Effect of different machining methods on the performance of air compressor check valves
Air compressor check valves play a vital role in compressed air systems. Their main function is to prevent gas backflow and ensure stable operation of the system.
The core performance of air compressor check valves includes sealing, wear resistance, fatigue resistance, etc., and the quality of these performances depends largely on the machining methods used.
Therefore, this paper will explore the key components of air compressor check valves and their machining requirements, and systematically analyze the advantages and disadvantages of different machining methods, their impact on check valve performance, optimization strategies, and practical application cases.
1.Air compressor check valve – what is it and how does it work?
(1) Definition
The air compressor check valve is a valve installed on the compressor outlet pipe, mainly used to prevent compressed air from flowing back when the compressor is shut down. It is an important component in the compressed air system to ensure efficient operation.
(2) Main functions
1) Prevent air backflow:
Prevent compressed air from flowing back to the compressor to prevent damage to the compressor blades or pump.
2) Maintain system pressure:
Maintain the air pressure in the air tank to prevent the compressor from starting frequently.
3) Protect the compressor and system components:
Reduce the pressure shock to equipment such as pipelines and filters, and extend the life of the equipment.
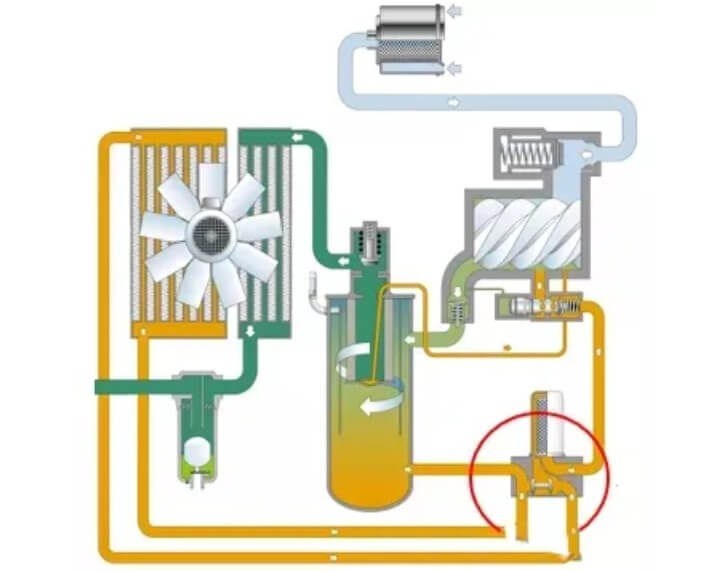
(3) Working principle
The check valve is a type of fluid control valve. It is a valve specifically used to control the one-way flow of fluid (liquid or gas).
1) When the air flows in the forward direction:
The air generated by the compressor pushes the valve disc, causing the check valve to open, and the air flows smoothly to the air tank or pipeline system.
2) When the air flows in the reverse direction:
When the compressor stops or the pressure in the air tank is higher than the pressure at the supply end, the spring or gravity will close the valve disc to prevent air from flowing back.
(4) Main types
1) Spring check valve:
Controls opening and closing through spring force, responds quickly, and is suitable for most air compressors.
2) Gravity check valve:
Closes by its own weight, suitable for lower pressure systems.
3) Piston check valve:
Used for high-pressure systems, with better sealing performance.
