A Comprehensive Guide to Machined Plastic Parts
In the rapidly evolving manufacturing industry, machined plastic parts have become an integral component across industries.
This article explores the complexities of machined plastic parts, delving into their applications, benefits, and the machining processes that influence their precision.
1.Understanding Machined Plastic Parts
In the dynamic world of manufacturing, the term “machined plastic parts” symbolizes precision, versatility, and innovation.
Understanding the intricacies of this manufacturing process is critical for industries that rely on plastic parts, as it lays the foundation for superior quality, customization, and efficiency.
1) What are machined plastic parts?
Custom machined plastic parts include components that are manufactured using various types of plastics through machining processes, including CNC machining.
Unlike traditional manufacturing techniques such as injection molding or extrusion, machining requires extracting material from a solid block or sheet to achieve the desired shape.
This subtractive manufacturing method allows for unparalleled precision and customization in the production of plastic parts.
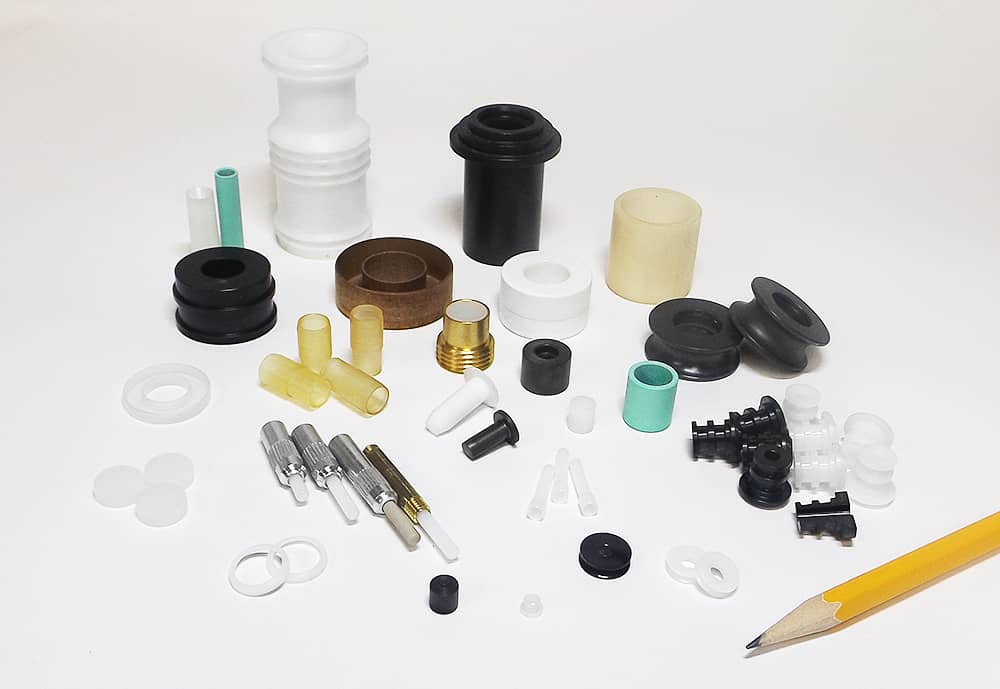
2) How do they differ from other manufacturing methods?
① Precision production and mass production:
- Injection molding
While injection molding performs well in mass production, it does not always achieve the level of precision required for complex designs or tight tolerances. - Machining
When precision is critical, machined plastic parts shine. CNC machining can create fine and precise components that are ideal for professional applications.
② Customization and complexity:
- Extrusion
Extrusion is often used to create continuous shapes such as pipes or tubing, but may face limitations when dealing with complex geometries. - Machining
Machinery-processed plastic parts offer unparalleled customization, making them suitable for complex designs and complex structures to meet the unique needs of various industries.
