Advantages of Aluminum Prototypes and Their Manufacturing Process Introduction
1.Top Ten Advantages of Aluminum Prototypes
1) Fast Turnaround Time
The ductility of aluminum and the efficiency of the manufacturing process facilitate fast turnaround, which is essential to meeting tight project timelines.
2) Cost-effectiveness of Prototyping
Compared to other materials, aluminum has proven to be cost-effective, providing high-quality prototypes without breaking the bank.
3) Iterative Design Opportunities
The flexibility of aluminum prototyping allows for rapid iterations, helping to improve designs based on testing and feedback.
4) Superior Functional Performance
Aluminum prototypes exhibit superior functional performance, meeting the stringent requirements of various industries.
5) Higher Heat Resistance
With its high thermal conductivity, aluminum prototypes can withstand high temperatures, making them suitable for thermally challenging applications.
6) Better Aesthetics
Surface treatments and coatings enhance the aesthetics of aluminum prototypes, ensuring that the final product is visually appealing.
7) Testing Accuracy
Prototypes made from aluminum have high testing accuracy, which is essential for validating designs and ensuring that they meet specifications.
8) Better for Mass Production
Aluminum is suitable for mass production, making it an ideal choice for industries that require large quantities of high-quality prototypes.
9) Increased investor interest
The use of aluminum prototypes not only demonstrates a commitment to quality, but also attracts investor interest due to the material’s positive attributes.
10) Superior strength
Despite its lightweight nature, aluminum prototypes have exceptional strength that contributes to their durability and reliability.
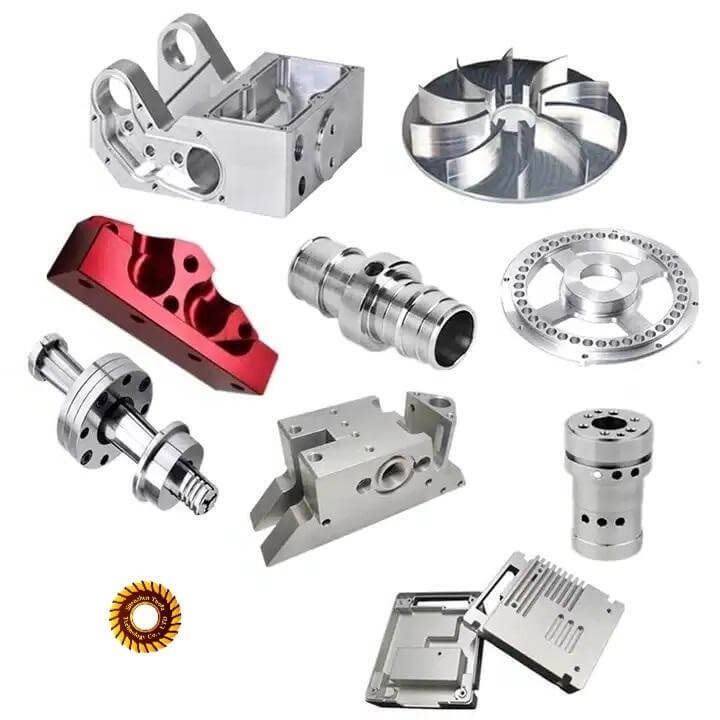
2.Applications of aluminum prototypes
Aluminum prototypes can give us an idea of how the final product will perform, allowing for critical evaluations and modifications before mass production. China TuoFa has been producing aluminum prototypes since 2006, which can be used in the following common areas:
1) Aerospace parts
In an industry where every gram counts, aluminum prototypes are invaluable for testing components such as turbine blades, fuselage panels, and landing gear assemblies. Their lightweight properties greatly improve fuel efficiency and the overall performance of aircraft.
2) Automotive component testing
The automotive industry relies on aluminum prototypes to test and refine parts such as engine blocks, transmissions, and chassis components. These prototypes help evaluate factors such as weight reduction, heat dissipation, and structural integrity.
3) Heavy machinery development
In areas such as construction and mining, aluminum prototypes are used to design and test heavy machinery components. This includes parts such as hydraulic systems, gears and armatures, where strength and reliability are critical.
