CNC Turning: The Comprehensive Guide
CNC turning services offer a variety of techniques for manufacturing cylindrical parts made from a variety of materials. Chatter in machining is also normal.
Unlike CNC milling, CNC turning rotates the workpiece and inserts a stationary tool into the workpiece. Advanced CNC turning centers produce highly complex parts by adding milling capabilities to the machine, as shown in the figure:
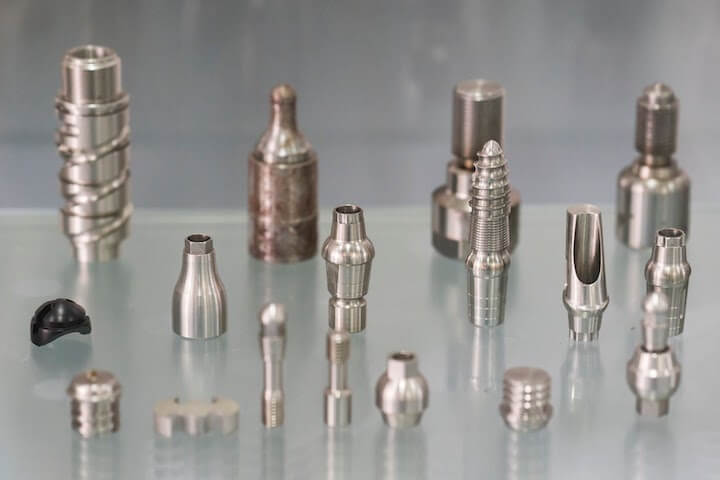
This article will provide a top-level introduction to CNC lathes and describe typical naming conventions, how CNC turning works, the types of operations available, and the various components of a CNC lathe.
1.CNC Turning Explained
CNC turning is a subtractive manufacturing technique that refers to the process of removing material from a stock that is typically cylindrical, although CNC turning can also be performed on a variety of stock shapes such as hexagonal or square bars. The machine rotates the workpiece while the tool moves to engage and remove material until the desired shape is achieved.
Lathes can be either vertical or horizontal. Vertical CNC lathes are often used to machine large and heavy designs because the center of gravity of the material is aligned along the axis of rotation.
Horizontal CNC turning uses a cantilever effect because the workpiece is mounted in a way that creates a cantilever effect. Cantilevered setups can cause vibrations in large, heavy workpieces that can affect machining quality and can also cause damage to the lathe and tooling.
However, vertical turning also has its own disadvantages. One of these disadvantages is chip evacuation: if the chips are not evacuated effectively after cutting, this can lead to potential problems such as chip re-cutting and part scratching. Therefore, horizontal CNC turning is the most common setup.
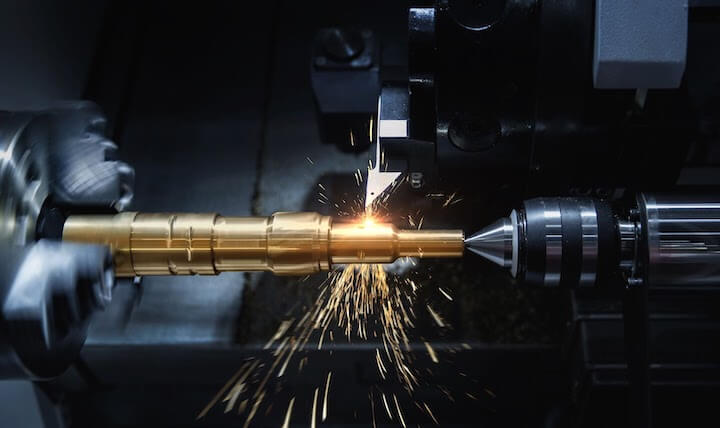
2.CNC Lathe vs. CNC Turning Center
The difference between CNC Lathes and CNC Turning Centers can be simply expressed as the difference in their capabilities, with turning centers typically being able to perform multiple operations, while lathes are limited to turning.