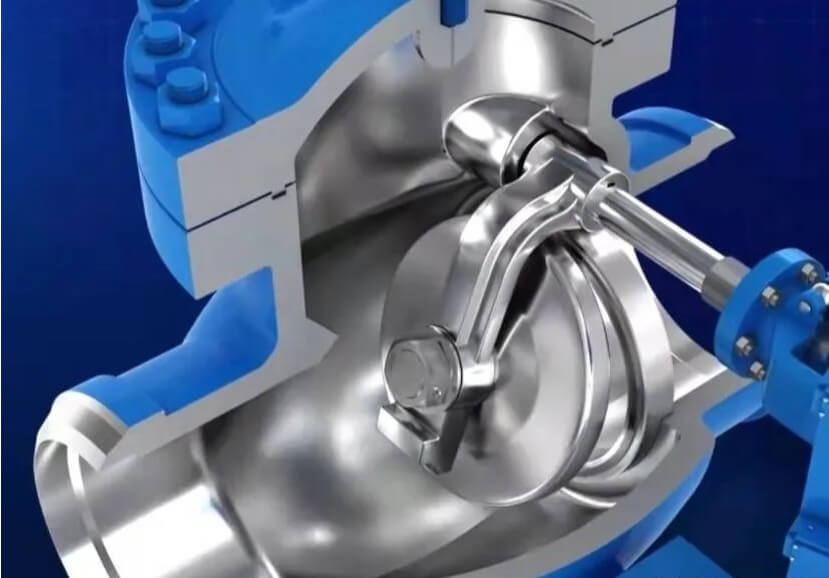
2.Key components and machining requirements of air compressor check valves
(1) Valve body
The valve body is the main structure of the check valve, usually made of aluminum alloy, stainless steel, brass and other materials. The machining requirements of the valve body mainly include:
● High-precision dimensional control to ensure good coordination with other components.
● Corrosion-resistant surface treatment to avoid oxidation or corrosion caused by moisture in the compressed air.
● Good mechanical strength to ensure that it will not deform after long-term use.
(2) Valve disc
The valve disc determines the sealing of the check valve, and its machining requirements include:
● Precision machining of the sealing surface to reduce the risk of leakage.
● Wear-resistant treatment to ensure that it still maintains a good sealing state after long-term use.
● Reduce the impact of cavitation and improve the fatigue resistance of the valve disc.
(3) Spring
The spring is used to control the opening and closing of the valve disc. Its main requirements include:
● Precise elasticity control to avoid unstable opening/closing of the valve disc.
● Anti-fatigue treatment to extend the service life.
● Surface anti-corrosion treatment to reduce the impact of air humidity on the spring.
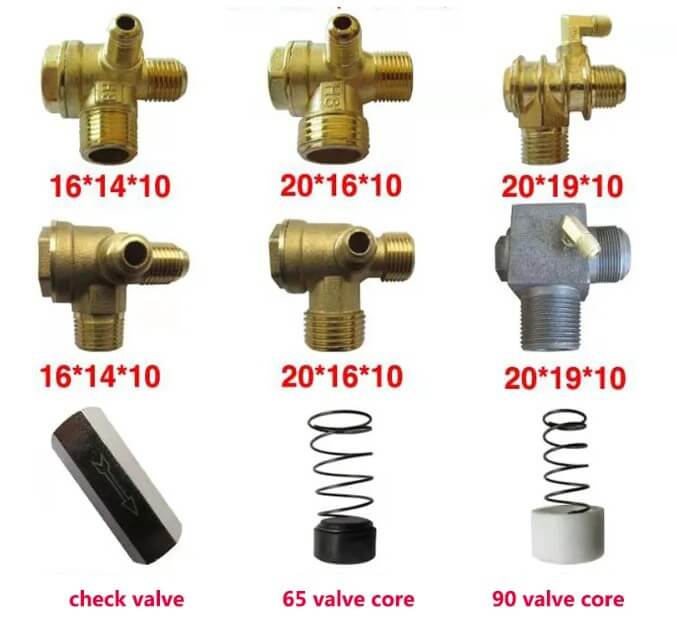
(4) Sealing structure
The machining accuracy of the sealing surface directly affects the performance of the check valve, so it is necessary to:
High-precision grinding and polishing to ensure the tightness of the seal.
Reduce surface roughness, improve wear resistance and sealing effect.
3.Main machining methods of air compressor check valves and their effects
(1) Traditional machining methods
1) Turning
Turning is the main method for machining valve bodies and valve discs, usually used for preliminary molding. Its advantages and disadvantages include:
●Advantages: fast processing speed, suitable for mass production.
●Disadvantages: high surface roughness, requiring subsequent processing to improve the sealing effect.