4) Medical Device Prototyping
The medical industry benefits from the precision and safety provided by aluminum prototypes. They are used to develop surgical instruments, diagnostic equipment and medical machinery housings, ensuring the highest standards of hygiene and quality.
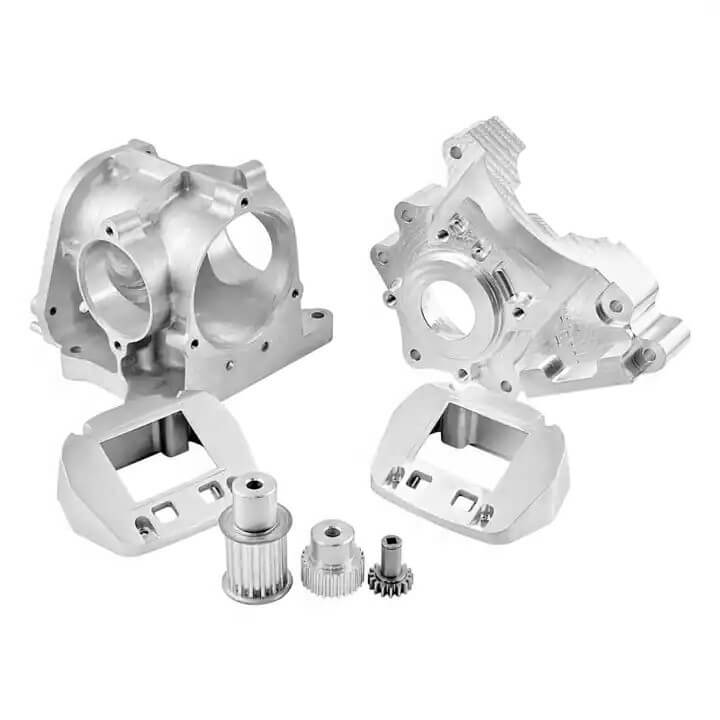
3.Aluminum Prototyping Process
Aluminum prototyping involves a variety of technologies, each suitable for different stages of the design process and with unique advantages. Here are 10 common technologies used in aluminum prototyping:
1) Aluminum Prototype CNC Machining
Computer numerical control (CNC) machining is a subtractive process that uses a variety of cutting tools to remove material from a solid block of aluminum. It is highly accurate and can produce complex geometries. Review Aluminum Machining Services China Tuofa
① Advantages of CNC Machining Aluminum
- Allows complex designs;
- Rapid prototyping;
- Minimizes material waste;
- No special tools or molds are required.
② Disadvantages of CNC Machining Aluminum
- Limited strength compared to other methods; post-processing is often required to achieve a smooth surface finish;
- Can be expensive for large parts.
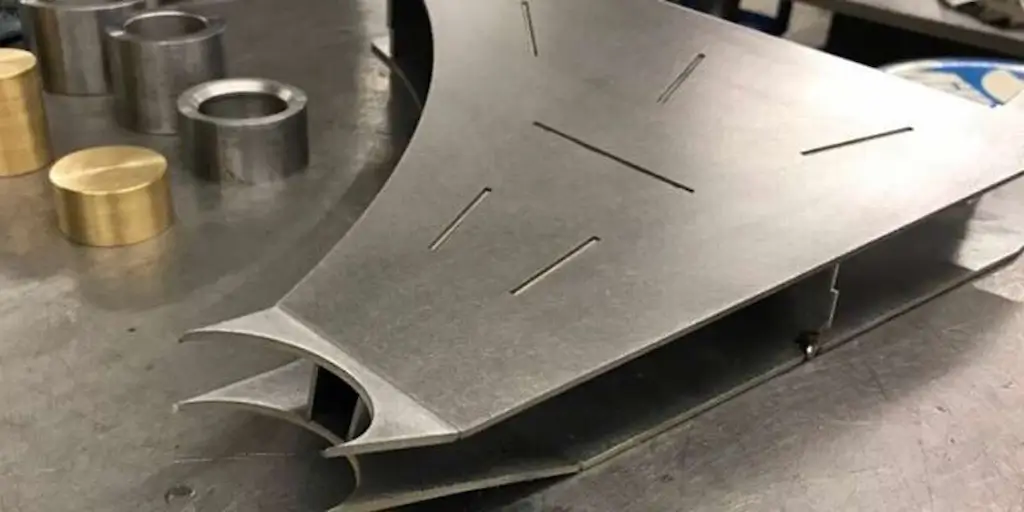
2) 3D Printed Aluminum Prototypes (Additive Manufacturing)
3D printed aluminum is becoming more and more common. It allows for the creation of complex and intricate designs that are difficult or impossible to achieve with traditional manufacturing methods.