A lathe is a machine designed to cut rotating workpieces, while turning generally refers to the process of cutting with rotation. Before the advent of CNC technology, lathe machines were similar and easy to identify.
However, as technology has advanced, many new capabilities have emerged. Therefore, we need to distinguish between simple CNC machines that perform primitive lathe operations and enhanced machines that can perform turning cuts in other ways (CNC turning centers).
Some companies distinguish between the two based on the number of axes of toolpaths that the machine can perform. CNC toolpaths can be classified as 2D, 3D, 4-axis or 5-axis (this applies to milling and turning-cutting processes).
Lathes are usually 2-axis machines, while turning centers are usually 3-axis, 4-axis or 5-axis machines. Other companies refer to machines that can perform turning as well as milling and drilling operations as turning centers.
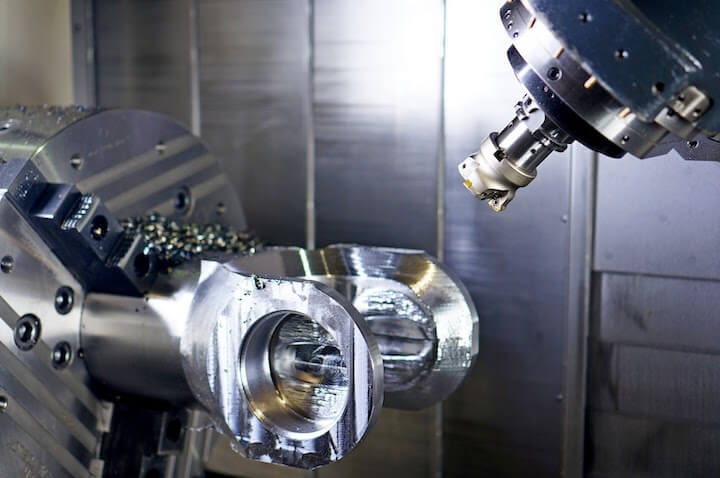
3.CNC Lathe Components
A lathe consists of a spindle that is connected to the machine drive system at one end and a chuck that holds the workpiece to be cut at the other end. The chuck usually has three or four jaws, with three-jaw chucks being the most common. Four-jaw chucks can be used to hold square bars and can also be used for eccentric turning.
The cutting tools are usually made of carbide inserts. These inserts are mounted in toolholders that are bolted to the turret using a variety of specialized toolholder bolts, depending on the tool type. The tool is then indexed as part of the preparation before machining begins.
4.CNC Turning Tool Materials
Several companies have put a lot of research effort into designing better inserts, coatings, and alloys to extend tool life and improve performance.
With so many different insert designs, choosing the right insert for the material being machined is critical. Trying to machine a hard material with a tool designed for a softer material (while using the same speed and feed values) can damage the tool or the workpiece.
A key part of CNC turning tool insert material engineering is crystal orientation. In magnified images taken through a microscope, individual crystalline regions (called grains) in the material can be analyzed.
The structure, size, and orientation of these grains depend on the material composition (alloy) and how the material is manufactured or modified through heat treatment and various other processes. These grain sizes and orientations are related to mechanical properties.
This change in microstructure increases resistance to crater and flank wear and improves heat transfer during machining. As a result, the unidirectional crystal structure helps the cutting edge retain its shape longer, improving wear resistance and tool life, and significantly reducing machining costs.
