Different applications of compression molding in aerospace
Compression molding is a widely used manufacturing process that involves shaping materials through the application of heat and pressure. The technology is widely used in various industries, including aerospace. In this article we will look at the different applications of compression molding in the aerospace sector.
Compression molding in aerospace applications
1.One of the main applications is the production of composite parts. Composite materials such as carbon fiber reinforced polymer (CFRP) have an excellent strength-to-weight ratio, making them ideal for aerospace applications. Compression molding can efficiently and economically produce complex composite parts with high structural integrity.
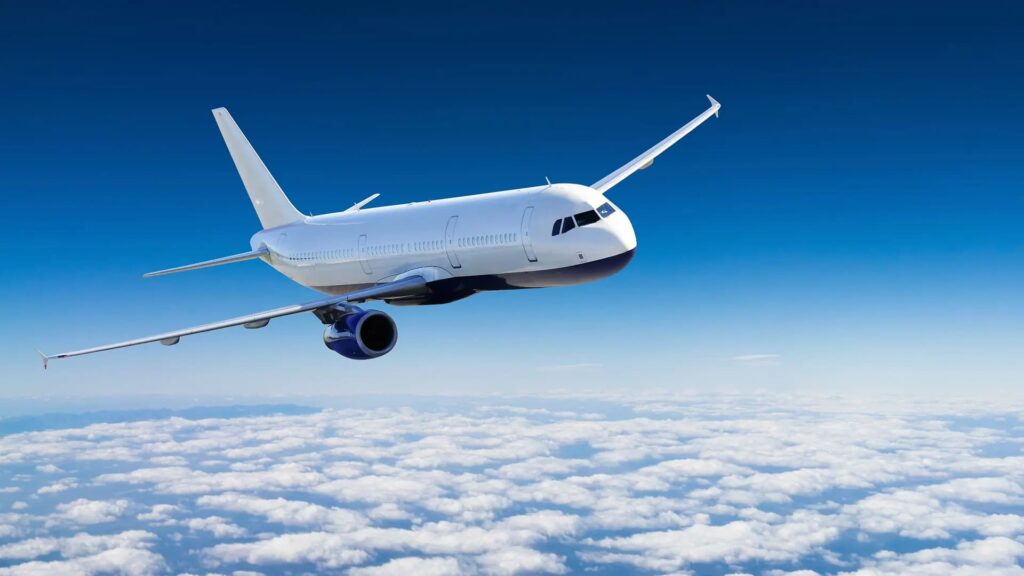
2.Produces components such as aircraft panels, fairings and interior parts. The process involves placing multiple layers of composite material into a mold and then applying pressure and heat to shape the material. This makes the parts lightweight, durable and resistant to fatigue and corrosion.
3.Producing thermal insulation materials. Spacecraft and aircraft require effective thermal insulation materials to protect sensitive equipment and maintain stable temperatures. Compression molding can produce thermal insulation materials with precise dimensions and excellent thermal properties.
4.Used to manufacture aerospace seals and gaskets. These components play a vital role in ensuring the integrity of various systems such as fuel tanks, hydraulic systems and engines. Seals and gaskets can be produced with tight tolerances and excellent resistance to high temperatures, chemicals and pressures.