③ Material flexibility:
- 3D printing
While 3D printing is versatile in terms of material use, it may not always meet the requirements of certain industrial-grade plastics. - Machining
The machining process supports a variety of plastic materials, ensuring that it can adapt to different industry needs without compromising precision.
3) Importance of Precision and Accuracy:
① Meeting Tight Tolerances:
Precision in the production of plastic parts is critical, especially in industries where tight tolerances are non-negotiable.
Machined plastic parts manufactured using CNC machining technology are guaranteed to meet tight tolerances, ensuring that each component meets precise specifications.
② Improved Product Performance:
The precision achieved through the machining process directly translates into enhanced product performance. Whether it is a critical automotive component, medical device or aerospace component, manufacturing accuracy affects the reliability and functionality of the final product.
③ Customized Solutions for Unique Challenges:
In industries where generic solutions cannot meet the needs, machined plastic parts shine. The ability to customize components to unique specifications enables manufacturers to meet specific challenges and requirements, thereby promoting innovation and efficiency.
④ Reduced Material Waste:
Precision machining reduces material waste by selectively removing material to achieve the desired shape. This not only improves cost-effectiveness, but also meets environmentally friendly manufacturing practices, emphasizing sustainability.
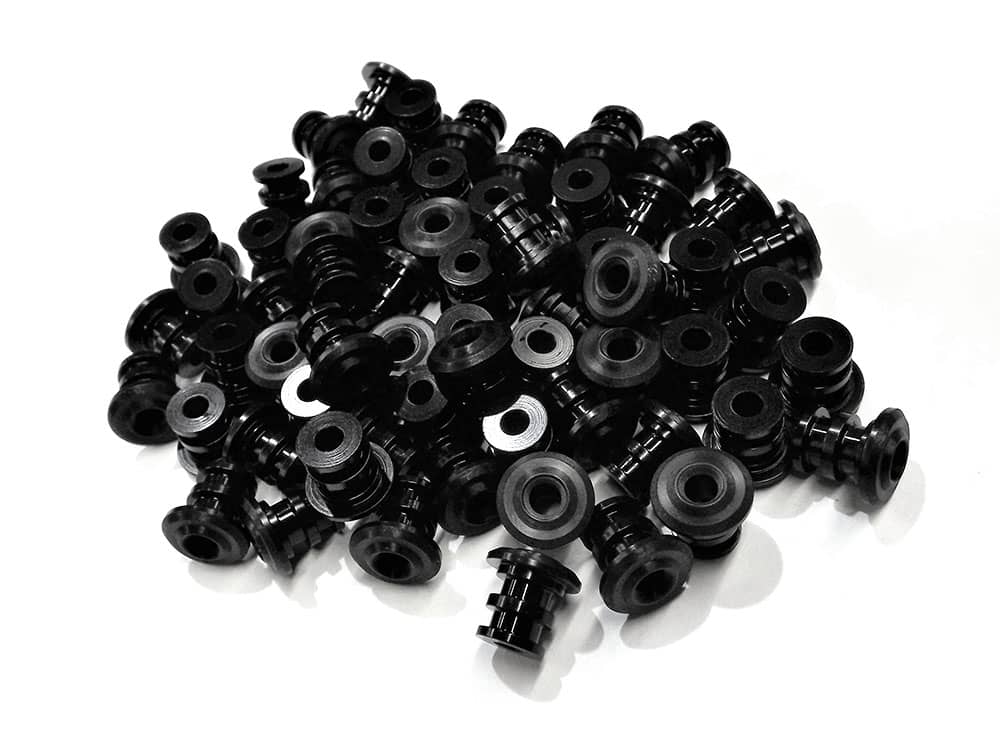
2.Explore the Different Types of Plastics Commonly Used in Machining
Understanding the different types of plastics commonly used in machining is essential for industries seeking precise and customized solutions.
