Why Aluminum CNC Machining Services Are So Popular
Aluminum CNC machining services provide a precise and efficient method of forming aluminum parts for a wide range of equipment, tools, and fixtures. Atlas Machining has a range of equipment to meet your machining project needs.
These services utilize computer numerical control (CNC) technology to create complex designs using sheet metal, aluminum blocks, and extrusions. The importance of aluminum CNC machining lies in its ability to ensure reliability and consistency, and its ability to manufacture parts with tight tolerances.
Aluminum is a durable and lightweight material, which, combined with the precision of the CNC machining process, makes it ideal for manufacturing prototypes, end-use parts, and functional components for the aerospace, electronics, and automotive industries.
This article explores the benefits of aluminum CNC machining services and some of their latest trends.
1.Benefits of Aluminum CNC Machining Services
1) Lightweight and High Strength
Aluminum is highly regarded for its excellent strength-to-weight ratio, making it a popular choice across a variety of industries such as aerospace, automotive, and consumer electronics. CNC machining can precisely shape and manufacture aluminum parts without compromising its lightweight properties.
2) High Precision
CNC machining offers unparalleled precision and accuracy in producing precision aluminum parts with tight tolerances. This is critical for industries such as aerospace and automotive, where parts must meet stringent quality standards and precise specifications.
3) Versatility
Aluminum is a versatile material that can be machined into a wide range of shapes, sizes, and geometries. CNC machining is able to produce complex parts with intricate features, making it suitable for a wide range of applications across a variety of industries.
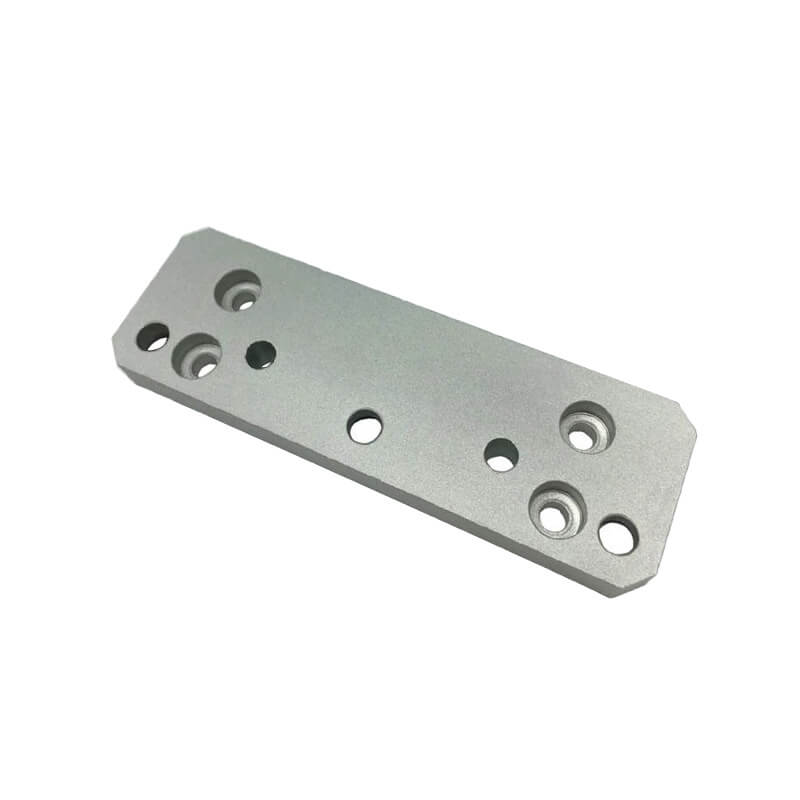
4) Cost-effectiveness
Despite its superior properties, aluminum is relatively inexpensive compared to other metals such as titanium or stainless steel. CNC machining allows for efficient material utilization and high productivity, resulting in cost-effective production of aluminum parts.
5) Material properties
Aluminum has excellent corrosion resistance, thermal conductivity, and electrical conductivity, making it suitable for a wide range of applications from heat sinks and electronic housings to structural components and decorative elements.
6) Ease of machining
Aluminum is known for its ease of machining, which means that it is easier to cut, drill, and shape than other metals. This can reduce machining time and tool wear, which can help save overall costs in the production process.
7) Recyclability
Aluminum is highly recyclable and there is no loss of quality during the recycling process. This sustainability is becoming increasingly important for industries seeking to reduce their environmental footprint and adhere to eco-friendly practices.
8) Design Flexibility
CNC machining offers designers and engineers unparalleled design freedom when working with aluminum. Complex geometries, intricate features, and custom shapes can be easily achieved, allowing for innovative and optimized product designs.
