Advantages of Additive Manufacturing
Since the advent of additive manufacturing, 3D printing hardware and material suppliers have considered the aerospace industry as an important target for their products. The definition of additive processing is also simple, machining services tailored to the needs of the aerospace industry, also known as 3D printing.
Aircraft are highly complex systems with a variety of parts, so they will benefit from cutting-edge developments in production tools and materials, especially those that can reduce weight or increase the strength of parts. Some 3D printing processes claim to achieve both.
Unfortunately, this does not mean that the aerospace industry is adopting additive manufacturing faster than other industries. In fact, since aircraft and their many components must undergo the most rigorous certification and testing procedures (for obvious reasons), 3D printed aerospace parts can take years or even decades to go from concept to implementation. The technology is there, but the knowledge gained from years of testing and observation is not. Therefore, it is much easier to implement additive manufacturing in lower-risk industries where fewer lives are involved.
While the implementation of 3D printed aerospace products may be slow, the parts that have been successful are already having a significant impact on the industry. From simple parts like 3D printed cabin walls to absolutely critical parts like additively manufactured metal engine components, AM is undoubtedly starting to take off in one of the most lucrative and fastest-growing industries in the world. This article outlines some of the ways AM is being used in the aerospace industry and how it could be used in the future.
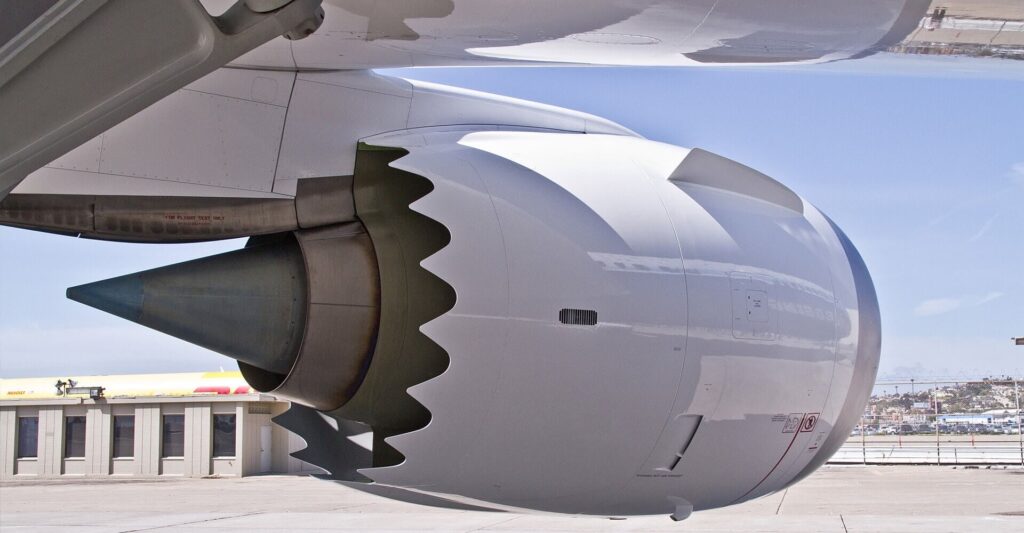
1.Lightweighting vs. Strength Optimization
There are significant differences between additive and subtractive manufacturing, and dilemmas often arise when choosing between 3D printing and traditional manufacturing methods. One of the key differences is the ability to shape the internal geometry of the part. Additive manufacturing is extremely useful in the aerospace industry, where it can create parts with partially hollow interiors and complex geometric patterns to maximize internal strength without adding weight.
3D printers build parts from the bottom up, creating mesh-like structures inside things like metal engine parts or plastic cabin bulkheads that cannot be done with traditional molding or machining.
The importance of lattice structure in the aerospace field cannot be ignored. When building an aircraft, every gram counts, and additive manufacturing can significantly reduce component weight through partially hollow lattice structures. The thin wire-like lattice is arranged in a mathematically optimized way that both increases strength and reduces stress, ensuring lightweight parts are as strong as or better than solid ones. At the same time, the space between the lines is weightless, further reducing the overall weight of the component.