① Advantages of aluminum 3D printing
- Allows for complex designs;
- Rapid prototyping;
- Minimizes material waste;
- No special tools or molds are required.
② Disadvantages of aluminum 3D printing
- Limited strength compared to other methods;
- Post-processing is often required to achieve a smooth surface finish;
- Can be expensive for large parts.
3) Die casting
The process involves pressing molten aluminum into a mold cavity under high pressure. It is suitable for mass production of thin-walled and complex geometric parts.
① Advantages of aluminum die castings
- High productivity;
- Excellent dimensional accuracy;
- Smooth casting surface;
- Thin walls can be cast.
② Disadvantages of aluminum die casting
- High initial mold cost;
- Limited to large-scale production for cost-effectiveness;
- Porosity may be a problem.
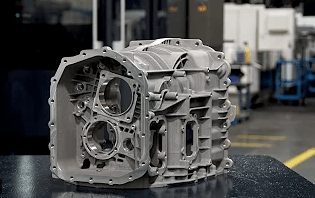
4) Investment casting (lost wax casting)
This method involves creating a wax model of the part, which is then encapsulated in a ceramic material. Once the ceramic hardens, the wax melts and molten aluminum is poured into the cavity.
① Advantages
- Excellent surface finish and dimensional accuracy;
- Ability to produce complex shapes; Suitable for small and medium-sized parts.
② Disadvantages
- High mold and material costs;
- Labor-intensive process;
- Not suitable for very large parts.
5) Sand casting
This is one of the oldest and simplest aluminum casting methods, where molten aluminum is poured into a sand mold. It is best suited for large parts with relatively simple geometries.
① Advantages
- Low mold cost;
- Suitable for large parts;
- Can produce very large parts;
- Flexible in size and shape.
②Disadvantages
- Rougher surface finish than other methods;
- Lower dimensional accuracy; slower production speed.
6) Sheet metal prototyping
This involves cutting, bending and assembling aluminum flat sheets into the desired shape. It is well suited to creating housings, brackets and other thin parts.
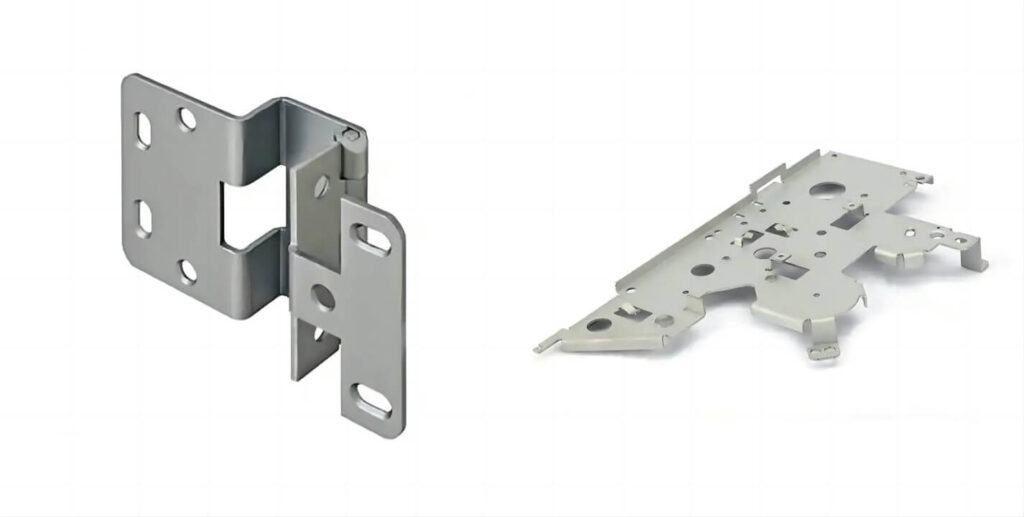
7) Extrusion processing
Aluminum extrusion is a process in which aluminum alloy is forced through a die with the desired cross-section to produce long parts with uniform cross-sections, such as frames and rails.
