12-8 = 4 mm.
Sometimes, instead of mentioning the upper and lower limits, the limits are described in the form of variations, such as 10 ± 0.2 mm. In this case, the upper and lower limits can be calculated by adding and subtracting the variations, respectively.
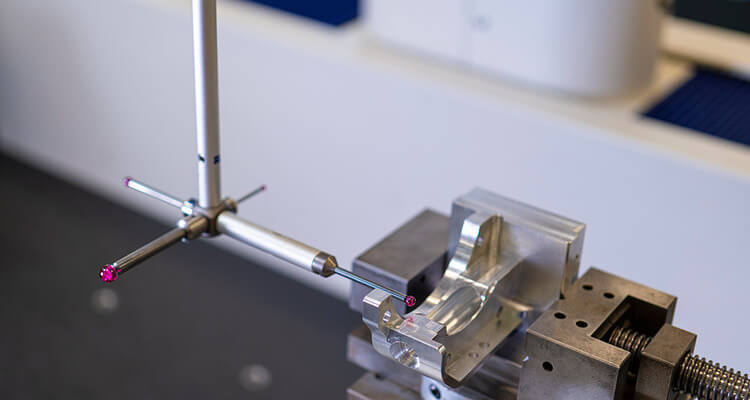
3.Different Types of Machining Tolerances
Due to the different geometries of the parts and the different types of machining processes, tolerances in CNC machining are expressed in different ways.
Let us go through these different tolerances one by one:
1) Unilateral Tolerance
Unilateral tolerance in CNC machining implies that the allowed deviation can only occur in one direction. The basic dimension of the part is the same as the upper or lower limit, and the tolerance can only be positive or negative, not both.
For example, if the pipe diameter is 10 mm and the single-sided tolerance is +1 mm, the basic dimension and the lower limit of the process are both 10 mm. The upper limit in this example is 11 mm. All acceptable parts should be within this range, and any part that is 10 mm less than the basic value will be rejected.
Similarly, if the pipe diameter is 10 mm and the single-sided tolerance is -1 mm, the basic dimension and the upper limit of the process are both 10 mm. In this case, the lower limit is 9 mm. The manufactured parts should be within this range, and all parts that are slightly greater than the basic value of 10 mm will be rejected.
2) Bilateral Tolerance
In contrast to the single-sided tolerance, the bilateral tolerance allows variation in two directions. The basic dimension of the part is between the upper and lower limits, and the tolerance value can be positive or negative.
If the variation in both directions is equal, the bilateral tolerance is ±0.x mm. If the variation is not equal, then the bilateral tolerance can be written as +0.x mm and -0.y mm.
For example, if a tube has a diameter of 10 mm and the bilateral tolerance is ±1 mm, then the basic dimension is 10 mm, the upper limit is 11 mm, and the lower limit is 9 mm. All parts between 9 mm and 11 mm are acceptable. Therefore, the actual part can be smaller or larger than the basic expected part.
3) Limit Tolerance
Limit tolerance is another common way of expressing tolerances in CNC machining and other manufacturing methods. Limit tolerance does not use any “+”, “-” or “±” symbol language. Instead, it mentions the upper and lower limits of the part. Instead of using the basic dimension and making the actual dimension conform to the allowed variance of the basic dimension, the only requirement is to make the part within the provided limits.
Limit tolerance is easy to use and does not require any calculations. If the limit tolerance is expressed in the form of a diagram, the upper limit means above a certain dimension and the lower limit means below the upper limit and above a certain dimension.
An example of using limit tolerances is machining a pipe between 9 mm and 11 mm in diameter, rather than requiring a pipe between 10 ±1 mm in diameter.
One important thing to remember is that while the limit tolerances are expressed differently than bilateral tolerances, the part results will be the same. The difference is only in how easy it is for the blueprint reader to understand the design criteria.
4) Profile Tolerance
Profile tolerance is very different from the other types of tolerances mentioned above. So far, the other tolerances have been variations in dimensional accuracy, while profile tolerance is related to the curvature of the cross section of the part. Its symbol is a semicircle located on the diameter of its cross section.