For example, researchers at Boeing’s HRL Laboratory have developed an extremely lightweight metallic material with a lattice structure of interconnected hollow tubes, demonstrating the potential of additive manufacturing to optimize lightweighting and strength. As research continues, aerospace companies will increasingly adopt additive manufacturing technology.
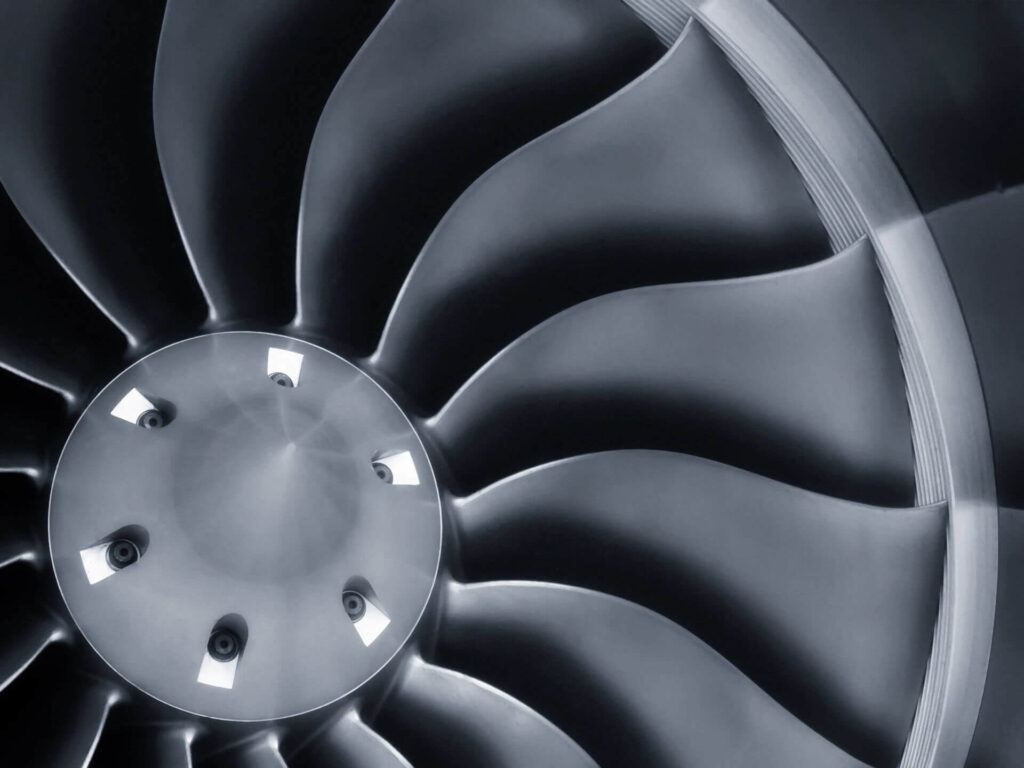
2.Prototypes and Spare Parts
One of the main benefits of additive manufacturing is the ability to manufacture parts in-house on demand. 3D printers can be installed anywhere and operate largely autonomously, allowing for extremely short lead times for parts. This means that aerospace companies can quickly manufacture new versions of parts for testing, shortening the development process and speeding up part completion.
As a result, faster prototyping is one of the main uses of additive manufacturing in the aerospace sector. According to additive manufacturing giant Stratasys, using in-house 3D printing to make aerospace prototypes takes about 43% less time than injection molding and CNC tools, and about 75% less time than 2D laser cutting.
The aerospace industry can also benefit from additive manufacturing when it comes to inventory maintenance. A commercial aircraft is made up of about 4 million parts, not all of which are produced by the same manufacturer, which results in aircraft suppliers having to stockpile a large number of spare parts, costing a lot of money and storage space.
3D printers offer an effective solution here. By keeping a 3D printer on site and keeping a digital library of spare parts in a printable format, companies can use 3D printed parts when needed without filling up giant warehouses with large quantities of expensive spare parts. This digital spare parts library strategy is gradually being adopted by multiple industries, and the aerospace industry is expected to be one of the biggest beneficiaries.