1) Acrylonitrile Butadiene Styrene (ABS):
Features:
- Excellent impact resistance
- High tensile strength
- Good processability
Applications:
- Prototype design
- Automotive parts
- Consumer goods
2) Polyethylene (PE):
Features:
- Lightweight
- Chemical resistance
- Low moisture absorption
Applications:
- Food packaging
- Medical parts
- Conveyor parts
3) Polypropylene (PP):
Features:
- Low density
- High resistance Chemical resistance
- Low hygroscopicity
Applications:
- Laboratory equipment
- Automotive parts
- Packaging
4) Polyvinyl chloride (PVC):
Features:
- High chemical resistance
- Good electrical insulation
- Flame retardant options available
Applications:
- Electrical components
- Building materials
- Signage
5) Polycarbonate (PC):
Features:
- Excellent transparency
- High impact resistance
- High temperature resistance
Applications:
- Optical lenses
- Medical equipment
- Aviation Aerospace parts
6) Polyethylene terephthalate (PET):
- High strength
- Dimensional stability
- Good chemical resistance
Applications:
- Bearings
- Gears
- Electrical insulators
7) Polyoxymethylene (POM) or polyoxymethylene:
Features:
- Low friction
- High stiffness
- Excellent wear resistance
Applications:
- Gears and bushings
- Mechanical precision parts
- Automotive parts
8) Polytetrafluoroethylene (PTFE):
Features:
- Low friction
- Excellent chemical resistance
- Wide temperature range
Applications:
- Seals and gaskets
- Bearings
- Electrical insulation
9) Nylon (polyamide):
Features:
- High tensile strength
- Excellent wear resistance
- Self-lubricating
Applications:
- Bearings and bushings
- Gears
- Structural components
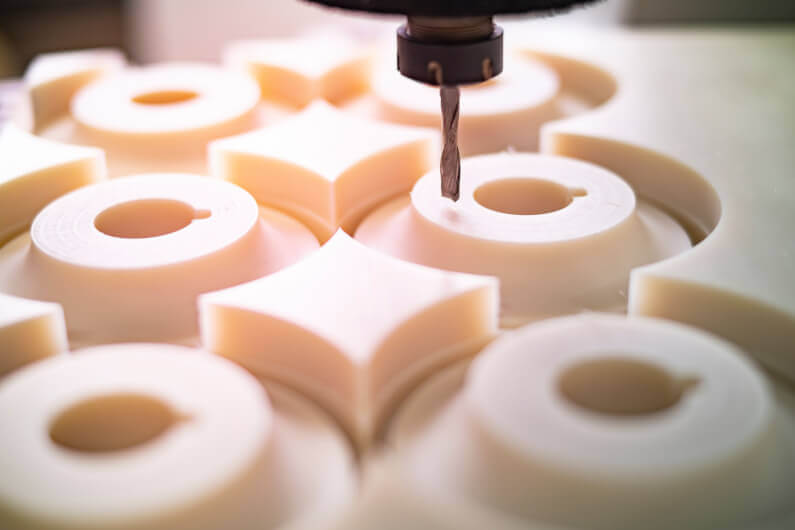
3.Cross-industry applications
1) Automotive: Precision in motion
In the automotive sector, machined plastic parts have become an indispensable component that is both beautiful and practical. Here is how they are seamlessly integrated:
- Interior components
Machined plastic parts are used to make complex interior components such as dashboards, instrument clusters, and trims. The precision of machining ensures a seamless fit and finish.
- Engine parts
Components within the engine compartment, including housings, brackets, and intake manifolds, benefit from the durability and heat resistance of machined plastic parts. - Exterior elements
From sleek grilles to aerodynamic body panels, machined plastic parts help enhance the aesthetics of a vehicle’s exterior while maintaining a balance between form and function.
2) Aerospace: Lightweight, durable, and enhanced performance
The aerospace sector requires components that are both lightweight and can withstand extreme conditions. Machined plastic parts meet the challenges:
- Lightweight components
Known for their superior strength-to-weight ratio, machined plastic parts are widely used in aerospace components, as reducing weight is critical to improving fuel efficiency and overall performance. - Long-lasting solutions
From cabin interior components to critical structural parts, machined plastic parts help improve the durability of aerospace systems and provide reliable solutions for demanding environments.