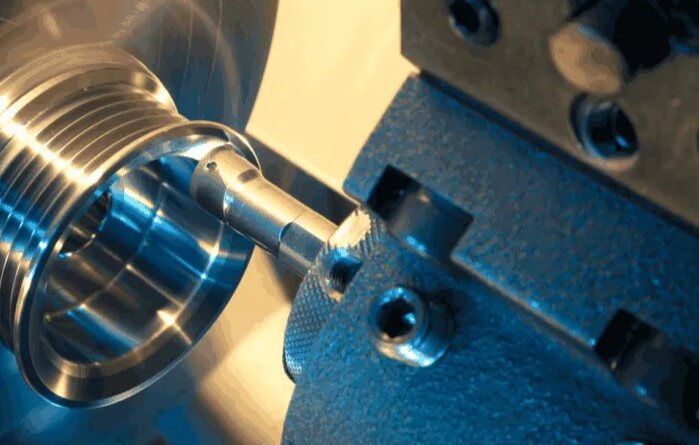
2) Milling
Used to process complex geometric shapes, such as the flow channel part of the valve disc.
●Advantages: high precision, can be used for fine structure processing.
●Disadvantages: fast tool wear and high processing cost.
3) Drilling and tapping
Used to process threads and channel holes.
●Advantages: high processing efficiency, suitable for mass production.
●Disadvantages: The aperture error is difficult to control and requires precise positioning.
4) Grinding and polishing
Used to improve the finish of the sealing surface.
●Advantages: Improve surface quality and improve the sealing of the check valve.
●Disadvantages: Slow processing speed, suitable for high-precision parts.
(2) High-precision processing methods
1) Precision processing
Use computer numerical control machine tools for high-precision processing.
●Advantages: Good repeatability, small error, and improved production consistency.
●Disadvantages: High equipment cost, suitable for high-end products.
2) Ultra-precision turning and grinding
●Scope of application: Used for ultra-precision processing of check valve sealing surfaces and key components.
●Impact: Improve surface finish and reduce leakage risk.
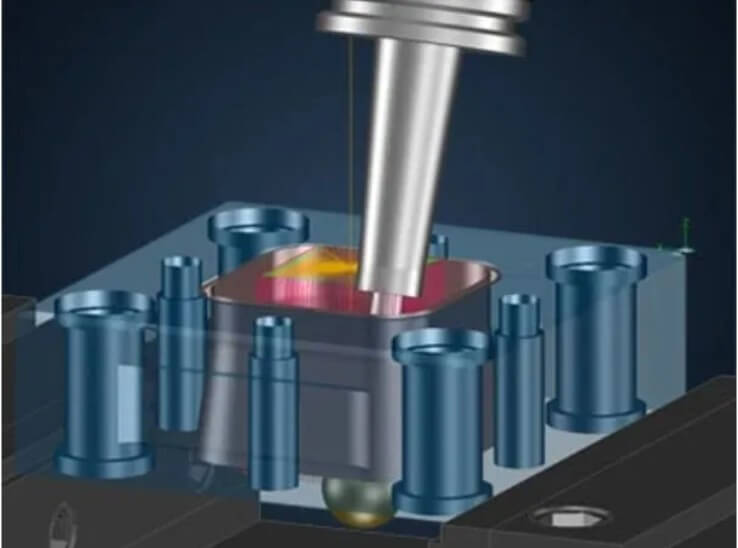
3) Electrospark machining (EDM)
●Scope of application: Used for processing high-hardness materials or complex structures.
●Impact: No mechanical stress, suitable for high-demand scenarios, but low efficiency.
4) Laser processing
● Scope of application: used for micro-hole processing and surface modification.
● Impact: improve wear resistance and corrosion resistance, but the equipment cost is high.
(3) Surface treatment and modification technology
1) Nitriding treatment: improve hardness and wear resistance, suitable for high-strength alloys.
2) Chrome plating and nickel plating: reduce friction and improve corrosion resistance.
3) Teflon (PTFE) coating: reduce adhesion and improve sealing effect.