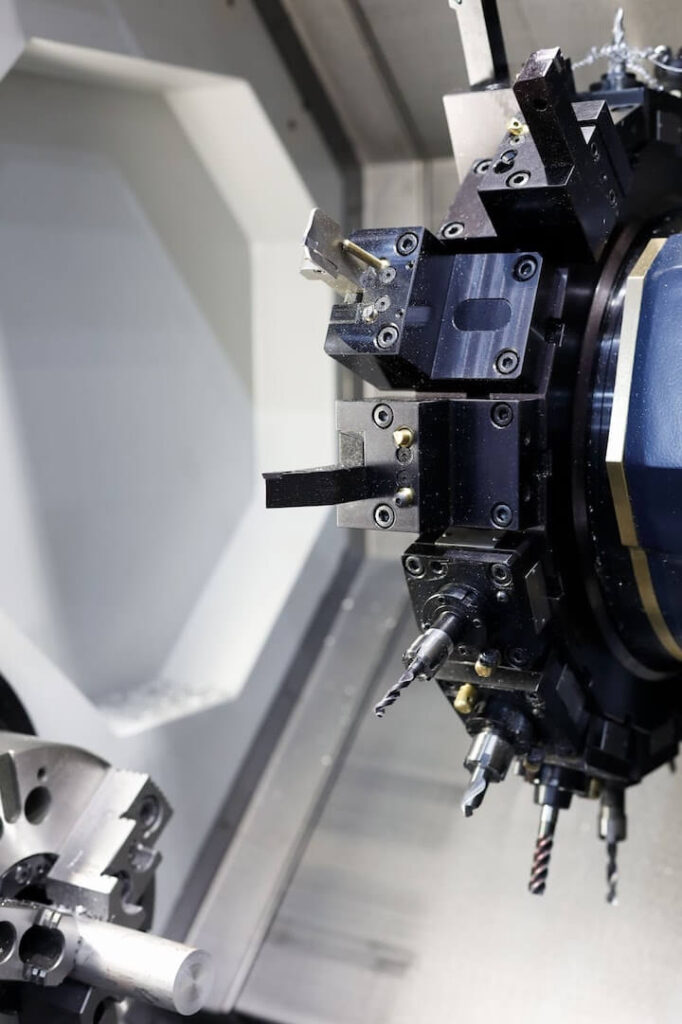
5.Types of CNC Turning Operations
Turning is a term used to describe a range of different operations that can be performed on a turning center. Some of the more common types of turning are listed below:
1) Facing
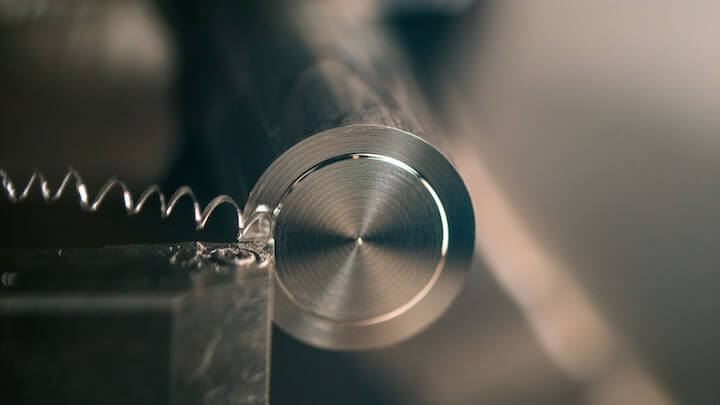
Facing is a process used to cut flat surfaces that are perpendicular to the axis of rotation of the workpiece. The tool is mounted in a tool holder on the lathe carriage. During this process, the facing tool is fed perpendicular to the axis of rotation of the part. Facing can be performed as a roughing operation or a finishing operation.