In order to understand the concept of profile tolerance in CNC machining, it is very important to understand what a profile line is. A profile line is a line that runs along the cross-sectional area of the workpiece. The profile tolerance range means that the curve of this line should be within an acceptable range of variance. This value is measured in dimensional units (millimeters or inches).
5) Directional Tolerance
Directional tolerance is the variation in the shape of the workpiece relative to a reference shape. The reference shape or plane used to check the relative variance is called a datum. Directional tolerances are measured for the perpendicularity or angle of the workpiece. Even when measuring angular offsets, directional tolerances are measured in millimeters or inches rather than degrees.
6) Positional tolerance
The range of positional tolerances is similar to that of directional tolerances. Positional tolerances in CNC machining refer to the offset in the position of a specific feature of the workpiece. To measure the offset, a reference line called a datum is used. The expected position of a feature is called its true position.
7) Form tolerance
Form tolerances are related to the physical characteristics of the workpiece, such as its flatness, roundness, or straightness. These tolerances are also measured in millimeters or inches, using measuring tools such as height gauges, calipers, micrometers, etc.
8) Runout tolerance
Runout tolerance refers to the fluctuation of a specific feature of a workpiece relative to the datum when the workpiece is rotated 360 degrees around the center axis. Runout tolerance is important and measurable for any or all features of the workpiece. The symbol for this tolerance is a box with an arrow pointing to the upper right corner.
9) Unequal Tolerances
Unequal tolerance zones are sometimes also called U modifiers because its symbol is the letter “U” in a circle. These tolerances are used when a specific profile of a workpiece requires unequal single-sided tolerances.
10) Geometric Dimensioning and Tolerancing (GD&T)
Geometric Dimensioning and Tolerancing is a system for detailing and communicating standard machining tolerances. Since there are many types of tolerances for many different types and shapes of parts, a standardized system helps the parties involved in manufacturing communicate with each other. GD&T is the most widely used standard tolerancing system in the world.
GD&T assigns symbols to different types of tolerances and establishes a detailed set of rules for how to measure specific tolerance zones.
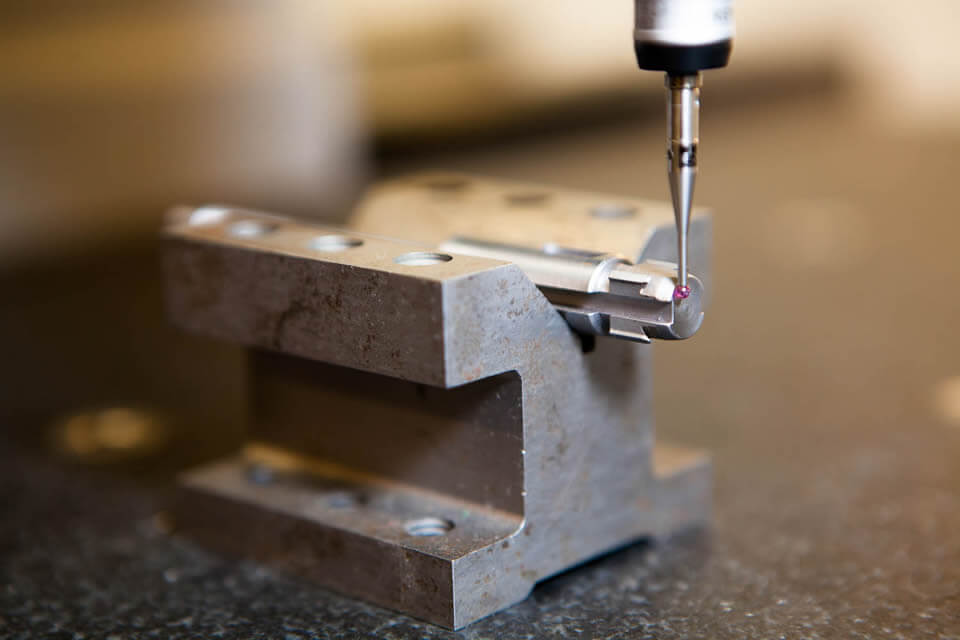
4.Common CNC Machining Tolerances
CNC machining is a broad field that covers many different processes. CNC machining tolerances are different for each process due to the different types of cutting tools used.