3) Medical: Precision treatments
In the medical field, where precision and biocompatibility are critical, machined plastic parts provide tailored solutions for a variety of applications:
- Equipment and devices
Surgical instruments, diagnostic equipment, and medical devices often use machined plastic parts because they are high-precision, biocompatible, and can meet strict hygiene standards. - Biocompatible components
Machinery plastic parts play a vital role in implantable medical devices, where biocompatible materials are essential to ensure patient health.
4) Electronics: Powering connectivity
The electronics industry relies on machined plastic parts to ensure seamless connectivity, protection, and functionality:
- Electronics
Housings for electronic devices, connectors, and insulating components benefit from the precision machining of plastics, providing protective and functional housings for sensitive electronic devices. - Housings and connectors
Machinery plastic parts provide the necessary insulation and structural support for electronic housings and connectors, ensuring reliable performance of electronic systems.
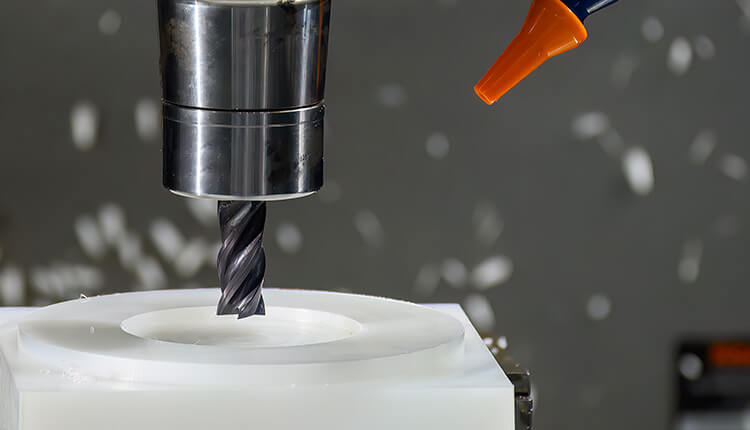
4.Machining of plastic parts
Machining of plastic parts is the embodiment of precision engineering, providing the industry with the flexibility and accuracy required to manufacture complex components.
Let’s take a deep dive into the key machining processes that shape the world of plastic part manufacturing, ensuring that each part meets strict standards and unique specifications.
1) CNC machining: precision is at the core
Definition:
CNC machining is a versatile and widely used process that uses computer-controlled machines to precisely remove material from plastic workpieces to create the intended shape with fine precision.
How it works:
- Design specifications are translated into a computer-aided design (CAD) model.
- CNC machines equipped with cutting tools follow these digital instructions to carve, mill or form plastic materials into the final product.
Advantages:
- Unparalleled precision: CNC machining provides micron-level accuracy, ensuring that each plastic part meets tight tolerances.
- Versatility: Applicable to a wide range of plastic materials, from ABS and PVC to high-performance thermoplastics.
2) Thermoforming: Forming possibilities
Definition:
Thermoforming involves heating a plastic sheet until it is pliable, then stretching and forming it over a mold to form the desired shape, which is then trimmed into the final product.
How it works:
- A plastic sheet is heated until it becomes malleable.
- The heated sheet is draped over a mold to form the desired shape.
- The molded part is cooled and trimmed to meet specifications.
Advantages:
- Cost-effective: Thermoforming is generally more economical for large, simple parts.
- Rapid prototyping: Great for creating prototypes and small batches.
3) Injection molding: Mastering mass production
Definition:
Injection molding is a manufacturing process that requires injecting molten plastic material into a mold cavity. It subsequently cools and solidifies to form the desired plastic part.
How it works:
- Plastic pellets are melted under high pressure and injected into the mold.
