Wire EDM Impellers:Advantages analysis
When using wire EDM to machine impellers, there are the following advantages and applicable scenarios:
1.High-precision machining of wire EDM
It is a non-contact machining method that cuts the material by electrical discharge, so it can achieve very high machining accuracy. This is very important for applications that require high-precision impeller contours, such as the aerospace, automotive and energy industries.
2.Complex shape machining
Wire EDM can be used to machine impellers with complex shapes, including spiral blades and very small blades. Since it is based on pre-programmed paths, it can achieve almost any impeller shape.
Hard material machining: Impellers are usually made of high-strength and wear-resistant materials, such as titanium alloys, nickel-based alloys, etc. Wire EDM can effectively machine these hard materials because it does not rely on traditional cutting tools, but cuts by electric spark discharge.
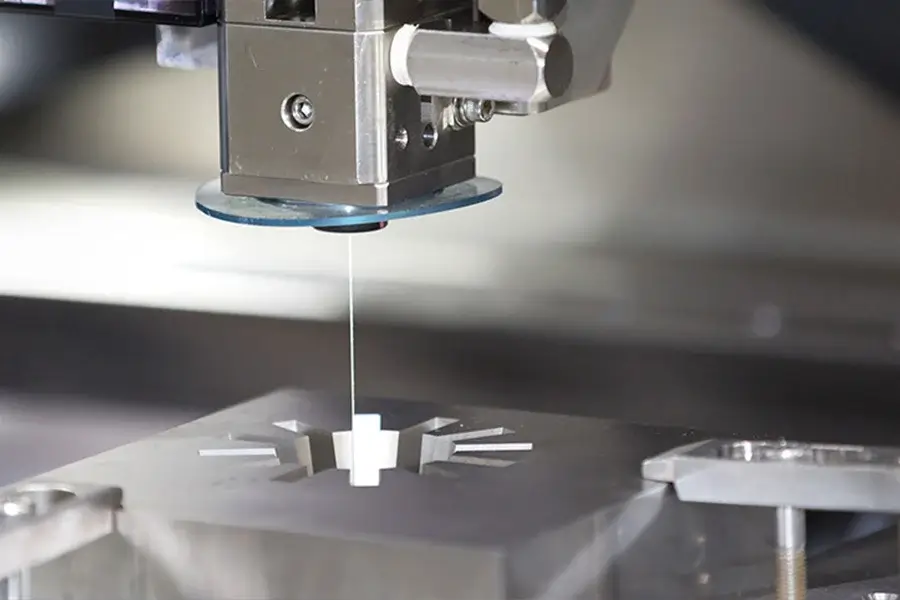
3.Deformation-free machining
Since it is a non-contact process, no high forces are applied or heat-affected zones are generated, thus avoiding material deformation. This is very important for applications where the impeller shape and dimensional stability must be maintained.
4.Mass production and automation
Wire EDM can be applied to situations where impellers are produced in large quantities. Once the program is written, it can be processed continuously in an automated manner to improve production efficiency.
In general, the advantages of wire cutting impellers are high precision and complex shape processing capabilities, suitable for hard materials and applications that require shape stability. It is an advanced processing method suitable for specific impeller requirements.