The following are standard CNC machining tolerances for common processes:
- Router: ± 0.005 in. or 0.13 mm
- Lathe: ± 0.005 in. or 0.13 mm
- Router (shim cutting tool): ± 0.030 in. or 0.762 mm
- Milling (3-axis): ± 0.005 in. or 0.13 mm
- Milling (5-axis): ± 0.005 in. or 0.13 mm
- Engraving: ± 0.005 in. or 0.13 mm
- Rail cutting tolerance: ± 0.030 in. or 0.762 mm
- Screw machining: 0.005 in. or 0.13 mm
- Steel rule die cutting: ± 0.015 in. or 0.381 mm
- Surface Finish: 125RA
If you compare these values to alternative remanufacturing techniques, you will find that the CNC machining process involves tighter tolerances.
Important Things to Remember When Working with Tolerances
Knowing a few things beforehand when working with tolerances can lead to better end results, better planning, and better resource utilization.
1) Do You Need Tight Tolerances?
Since tolerances directly reflect the accuracy of a part, at first glance, the tighter the better. However, for CNC machined parts, too tight tolerances can increase production costs and make the machining process time-consuming. Therefore, too tight tolerances should be used when necessary.
Tight tolerances are often required when the part will be used in a secondary assembly process. In this case, loose tolerances may cause assembly failure. Therefore, tolerance bands are of interest.
Another use case for tight tolerance machining is designing prototypes of innovative parts. Designers want the prototype to function exactly like the finished product. Therefore, they use the tightest requirements possible.
2) Cost
To better optimize resources, manufacturers do not pursue the absolute smallest tolerances. Instead, they use the smallest tolerances that fit within their budget. A good way to factor in budget is to plot the increase in cost versus the decrease in tolerance band and find the acceptable range where these two values intersect for a particular project.
3) Inspection
Most projects that use CNC machines or any other manufacturing process have a quality control phase to check that the final product is within acceptable limits. If the product fails to meet acceptable limits, it will be rejected.
If very tight tolerances are used, the time for the inspection phase will increase significantly. In addition, complex equipment may be required to measure tighter tolerance levels.
4) Machining Methods
CNC machines are often favored for their high precision and low tolerances. However, even among CNC machines, the type of machine used can significantly affect part tolerances. Therefore, if you have an in-house CNC machine, check the tolerance level of the machine beforehand and then design your project accordingly.
5) Surface Roughness
No matter how smooth a surface may appear, every surface will have rough aberrations. For some surfaces, such as polished natural stone, these aberrations are much smaller, and therefore the surface roughness is lower. For other surfaces, such as wood, the surface roughness is much higher.
Therefore, when choosing tight tolerances for CNC machining, keep in mind the surface roughness that already exists. Rough surfaces can create difficulties when the goal is to achieve tight tolerances.