- The mold is then cooled to allow the plastic to solidify and the part to be ejected.
Advantages:
- High efficiency: Good for mass production of identical plastic parts.
- Complex geometries: Injection molding can create intricate shapes.
4) CNC engraving: Cutting precision
Definition:
CNC routing is a subtractive manufacturing process that utilizes a computer-controlled router to cut, trim, and shape plastic materials into specific designs.
How it works:
- A computer-guided router cuts plastic materials along a predetermined path.
- Good for creating high-precision 2D and 3D shapes.
Advantages:
- Versatility: Can be used in a variety of plastic materials and thicknesses.
- Customization: Great for creating complex designs and intricate shapes.
5) Waterjet Cutting: Fluid Precision
Definition:
Waterjet cutting uses a high-pressure stream of water to combine water with abrasive particles to achieve precise cutting of plastic materials.
How it works:
- A waterjet machine uses a nozzle to eject high-speed water and abrasive particles, resulting in precise cutting.
- Suitable for a wide range of plastic materials without causing heat-related damage.
Advantages:
- Minimum material stress: Waterjet cutting does not subject the material to thermal stress.
- Precision: Suitable for cutting complex shapes with high precision.
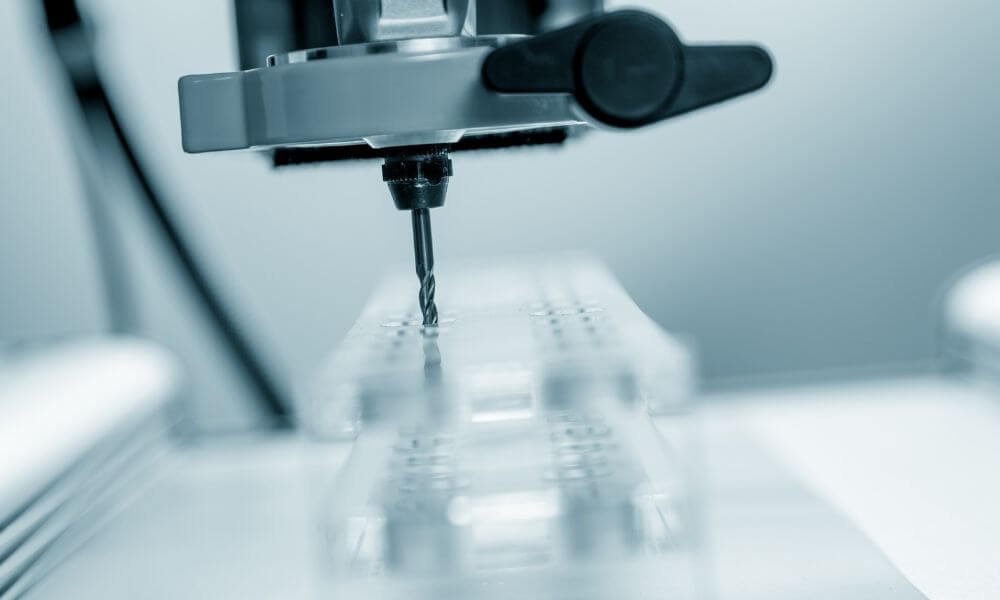
5.Challenges and Solutions for Machining Plastic Parts
The world of plastic part machining is one of innovation and precision, but it is not without its challenges.
This section delves into the obstacles faced in the manufacturing process of machined plastic parts and explores clever solutions that are driving the industry forward.
1) Material Selection Challenges: Meeting Diverse Needs
Challenges:
Choosing the right plastic material for a specific application can be difficult, given factors such as strength, high temperature resistance, and chemical compatibility.
Solutions:
- Material Expertise: Hire engineers with expertise in plastic properties to ensure optimal material selection.
- Testing and Prototyping: Rigorous testing and prototyping help evaluate material performance under real-world operating conditions.