2) Turning
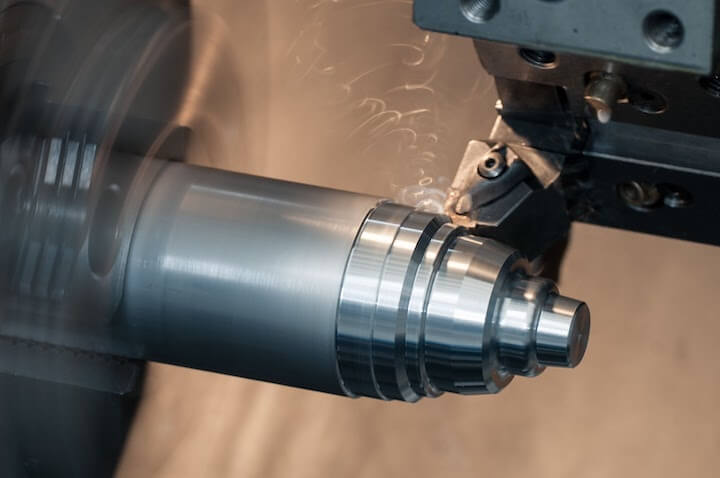
CNC machine turning operations refer to the removal of material from the outside diameter of the workpiece. Turning can be performed parallel to the axis of rotation of the part or at an angle to create a tapered part.
3) Drilling
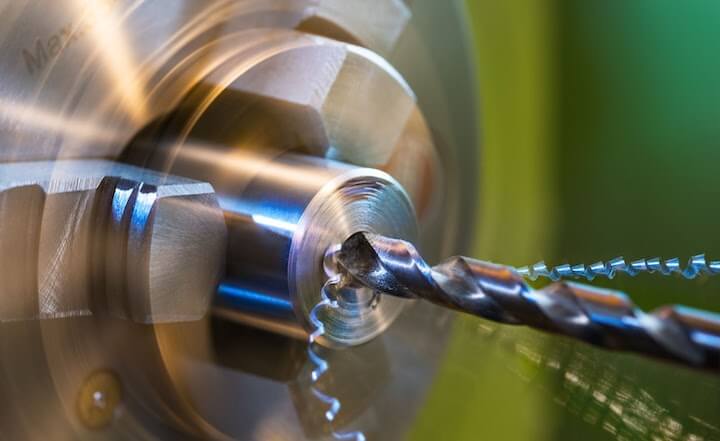
If a hole needs to be drilled in the rotating axis of a part, a drill is used. On more advanced turning centers, holes can be drilled in almost any direction, not just the center axis.
4) Boring
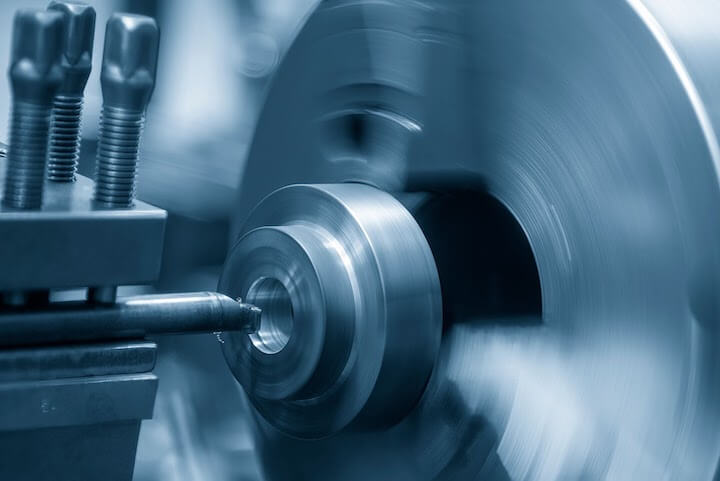
After drilling a hole, it may be necessary to enlarge it. The simplest way to do this is through a drilling operation, where a cutting tool is fed into the existing hole and removes material from the inside wall of the hole.