9) Industry Demand
Industries such as aerospace, automotive, electronics, and medical devices are experiencing a growing demand for lightweight, high-performance parts made from aluminum. As these industries continue to expand and innovate, the demand for aluminum CNC machining services is expected to rise further.
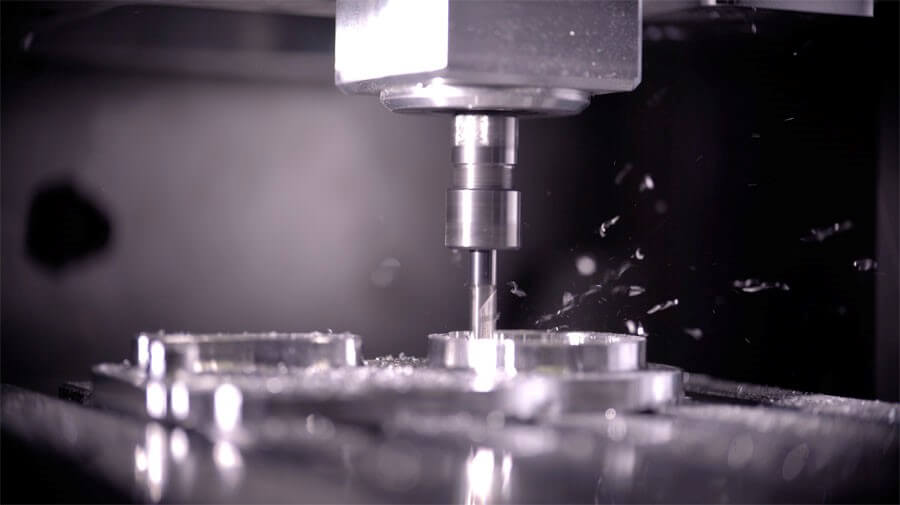
2.Latest Trends and Innovations in Aluminum CNC Machining Services
In the field of aluminum CNC machining services, several trends and innovations have emerged to improve efficiency, precision, and versatility. Here are some of the latest developments:
1) High-Speed Machining (HSM)
HSM technology involves cutting aluminum at significantly higher speeds and feeds while maintaining precision. This approach reduces cycle times and increases productivity, making it increasingly popular in aluminum machining.
2) Tool Innovation
Innovations in cutting tool technology, such as coated carbide and polycrystalline diamond (PCD) tools, extend tool life and improve surface finish. In addition, tool solutions tailored for aluminum machining are becoming more common to address specific challenges and optimize performance.
3) Simulation and Modeling
Using advanced software for simulation and modeling, manufacturers can optimize machining processes before production begins. This helps predict and prevent problems such as tool wear, vibration, and material deformation, thereby improving efficiency and saving costs.
4) Integration of IoT and Data Analytics
Installing IoT sensors in CNC machines can monitor various parameters such as temperature, vibration, and tool wear in real time. Combined with data analytics, this information helps predictive maintenance, process optimization, and quality control.
5) Additive Manufacturing (AM) Integration
The combination of AM and traditional CNC machining processes opens up new possibilities for complex component design and lightweight structures. Hybrid manufacturing technologies, such as additive deposition after CNC machining, can produce components with greater functionality and less material waste.
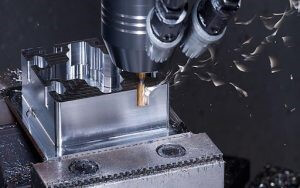
6) Green Machining Practices
With sustainability gaining traction, manufacturers are adopting green machining practices in aluminum CNC machining. This includes optimizing cutting parameters to minimize energy consumption, recycling coolant and chips, and using environmentally friendly lubricants and coolants.
7) Precision Micromachining
Precision micromachining of aluminum is gaining popularity as demand for miniature components grows in industries such as electronics, medical devices, and aerospace. Advanced CNC machines are capable of sub-micron accuracy, enabling the manufacture of complex features on small components.
8) On-Demand Manufacturing Services
The rise of on-demand manufacturing services and digital platforms has made aluminum CNC machining more accessible for prototyping, low-volume production, and custom part manufacturing. These platforms connect customers to a network of vetted machining shops, streamlining the procurement and production process.
9) Industry 4.0 Integration
Industry 4.0 principles, including automation, connectivity, and data exchange, are being incorporated into aluminum CNC machining operations. Smart factories equipped with networked machines and intelligent systems enable seamless communication and coordination, resulting in increased productivity and flexibility.
By leveraging these trends and innovations, aluminum CNC machining services continue to evolve, offering greater efficiency, precision, and versatility to meet the diverse needs of industries ranging from automotive and aerospace to electronics and consumer goods.