2) Tool Considerations: Maintaining Precision
Challenges:
Tool wear during machining affects precision and increases costs over time.
Solutions:
- High-quality tools: Investing in high-quality cutting tools ensures long-term durability and continued precision.
- Regular Maintenance: Implementing a proactive maintenance program minimizes the risk of tool-related issues.
3) Machining Parameters and Settings: A Balancing Act for Efficiency
Challenges:
Fine-tuning machining parameters such as feed rates and speeds for different plastics can be complex, affecting efficiency and product quality.
Solutions:
- Advanced CNC Programming: Advanced CNC programming allows you to optimize machining parameters for each specific plastic.
- Continuous Monitoring: Implementing a real-time monitoring system ensures that adjustments can be made in a timely manner to achieve optimal efficiency.
4) Heat Dissipation Considerations: Precision at High Temperatures
Challenges:
Machining plastics generates heat, which can lead to potential thermal damage and deformation.
Solutions:
- Coolant Systems: Implementing an effective coolant system dissipates heat during machining.
- Precision Cooling: Employing a precision cooling strategy helps maintain material integrity.
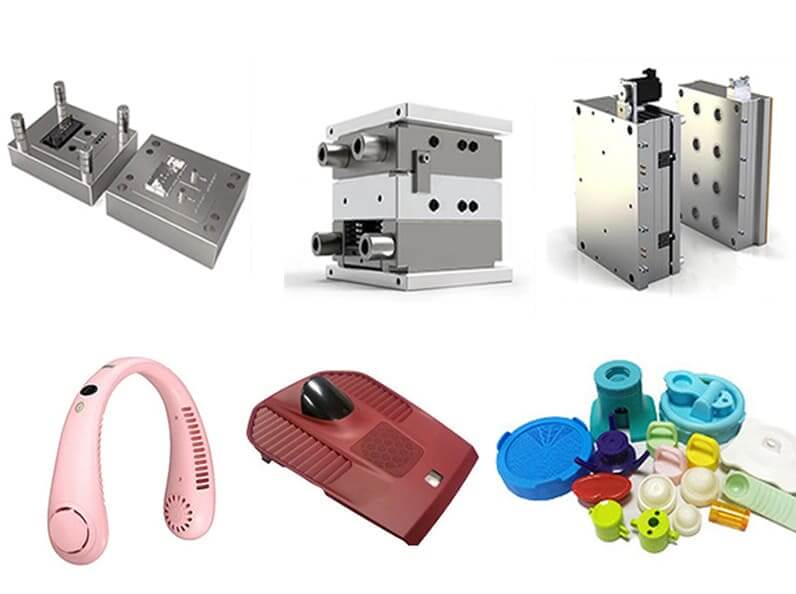
5) Environmental Impact: A Sustainable Approach
Challenges:
Environmental concerns regarding plastic waste and the carbon footprint of the machining process.
Solutions:
- Sustainable Practices: Employ sustainable machining practices, including recycling and waste reduction.
- Material Innovation: Explore environmentally friendly plastic alternatives that maintain performance standards.
6) Design Complexity: Navigating Intricacies
Challenges:
Creating complex designs with intricate features can present challenges in terms of machining feasibility.
Solutions:
- Collaborative Design: Encourage collaboration between design and machining teams to ensure designs are practical and efficient.
- Advanced Machining Technologies: Leverage advanced machining technologies, such as multi-axis machining, to perform complex designs.
6.Conclusion
In summary, machined plastic parts are more than just parts; they are a reflection of craftsmanship, innovation, and a relentless pursuit of excellence.
As the industry evolves, so too will the role and impact of machined plastic parts, ensuring that future parts not only meet today’s needs, but also anticipate tomorrow’s challenges.
If you are looking for an experienced machining manufacturer, Xavier is your ideal choice. The Xavier team is well-equipped to provide high-quality machining solutions. If you need more information or to discuss your machining needs with us, please feel free to contact us.