5) Threading
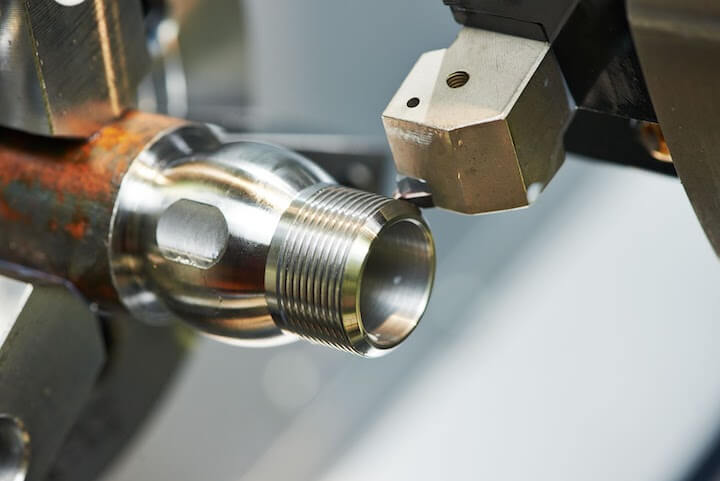
Threading is the process of cutting threads into a hole or into the outside diameter of a workpiece.
6) Grooving or Cutting Off
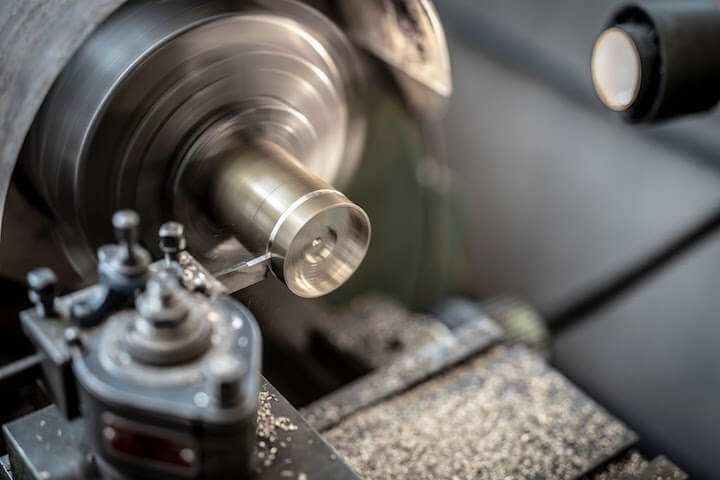
Grooving is often used to create features such as O-ring or spring circlip grooves, as well as contouring operations. Grooving tools, sometimes called cut-off tools, are used to remove completed parts from workpiece stock.
7) Knurling
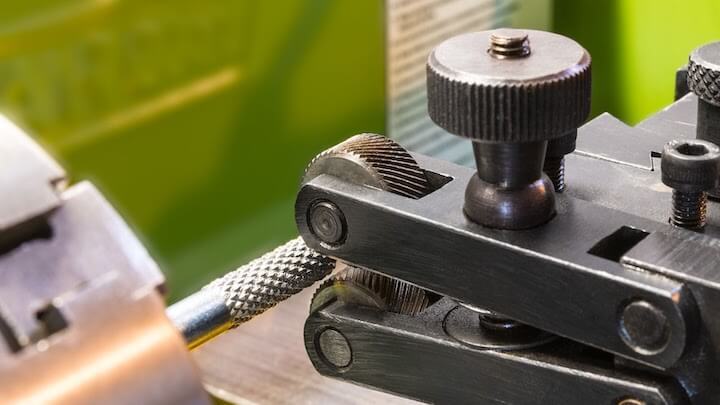
Knurling creates a diamond pattern on the outside diameter of a part. This pattern is not created by cutting, but rather by compressing the material into the desired pattern with a knurling tool. Knurling is most often used to add handles to a part.
6.Advantages of CNC Turning
CNC turning offers many advantages, some of which are listed below:
1) Accuracy
CNC turning can reliably produce extremely accurate parts, as the automated nature of the system eliminates the human factor.
2) Flexibility
CNC turning is a flexible manufacturing technology that can produce a wide range of complex parts. CNC turning centers go a step further and combine milling and turning capabilities for maximum flexibility.
3) Safety
All cutting processes take place behind machine guards, meaning the operator never gets close to the rotating material, eliminating the typical risks of manual lathes.
4) Faster Results
CNC lathes can produce parts quickly because they follow a precise set of instructions without pausing and can quickly change to different tools when needed.