4.Specific impact of different machining methods on the performance of air compressor check valve
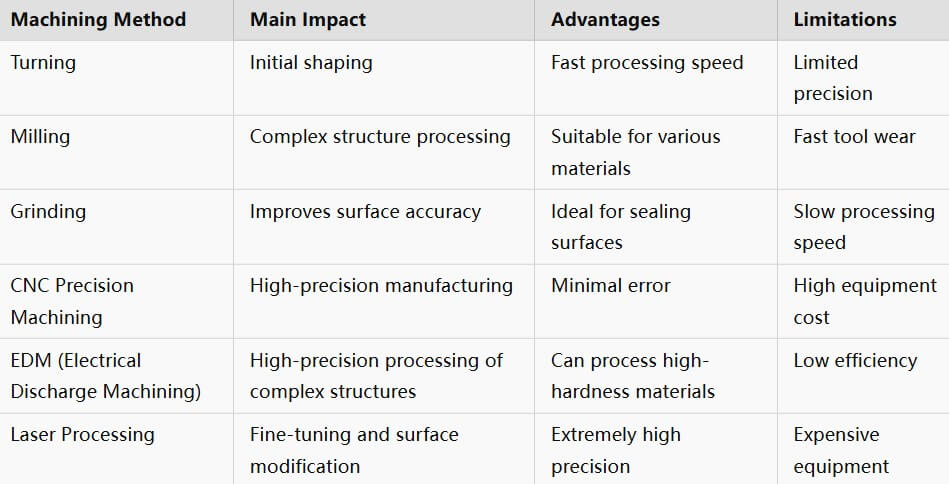
5.Application field of air compressor check valve
As a key component, air compressor check valve is widely used in many industries to ensure the one-way flow of compressed air, prevent backflow, and improve system safety and efficiency.
(1) Industrial manufacturing
Applicable to the automotive, electronics, textile and other industries to ensure the stable operation of pneumatic tools, spraying equipment, and automated production lines.
(2) Building and Construction
Used to drive pneumatic drills, nail guns, and pneumatic picks to ensure the normal air supply of construction equipment and prevent backflow from damaging the compressor.
(3) Medical Industry
In medical devices such as ventilators and dental equipment, prevent compressed air contamination and ensure a clean air source.
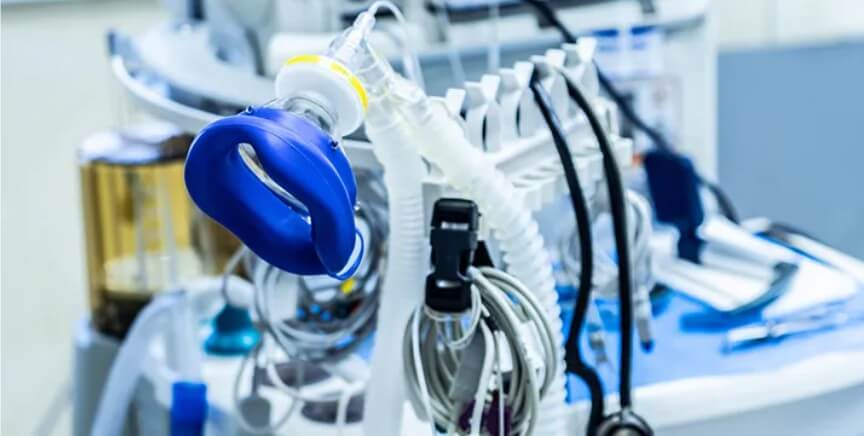
(4) Food and Beverage
Applied to packaging, filling, spray drying and other processes to ensure that food-grade compressed air is not contaminated.
(5) Energy and Mining
In scenarios such as oil extraction and mine ventilation, prevent air backflow and improve equipment safety.
(6) Transportation
In railway braking systems and tire inflation stations, prevent gas backflow from affecting system pressure stability.
6.Summary
In modern industry, the performance optimization of air compressor check valves is inseparable from advanced machining technology. Whether it is traditional machining methods or modern CNC technology, scientific selection and reasonable application according to demand can maximize the performance potential of air compressor check valves.