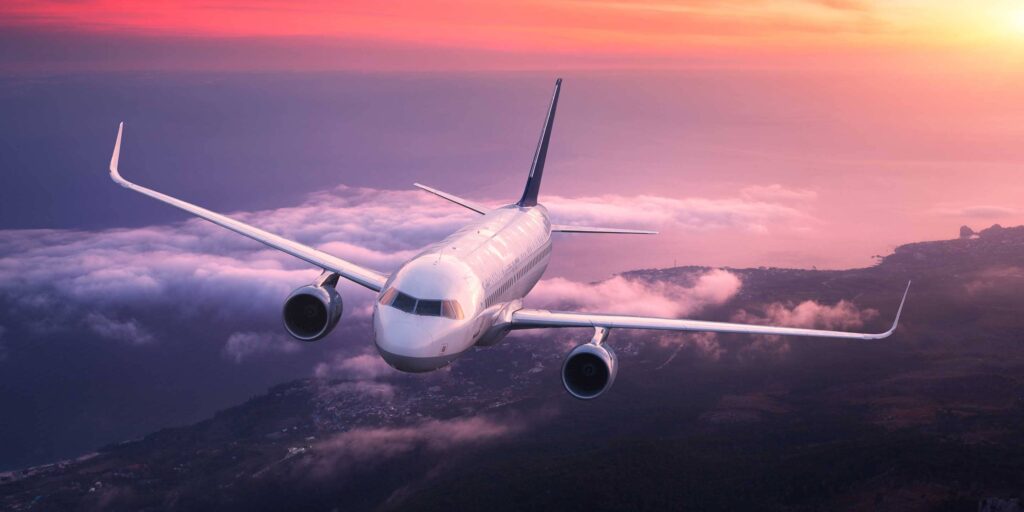
5.It is also used in the production of aerospace tools. Tooling refers to the molds, dies and fixtures used in the manufacturing process. Compression molding can produce molds with complex geometries and high precision, ensuring efficient and precise production of aerospace parts.
6.The aerospace industry requires high-quality and reliable components that can withstand extreme conditions. Compression molding offers several advantages that make it ideal for aerospace applications. First, the process produces parts with consistent dimensions and an excellent surface finish. This is critical in the aerospace industry, where even small changes can affect performance and safety.
7.Produce parts with higher fiber volume fractions, resulting in superior mechanical properties. The ability to control fiber orientation and distribution within a part can optimize strength and stiffness, further improving the performance of aerospace components.
8.Cost savings. The process is relatively simple to operate, requires less equipment, and is particularly suitable for large-scale production. In addition, compression molding can reduce cycle time, shorten production cycles, and improve overall efficiency.
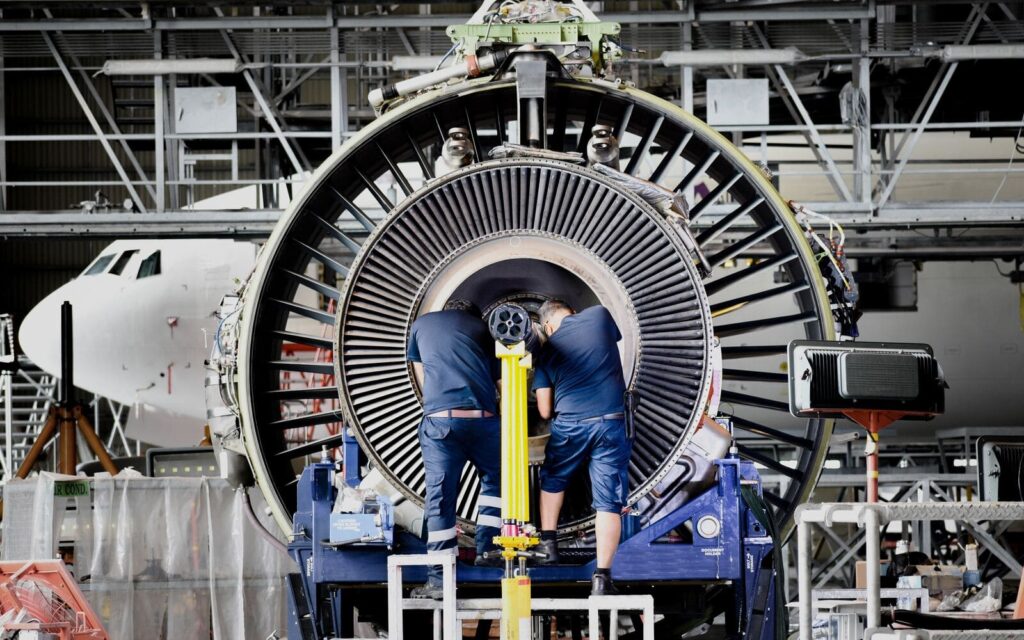
In summary
Compression molding plays a vital role in the aerospace industry. Applications range from producing composite parts and insulation materials to seals, gaskets and molds. The process offers many advantages, including high precision, excellent surface finish and cost savings.