① Advantages of aluminum extrusion
- Efficient production of parts with uniform cross-sections;
- High productivity; excellent material utilization.
② Disadvantages of aluminum extrusion
- Limited to profiles with constant cross-sections;
- Initial tooling can be costly;
- Limited to simpler shapes.
8) Casting
Forging involves shaping aluminum by applying compressive force. It is known for producing parts with high strength and durability, such as gears and structural components.
① Advantages
- The parts produced are strong and reliable;
- Excellent material utilization;
- Suitable for high stress applications.
②Disadvantages
- Limited to simpler shapes;
- High mold cost;
- Not suitable for complex designs.
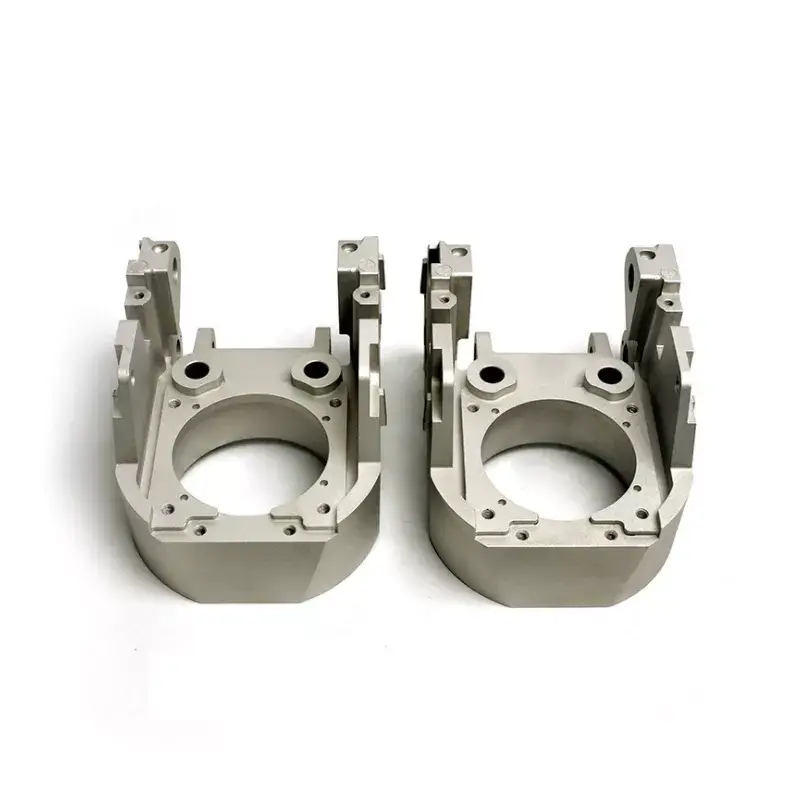
9) Electrospark Machining (EDM)
EDM is a manufacturing process that uses electric sparks to remove material to shape metal. It involves using dielectric fluids and electrodes to produce discharges to erode aluminum materials. The technology is particularly useful for creating intricate details and complex geometries that are difficult to achieve with traditional machining methods. It is particularly valuable for making tools, molds, and precision parts with tight tolerances and fine features.
①Advantages
- Ability to produce complex, intricate shapes;
- High precision;
- No direct contact with the material, reducing the risk of mechanical stress.
②Disadvantages
- Slow process;
- High operating costs;
- Limited to conductive materials.
10) Aluminum Laser Cutting and Engraving
This method uses high-powered lasers to cut or engrave flat aluminum sheets. It is very precise and can create intricate details, making it suitable for decorative elements or complex components.
①Advantages
- High precision and good repeatability;
- Can create complex patterns and details;
- Fast processing of thin materials.
②Disadvantages
- Limited to flat or slightly curved surfaces;
- High energy consumption;
- Costs can be high for thicker materials.
Each of these processes has its own unique advantages and limitations, and they are more or less suitable depending on the specific requirements of the aluminum prototype being manufactured. Each technology provides a balance of precision, speed, cost, and applicability for different types of designs, making it a valuable tool in the prototyping process.