Increased productivity and efficiency in manufacturing processes with centerless grinding
Centerless grinding is a machining process that is becoming increasingly popular in the manufacturing industry due to its numerous benefits. This article will explore the benefits of centerless grinding, focusing on improving productivity and efficiency in the manufacturing process.
1.No Centers or Fixtures Required
Traditional grinding methods require the use of centers or fixtures to hold the workpiece in place, which can be time-consuming and costly. With centerless grinding, the workpiece is supported by the working blade and regulating wheel, eliminating the need for additional fixtures.
Not needing a fixture not only saves time, it also increases productivity. Grinding machines can process multiple parts at once, thanks to their high-speed grinding wheels and the ability to grind multiple diameters at once. This means manufacturers can produce more parts in less time, increasing productivity and efficiency.
2.Excellent Dimensional Accuracy and Surface Finish
The grinding wheel and regulating wheel work together to remove material from the workpiece, ensuring precise and consistent results. This level of accuracy is essential in industries such as aerospace and automotive that require tight tolerances.
3.Excellent Roundness Control
The regulating wheel acts as a guide for the workpiece, ensuring it remains centered during the grinding process. This results in a perfectly round part, which is essential for applications where concentricity is critical.
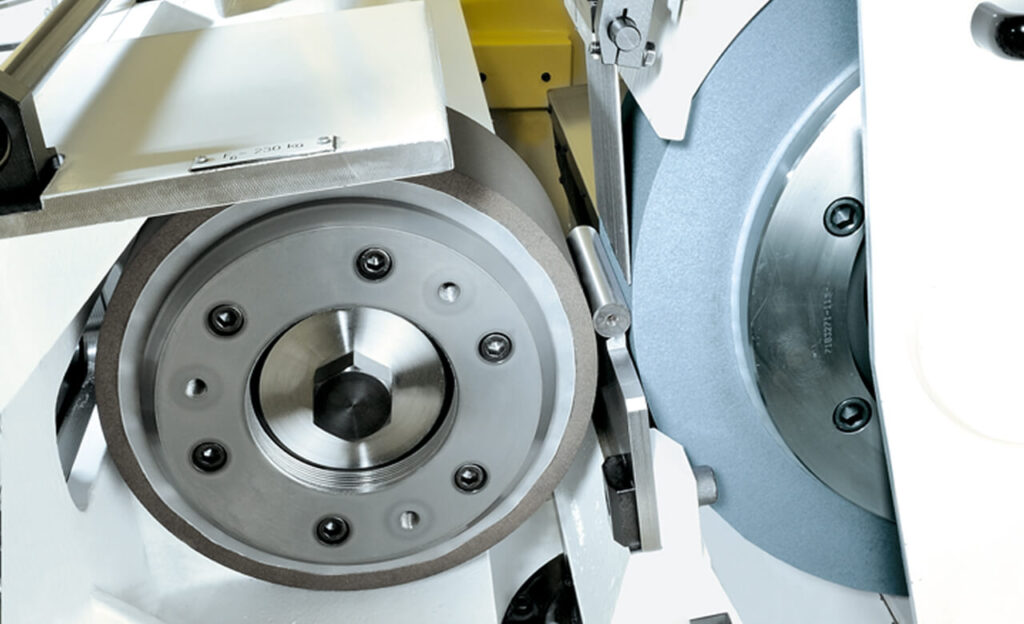
4.Versatility
It can be used to grind a wide range of materials, including metals, plastics, and ceramics. This versatility makes centerless grinding suitable for a wide range of industries, from automotive and aerospace to medical and electronics.
5.Cost-effective
Centerless grinding is a cost-effective solution for manufacturers. The ability to process multiple parts at once without the need for fixtures reduces setup and labor costs. Additionally, high-speed grinding wheels and the ability to grind multiple diameters at once reduce cycle times, further reducing production costs.
6.Reliability and ease of use
They are designed to withstand heavy use and require minimal maintenance. This means that manufacturers can rely on centerless grinders to provide consistent results without frequent repairs or downtime.
In summary, centerless grinding offers many advantages that help improve the productivity and efficiency of the manufacturing process. It grinds materials without fixtures and is able to process multiple parts simultaneously, saving time and money. The dimensional accuracy, roundness control, and versatility of centerless grinding make it suitable for a wide range of industries.
In addition, its cost-effectiveness, reliability, and ease of use also make centerless grinding a top choice for manufacturers. With all these advantages, centerless grinding has become an integral part of the modern manufacturing process.