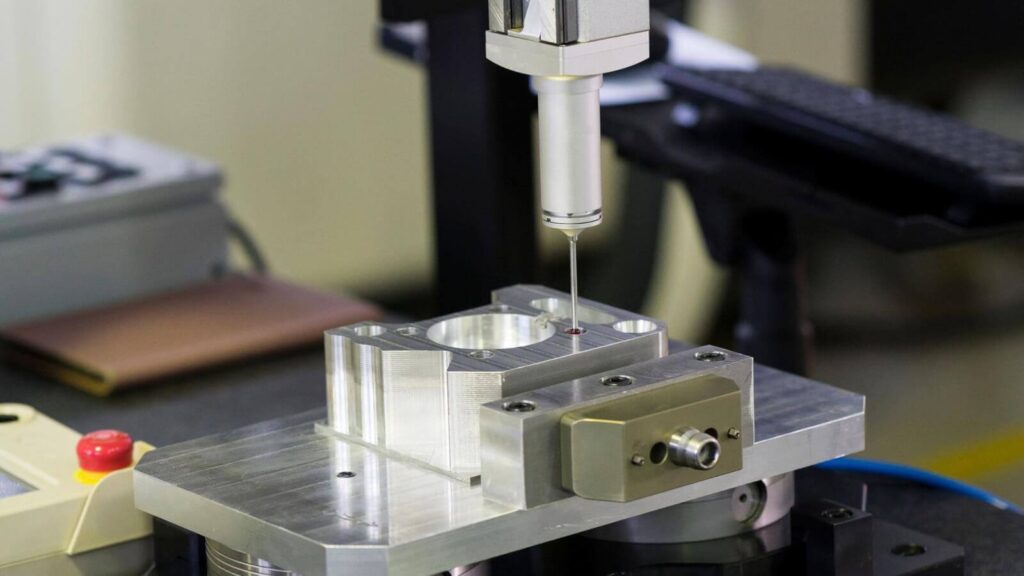
5.How to Find the Right Tolerances?
There are many options when it comes to finding the right tolerances for your parts.
Let’s go through these options one by one:
1) Use a Reputable CNC Machining Company
Outsourcing your project to a good CNC machining company can save you the hassle of dealing with technical issues of tolerances and many other issues. Xavier is one of the leading CNC service providers in this regard.
Xavier CNC machining services are provided by a team of highly skilled experts and the most advanced machines and equipment on the market. This means that you not only have professionals suggesting the best tolerances to use, but also the best equipment to achieve those tolerances in real life.
2) Calculate Tolerances Yourself
To calculate the tolerances of a part yourself, you first need to envision the purpose of the part. The function of the part will determine how much attention you need to pay to the tolerances of the part. After that, you can use general rules to determine the tolerances.
3) Are there international standards for machining tolerances?
Yes, there are many international standards for machining tolerances. Geometric Dimensioning and Tolerancing (GD&T) itself contains seven different standards for measuring standard machining tolerances. There is also the ISO 2768 standard.
4) What is ISO 2768?
ISO 2768 is an international standard that specifies general tolerances for manufacturing parts to international standards. It itself contains different categories such as:
- Linear dimensions
- External radius and chamfer height
- Angular dimensions
- General tolerances for straightness and flatness
- General tolerances for perpendicularity
- General tolerances for symmetry
- General tolerances for circular runout
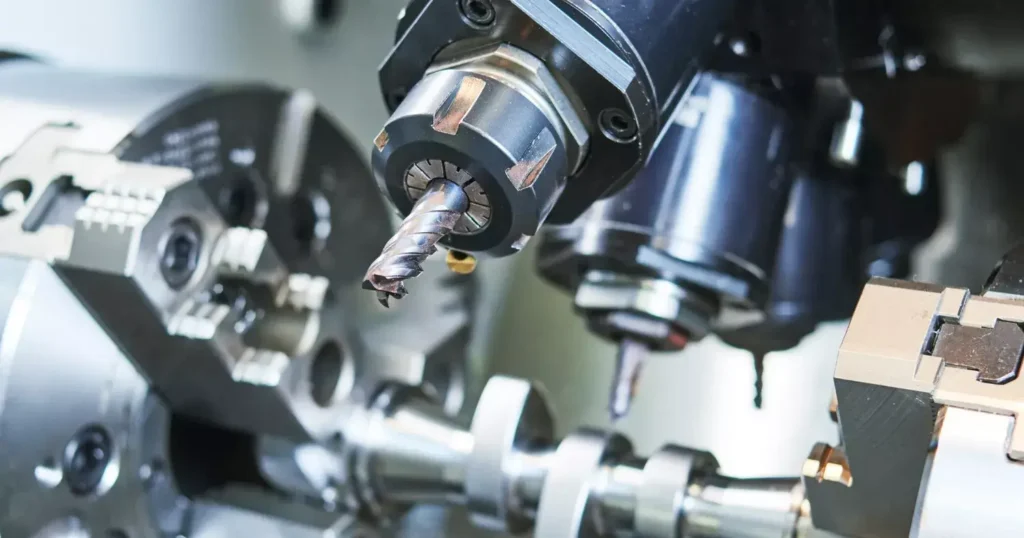
6.Tips for Improving CNC Machining Tolerances
Following the following tips will help you achieve tight machining tolerances and higher quality parts:
- Remember that tolerances are not one size fits all. Different tolerances are calculated for different materials and different applications. For metal parts, the standard tolerance is +/- 0.005 inches, and for plastic parts, it is +/- 0.01 inches. Due to different geometric dimensions, these values may be more or less in actual implementation.
- Choose a manufacturing process that can achieve the tolerances you need. Although processes with tighter tolerances may be costly, they are more cost-effective overall due to better optimization.
- Never underestimate the importance of parallelism and perpendicularity tolerances. These tolerances should be given priority because any change in these values will affect all other values and even change the appearance of the part itself.
- Tolerance expectations should be consistent with the machinability of the material. To achieve tighter tolerances, more machining of the material is required. This additional work can be very difficult for materials that are already difficult to machine.
- Avoid tight tolerances altogether if the project does not require it. This can save a lot of cost on the project.
- Emphasize the tolerances of important features of the part, such as features that help with assembly or features that bear stress. At the same time, the tolerances of some features can be ignored, such as features for aesthetic purposes.
1) What degree of tolerance is considered tight in machining?
While there is no exact tight tolerance range, for CNC machining, anything around ±0.005 inches is considered a tight tolerance. Tight limit tolerances can go as low as ±0.001 inches, below which machining becomes very difficult.
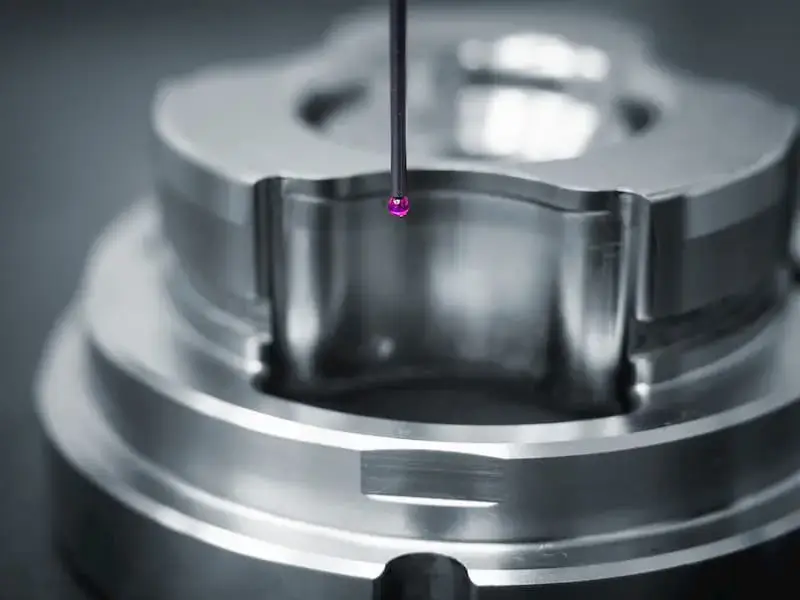
7.Importance of Machining Tolerances
Tolerances and dimensional accuracy of parts are much greater than what might appear at first glance. Every manufacturing process, whether manual or CNC, has a certain amount of error, some greater than others. Machining tolerances represent the range of error that can be allowed.
Keeping tolerances in mind can produce high-quality parts. At the same time, ignoring tolerances can result in significant manufacturing errors that lead to rejection of large numbers of products or even entire batches of products.
8.Conclusion
Machining tolerances are an integral factor in the manufacturing process. While the extent of these tolerances can vary from project to project, there are few use cases where these values can be completely ignored.
Therefore, paying attention to the above information can save your project costs and lead to better quality results. If you feel that the concept of tolerances is too technical, difficult, or hard to calculate for your specific project, Xavier is here to help.